By Bob Sperber
Process analyzers havent changed much for more than a half century and neither have the pipes and fittings used to transport samples to and from them. Likewise, things didnt change much for Rajko Puzic, instrument engineer at ExxonMobils Imperial Oil Products and Chemicals Div. in Sarnia, Ont., Canada, for more than 27 yearsuntil he discovered a smarter mechanical mousetrap.
That mousetrap is the New Sampling/Sensor Initiative (NeSSI) that seeks to standardize sample transport, digital networking and breakthroughs in analyzer miniaturization. There are three parts, or generations, to NeSSI. Generation 1, defined by ANSI/ISA SP76.00.02-2002, specifies the modular layout of fluid-flow channels and mechanical fixing holes to connect 1.5-sq.in. modular components to a substrate. The ISA SP-76 working group is in the midst of a Gen 2 standard that will provide an intrinsically safe, digital NeSSI bus that will interface with Ethernet and/or existing field and device buses. Finally, a third generation focuses on providing a standard for developers in the emerging lab-on-a-chip and broader microfluidics and microelectro mechanical systems arenas.
Whats available today is a finished Generation 1, with products widely available in the marketplace. Even without the additional layers of standards, users are justifying their NeSSI investment based on sampling benefits such as streamlined design and installation, reduced space requirements and simplified maintenance. Imperial Oils refinery and chemical plant in Sarnia provide a testament to these benefits; of the roughly 500 process analyzers there, Puzic says at least 60% have been connected to NeSSI-based sampling systems in last few years. Other users validate this success.
Speeds Design, Fabrication
In a conventional sampling system project, the typical user might work with a designer to build a bill of materials, lay out the system and generate construction drawings, then send them out for bids. But using NeSSI components to design systems for a plant in Malaysia, Matt MacConnell, analyzer systems technology manager for Air Products and Chemicals Global Engineering outside Allentown, Pa., just worked with the supplier to build what I wanted, and once I got those drawings, I just sent those to the field contractor who interconnected the system.
MacConnell says he didnt have to buy 50 or 100 pieces. With these NeSSI systems, you can cut your bill of materials down to just one or two parts. It pretty much eliminates the designers time, he says.
As with any sampling system, users have to do their up-front engineering. But once they know their system requirements, any up-front price premium paid for NeSSI components is way overcome by cost savings in the fabrication alone, says Steve Jacobs, development associate chemist at Eastman Chemical, Kingsport, Tenn. Research he did some time ago showed NeSSI cuts $5,000 to $25,000 on fabrication alone, depending on the size of the installation.
Three companies currently supply substrates along with other components: Parker Hannifin; Swagelok; and Circor. Companies or end users can assemble the systems using dedicated software configuration tools.
The software is instrumental in reducing up-front design efforts. Circor bases its web-based (and downloadable) configurations on Microsoft Visio. All substrate suppliers offer roughly similar software applications to generate process P&IDs and schematic assembly diagrams automatically from the users bills of material. These software tools generally follow modern expectations by providing a graphical environment with libraries of components from substrate parts to flow indicators and controllers, pressure regulators, valves and pumps from major instrument suppliers.
Saves Precious Space
Users report that NeSSI sampling systems occupy 30% or less space than conventional systems, though there is wide variation because space might not have been a guiding factor in old installations.
Sample heating is more compact and efficient because each supplier provides modular components that directly heat the NeSSI substrate, as opposed to the using radiant heating on larger, conventional systems. Shrinking the footprint of systems also allows cold-climate plants to reduce the size of heated enclosures.
While sample systems dont typically determine the need for constructing analyzer houses, in some cases analyzers and sampling can be co-located with the sample, which is beneficial for space saving, among other things.
And boy, if you have to start dropping analyzer houses in, you start getting into some serious money, says Eastmans Jacobs. With most of these [NeSSI] systems, I can just wrap some environmental control around them or an enclosure if we need it.
In replacing a bunch of systems in one of Eastmans polymer processes, Jacobs replaced two panels measuring roughly 6 x 8 ft with one 3 x 4 ft enclosure that added a lot more functionality than the old system, including automatic sensing of flows, automatic back-flushing and cleaning where none of that existed on those other two boards. He adds that he would have had trouble trying to find a place to put it on the old system.
Tell me: How many refineries have been built in North America in the last 10 years? None, says Puzic, stressing the very precious real estate refineries sit on. He says a four-stream liquid sampling design could be shrunk from a 6 x 6 x 2 ft deep enclosure to something perhaps 10 times smaller, depending upon the space efficiency of an older design.
Lowers Volume for Better Results
Along with its smaller footprint, NeSSI systems greatly reduce piping. Less piping, a shorter flow path, lower dead volume, less liquid circulating in the lines all add up to high reliability and faith in sampling.
These characteristics lead to a reduced risk sample contamination, because theres less surface area in contact with your sample, says Air Products MacConnell, which in turn has substantially reduced the quantity and cost of treatments required for wetted surfaces in moisture and sulfur testing.
Reduced contamination risks and greater overall reliability lead users to entertain the notion that NeSSI might improve the accuracy of analysis, though this has not been quantified. But Puzic cites greatly improved analyzer performance in some cases specifically because of the flow path that we can accomplish using NeSSI system. We can manipulate that liquid more effectively, and we dont end up with huge amounts of tubing and fittings or a million components that have to be put together.
Users agree that lower dead volume can significantly speed analyzer results, depending on the application.
Improves Maintenance, Reliability
When components or lines need removal or replacement, plug-and-play standardization saves time and reduces the risk of leakage. And, while substrate sales reps on the street naturally tout their systems over others, end users agree that all NeSSI-based systems represent a leap forward for maintaining and replacing components.
Since there is no connecting and disconnecting of tubing, it takes just a minute or two if I want to unscrew four screws, take a valve out, replace a couple of o-rings, put the valve back in and boom! Job done, Puzic says, versus half an hour or more on a conventional system. He adds that this reduces analyzer downtime as well as the cost of parts inventories because we have standardized components.
With a conventional system layout, an inefficient design can cause extra maintenance time and labor if tubing has to be taken apart in order to access or replace parts.
But the greatest justification may come from better management of risk.
All it takes is preventing one analyzer downtime event, and youve covered your up-front capital, even without getting into calculating your operational cast, says Jeff Douglas, director of marketing for Circor.
Consider the lag time between an alarm and its associated, corrective maintenance activity: In that period, youre either producing off-spec product, or it goes into a recirculation loop. Or worse yet, in an older plant that doesnt have one, you just keeps making bad product, he adds.
Even if NeSSI sampling systems cost twice as much as conventional systems, Douglas says plants trying to save $5,000 on a $10,000 sampling system are penny-wise and pound-foolish when a plant realizes it just blew a fussy $80,000 analyzer to save $5,000 on a $10,000 sample system.
Pays for Itself
Douglas came to this conclusion during a presentation to a group of analyzer technicians. There must have been 20 incidents in that two hours. He says plants that operate in firefighting mode are most likely to resist NeSSI adoption because if theres no fire, people may be thinking they wont be needed. Extending this logic, it appears that NeSSIs value may be best justified when viewed from the reliability engineering perspective of preventing a costly or catastrophic failure.
While early estimates placed up-front NeSSI costs at twice that of conventional systems, the price now getting to be about equal, says Mel Koch, executive director for the Center for Process Analytical Chemistry and host organization to NeSSI development since 2000, and it may well be lower considering life-cycle costs.
Users agree, placing up-front hardware costs 20% to 50% higher, but less after calculating the savings. Even Swagelok, which has had a reputation as the highest-priced substrate provider, has seen a significant decrease recently on the initial costas much as 25% to 30%, depending on what kind of system Im quoting, said one distributor.
Koch says plants worldwide are jumping all over NeSSI and while North American companies have been slower to adopt, they are now realizing that NeSSI will be very, very big.
Halfway to Process Control: Gen 1.5
Not content to wait for a full Generation 2 standard, users are moving ahead to integrate their NeSSI systems to process operations in projects dubbed Gen 1.5 by developers.
Puzic says most of the NeSSI-based analytical measurements are being used for process control, safety or environmental measurement, connected by traditional 4-20mA analog writing to PLCs. Eastman Chemical, too, is moving ahead with hard-wired PLC connections and will hang a HMI onto it using Ethernet. Its not a self-describing, full-blown Gen 2 solution, but we have a need, and Im not going to wait! says Eastmans Jacobs.
Air Products MacConnell is looking into integrating NeSSI with Profibus control networks running in hydrogen processing plants using Siemens distributed controls. He says he doesnt care if a full Profibus solutions carries a reasonable up-front premium as long as it works, although most in the industry are developing more streamlined and lower-cost solutions. The likely candidates are an intrinsically safe version of the CAN protocol and/or Siemens Applied Automations I2C bus.
Parker Hannifins Steve Doe, analytical market manager, describes a 1.5 prototype that includes a sensor and solenoid administration module using an intrinsically safe CAN bus to connect to Ethernet and possibly other field/device networks. In cases where additional logic is required for control, for example in a moisture or O2 measurement, we can also populate the module with a PLC, he says. Parker, which has sold systems to all the users cited here, is also developing interface software for local or remote workstations.
But Gen 1.5 is only a stopgap, says Rob Dubois, a process analytical consultant from Sherwood Park, Alberta, Canada, and a pioneer in the development of NeSSI systems.
Generation 1.5the use of 4-20 mAespecially in hazardous classified areas should be considered a stopgap. For compact systems it can be costly, take up valuable space, have limited flexibility and be incompatible with the emerging class of microanalytical Generation 3 devices. Not until the Generation 2 purpose-built digital bus for process analytical systemsboth sensors and actuatorsare widely used can we make the leap from manual to automated, smart systems, he says. The first working examples of Generation 2 buses are essentially extensions of the digital busesalbeit modified for use in hazardous areasalready working inside of smart analyzers, such as process gas chromatographs. An end user, when purchasing a gas chromatograph, may want to consider specifying a NeSSI-bus-enabled GC integrated with a NeSSI sample system to serve as an entry point into Generation 2.
Generation 3 is ongoing and concurrent, with oxygen, moisture, refractive index, UV and n-IR spectrometers on the market today. Miniaturization prototypes are now making the rounds on larger instruments including gas chromatographs.
Bob Sperber is a freelance writer and former Control editor.
Latest from Home
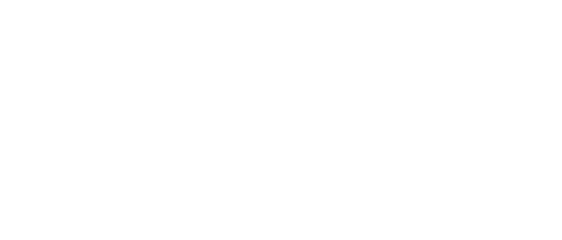
Leaders relevant to this article: