The old instrument engineer leaned back in his chair and opened The Big Golden Book of Manufacturing and began to read. “Believe it or not, children, once upon a time, and not so very long ago, there were people who lived on the C-level of corporations who didn’t think that they needed to know what was happening on the plant floors of their enterprises. There were vendors like SAP who had told them that all they needed to do was to count the goesintas, know their prices, count the goesoutas, and they could run their enterprises swiftly, efficiently and entirely based on monthly reports that were at least 60 days removed from real time.” (See Figure 1 below.)
The old instrument engineer paused and looked up at his listeners. “Nowadays we call those people bankrupts. They got run over by the tide of leaner, nimbler companies that understood that you need to see the information from the plant in near-real time in order to make effective decisions.”
That”s not exactly what’s happened, but it is close. Nor is the tide at flood. The vast majority, probably 80%, of manufacturing plants—and not just in North America or Western Europe, either—still operate entirely based on cost-accounting principles developed in the first half of the twentieth century. Decisions are made based upon cost roll-ups generated from manufacturing and sales reports that take sometimes as much as 60 days to produce. Any problem in the supply chain or in the manufacturing process, therefore, doesn’t get seen at all by top management until it is far too late to do anything about it.
As automation professionals, we know all about control loops. It’s an axiom of loop theory that a loop with too much physical lag time simply cannot be controlled.
The loop lag time is as much as 60 days, sometimes more, so the loop is essentially uncontrollable.
“By putting on-demand KPI (key performance indicator) data in the hands of employees, we’re enabling more efficient and smarter decision-making,” says John Ragone, automation manager, electric production for KeySpan Energy, the largest electrical utility in the northeastern U.S. “That translates to reduced risk and, ultimately, to a significant competitive edge.”
Spry and Nimble—That’s the Ticket
So what happened to get people to think like Keyspan’s John Ragone? According to Fred Fishman, manager of strategic purchasing programs at Techsolve, Inc., a manufacturing assistance organization in Cincinnati, companies “are all feeling the pressure of relentless increases in the prices of what they buy, and the equally unyielding pressure of their customers’ resistance to price increases in what they sell.”
“Profitability is the name of the new game,” Fishman continues.”While selling more is important, profitability is the critical element. To regain lost levels of profitability, manufacturers need to reinvent themselves into faster, more efficient and more agile entities that focus on efficiently converting the voice of the customer into must-have products that their customers wait in line to buy.”
This has been coming for a long time. Companies that saw it coming first broke their unions and moved from the Northeastern “rust belt” to the New South, and then fled to low-cost producer countries like China and the Pacific Rim nations.
Consultants who saw it coming have produced a long line of optimization strategies, such as Total Quality (TQM), worker empowerment, Six Sigma, Kaizen, Value Engineering and other candidates for buzzword bingo.
Yet, as Keith Larson reported in last month’s Control ("Best-practices Gulf is Poised to Widen"), the Aberdeen Group study, “Global Manufacturing: MES and Beyond” indicates that only 20% or less of manufacturing companies are putting in place and operating any of these optimization strategies. As Larson points out, “This best-practices gulf is poised to widen.”
Now why would companies not implement these policies and these strategies, if, as Ragone notes, it gives them a significant competitive edge in an increasingly competitive global market?
Partly, it’s that old booger, cost accounting, again. Costs are rolled up from the bottom, while profit targets and internal hurdle rates are set at the Wall Street analyst level.
Think that’s not true? Rockwell Automation announced in July that third quarter fiscal year profits rose above expectations. The earnings the company reported exceeded analyst expectations by $0.02 per share. Sales grew by 13%. And what happened? The stock lost 10% in overnight trading on the New York Stock Exchange. Analysts didn’t like the internal hurdle rates that were weakened by Rockwell’s investment in new technology and its move into the process industries. If you invest in yourself, it dilutes the stockholders’ gains. CEOs and boards have to be able to visualize gains that don’t appear on the balance sheet, and then sell those concepts to the analysts who determine stock prices.
Partly, it is the old command-and-control architecture of corporations, as originally designed by General Motors’ Alfred P. Sloan. Many companies are full of people who have neither the training nor the capacity to do anything other than rigidly follow rules and procedures. “Unfortunately,” says Fishman, “day-to-day activities can become so tightly woven into the fabric of a business that it becomes difficult, if not impossible, for these businesses to internally recognize the need for change. Intelligent and well-intentioned employees at every level often become protective of their space, function and what they know, typically to the detriment of their employer, the company’s performance and its customers. The added work and the overly embellished products ultimately drain the company’s bottom line.”
Stand and Deliver!
Companies that fled south or overseas have found that their problems followed them. The September 2006 issue of National Geographic (“The Manchurian Mandate”) describes the same failures affecting China’s Northeastern manufacturing belt, once the crown jewel in Chairman Mao’s plan to industrialize China. Far from being the monolithic economic powerhouse often depicted, China is just a few years behind North America and Western Europe in having the same profitability and enterprise control issues we are.
Fundamentally, there is no place to go.
Companies are now seeing that they need to suck it up and move to enterprise optimization strategies, as Rockwell is doing, both internally as a manufacturing company, and externally, with its FactoryTalk software suite, regardless of what the analysts say.
There is a whole potfull of enterprise optimization strategies, among them supply chain optimization, restructuring the distribution chain, and a whole group of manufacturing optimization strategies such as lean and Six Sigma.
But the biggest bang for the buck, beyond doubt, is enterprise asset management, from the plant floor level all the way up to the conception of each plant itself as an asset to be managed. If you can implement it properly, enterprise asset management can put the spring back in your plant’s step, add years to its life and probably keep you going for a while longer too.
Look! It Works!
Way back in the manufacturing dark ages, about 1984, a small co-op of cranberry growers called Ocean Spray decided to implement asset management in an attempt to manage consistent production quality and growth. Today, Ocean Spray has approximately 930 co-op member/owners producing cranberries and grapefruit all over North America, with nine bottling and processing. (See Figure 2 below.)
One of the few products available was Maximo by MRO Software. Maximo has been implemented at all nine North American plants, and it keeps track of close to 24,000 assets; everything from flatbeds and forklifts to controls and field instrumentation.
Harvesting cranberries used to be a manual operation, but with nine plants and almost 1000 owners, Ocean Spray isn’t your grandfather’s berry bog.
“The Henderson [Nevada] facility recently reached a landmark of more than one million hours with no lost time accidents,” says Greg Estermyer, technical services and engineering manager. “This is a testament to our commitment to employee safety and our ability to combat accidents with properly tracked preventive maintenance and safety information.”
Asset management isn’t just about fixing machines and eliminating downtime, either. According to Dave Bone, Maximo network resource for Ocean Spray, asset management “enables us to establish internal and external benchmarks to give the company more purchasing discipline. For instance to clean our processing equipment, we typically purchased chemicals from several external vendors. Maximo allowed us to compare vendor prices and consolidate suppliers. We also monitor usage, and if a facility seems to be using an excess of chemical inventory, we evaluate the root cause.”
Now enter wireless. The wireless asset manager “allows technicians to receive, complete and send work orders from the field,” says Rick Hole, plant manager for Ocean Spray. “They access job plans, safety plans, work order histories and failure. This streamlined process decreases the amount of time personnel spend walking back and forth to input data and eliminates duplicate entries.”
And It Keeps on Working!
“It is important to remember,” says Warren Way, control systems engineer from E. I. DuPont de Nemours Co., Fayetteville, N. C., “that an asset management system is not just a software package, but a whole new way to manage instrument maintenance and support.”
Way should know. He implemented asset management using Emerson Process Management’s AMS Suite and Intelligent Device Manager at the Fayetteville Teflon intermediates plant in early 2001. “Results indicate,” Way reported, “that the asset management system—including the required hardware—paid for itself during startup and commissioning.”
Five years later, Way is still positive about the benefits. “In an operating plant, AMS remains a valuable tool,” he says. “For troubleshooting, when operations reports an instrument problem, the first step is to check AMS. Since startup we have not pulled an instrument or control valve that we did not know there was a problem with beforehand.”
And asset management isn’t just for field instruments, either. “Probably the most complex devices on the AMS network are the control valves,” Way says. “In highly sensitive loops it may be necessary to tune the control valve positioner to accommodate changes in process conditions, and when a loop does become unstable, it is possible to compare the valve response to a previous benchmark. AMS can be used to do this from a remote location.”
So, does asset management pay for itself and continue to generate savings?
“The savings are there, but it may be necessary to change the plant culture in order to get to them,” Way concludes.
The Devil’s in the Details!
When they set about to transform themselves into a world class brewer, Florence Mostaccero, vice president of technical services and business process development for MolsonCoors (Golden, Colo.), says the company spent the first three years of the project designing the change management—they convinced their teams to do it, and only then designed and implemented the hardware and software solutions necessary to make it work.
The problem with the enterprise optimization toolset, as DuPont’s Warren Way pointed out, is that you simply can’t buy the tools. You also have to integrate them into your operations, which is much easier to say than to do.
Just implementing a plan to manage field instrumentation and control valves may not put the pop back in your plants. You will first have to decide if the value is there, and what you will have to do to produce and keep that value. You will have to re-educate both employees and managers into accepting what Warren Way called “a whole new way to manage.”
Once you do that, many avenues to improve operational excellence, not simply asset management, open up to you.
Ocean Spray has expanded into managing its entire supply chain as an asset. DuPont has transformed the way it thinks about calibration and proactive maintenance of field instruments. Keyspan has provided its employees with a way to stay in real-time control of their entire enterprise, regardless of where in the world they are.
“And so,” the old instrument engineer said, as he closed the big book, “that’s how the world of manufacturing changed.”
And Technology Keeps Getting Easier to Use…
Visual KPI software works on any Internet-enabled device.
Key performance indicators can be assigned to the performance of any asset or group of assets and then can be monitored in real time, even if you are on the beach in Mazatlan. According to Ragone, “It took longer to set up the purchasing for the project than to implement the project itself.”
Keyspan is targeting two key groups for immediate deployment: operations managers who need access to data after-hours and in off-site situations, and technicians who can use Visual KPI as what Ragone calls “a tech toolbox” to get specific data about remote locations and site areas.
Now, what if Wall Street’s analysts could carry around any company’s KPI scorecard and see corporate performance in real time?
Latest from Asset Management
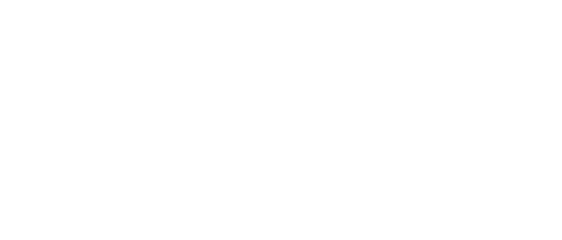
Leaders relevant to this article: