SCADA upgrade provides quick compliance for wastewater treatment facility
Figure 1: These tanks hold the acid and caustic needed to balance the pH of the wastewater produced from a large agriculture components metal cooling process.
A local municipality wanted confirmation, and the data to prove it, that the wastewater released into the sewer system by a large agricultural component manufacturer was within the county standards, and they wanted it immediately. What made this request difficult was that the current plant wastewater treatment system used only manual data logging. What made it worse was that the system’s process measurement instrumentation was uncalibrated and unvalidated, resulting in unreliable chemical dosing (Figure 1).System integrator Sensible Automation Solutions was brought in to quickly upgrade the wastewater treatment system. Although the original system operated well with an AutomationDirect Click PLC and C-more HMI, it couldn’t be used to meet the advanced requirements now demanded by the municipality.
It was necessary to add automatic data logging in place of the manual data logging. To better record process data, high-speed inputs to the system were needed to read flowmeter pulse outputs. Plant personnel also requested daily reports on the wastewater system process data, with the ability to email this information to their managers. None of this functionality was available with the Click PLC, so Sensible Automation Solutions chose the AutomationDirect BRX PLC to replace the existing controller and meet requirements.
Fitting BRX
The control system upgrade was performed on the existing wastewater treatment system, housed in a 200,000 sq. ft. facility with fabrication and metal coating processes for agriculture components used on large equipment. The system treats wastewater from the metal coating side of the plant, and it supports the power coating line, which uses a variety of chemicals. These chemicals are changed out or refreshed multiple times a day. This requires treatment of 25,000 to 30,000 gallons of wastewater per day so it can be safely released to the municipality’s sewer system.
The BRX PLC was a cost-effective and capable choice for this system, made easier because a couple of the technicians at the facility had prior experience with AutomationDirect. Sensible Automation Solutions has used a lot of PLCs in the past, but the BRX brings new capabilities for its form factor and cost. It’s a small, brick-type PLC with analog inputs and outputs, configurable high-speed inputs, and high-speed outputs—filling the needs of many different processes. The PLC’s Do-more programming software is powerful yet easy to use, adding to the appeal of the platform.
Figure 2: This new AutomationDirect BRX PLC replaced the existing Click controller with minimal required changes or wiring additions.
Another reason the BRX was chosen was because it fit in the panel space originally occupied by the small Click PLC. We simply unwired the existing Click controller and installed the BRX, along with ZIPLink connector modules and cables, and reattached the existing power and field wiring. Everything fit with minimal required changes and wiring additions (Figure 2).Some of the I/O that was already in place included a Rotex flowmeter, three analog pH sensors and an ultrasonic level sensor. Preexisting solenoids were used to run the air-operated diaphragm pumps.
Connecting and collecting
There are various tanks at the facility filled with chemicals used to treat and prepare the surface of the steel before it’s powder-coated. These chemicals are consumable. Once a tank’s chemical gets dirty, for example, it must be removed and changed out with fresh chemicals. Used chemicals are dumped to a waste manifold that drains into a pit.
The system must treat caustic and acidic chemicals in the pit. Every time the chemicals are changed out, they are drained into this pit. The pit must be brought to a pH between 5.5 and 8.5 before release to the sewer system. The control system monitors fluid level in the pit, adding either an acid or a base depending on measured pH.
The system logs pH data throughout the day including how much acid or base is being added and when, and how much water has been discharged. Once the water is within specification, the system pumps it out and logs process data such as when the water was pumped out, how much was pumped out, the amount of chemicals needed to achieve the final pH level, and the pH level when it was released to the sewer system.
The coating line is almost three quarters of a mile long. Workers hang components such as racks, engine mounts and frames onto hooks connected to an overhead monorail conveyor line. The line is powered, transporting the components and dipping them into the different tanks using conveyor elevation changes. There are also two or three robots inside a paint booth that apply the power coat to the components. Once coated, the components move through an oven where the coating is cured.
The monorail conveyor moves components through five different tanks. The first two are cleaning and neutralizing tanks. The next tank contains a surface modifier to help the powder coat attach to the substrate. A rinse tank follows, and the final tank is a specialty tank, sometimes used or not, depending on the process.
Capable control
The BRX PLC controls two 15-GPM diaphragm pumps used to feed the acidic or base solution to the pit based on the monitored pH levels. The amount of solution pumped varies depending on pit fill level. For example, if the pH is 5 and needs to be brought up to a pH of 7, the PLC will pump in the base while also running a recirculating pump that moves water from the bottom of the pit to the top for improved mixing. The PLC directs dosing of the pit, waits for 60 seconds and records the pH reading. If the pH level is acceptable, it will turn on the discharge pump to empty the pit into the sewer system.
The dosing needs vary. The pit could be holding 1,000 to 5,000 gallons, depending on the changeover process running. Because of this, a programmed routine in the BRX PLC, including a PID function, calculates the amount of acid or base to add to the pit depending on the measured pit level and measured pH in the pit, using this information to calculate the run time of the dosing diaphragm pumps.
Plant personnel knew about how much chemical was needed to treat the wastewater, but the tricky part was that it was just an estimate, depending on what the wastewater was composed of and the mixture of chemicals in the pit. Sometimes adding a gallon of base wouldn’t necessarily change the pit pH as expected, requiring more dosing.
The flowmeter added to the system had high-speed outputs proportional to flow that could be read by the BRX PLC. Since this flow and other data was logged and sent to the municipality, it needed to be accurately date-stamped, and the PLC provided this capability with its built-in clock.
The program to control the system was written from scratch for use in the new BRX PLC using the Do-more Designer Software. The facility provided a sequence of operations defining how it wanted the system to work. Ladder logic was then used to satisfy the requirements of the provided process sequence.
Installation tricks and tips
It was tricky to install the equipment—and time sensitive. The facility runs 24/7, so only six hours of shutdown time were available to remove the old controller, install the new one, power up, debug and test the system. Fortunately, another feature of the BRX helped with this quick upgrade, namely the on-board simulation, which was used extensively before installation to debug the program code.
Using simulation, it was possible to change pit level and pH process variable and see how the code responded. Using the simulation GUI interface, which is configurable, the process variables could be changed, and the interface made it easy to understand the program’s response by providing visualization of the controller outputs. As the actual program was simulating running, it even logged data.
On the hardware side, there were about 60 wires to remove and reinstall for the new controller. There were also some discrete signals, such as manual override pushbuttons and selector switches on the front panel. It all went together quickly.
HMI, trending and logging
Figure 3: An AutomationDirect C-more EA9 Series 15-in., touch-panel HMI was added to the new control system to provide status, data trending, historical data, reporting and other functions.
The new control system includes an AutomationDirect C-more EA9 Series 15-inch touch-panel HMI. The old system only had three or four pushbuttons on the HMI, so a new graphical interface program was created from scratch to take advantage of the C-more’s capabilities (Figure 3). Screens were added for data trending, allowing viewing of historical data for the past few hours. Screens were also added to view logged data from previous days. New operational screens were provided to view the level of the pit, dosing activity and general process status.Data is logged in two places because of its criticality, in the BRX and the C-more touch panel. The C-more has memory onboard and more can be added using a USB memory device or microSD card. Data is logged to the C-more’s microSD card, from which it’s pulled for reports and emails.
The automation system creates reports and sends them via email. For example, every day at 12:01 am, or any configured time, the C-more panel is set up to transfer the data via email to company managers. These reports are set up so that every night, it also sends a picture of the multivariable trend graph, along with a comma-separated values file of all the data trended in the graph. The automation system also sends out other specialized reports such as how much acid and base solution was used throughout the day.
Sensible Automation Solutions is currently working with the agricultural component manufacturer on three more projects, including automatic leveling of process tanks, and adding additional data logging on other C-more panels in the plant for additional plant processes.
The biggest challenge was doing the work quickly to satisfy the local authorities. To meet this requirement, Sensible Automation Solutions installed the new automation system within 10 days after the first call from the agricultural component manufacturer.
About the author:
James Catlett, the founder, owner and president of system integrator Sensible Automation Solutions, can be reached at [email protected].
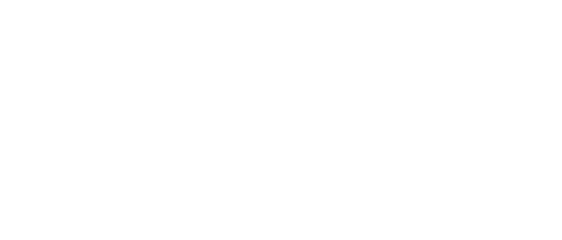
Leaders relevant to this article: