Recently, Reichhold, Inc. implemented an automated batch process system at its Azusa plant in California . The Azusa facility manufactures a broad range of unsaturated polyester resins. These thermosetting resins are used in a wide variety composites applications in the construction, marine, automotive and specialty segments- including California surfboards. The Batch Management and Recipe Management systems are linked to a process information management system (PIMS) to provide operations with a fully integrated batch automation system.In addition production orders are handled by an SAP system, though manually produced for the operators. Using OPC, quality information is passed to and from the PIMS systems to ensure the batch is within specification and allows adjustments based upon laboratory quality checks. An audit has recently been performed that substantiates savings predominately on reduction of off-spec batches and reduced reruns.After a thorough examination of process performance goals and available technology Reichhold's process engineers selected Yokogawa’s Centum CS 3000 batch process system. The installation consisted of three dual-monitor operator stations and a Field control station that handles 166 Analog and 728 Discrete points. Also installed were eight Foundation fieldbus on/off valves.Fully Integrated
By linking batch management, recipe managementand process information management, full S88compliance was achieved. The batch automation configuration spanned from raw material movements up to final loading of finished goods. The plant model is a multi-product, multi-train, multi-path arrangement and it consists of 11 batch units (Unit Instruments) representing the major processing vessels. There are six Shared Equipment Modules providing coordinated control of raw material movements and intermediate material transfers through cross-linking manifolds. Recipe configuration is segregated into groups representing the synthesis and finishing aspects of the product. The operation library consisted of 57 procedural function charts, written with generic modeling, and applied across three unit classes.Dude, It’s S88The automation of the batch is recipe driven per S88 guidelines. The recipe procedure links to unit procedures, which are wholly run in a unit function block that executes entirely in the controller. Dynamic linking of generically written operations with the actual tag names is made when the unit procedure is parsed to the assigned unit. The unit procedure and operations, both represented by an SFC becomes a real-time diagnostic display allowing the operators to view the running of the unit procedure logic, even down to the phase logic and specific line of structured text within the phase and the values being evaluated. The phase logic orchestrates the operation of the equipment and control modules represented by function blocks within the controller. Formula values, such as ingredients, reactor temperatures, and the like are also parsed to the units for use with the operations as run.The recipe formula values are based upon a standard batch size. When executed for a specific unit, the formula values are automatically sized for execution in a specific unit for a specified batch size that comes from the SAP master schedule.Implementation revolved around a recipe-based product sample and analysis procedure providing operations with the time-sequential sampling profile while simultaneously delivering specifications and test methods for the sample to the quality-control (QC) lab. Remote notification is provided by the control system through the site’s PIMS system by signaling to the lab when to come and take a sample, and from the lab when the sample results are available. This becomes a real-time operator transaction through a facility called an operator guide message that pops-up on the operator console when sample results are ready. A simple user interface using graphic panels and an Excel spreadsheet allows both the lab and the operators to view the same data. Based upon the incremental results, recommendations of further additions and amounts are made. The operator then provides for additional charges of the recommended materials to provide a product made to a higher specification.The PIMS system stores all results, including incremental results, while the control system stores the final results. Data management objectives were to provide up-to-date analytical specifications, adjustment recommendations, timeliness and synchronization, accessibility of data, and an organizational structure that facilitates elimination of paperwork by electronic transfer of batch ticket and SAP transaction automation.An opportunity to try out Foundation fieldbus discrete devices, evaluate their ease of use and analyze any savings in installation and commissioning presented itself. Reichhold had previous, successful experience with Foundation fieldbus deploying them to replace traditional analog devices in a material storage and handling system.True to the literature that abounds about Foundation fieldbus, the installation’s cost/return ratio came out about even, despite it being a very small implementation. As many are well aware, Foundation fieldbus devices have a price premium over the equivalent standard analog or discrete device. Although this was an installation of on/off diverter valves in a material delivery manifold, there was still an incremental cost impact for the valve controllers as compared to other discrete oriented networks such as DeviceNet or ASi-Bus. We also chose to install armored cable which also has a premium price over standard twisted pair. However, by eliminating the conduit and using junction tees instead of junction boxes helped offset that cost.Interoperability a Non-IssueInteroperability wasn’t necessarily an issue because we used a single vendor’s on/off valve controller. However, the discrete valve manufacturers are not as advanced in embedding valve diagnostics and statistics within the device function blocks as are the regulating valve manufacturers. As a result, the benefit of Foundation fieldbus for control and diagnostics in the field are not as well defined. In addition, the skill set of the plant for Foundation fieldbus must be higher as devices are networked entries with addresses and identifiers (DeviceID). Thus, diagnostic tools to determine networking issues of the devices is necessary.There were issues with a device dropping off the segment due to an as yet undiagnosed problem. The solution was to have the manufacturer come out and replace the device under warranty. Having local skill sets to troubleshoot and diagnose these problems is necessary in order to adequately maintain the installation. Otherwise, dependence upon the control system and device suppliers is required, and, while they were both quite helpful, it is not a desired circumstance. As a test case, the Foundation fieldbus installation for discrete devices was considered a qualified success and Reichhold has since moved forward with other opportunities to utilize field-level networks.Significant BenefitsBenefits from automating the facility have been significantly reduced re-work of product. In the past, error of material additions to the reactors or blend tanks had been made. With recipe control, this has virtually been eliminated. Charge amounts and additions controlled through automated control via formulas and procedures provide for an error free.Azusa Batch Automation project represents a significant advancement for the company as it continues to enhance its position as an important supplier to the composites market. The improvements achieved through the comprehensive implementation of an S88-compliant Recipe and Batch Management system have resulted in increases in quality, consistency and performance indices of the plant. The technologies employed continue to be expanded within the Azusa operation and to be deployed across the full manufacturing organization of Reichhold.
Tom Craig, with Reichhold for 10 years, is a senior process engineer with responsibilities in instrumentation, controls and automation. Based out of corporate headquarters in
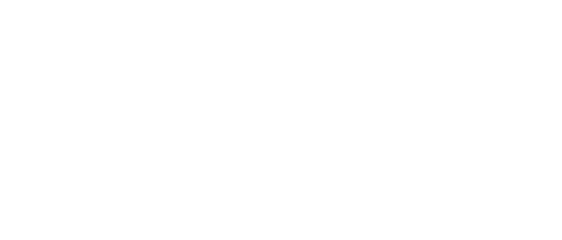
Leaders relevant to this article: