By Jim Montague, Executive editor
To paraphrase Mr. Twain, reports of the demise of the industrial computer have been greatly exaggerated. Sure, recent technical advances are making the desktop PC-in-a-box and many of its traditional capabilities unrecognizable. However, there remain many applications in which operators need screen-based HMIs on or close to machines, production lines or other systems. So rather than eliminating the need for industrial PCs (IPCs) and enclosures, diversifying computing capabilities are fueling an increasing variety of new industrial computing form factors.
Evolution and Diversification
“There’s a lot of confusion in the market these days about what constitutes an industrial computer. Everyone even uses the word ‘ruggedized’ in different ways. So, we try to define an industrial PC by how well it matches its application.” says Ed Boutilier, president and CEO of Stealth Computer Corp.
“What makes an IPC worthwhile is an application’s downtime expense, and this is based on how much it will cost a user to replace the PC itself and how long it will take to transfer its data over to the new PC.”
Figure 1. A user performing real-time flood monitoring and alert services is using UNO-2053E and ADAM-4017 to remotely check water-level sensors in Malaysia’s rivers, and broadcast warnings when high water levels occur.
Mike Berryman, market development director in Advantech Corp.’s industrial automation group, explains, “The transformation of industrial PCs from desktops to all the variants we’re seeing now is caused by open computing technologies—such as Ethernet and Intel’s processors—being driven from commercial settings and into the industrial space. This is why things are moving so fast now. PCs can now use Flash memory to run at 2 GHz without a fan or other moving parts, which improves reliability, lets PCs be located on DIN rails and even lets them look like PLCs. In the past five years, Intel’s low-power, low-heat Centrino processors have allowed builders to put a heat sink on their PCs and run at 60 °C to 70 °C without a fan.”
In addition, while the emergence of Flash memory might seems to bad news for those traditionally devoted to protecting rotating media, Boutilier explains it’s actually good news because it makes IPCs more affordable than ever, enabling users to take computing into new applications, most of which will need some level of protection. For instance, Stealth’s Little PCs are small, fanless units that can be machine-mounted directly.
Monitoring Wind Power, Metallurgy, Envionments
End users are employing Advantech Corp.’s UNO industrial computers to migrate from larger computers to smaller PCs in a variety of applications. The firm reported on them at its recent 2007 World Partner Conference in Shanghai, China. For example, a 5,600-megawatt wind power generation facility in Germany recently used Advantech’s UNO-2160 embedded automation PC to monitor the status of its generator and communications with its field-based PLCs and fieldbus equipment. This fanless PC checks and controls the generator’s turbines and stores data in a small database.
A Malaysia-based user performing real-time flood monitoring and alert services is using UNO-2053E and ADAM-4017 to remotely check water-level sensors in local rivers and broadcast pre-recorded warnings when high water levels are reached (see Figure 1). Finally, one of the largest rolled-aluminum producers in the U.S. updated its HMI software using UNO-2053 to deploy Microsoft’s Terminal Server technology. This allowed it replace its former PCs with thin-client terminals running ThinManager software, and communicating via a 100 Mbps fiber network.
Preserving Protection
To give users the access they want, but maintain the seals and protection they need, Nathan Espinosa, Hoffman’s product manager, reports his company’s enclosures are adding USB ports, an access door right to the CD drive, touchscreens instead of keyboards and pushbuttons, and more displays on pedestals and pendant arms, so workstations won’t have to sit on the floor. “As PCs get smaller and thinner, as they’re mounted in more different ways and locations, and as they gain more entry points, all of these create the need for more different types of protections,” says Espinosa. “For example, we just got a new Amada press in for our own metal stampings, and it still has its stand-up floor cabinet, but the PC sent to run it is in an HMI frame installed in the top of the cabinet.”
How to Decide What IPC You Need
To find and implement the most appropriate industrial PC for their applications, Mike Berryman, market development director in Advantech Corp.'s industrial automation group, says users need to consider the following questions:
|
Scott Kortier, marketing, sales and communications manager at Pro-face America, adds, “We laugh when we hear that Dell is supposedly the most used industrial PC because some users may not be looking at their true costs of ownership and getting their PCs back up to speed. They can install a $400-$500 PC in an enclosure rated to only 30 °C to 35 °C. However, when it fails on the plant floor and it takes eight hours to get it and the application going again, then that downtime may cost a lot more than some users might think. If users don’t know the actual cost of their downtime, then they can’t make an informed decision about what kind of PC and protection they need.”
Self-Monitoring and the Future
Just as industrial PCs help monitor industrial processes, some innovative users are turning them around to periodically check the PCs own health. For example, Pro-face recently launched its Reliability, Availability, Serviceability (RAS) program to monitor the health of its industrial PCs locally or remotely. RAS will check a variety of operating parameters, including internal temperature, hard drive, fan speed and flat-panel backlight, and then output alerts or alarms from the PC to a stack light, pop-up message on another screen in a central control or elsewhere via the Internet.
IPCs aren’t likely to disappear in the future, but their forms and functions will be driven by users’ needs and whichever software and hardware solves these problems best. Some developers are finding ways, such as using USB ports, to reduce internal hardware and remove much of the bus wiring. “Boards are being extended further out to the edge of some PCs, which mean less wiring, but more solder,” explains Berryman. “So even if there are fewer PCs on the plant floor in the future, there will be more computing and data processing going on there.
Under Power, In the Mill, Up in the Air
Just as the hat makes the man, the appropriate housing may define the industrial PC. For example, National Instruments reports users are employing its PXI PC-based platform and LabView software in several unusual locations.
- Testing and certification organization, KEMA Netherlands B.V., synchronized PXI-6133 boards and PXI-5122 digitizers to develop a faster-acquiring transient recording system that measures three-phase AC currents and voltages when testing for faults up to 1,060 kV peak at 63 kA.
- Pitel Engineering developed a PAC-based gauge-monitoring system using PXI, Compact PXI and LabView software to check and control metal strip thicknesses in cold-rolling steel mills in Thane, Maharashtra, India. This new system provides micron-level deviation from setpoints as an analog input to the PXI hardware, which enables higher-precision monitoring, faster response times than PLCs and allows 24/7 operations.
- Boeing reports using PXI controllers and chassis, FPGA dynamic signal analyzers, and LabView to build a process data acquisition system (DAQ)—including 600 ground-based microphones—to test the effectiveness of designs for reducing commercial jetliner noise during takeoff, landing and sustained flight. Boeing’s new DAQ solution is distributed across multiple PXI chasses, synchronizes all channels, provides high channel count with full, simultaneous bandwidth and reduces required cable.
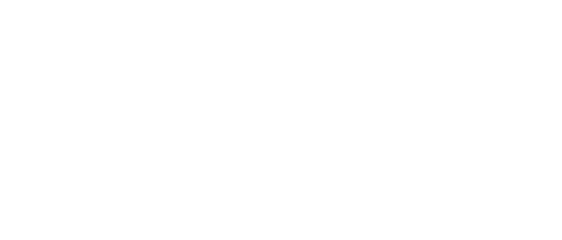
Leaders relevant to this article: