Frank Hein, principal engineer at Abbott Laboratories, North Chicago, Ill., has installed an advanced energy optimization system from Pavilion. "With all elements of the program in place, Abbott expects to save at least $273,000 per year, based on the current production rate," he says.
However, as Bela Liptak says, before you can control something, you have to measure it. Here's how and why to make power measurements (Figure 1) and do your own analysis and optimization. As we can see from Abbott's results, the payoff can be enormous.
Problems With Power
Electric power is expensive. "Manufacturing plants consume the most electricity in the United States, totaling more than $3.3 billion per year," says Dick Eshelman, vice president of engineering solutions at Rockwell Automation. "From downtime due to dirty power to avoiding peak demand charges, reducing energy-related expenses starts by understanding when, where, and how much energy is being consumed, and turning that knowledge into results."
Demand charges can be substantial. Although they vary from utility to utility, essentially the utility determines how much power your plant needs, sizes its substations accordingly, and then hits you with a significant surcharge (the peak demand rate) if you use too much power at any point in time. Exceed the peak demand rate one time in a month, and you get charged for it.
Therefore, the first energy monitoring program most plants install is a load-shedding system that measures and tracks electrical power consumption on a real-time basis. The system uses the same technique as the utility does to calculate peak demand, and sheds loads (turns off systems) to keep from exceeding the critical demand level.
If you do not understand your utility's tariff structure, it might be a good idea to get a copy of the rules and see how your energy bills are calculated.
Utilities are beginning to have problems delivering power, say market researchers at Frost & Sullivan. "Insufficient power infrastructure and the growing load on energy utilities are driving the end user market to uninterruptible power supply (UPS) systems. In the absence of clean and consistent power, UPS systems are needed to decrease downtime and protect sensitive equipment," says analyst Farah Saeed.
Is your incoming power clean and consistent? If not, it could cause severe problems. Richard Brown, engineer at ABB, says voltage sags and interruptions can cause havoc in a manufacturing line. He provides this list of potential problems for people in the semiconductor industry:
- A 20 msec. voltage sag to 65% will cause electronic controllers to crash.
- A 200 msec. voltage sag to 50% will cause an entire process to crash.
- An interruption lasting several minutes can cause problems with air and water filtration systems.
- Longer interruptions can affect critical temperature and humidity tolerances in a process.
(Stop wasting money on backup power)
"Because of the high economic cost of power quality disturbances, many sensitive facilities are beginning to ask electric utilities to guarantee levels of reliability in their energy contracts," says Brown. "Although not widespread at this time, such guarantees are already in effect for several car manufacturing facilities in Michigan. If a factory experiences a power quality disturbance that disturbs the production process, it receives a large credit on its energy bill."
California companies faced electric supply problems every day in 2001, as the energy crisis there reached epidemic proportions. At Cargill's salt plant in Newark, Calif., interruptions in the power supply caused production delays, leading some longtime customers to switch to alternate suppliers. "Our electricity costs doubled here, even with the incredible energy conservation measures we put in," says Lori Johnson, public affairs manager at Cargill Salt.
You need to monitor your incoming electric power to see if you have problems, avoid demand charges, decide what kind of protective and backup equipment to install, and catch your utility with its electric pants down.
Mike Powell, president of eLutions, says his company's EP Web monitoring and control software was installed in a chocolate manufacturing plant and quickly uncovered a severe problem during training. "The client's energy manager discovered a utility feed that had a 1 MW variance when compared to the other two feeds," Powell explains.
The utility found that the underground feeder was undersized before it entered the facility. "Using the EP Web software with the integral billing module, we were able to determine that the higher demand caused by the undersized feeder cost the facility millions of dollars in overcharges. This information was provided to the utility and an adjustment was received."
(Redundant Power Allows 'Live Maintenance' of IS Segments)
Perhaps your utility will help you monitor power. Georgia Power, Atlanta, offers EnergyDirect.com, an online tool that its business customers can use to analyze and track their current and historical energy use and billing information. The standard package is free, and allows businesses to track energy costs; correlate energy usage with production data, changes in operations, or weather; forecast energy costs for the next year; and spot increased energy usage by faulty equipment.
What a Waste
The other side of the energy question is, are you using power efficiently? As John Havener, energy czar at Pavilion Technologies.
That's a lot of systems to monitor. What uses the most power? "Motors are by far the biggest consumer of electrical power at our site," reports Michael LaRocca, senior process control specialist at Solutia, Sauget, Ill. "Electric heaters for a particular unit operation are second."
The Dept. of Energy agrees. "Over 13.5 million electric motors of 1 hp or greater convert electricity into work in U.S. industrial process operations. Industry spends over $33 billion annually for electricity dedicated to electric motor-driven systems," says a 1998 DOE report. "Because nearly 70% of all electricity used in industry is consumed by some type of motor-driven system, increases in the energy efficiency of existing motor systems will lead to dramatic nationwide energy savings."
Installing efficient motors is one way to save money. Table I shows how much energy electric motors can consume, and Table II summarizes the results of a DOE program where more efficient motors were installed. (See www.oit.doe.gov/bestpractices/motors for more information on the DOE program.)
There are dozens of other ways to save energy in a plant. At Cargill Salt, an Energy Team of workers and supervisors was formed to identify conservation measures. Eric Hoegger, refinery project engineer, says changing lighting systems, installing manual on/off light switches, and a reduction in air pressure throughout the plant helped cut power consumption. Lighting changes alone saved $24,000 per year, he says. Other changes included work practices and moving loads to off-peak hours. Overall, Cargill reduced power consumption by 42% and shaved its peak demand by 52%.
Clearly, if you want to eliminate the energy villains in your plant, you need a plan.
What to Monitor
Several companies will be happy to do an energy program for you. They will analyze your plant, make recommendations, and install the necessary equipment. For example, if you hire Rockwell Automation's Energy Consulting Services to optimize your plant, here's what they will do:
- Tariff Analysis: Using information compiled from energy bills, energy tariffs, and electrical supplier contracts, Rockwell's analysts will identify alternative methods to reduce energy costs, such as aggregating multiple meters or evaluating new supplier, delivery, and tariff options. In other words, they analyze how you are paying for electric service now, and see if they can renegotiate with that supplier or find an alternate source. This may or may not be something you can do yourself.
- Power Quality Studies: Rockwell measures and monitors incoming power to determine the causes of voltage excursions, momentary power losses, phase reversals, and harmonics. They determine the correlation between power quality, premature equipment failures, and the cause and frequency of plant shutdowns. Now this is definitely something you can do yourself. Mark Liemiller, director of marketing at Power Distribution Systems at Siemens, says new power monitors are available to make most of the necessary measurements; then they put the information in a form that is usable. "These can be very basic or quite elaborate devices that monitor and display critical power data," says Liemiller. Table III summarizes the major variables Liemiller says you should be monitoring.
- Plant Energy Audits: Rockwell determines energy consumption patterns in the plant, and identifies equipment and processes that should be modified to reduce power consumption. Again, this is within your grasp. Once you make the necessary power measurements, a host of software is readily available to analyze the data and make recommendations.
The approach seems to work. For example, at Chevron's refinery in Richmond, Calif., Rockwell's energy analysis showed that two pumps in the diesel hydrotreater were oversized, sometimes operating at 40% below their best efficiency points. Chevron installed new medium-voltage drives on a 2,250 hp primary feed pump and 700 hp product pump and saved $330,000 per year.
Monitor Thyself
Engineers have monitored power for decades. "Before the microprocessor revolution, power system engineers recognized three classes of instruments," says Reaz Tajaii, a staff engineer in Power Systems Engineering at Square D. These include digital fault recorders, which obtain oscillograms of fault currents and voltages to evaluate the effect of voltage sags and to construct sequences of events; transient recorders and oscilloscopes, which capture oscillatory and impulsive voltage transients; and power monitors, which report steady-state currents and voltages and provide basic energy and power calculations.
(Poor Power Quality Can Plague Process Industry Drives)
"With microprocessor-based technology, the three classes are slowly merging," he says. "The power monitor is becoming a universal measurement and recording instrument. Power monitors now do much of what digital fault recorders and transient recorders do. In the near future, it is likely that power monitors will take over most of the functionality of these devices."
Power meters at substations have changed, too. Now they are called intelligent electronic devices, or IEDs. Modern IEDs measure phase currents, voltages, power factor, frequency, harmonics, and other data, according to Mike Coleman, North American manager for GE Multilin, a division of GE Industrial Systems. He says the cost has dropped dramatically, too. "Ten years ago, a fully loaded system with metering equipment, oscillography, and protective relays for a feeder would have cost $20,000 to $30,000. Today, a state-of-the-art IED will do all these functions for a fraction of that money," says Coleman.
Not only that, an IED can communicate all this information over an Ethernet connection. "Data from an IED connected to the corporate network can be accessed to see the energy consumption of a particular feeder, or an engineer can access the IED to check currents and voltages or analyze an event," explains Coleman.
Soft Switching Technologies says its I-Grid power monitoring system can be installed for less than $300 per monitor. A web-based monitor plugs into a 120 or 240 VAC outlet and a phone line. It monitors the power line and records voltage profiles for sags, swells, brownouts, overvoltages, and outages, and sends power quality information through the Internet to the monitor owner and to a central server for display on the I-Grid web site.
"I-Sense
Power equipment manufacturers have been embedding power monitoring functions and communications capabilities into panelboards, transformers, and circuit breakers for several years. Such smart power distribution equipment can monitor its own health and communicate with any device that wants the data.
Rick Grove, staff project engineer at IMC Phosphates, Mulberry, Fla., uses such equipment to monitor total incoming power. "GE Multilin 750 relays, which are used to trip incoming breakers, are connected by Modbus to Allen-Bradley PLCs, and then to MSSQL via RSSQL, and then to web servers," says Grove. This means that Grove is getting the data he needs from circuit breakers, then passing it through the system all the way to a web server for display and analysis. "Metering potential transformers and current transformers are mounted within the metal-clad switchgear, and are the inputs to the Multilin 750 relays."
(Power Plant Takes 10-Year AMS Odyssey)
If you have a DCS in your plant, you might be able to hook directly into such equipment. Honeywell, for example, can plug right into third-party multifunction power meters, relays, and motor monitors. "We make nodes such as the Communications Link Module that interface to these meters via Modbus," says Mark Converti, manager of power generation marketing at Honeywell. The link feeds directly into Honeywell's Power Monitoring and Control, Power Emergency Load Shed, and Tie Line Control software packages. "Power system faults are initially detected at the power meters. Later, the cause of the fault and any harmful effects can be determined by uploading the waveform data captured by the meters to our Plant History database."
It might be a good idea to check with your control system vendor to see what type of similar power monitoring packages they offer. You may be able to tie directly into your existing switchgear and panelboards to get the power quality information you need.
If you can't get a free ride from existing power monitors or smart switchgear, you may have to install the necessary equipment yourself. "Most of the time, the measurement is done at the switchgear or distribution center," advises Jay Park, Power Rich System group product manager at ABB. "Each feeder supplies power to different sections or operations of a plant."
Power quality meters and/or IEDs from companies such as Siemens, Square D, Landis+Gyr, General Electric, and other companies are reasonably easy to install at key distribution points. In almost all cases, they have communications capabilities and software support. "All markets use the same devices for data-gathering," says Park, implying that integration is easy.
Portable tools, such as the Square D analyzer shown in Figure 1, can be used to perform power system surveys, track down problems, or monitor units temporarily. They also can be installed permanently. Like the IEDs, the portable units come with software support and communications capabilities.
Analyzing the Situation
The goal of monitoring power is to find places where you can reduce power consumption and save money. Sometimes, the answer is obvious: Replace a motor with a more efficient one. Other times, the situation requires much more analysis.
Fortunately, power analysis software is available from several vendors, including:
- Siemens: WinPM.Net web-enabled software manages intelligent metering and protective devices, analyzes data, and shares energy usage and power quality data across an entire enterprise.
- ABB: Power Rich monitors and controls power in substations and distribution networks. It fits in applications ranging from $7,000 to $3 million, says Park.
- eLutions: AEM/EP Web is a web-based energy information package that measures, manages, and controls energy usage.
- DOE: MotorMaster+, available free from the Dept. of Energy, helps determine when efficient motors will help.
- Honeywell: PMC power monitoring and control software runs on Honeywell control systems. It has three parts: power control; analysis and predictions of energy usage; and load shedding.
- GE Industrial Systems: Envision, to be announced soon, analyzes the costs of electricity and other plant utilities, and generates real-time and historical views of utility costs.
- Pavilion: Energy Center Optimization Solution is a neural-network energy optimization package that analyzes a plant's energy consumption and devises ways to change plant operations to minimize energy use.
Power monitoring can help find all the "low-hanging fruit," as Frank Hein of Abbott puts it. To get huge energy savings, it may be necessary to install an energy optimization system. "Abbott recognized that to get to the next level of savings, we would have to stop concentrating on improvements in individual pieces of equipment and focus on entire systems," he explains. "Multi-unit optimization allows us to focus on the entire utility system and exploit the complexities of our large equipment set to find the optimal operating scenarios."
Nevertheless, you have to start somewhere. Monitoring power is the first step.
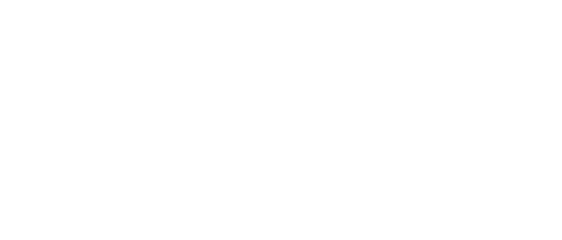
Leaders relevant to this article: