When one is designing the control system of a new plant or updating the control system of an existing facility, the inexperienced might just make a quick I/O count and based on that figure, obtain bids and select the distributed control system (DCS) supplier. That's the wrong approach and is likely to result in endless extras and delays.
In order to develop an operator-friendly control system and guarantee a smooth start-up, one should first integrate the four main components of the total plant automation package: field instrumentation, safety systems, maintenance and simulation segments, and the plant-wide buses and networks.Only after these four systems been defined and integrated, should one obtain bids from the DCS suppliers.Field Instrument Integration
The first step in designing a new plant, should be to specify all the sensors, transmitters, final control elements, local controllers, motors and all other microprocessor-operated devices in the field, that are planned to be connected to the plant's networks or used to send information to, or receive commands from, the DCS system.
If the project is an addition or expansion of an existing plant, all the interfacing between the old and new must also be specified. The three types of interfaces most often used are OPC (OLE for Process Control), serial-to-highway-gateway and serial-to-serial port. Because digital field devices utilize a variety of communication protocols, the manufacturers provide interface cards to the common buses. Such cards are available for AS-interface, ControlNet, Ethernet TCP/IP, Foundation Fieldbus, HART, Modbus or Profibus.
This integration is not simple because some smart field devices are proprietary, and manufacturers implement the same task in different ways. To offer just one of the many examples, some manufacturers describe controller status by two parameters: Auto/Manual and Remote/Local, while others use a single parameter: Manual/Auto/Cascade/Remote-Cascade/Remote-Out.
Safety Integration
The second step in the overall design is to specify the requirements for physical layer redundancy in terms of the number and type of network levels required. It is at this point that one must decide if the plant's safety instrumented systems (SIS) and the plant's control systems will be separate, and, if they are, what kind of interfacing to use.
If the safety and control systems will not be separated, a decision is required on prioritizing, redundancies, hard wiring, etc. Some suppliers provide redundancy by building two of everything in the system as standard, others provide redundancy on an optional basis for power supplies, data highways, traffic directors, remote controller electronics and workstation video terminals. Yet others provide 1 for 1, 1 for 4 or 1 for 8 backup of controller file cards. In addition to the redundancy method, there are also differences in back-up diagnostics and of switchover method: automatic or manual.
Maintenance and Simulation IntegrationThe third step is to specify the requirements for interfacing between the maintenance system and the control systems and to decide on the optimization, simulation, training and commissioning tools that will be used, and therefore, integrated into the total plant automation package. When it comes to process simulation, the process modeling software packages (which will be discussed in subsequent column) can be very large and might reside in separate PCs or might even be accessed via the Internet. Therefore, it is essential that the communication bus network be able to interface with the process modeling software and that it is able to handle the volume of the information flow without interrupting the control functions.Network and Bus Integration The fourth step in the definition of the total plant automation package is to specify the network. In this step the user should evaluate which bus network is best capable of meeting the requirements of the previously listed three steps. HART is becoming the standard for interfacing with analog systems and Ethernet is becoming the standard for most office solutions. SCADA serves to combine field and control data to provide the operator with an overall view of the plant. While, there is no common DCS fieldbus protocol, all protocols use Ethernet at the physical and TCP/IP at the Internet layer. MODBUS TCP is used to interface the different DCS protocols.The major DCS manufacturers accepted the IEC1158-2 fieldbus standard for integrating their systems by providing the means of communication between them. IEC-61804 specifies function block interfaces between technologies, while others can be integrated proxy function blocks, which can map the data from the systems of the other suppliers. The digital communication among these devices should be specified to include not only the requirements of control, but also those of self-diagnostics, maintenance and safety.Selecting the DCS Supplier
The fifth and final step in this process of designing the total plant control system is to send out the whole automation package for bids. Only those DCS suppliers that support the selected network should be invited to submit bids.
In the specifications, it is essential to list all the intelligent field devices and external systems that must be integrated into the total control system. The bid specification should require the DCS supplier to include all that is needed, both in terms of hardware and supporting software to integrate the external devices and systems into the overall control system. Similarly, it is essential to clearly specify what software packages (advanced control, maintenance, graphics, simulation and training tools) must be included in the bid.In case of the required graphics, the bid package should state which of the three IEC 61131-3-approved graphic control languages are to be used. The specification should also list the displays (graphic, detail, faceplate, alarm and event summary, trend, tuning, diagnostic and report), which the DCS supplier is responsible for preparing, and the types of dynamic elements (dynamos), background colors and aliases that are to be used.The specification should also state the division of responsibilities between the user, engineering firm, system integrator and the DCS supplier for advanced control, graphics or other software development, simulation, training and commissioning tasks. The DCS supplier's responsibilities should be clearly stated in connection with training, preliminary checkout, fieldbus testing, safety system and advanced control testing, startup and controller tuning. If the DCS supplier is selected before the control system project's scope is clearly specified, the consequences may be expensive, but cause construction delays, startup problems and compromised safety.Bela Liptak, PE, process control consultant, is also editor of the Instrument Engineers' Handbook and is seeking new co-authors for the forthcoming new edition of that multi-volume work. He can be reached at [email protected].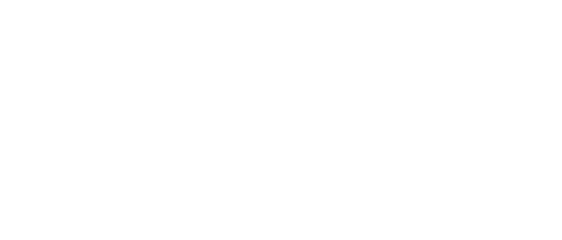
Leaders relevant to this article: