Automation Fair is Rockwell Automation’s annual gathering of its customers and partners to showcase what’s available and imagine what’s possible. “All of the ecosystem that has come together is about building the future of industrial operations,” said Tessa Myers, senior vice president, intelligent devices, Rockwell Automation.
With a flurry of acquisitions leading into the Boston event, Myers focused her keynote presentation on how companies can achieve resilience, agility and sustainability in their operations. “Complexity for any industrial company is increasing,” she warned. “And global value chains are being transformed.”
That transformation is taking place by combining technology, such as production design and control, intelligent devices, production logistics and edge-to-cloud solutions, with expertise in cybersecurity, digital consulting and industry-focused solutions.
“We live at the intersection of your most pressing problems and the technology that can help you overcome them,” said Myers. “We’re focused on simplifying the difficult work you have. Over the next decade, we’ll see supply chains powered by autonomous technology.”
Myers was joined onstage by four colleagues who described Rockwell Automation offerings to address significant technology trends, including production-logistics transformation, rapid startup with new design tools, resilience building, data-driven productivity and data-driven sustainability.
Production logistics
Matt Rendall, co-founder of Clearpath Robotics’ Otto Motors, one of the recent Rockwell Automation acquisitions, along with three Rockwell Automation employees—Matheus Bulho, vice president and general manager, production automation; Andrew Ellis, vice president, global portfolio engineering; and Rachael Conrad, vice president, global enterprise customer experience—showcased products poised for the next wave of automation implementations.
“Logistics is an opportunity to optimize production and empower people,” explained Myers. “There’s a need to retool operations and increase output. Historically we had one tool to handle product variations—throwing people at the problem. That’s no longer an option.” Labor shortages and the aging workforce are putting a strain on industrial operations. Traditionally forklifts and carts were driven and operated by human employees, for example.
“Our goal is to use autonomous mobile robots (AMRs) to create safer and more productive workplaces,” explained Rendall. “Otto Motors AMRs are deployed in factories all over the world. Finding enough people has been a challenge. It’s important to invest in new forms of automation to make better use of the scarce talent we have.”
Rendall cited a manufacturer in Indiana that had been able to run at only 75% of production because of a staff shortfall. By implementing AMRs from Otto Motors, the factory was able to reallocate employees from material-handling functions to operate an additional production line and increase productivity. “You want humans focusing on things they’re meant to do, and you want robots focusing on work they’re meant to do,” explained Rendall.
“Autonomous technology is not the realm of science fiction,” Rendall reassured the keynote audience. “We have lasers and cameras and advanced artificial intelligence (AI), allowing each Otto to perceive its environment and figure out the best way to get where it needs to go. The vehicle needs to be intelligent enough to respond to the unexpected. Our Fleet Manager [software] makes sure that the right vehicle gets assigned the right job, and it integrates with an enterprise resource planning (ERP) system and takes information from all sources. By automating material handling, manufacturers can elevate workers out of those jobs so they can work on other jobs where they’re needed.”
Digital design
Next up, a demonstration of machinery from Eagle Technologies, which was acquired in August by Convergix Automation Solutions, showed how digital tools can be utilized to speed design and commissioning, as well as provide data for predictive-maintenance capabilities.
“We have been working with companies all over the world to deploy new production systems and retool existing ones,” explained Rockwell Automation’s Bulho. “Leveraging virtual design and commissioning tools is one way we’re doing this. Convergix is a great example of how we emulate devices, test and commission in a virtual environment. It’s not uncommon for us to see companies like Eagle and Convergix take advantage of a 30% reduction in time of design and commissioning, which reduces the cost of startup delays.”
FactoryTalk Twin Studio is part of the FactoryTalk Hub. It hosts FactoryTalk Logix Echo and Emulate3D. “One of the key technologies in the Convergix is independent cart technology,” explained Bulho. “It frees equipment from traditional mechanical constraints.” Other technologies, such as FactoryTalk Optix, Plex and Fiix, make the machines information-ready.
Data-driven productivity and sustainability
Rockwell Automation’s been working across its portfolio to make products smarter and enable users to bring that intelligence to the edge and the cloud by creating the necessary infrastructure. “We’ve been investing in new capabilities,” said Ellis. “We’ve had a long history of partnering with best-in-class companies, and we’ve partnered with Microsoft to do just that.”
Ellis described the conceptual design of a machine with data-readiness as part of its inception. “We started with a digital twin,” he said. “This provided us with the ability to visualize the machine before we started fabrication. We have a lot of intelligent devices, including 15 sensors, on it. This data is used to provide visibility to help drive productivity and efficiency. It has our Armor PowerFlex drives to provide an on-machine solution that reduces the overall footprint.”
Once the data sources are established, they are integrated in FactoryTalk Optix, which connects to those devices and Plex Asset Performance Management (APM) software for rapid integration of OT sources. “It allows us to do production monitoring and reporting,” said Ellis. “Now that we have the context on the machine, we can be more predictive. When we need to gain further insight, we can add context with IT data sources and OT data sources using FactoryTalk DataMosaix. It’s all about connectivity—from the device to the edge to the cloud.”
Cyber resilience
Finally, Rockwell Automation’s Conrad joined Myers to walk through a cybersecurity demonstration at a fictitious water treatment plant. “We’ve experienced a perfect storm of disruptions,” said Myers, “including COVID, climate change and cyber threats.”
Using Rockwell Automation cyber tools, along with others from Cisco, Microsoft, CrowdStrike, Claroty and Dragos, Conrad was able to illustrate how an initial cyber attack and a secondary attack could be thwarted. “It takes an ecosystem to be able to deliver the right security,” noted Myers, who also recommended a zero-trust approach to cyber resilience.
“We have a partner ecosystem to leverage,” added Conrad. “While the challenges of OT are tricky, we can work through this together.” Verve Industrial, a U.S.-based company with a powerful vulnerability management platform is the latest acquisition announced by Rockwell Automation. “This platform was built with IT level security to address OT challenges,” noted Conrad. “With an asset approach, we’re able to aggregate all of that data, even from other partners’ tools, into a single pane of glass.”
Latest from Sponsored Content
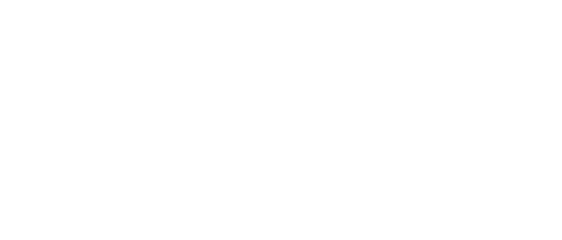
Leaders relevant to this article: