Industrial process operations are continually evolving, and for good reasons. These days, the goals are not only to get products to market, but also to get them there in the most efficient and safest manner possible. This is especially true in industries such as oil and gas, refining, energy transmission and chemical processing, where public and government scrutiny are abundant, dangers to workers are frequent, and cost efficiencies are paramount. So, it comes as no surprise that the venerable Rosemount 3051 Pressure Transmitter family has evolved with a focus on transforming the user experience to help users with each of those three core needs.
The most recent update to the Rosemount 3051 Pressure Transmitter is the biggest since its inception in 1988, and while the user experience has now been made more efficient and productive, the transmitters themselves remain as familiar and trustworthy as ever. Users already familiar with the Rosemount 3051 Pressure Transmitter won’t be lost when they connect to the device because Emerson has eased configuration, information gathering, and data analysis while transforming the user experience in many beneficial ways. Several improvements have been implemented to the Rosemount 3051 Pressure Transmitter that are designed to create a more efficient experience for technicians in the field while maintaining the familiarity of the product that many have grown to trust.
A better look at the graphical display
It all starts with how users can now interface with the pressure transmitters. Brad Burton, senior product manager at Emerson, says the improved graphical display is the improvement users will notice first. The Rosemount 3051 display now has backlighting for easy readability in all lighting conditions. It supports eight languages to make information gathering simpler across the globe.
In addition, Burton says the ability to display data in localized languages increases clarity and responsiveness for many Rosemount 3051 Pressure Transmitter users. It eliminates the need for translation on the plant floor. “As you can imagine, translating anything across languages can be confusing. Giving users device reporting information in their local language is a big improvement for giving them the information that they need in a clear and understandable way.”
He adds the display presents more information to the user at one time, while the percentage of range is always present, so the user has an indication of where they are on their output range. There’s a large numeric representation of the dynamic process variable whether pressure, flow, totalized flow, level, volume, or module temperature. A clear indication of the unit of measure sits below that indicator and is easily visible. “We also indicate clearly which variable we’re measuring,” Burton says. “Our Rosemount 3051 measures pressure, but our users infer things like level and flow rate from that pressure measurement.”
With that in mind, Emerson updated the pressure transmitter to make flow and level configurations easier, allowing users to see the dynamic variable that they’re trying to measure on the display. For example, in the case of flow rate, they may want to see the units in GPM or SCFM. The same can be said for level, where the transmitter can support level measurement in a variety of level or volume units.
Simplifying configuration
By providing installation and process details, the transmitter will automatically perform the necessary calculations to set the device up for level. All the user needs to provide is some DP level system installation information as well as key process details. Volume measurements are also possible for common tank styles or even customized tanks that require a strapping table.
The additional Quick Service Buttons also improve usability of the device. Following consultation with many long-time users of this iconic device, the company found being able to zero the device, re-range it, perform a loop test, view configuration, and orient the screen according to installation specifics was vital. For example, Burton says that if a technician sees a reading of a certain pressure and is concerned the device hasn’t been zeroed properly and that the reading isn’t correct, the technician doesn’t need to call the control room to get access to the device through the asset management system or find their AMS Trex communicator to connect to the device to be able to access the configuration. They can simply push buttons on the transmitter that activate the menu so they can check the configuration of the device. They can also make sure that it’s reading zero when the transmitter is vented or when the device is equalized between the high- and low-pressure sides.
Another area where the Rosemount 3051 has been improved is the ability to orient the unit as needed. The transmitter isn’t always mounted vertically in the field, so using the added Quick Service Buttons users can rotate the display screen to be readable in different orientations.
Maintaining more traceability
In the age of the smartphone, it’s no secret that users of any device have grown not only accustomed to, but also reliant upon the ability to access data and information at any given time. The Rosemount 3051 Pressure Transmitter is no different, particularly when it comes to maintenance tasks in the plant.
One of the major updates to the Rosemount 3051 transmitter family is its logs. It now offers more information stored directly within the transmitter. New diagnostic, calibration, and safety proof test logs can record and store multiple events to provide a better picture of device health and history. The diagnostic logs can track up to 100 events while calibration logs can track up to 20 events.
“From a traceability and maintenance standpoint, being able to reference when a unit was calibrated, how it was calibrated, and view the results of a given calibration is a big benefit,” says Connor Oberle, product manager at Emerson.
The unit features a Guided Proof Test as well. A lot of Rosemount 3051 transmitters are used in SIS or safety installations. One of the requirements for an SIS installation is to do a proof test at regular intervals, such as every six months or every year. Proof tests verify that the device is still working properly and will respond when it’s needed.
Depending on whether the user is doing a partial or comprehensive proof test, the device will drive the desired alarm settings and guide the calibration routine. With the proof test method that is built into the Rosemount 3051 Pressure Transmitter, the device walks users through the necessary steps to verify the alarm and perform any calibration verification.
“There are two keys that are the biggest value outside of the proof test steps themselves,” Oberle says. “One thing they [technicians] might not know is what alarm value the transmitter is using.”
That’s because devices may have different alarm values because they can be user-defined, he adds. The Rosemount 3051 Pressure Transmitter automatically pulls the correct value in, so the user knows what to test the reference meter against.
Oberle says the log is the other big advancement because it easily stores all the results of the proof tests. It even allows for customized notes to be included so that other users will know if it passed or failed and for what reasons. “
Track two alerts at once
“This is a big change from our legacy device in that the process alerts can drive analog output alarms,” says Burton. “Typically, with a 4-20 mA device, the analog output is the key piece of information that they’re relying on to be robust. If you configure your process alert to annunciate with an analog output alarm, now you’re putting a lot of weight on that process alert.”
The alert gives users the ability to tap into the information through the analog output channel rather than having to rely on interfacing it with a HART digital communication. “Some of our users are deeply rooted in 4-20 mA output, and they don’t even have that access to HART information. Having the ability is a big change,” Burton adds.
He also says that with two dynamic variables available, users can track pressure on one channel and flow rate on another, so they can have an alert that annunciates when the flow rate exceeds a certain value. "Having the flexibility to monitor two variables in the device and have them both independently configurable is a big value,” Burton says.
Latest from Sponsored Content
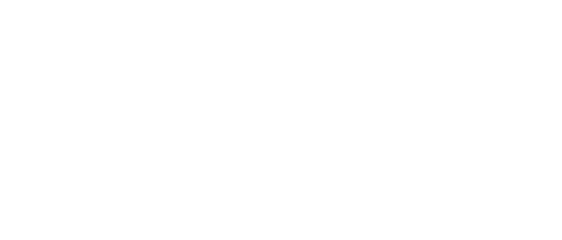
Leaders relevant to this article: