“Our customers were being asked to increase production with the same number of employees, making each person responsible for more automation and more data,” said Roy Tanner, System 800xA marketing manager at ABB, in his systems capability orientation session this week at ABB Automation World. “Global competition was also forcing our customers to re-evaluate their business models to accommodate continuous improvement,” he added.
“Global competition was forcing our customers to re-evaluate their business models to accommodate continuous improvement.” ABB’s Roy Tanner on the driving forces behind the development of the System 800xA extended architecture.
ABB customers’ needed a system that could interface with many different control platforms and applications in an integrated fashion. ABB’s answer was the System 800xA. The customer response has been overwhelmingly positive, with 3,700 systems purchased and deployed since its introduction in January 2004.
System 800xA provides a common platform that can interface easily to virtually any hardware or software automation product, Tanner explained. System 800xA provides seamless links to ABB controllers from other ABB control systems, including the MOD300, Harmony, DCI and Melody. OPC data sources also are accommodated, as are controllers from other vendors.
System 800xA facilitates integration of these controllers and data sources to a broad range of applications for functions from ABB and other providers, such as production management, information management, asset optimization, device management and ERP.
In fact, ABB’s IndustrialIT technology makes it possible to create a certified link between it and virtually any controller, data source or application, Tanner said.
System 800xA is designed with eight core functions: operations, engineering, control and I/O, information management, safety, device management, asset optimization and production management.
The operations function provides quick, flexible and secure access to information via a customizable user environment. “Advanced trending, sophisticated alarm management and powerful messaging capability help multiple users make sense of all available data,” commented Tanner.
The engineering function lets users focus on value-added engineering instead of cumbersome programming. Intuitive graphical design speeds screen creation and makes the process come to life for operations personnel.
The fully integrated engineering environment provides quick development and convenient re-use of objects. An object is created once, and modified instances of it can then be used throughout the control program. These objects contain not only control code, but also graphics and interface information. “Changes made to an object automatically reflect through each instance, saving development time and preventing errors,” explained Tanner.
Control and I/O are scaleable for cost-effective deployment in systems of any size, Tanner added. Process and safety I/O can be mixed and matched as needed, even on the same bus structure. Wide-ranging control functionality and fault tolerance provide reliable control of virtually any process.
Information management functions include a historian to store data and tools to make this data available across a wide range of operator interface platforms. Intuitive presentation of data allows for informed decision-making across the enterprise.
The safety function provides a host of options to accommodate both standard process and safety control in an integrated system.
Device management accommodates a variety of smart instrument protocols, including Foundation Fieldbus, HART and Profibus. Relevant device status, diagnostics and process information can be quickly accessed via pre-configured device objects.
Asset optimization extends far beyond smart instruments to encompass control networks, control loop performance, computer health and equipment performance. All of these assets can be optimized to reduce downtime and mean-time-to-repair. Root-cause analysis and recommended actions are other key attributes of the asset optimization function.
The production management function lets users easily configure recipes and procedures. Batches and campaigns can be scheduled, monitored and controlled. Batch information is seamlessly collected and stored for record keeping and analysis.
Recent System 800xA extensions include support for process analytical technology (PAT) applications and a thin-client interface. “ABB is continuously updating and improving System 800xA,” Tanner concluded.
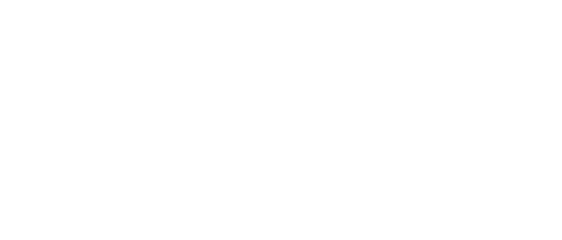
Leaders relevant to this article: