Jatinder, who came up through the facility’s engineering ranks, notes that before the plant’s automation platform upgrade to ABB’s latest offering in the late 2020’s, operations sometimes suffered under distributed control systems (DCSs) that were both inflexible and limited in capacity.
“The control system architecture was quite rigid, with all input/output (I/O) points mapped to one particular controller and all field data from those points necessarily streamed through that particular controller as well,” Jatinder explains. This setup also meant that only a certain number of tasks for a limited number of control loops could be run on a particular controller, which usually had been specified based on the application task cycle and amount of data to be ingested and processed from the field at the time it was installed. “But with the passage of time and incremental tweaks, many of the controllers had reached their limits,” Jatinder says.
“It was a very hardware-centric approach, which also meant that any sort of redundancy or fault-tolerance schemes were hardware-based as well,” Jatinder adds. Among other implications, this meant that if a redundant system failed, its back-up had to run in an unprotected state until repairs were made, increasing the risk to operations.
A new normal
“In the years leading up to our system upgrade, I had been impressed with all that ABB had been doing to liberate users from these dependencies,” Jatinder adds. “First at the I/O layer and then among what we now refer to as the control appliances.” These devices now include local compute capability—for both control loops and logic execution—as well as top- and bottom-side network connectivity to any system I/O, other control appliances and even server- or cloud-based resources that can all be called on for back-up.
“With our ABB system, we now have software-based control that is fully flexible from the perspectives of deployment and redundancy. The system’s now readily scalable as well and can easily support redundancy schemes ranging from 1:1 to N:M with controller operations backed up by a cloud server or local industrial computer.”
“We now have intelligent fault-tolerance, which means that if the system loses a critical control component, it can automatically spin up a new controller in a redundant form to maintain system operations in a secure, protected fashion,” Jatinder explains. And while I/O can easily be associated with any controller, it can also be dynamically reassigned as needed, supporting multiple redundancy schemes. Further, if a control appliance fails, the system can automatically and proactively move control functions to other components, allowing the failed appliance to be easily replaced on-line, with secure on-boarding features. Then, the system can easily and automatically redeploy control functions as appropriate to newly onboarded components.
“The capabilities of the ABB process automation system platform allow us the flexibility to continually optimize the performance of our refining processes and protect their continuous operations,” Jatinder adds. ”And do so in a cost-effective fashion.”
Note: The characters and organizations depicted in this vision are fictitious. The ABB DCS Vision, however, is very real. Download the white paper at https://new.abb.com/control-systems/control-systems/envisioning-the-future-of-process-automation-systems.
This was just one stop on our tour of ABB's Process Automation Systems Vision 10 years in the future. Don't miss a single stop. Read more at the articles below.
Latest from Sponsored Content
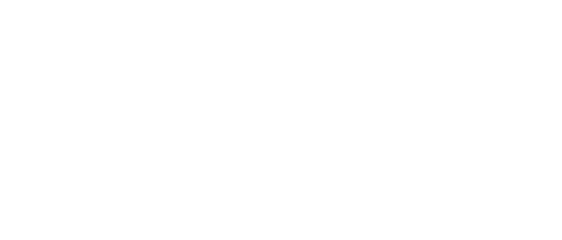
Leaders relevant to this article: