It’s been nearly 10 years since the process automation community first began investigating a protocol-neutral advanced physical layer (APL) that would extend Ethernet over the process industry’s last mile—providing connectivity with broadly distributed, two-wire, loop-powered field instruments in potentially hazardous environments. Today, we’ve also reached the last mile in that decade-long journey to make high-performance field device connectivity a practical reality.
Referred to as Ethernet-APL, the technology was successfully tested in trials at BASF in 2019, and a multi-vendor prototype network was shown at last November 2019’s NAMUR General Meeting. And at the ARC Advisory Group Forum in February 2020, ABB showed an implementation that effectively eliminated all gateways and protocol conversions from a level gauge all the way to a corporate network level (see sidebar, below). Automation suppliers are targeting ACHEMA 2021, to be held next June in Frankfurt, to show commercial products based on the standard.
Ethernet-APL is a significant technical achievement in that it dramatically increases the bandwidth available for digital instrument communications, as well as simplifies the network architecture in one fell swoop. At 10 Mbit/s, Ethernet-APL clocks in at more than 300 times faster than the fastest current fieldbus protocols. This means that transmitting 100 parameters to an instrument in the field takes mere seconds. And, since it’s Ethernet, the standard effectively facilitates top-to-bottom cybersecurity and the use of other IT-native software tools, while eliminating the need for gateways or protocol conversion from the field device all the way to enterprise business systems and the cloud.
Significantly, the consortium developing Ethernet-APL counts among its supporters four of the process industry’s key communications standards development organizations—FieldComm Group, Profibus & Profinet International (PI), ODVA and the OPC Foundation—as well as a dozen process automation companies that together represent considerable clout in the global marketplace: ABB, Emerson, Endress+Hauser, Krohne, Pepperl+Fuchs, Phoenix Contact, Rockwell Automation, Samson, Siemens, Stahl, VEGA and Yokogawa.
FieldComm Group and Ethernet-APL
As one of the three founding standards development organizations tasked with bringing Ethernet-APL to market, FieldComm Group has taken an active role in defining compliance and registration policies for devices that claim to support the standard.
Ethernet-APL represents a step change for instrumentation technology in that never before has a 10mBit/sec data pipe be available at the field level. And while HART-IP is an established technology in the infrastructure layer where WirelessHART gateways, and wired multiplexers can connect to Ethernet networks with HART-IP, the instrumentation layer represents the last mile of connectivity.
HART-IP enabled instruments represent perhaps the simplest path of migration to an Ethernet-APL network. The configuration software used by millions of technicians and engineers, remains the same. The asset management system software also remains the same. In other words, migration from HART instrument to HART-IP instruments, will be a low-risk, low-cost proposition.
To simplify development of HART-IP instruments, FieldComm Group offers a developer kit that includes communications hardware, a sample flow device application, and open source software for the HART-IP client and server software components. (Visit store.fieldcommgroup.org.)
A secure onramp to digital twins
Even as the APL Project has been working to extend an IIoT-sized expressway to field instruments, work has progressed on complementary standards from the software and systems side of the world that are poised to take full advantage of that new bandwidth. Notable among these are FDI and the OPC UA-based Process Automation Device Information Model (PA-DIM)—which both promise to bring new order and value to the digital field.
“FDI and PA-DIM are all about making it easier for software systems throughout the enterprise to consume information provided by instruments,” explains Paul Sereiko, director of marketing, and product strategy FieldComm Group. “Ethernet-APL is all about replacing gateways and remote I/O with Ethernet switches to facilitate the routing of the information from the device to the enterprise system. Ultimately, it’s possible that the higher speeds enabled will lend themselves to feature enhancements for FDI and PA-DIM that further simplify device integrations.”
“As a technology, FDI and PA-DIM are designed to help lower the bar for pulling information from field devices,” adds Andy Kravitz, flow transmitter marketing manager and APL working group representative for Emerson. “Given that Ethernet-APL increases the bandwidth to individual devices, we expect the combination of all of these technologies will help drive customers to more fully utilize the capabilities of our devices more easily than ever before. This will enable field devices to easily integrate with every level of the process data ecosystem from the control system all the way to the cloud.”
Ethernet-APL and PA-DIM in combination offer the possibility to access data from the field in a parallel communication path to the control integration, notes Lukas Klausmann of Endress+Hauser. “This second-channel approach supports the concept of NAMUR Open Architecture (NOA) without influencing core automation processes,” Klaussmann says. “This is the basis of plant-wide availability of data, and its easy interpretation without need for device-specific drivers. The possibilities of such digital services are numerous, and offer extensive support for optimization efforts and efficiency improvements in a process plant.”
The fact that Ethernet-APL supports the full Ethernet stack means that all the additional features of the IEEE world are available to increase usability, says ABB’s Merlin, citing Link Layer Discovery Protocol (LLDP), an out-of-the-box tool available once you’re part of the Ethernet ecosystem.
“The general multi-protocol capability of Ethernet is far-reaching,” Merlin says. “It makes the secure bridging between OT and IT world a lot easier. And due to universal applicability of OPC UA from field level to cloud, Ethernet-APL is a cornerstone to connect physical assets to their digital twins.”
Extended standards
Ethernet-APL is based on the IEEE’s recently approved 802.3cg-2019 (10BASE-T1L) standard, which effectively extends the 802.3 Ethernet standard to include single-pair wiring over distances up to 1,000 meters with the optional provision of power to devices. Ethernet-APL is of particular importance to the process industries because its focus is on extending 10BASE-T1L for use in hazardous areas.
The IEC PT 60079-47 technical committee is working on a technical specification called Two-Wire Intrinsically Safe Ethernet (2-WISE) to fulfill the requirement of intrinsic safety for loop-powered and separately powered devices in hazardous areas up to Zone 0, 1 and 2/Division 1 and 2.
To make engineering and verification of intrinsically safe loops as simple as possible, 2-WISE is inspired by the same Ex-concept as the well-established Fieldbus Intrinsically Safe Concept (FISCO). This concept is supported by successful tests executed at Dekra Testing and Certification GmbH. The final specification (IEC TS 60079-47) is expected in 2021.
In addition, Ethernet-APL defines port profiles for multiple power levels for use both inside and outside of explosion hazardous areas to ensure interoperability of field switches and field devices. These Ethernet-APL port profiles define multiple, precisely defined power levels that are specifically tailored to the needs of process industries and replaces power delivery via Power over Data Lines (PoDL), which is optional within the 10BASE-T1L standard.
“Compliance with this power profile concept is crucial in order to avoid hardware variances for field devices that could be installed in hazardous as well as unclassified areas,” notes Lukas Klausmann, senior marketing manager, Endress+Hauser Digital Solutions. So, devices for Ethernet-APL and for standard single-pair Ethernet (SPE) won’t mix and match in the same system in part because the Ethernet-APL field devices being developed won’t support PoDL functionality.
On the positive side, Ethernet-APL will deliver more intrinsically safe power to field instruments. “This will enable instrument vendors to design two-wire instruments that today require four wires due to high power demand,” says Michael Kessler, executive vice president, components and technology, Pepperl+Fuchs.
Finally, to ensure standards conformance, the APL Project will specify Ethernet-APL conformance tests to be integrated into the appropriate specifications of the relevant standards development organizations.
In many ways, the interoperability and openness promised by Ethernet-APL together with the OPC UA-based Process Automation Device Information Model (PA-DIM) at the field level complements the system-level efforts represented by the O-PAS standard from the Open Process Automation Forum (OPAF), Modular Type Package (MTP) concepts and the NAMUR Open Architecture (NOA) model. And at the ARC Advisory Group Forum, held in February, 2020, ABB showed a demonstration unit designed to illustrate just how these models can work together to provide an unprecedented level of openness and interoperability—from field devices up through process automation systems. In the physical demonstration, an ABB level gauge communicated via OPC UA over Ethernet-APL to a Phoenix Contact APL switch interfacing directly to an Ethernet-based O-PAS Connectivity Framework, or OCF, that included ABB programmable logic controllers (representing distributed control nodes, or DCNs controlling MTPs), local control panel and Virtual DCN. The demonstration also showed how this architecture could readily accommodate the MTP “Operational Orchestration System” communicating with multiple MTPs, that is, pre-automated modular process units designed to be easily added, arranged and adjusted according to production needs.
This architecture also readily accommodates the NAMUR vision of a parallel path for non-control instrument data to other plant applications, such as for condition monitoring or asset management. “We see APL as enabling the field device to take a more active role in an open process automation architecture,” explains Luis Duran, global product line manager for safety, ABB, and Business Working Group representative to OPAF. “In this architecture, that level gauge could just as easily be a final control element,” he adds.
Latest from Sponsored Content
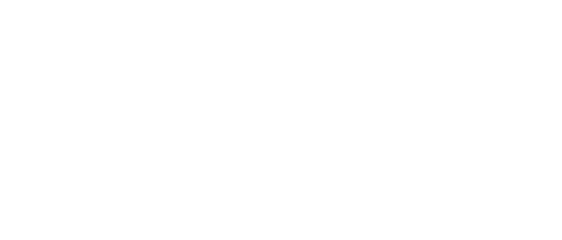
Leaders relevant to this article: