Greg McMillan and Stan Weiner bring their wits and more than 66 years of process control experience to bear on your questions, comments, and problems. Write to them at [email protected].
Greg: Do you remember going into a control room and noticing right away something was wrong—such as the uneaten doughnuts or the food burning in the kitchen?
Stan: You knew it was bad if the operators were too busy to enjoy the finer things of control room life.
Greg: Oh, the memories of loops gone bad and processes gone wild! Fortunately, we’re getting good at forgetting. What were we talking about? Oh, yeah, how to deal with a gyrating plant. The first step is to tune the loops, but without the loop monitoring and learning tools, you have to wait until things calm down to do some step testing if the operator is fighting just to keep the plant running or the batch going.
Stan: You can check for bizarre tuning settings without interfering with the operator. The reset time setting is often too small on columns, stills, reactors, crystallizers and surge tanks. These unit operations are integrating processes or behave like integrating processes. Because of a process time constant so much larger than the loop dead time, the process response looks like a ramp in the time frame of interest. You can frequently get these loops to settle down by simply increasing the reset time by a factor of 10. If there were a bunch of oscillating loops, the root cause is often the loop furthest upstream. By far the most frequent bad actor is a level loop on a surge tank. Here the reset time is typically 100 times too small, causing slow rolling oscillations that ripple through the plant. Really bad news is a disturbance upstream with a period of oscillation close to the period of a loop, because the result is resonance where the oscillations get in phase and amplified by the loop.
Greg: Another common source of oscillations is a valve with excessive stick-slip (resolution limit) and backlash (dead band). It’s a valve instead of a tuning problem if the oscillations have a constant amplitude and period for a given reset and gain setting. Such limit cycles are mostly caused by valves, provided the controller is not banging between its output limits or the flat portions of a titration curve. Stick-slip causes loops with reset action to oscillate regardless of tuning settings. For stick-slip, the amplitude of the oscillations is relatively constant, but the period increases as the reset time increases and the controller gain decreases. Dead band causes a similar problem for a loop with double integration (integral time setting for an integrating process or integral time settings in both controllers of a cascade loop). For dead band, the amplitude in the process variable oscillation is inversely proportional to the controller gain. The period of a dead band oscillation is proportional to the reset time, like stick-slip, but the inverse relationship to controller gain is weaker.
Stan: A particularly confusing situation is when the reset action of a primary loop is faster than the reset action of a secondary loop, or when the reset action of any loop is faster than the slewing rate of a control valve or the velocity limit of a variable-speed drive. The loop looks fine for normal operation, but goes unstable for large load upsets or big set-point changes. The dynamic reset limiting option available today in a DCS can prevent the problem of the controller output outrunning its manipulated variable.
Greg: If a periodic disturbance is faster than the loop, the best a feedback controller can do is nothing. By the time it does something, it’s too late or puts the loop at risk for resonance. Really fast disturbances are better known as noise. Signal filters can make a measurement appear to be smoother and reduce the reaction of the loop, but the correct solution is to get rid of the disturbance. If this isn’t possible, the next best thing is to slow down or attenuate the disturbance and speed up the loop by getting rid of loop dead time and using a higher controller gain setting. The biggest source of dead time is often the time it takes for the controller to work its way through stick-slip or dead band. A high controller gain reduces this dead time.
Stan: Tuning and valve problems start out as flow disturbances, but can become concentration, pressure or temperature disturbances as they work their way through the process. Batch operations, start-ups, shutdowns, operator actions, interlocks, discrete process actions and level switches can cause big, abrupt and disruptive changes in flows.
Greg: The best way to slow down and reduce the amplitude of a concentration disturbance is to take advantage of a back-mixed volume between the disturbance and the loop. The mixing can be caused by turbulence from agitation, boiling or recirculation. The attenuation (reduction in amplitude) is proportional to the period of the concentration disturbance divided by the residence time of the volume (liquid inventory divided by total feed flow).
Stan: The largest unknown source of concentration disturbances is the raw materials. The culprit could be a change in the concentration of a key reactant or a contaminant that degrades process operation. Unfortunately, the composition of these raw materials may not even be measured in the lab. Furthermore, feed tanks usually don’t have agitators, so the only smoothing from the unloading of tank cars is from flow-entry turbulence and the slow migration of components from areas of high-to-low concentration.
Greg: Liquid pressure disturbances are extremely fast. A volume with a vapor head space is the best way to attenuate these disturbances. Oversized pressure regulators are an insidious source of fast periodic upsets when the field-pressure regulator action and its pressure are not monitored in the control room. Pressure loops with analog or fast digital scan rate controllers and variable-speed drives can catch up with fast nonperiodic pressure upsets. Liquid pressure disturbances turn into flow disturbances across any flow resistance (e.g. valve, nozzle, piping or inline element).
Stan: Finally, measurement noise, drift and resolution are disturbances for all types of loops. Measurement resolution problems are mostly history, but sensor noise—particularly drift—are a continuing source of problems. Disturbances that directly get into the process variable for a control loop are especially disruptive because there’s no filtering of this disturbance by the process-time constant.
Greg: Changes in weather are generally slow, but can be relatively fast and are notorious for affecting the air compressor suction temperature and distillation column reflux temperature. There is nothing like a cold rainstorm on uninsulated lines to perk up control room activity. Even wind and sun can be the source of weight changes in a load cell installation. Wind, sun and shade temperature, humidity and precipitation should be historized and available for trending with the loops.
Stan: Changes in ambient temperature can cause a drift in those sensors affected by sensing line, connection or housing temperature. A severely coated sensor shows up as an attenuated, but much slower and less damped oscillation.
Greg: The story in trend charts is more in the trend of the controller output than its process variable. For stick-slip, the classic saw tooth is evident. For periodic disturbances, the oscillation in the controller output is often larger. The controller output could be hitting output limits or wandering along the upper, almost-flat installed characteristic of a control valve. Load disturbances and measurement drift show up as a shift in the controller output. Sensor drift or weather-induced changes are seen in the controller output. The controller output through the reset and rate action of the controller has important information on the type, persistence and speed of the disturbance.
Stan: I don’t understand why multivariate statistical process control (MSPC), focuses on process variables to the exclusion of controller outputs. I also don’t get the lack of recognition of the fact that some MSPC data alignment techniques may mask changes in oscillation periods and the duration of key sequences in a batch cycle, which are indicative of measurement and valve problems. Even more important, changes in the time durations of key portions of a batch sequence indicate changes in chemical or biological reaction rates and, consequently, changes in the secret concentration profiles.
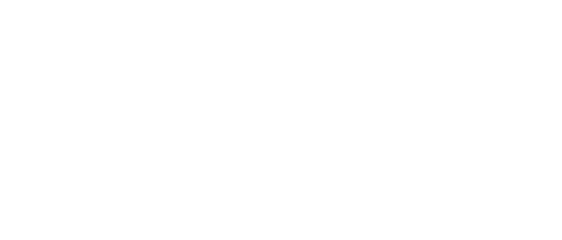
Leaders relevant to this article: