The first leg of the journey to Ethernet-APL is to fully liberate all that secondary instrument data that has long gone underutilized across the process industries. Indeed, a growing number of progressive process manufacturers are using multiplexer technology to extract all that rich, digital HART data from their 4-20mA analog loops—and already are using that data to effectively advance their digital transformation initiatives. HART-IP over Ethernet-APL will just make that access simpler, faster and easier.
Over the past several years, network infrastructure specialist Phoenix Contact has seen a significant uptick in the number of users retrofitting their plants to bring previously stranded HART data up into asset management and other monitoring systems, according to Garrett Schmidt, senior product manager.
“We know that most of these devices are going into brownfield facilities,” Schmidt explains. “They’re connecting to 4-20mA HART instruments with the highest value data first—typically more complex instruments such as valve controllers and flowmeters—then building out from there.” A confessed IoT junkie, Schmidt attributes the growing interest in continuous, full-time access to HART data to organizations’ digital transformation initiatives.
3M is among those end-user companies that has placed a new emphasis in recent years on the value it can derive from continuous access to HART data, according to Robert Sentz, senior engineering specialist. “We are using more and more of that the available diagnostic data from smart valve positioners, smart pressure, temperature and flow instrumentation,” he says. Indeed, the company is betting its operational future on digital technologies such as performance-driven analytics and prescriptive maintenance enabled by instrument data. “All that HART information is getting to be almost as critical as the process measurement, the process control piece itself,” Sentz says.
“HART over analog loops is very robust, but it’s also slow,” Sentz adds. “So, I’m very intrigued by the potential to further improve plant performance and availability with Ethernet-APL and HART-IP.”
And while HART-IP over Ethernet-APL will dramatically improve the accessibility and utility of data in today’s instruments, the second leg of the Ethernet-APL journey will pair that new speed with higher instrument power and protocol independence to launch a whole new world of transformative possibilities.
Enhanced capabilities
Higher bandwidth and more available power will allow makers of today’s process instruments to create new sources of value in their next-generation, Ethernet-APL-enabled devices. Future pressure transmitters, for example, may include multiple, automatically ranging sensors, which would allow a given transmitter to cover a broader range of pressures without sacrificing accuracy, envisions Jonas Berge, senior director, applied technology, Emerson. Notably, this would solve the problem of needing to stock a large inventory of pressure transmitters for various applications.
Similarly, more available power will allow makers of two-wire flowmeters to increase the excitation signal of Coriolis or magnetic flow-tubes, enabling higher turndown ratios—and more accurate measurements at low flow rates. It will also allow two-wire, Ethernet-APL flowmeters to handle larger pipe sizes than currently possible.
More available power would also allow two-wire flowmeters to continuously perform a broader range of process diagnostics, for example, detecting corrosion in Coriolis meter tubing, says Andy Kravitz, instrumentation connectivity product manager, Emerson. Currently, the negative effects of corrosion can be detected by initiating a Smart Meter Verification test. However due to the speeds of today’s protocols, most users only receive a pass/fail signal alerting them to a problem after it has affected meter performance. With Ethernet-APL, users will be able to easily pull the underlying diagnostic variables into their analytics systems. “In effect their ability to monitor the corrosion in their meter would change from reactive to proactive, allowing them to mitigate problems before a meter failure has occurred,” Kravitz explains.
Process-induced measurement noise is a problem for many sensors today, adds Berge. But with more power for the microprocessor, future sensors may feature more advanced signal processing to overcome the effects of noise. And in extreme cases, the sensor may be able to leverage the capabilities of a remote server to provide further analysis.
“Perhaps next-generation, non-intrusive ultrasonic flowmeters will perform at a level high enough to calculate mass and energy balances on heat exchangers,” Berge says. “This would solve the problem of having to cut and weld pipes or otherwise disrupt the process to get a reliable flow measurement.”
Pressure drop, flow, vibration and acoustic noise are useful inputs in detecting and predicting control valve failures, but typically go unmeasured on a routine basis. With Ethernet-APL networking, it will be more practical to measure and integrate such external variables into valve diagnostics to provide more predictive and prescriptive analytics.
The scope of diagnostics for instruments such as digital valve controllers will also begin to include other related data from “peer” devices on the network, predicts Kurtis Jensen, valve instrumentation portfolio manager, Emerson. “Instruments will become more process aware,” he predicts. “If my valve controller shows the valve is closed, yet there’s still pressure drop across a downstream orifice plate, it can tell me there’s a problem.”
More broadly speaking, Ethernet-APL will make it possible to utilize instruments’ auxiliary variable measurements more fully. For example, measures of ambient temperature across all instrumentation points in a plant could be used to create a thermal map of the entire facility, providing early detection of a fire or fire hazard. Most field instruments already include such auxiliary measurements today, but they usually go unutilized.
Another transformative aspect of Ethernet-APL technology will be to replace the patchwork of application-specific networks used in process environments, building toward a single, unified network architecture. For example, today’s addressable fire and gas (F&G) detectors use proprietary application protocols and therefore require dedicated networks. In the future, F&G detectors of various kinds may share the same Ethernet-APL/HART-IP network with the rest of a plant’s instrumentation. Such solutions will likely be more economical to deploy, allowing more detectors for better coverage in tight spaces such as offshore rigs and production units. The units will be safer, and the systems easier to maintain as a result.
One significant new capability of Ethernet-APL instrument networks actually has nothing to do with the instruments. Rather, it’s built into the network itself. Sometimes referred to as intelligent networking, the communications chips provided by Analog Devices continuously measure noise levels on each network segment and can alert if link quality degrades.
Devices can be configured to run such link quality diagnostics on a regular basis, and if there is an issue, the diagnostics can even indicate the location of the problem, explains Fiona Treacy, marketing manager, Analog Devices. “We can pinpoint the location of a problem to within 1%,” she says. “So, for a kilometer of cabling you can tell where a short is to within 40 meters.”
Novel devices, complementary protocols
Some in industry envision a real-time digital field network as just a replacement of 4-20mA process variables, control commands and secondary diagnostic and configuration data using digital HART-IP signals. But the possibilities are much greater than simply enhancing the capabilities of current field instruments and rapidly sharing their data with the people and applications that can put it to work. Rather, we should also recognize the potential for Ethernet-APL to enable entirely new kinds of field instruments solving previously unsolved problems.
Setting the range in a pressure transmitter without applying an input might have been impressive 30 years ago. But today we expect far more from a “smart” device. We should expect other time-consuming tasks to be eliminated or simplified in similar ways. And with 4-20mA signals replaced by HART-IP over a fully digital Ethernet-APL infrastructure, field instrumentation will finally be able to benefit from the dramatic technology advances that have transformed computing and communications in our personal lives.
Indeed, today’s expectations for new smart devices for industry should model the breakthroughs brought about by the mobile phone network. Once the GMS network supported GPRS data, it wasn’t long before the first smartphone appeared. Little did we realize; the smartphone was a full-fledged pocket computer and communicator that coincidentally made phone calls. So, expectations for industry’s future should not be just better transmitters, but also new classes of field devices.
Among other implications, digital transformation of plant operations means that many monitoring tasks which have until now been done manually by operators on rounds with portable testers will instead be done continuously and automatically by permanently installed sensors. Common examples of this include vibration, temperature, acoustic noise and corrosion (wall thickness) measurements.
Audible noise sensors (microphones) that share the common Ethernet-APL backbone may be used to identify noisy hotspots, helping to assure protective measures for employees, the tranquility of neighboring communities and compliance with ever more stringent regulations. The abundant power and high bandwidth of Ethernet-APL networking may also enable noise spectrum analysis, identifying sources of noise and possibly diagnosing process and equipment problems from changes in noise patterns.
Machine vision has been used in discrete manufacturing for years. In the future, perhaps there will be two-wire infrared cameras for liquid leak/spill detection sharing the same Ethernet-APL network as other devices. And instead of portable thermographic cameras to measure equipment temperatures, there may be permanently installed two-wire thermographic cameras to automate manual inspection. Other possible applications include flare monitoring and smoke detection, recognition of unauthorized intruders as well as proper use of personal protective equipment by authorized personnel. All these measures could reduce hazards and improve security and safety.
A field-mounted two-wire vibration transmitter sharing the same HART-IP over Ethernet-APL network as other field instruments may in the future support sophisticated, fast-Fourier-transform (FFT) edge analytics to head off quickly developing problems with pumps, fans and other rotating equipment. Operations, maintenance and reliability personnel may even collaborate over a livestreamed vibration spectrum, including waveforms and orbits, to better understand potential issues.
While HART-IP over Ethernet-APL is suitable for many of these new devices, others will operate best through other Ethernet application protocols often developed specifically for that type of device. A key attribute of Ethernet-APL is that contrary to previous field device communication alternatives, it is non-exclusive. That is, a mix of application protocols can be used simultaneously, even on the same pair of wires. On the industrial side, HART-IP can co-exist with Profinet, EtherNet/IP, OPC UA and others. Meanwhile, it can also coexist with non-automation protocols such as RTP or RTSP for digital video.
So, all devices on the network need not use the same protocol. Not even all the instrumentation. A transmitter using HART-IP and a valve using Profinet can even participate in the same control loop—but the controller in between must be able to handle both protocols.
A more transparent future
A key advantage of implementing Ethernet-APL together with HART-IP is the extensive, global interoperability ecosystem supporting HART together with industry-wide familiarity with HART and the tools and work processes that support it. Preserving this common ground will be critical to easing industry’s transition to an Ethernet-APL future.
Longer term, higher bandwidth and more powerful devices will make understanding the underlying protocols less significant for end users, predicts Peter Zornio, CTO Automation Solutions, Emerson. “Eventually, talking about whether a particular instrument is using HART-IP, Profinet or EtherNet/IP will be like talking about whether our cell phones are using CDMA or TDMA.” Similarly, intelligent device management software promises to abstract the management of field devices from the details surrounding Field Device Integration technology.
In the near term, however, what doesn’t go away is the interoperability ecosystem that underlies the HART configuration and management tools in every distributed control system (DCS) and asset management system on the market, Zornio stresses. “When you sit down at the DCS to configure a new Ethernet-APL device, you don’t have to care about the new physical network or the protocol—it’s just a HART device like 4-20mA HART and WirelessHART devices,” he says. “Granted, a lot more data comes out a lot faster than it used to. And if we can deliver that impact without changing a lot of processes along the way, we’ll have accomplished our goal.”
Latest from Sponsored Content
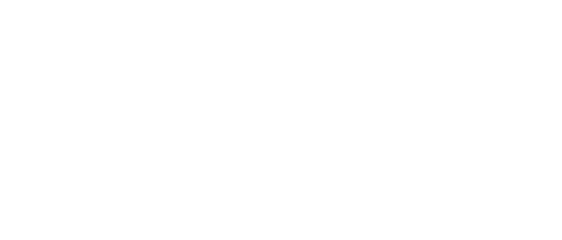
Leaders relevant to this article: