Greg McMillan and Stan Weiner bring their wits and more than 66 years of process control experience to bear on your questions, comments, and problems. Write to them at [email protected].
Greg: We continue our discussion with veteran engineer, Joe. Last month, we learned about some of the more unique demands in the pet food processing industry, the need to fix basic control systems before tuning and venturing into APC, and the importance of the technician and his/her education.
Stan: What have you done to help the operator get the most out of a control system?
Joe: In one control room, the operators were running the plant based on controller outputs being at a certain value by operating in manual or imposing restrictive output limits. The valves didn't have positioners, so controller output data was meaningless. One operator took pride in this methodology, and felt his presence was critical. Even after one of our "tune up" projects on his bank, he didn't feel comfortable leaving his comfort zone. We had a different operator fill in while that operator left on vacation. The new operator was able to push production past previous limits by actually using the automatic control modes.
You can't discount operator knowledge, even though in this case it did not play out properly. There is often valuable information. You just need to be able to interpret root causes. I worked with another operator who has a great understanding of the physics of what is happening inside the extrusion process. He goes to extrusion conferences on his vacation time. I have seen him work his way out of problems that other operators scratch their heads at.
Greg: How do you get useful knowledge from the operators?
Joe: I am never quite sure how to qualify the information at first. A lot of it is anecdotal stuff. Often operators will want to feel you out. A lot can be said about the attitude you take into the control room. I go in assuming the operators know more than me. They have been living with the plant for 30 years or more in some cases. They are sometimes wary of you and not willing to share. I scale back propositions until I have gained a mutual respect. You need to be able to have a conversation such as, "Have you ever tried this?" Give them a piece of the idea. This approach works with 95% of the operators.
You always want to get a connection with the most experienced operator. If anything hiccups, all eyes are on that operator. We are generally pushing equipment limits making operability challenging.
One operator was bound and determined that the automation system was not going to work in his plant. I tried to gain his trust. The best I could get after training with a simulation was, "Doesn't suck as bad as I thought it was going to." I took this as a win.
Stan: What can you do for the operator besides the personal interchange of knowledge?
Joe: What we can do for the operators is not blast them with alarms. We need smarter alarms. Interfaces are designed to show a lot of data. My pet peeve is digital values to the third decimal point. Operators can get obsessed with fluctuations in the last digit. When digital meters were first introduced, an operator complained the process was oscillating. I put a piece of black tape over the last digit behind the bezel. The operator thanked me for stabilizing the process. Inundating the operator with too much information is another problem. Engineers like to add information for their purposes on the screen. I prefer to create additional screens aside from the operator interface for that type of information.
Greg: Dashboards are the hot new thing. Is this the best we can do? I'd think intelligent trends showing where the process came from and where it's going to would offer more knowledge (see "Are We Misleading Our Operators?" entry on my website at http://modelingandcontrol.com/2011/03/are_we_misleading_our_operator/).
Joe: An operator may be responsible for 10 to 12 extruders, each with six to 12 loops. As you switch ingredient bins, you may get differences in fat or protein content. Even though these differences are within allowed ranges, they can cause differences in the cooking process. We are analyzing real-time data from the process, and created views of key values that affect quality with intelligent, sliding, 15-minute time windows.
We have developed these key indicators from palatability tests. The operator gets a score card based on these key process indicators on his operating screen. Indicators out of range or exceeding a coefficient of variance trigger changes in background color of digital values. Bar graph displays did not seem to prove useful to the operators. The operators can go to a trend chart to see a history of what specifically is going on if the window indicators show a shift in performance.
Stan: What do you enjoy the most?
Joe: I really enjoy getting into the process as much as possible and developing an in-depth understanding of the meaning of data. I am fascinated with the people who keep the plant running. I seek to understand and spread the knowledge (sometimes tribal) of the fringe groups. It is often far from what we see in technical societies and publications. I think you should learn something every day and something from everyone.
Greg: I think we're similar in that we're both motivated to gain a deeper knowledge, and then share what we learn on a more conceptual level (see "Top 10 Limitations—Concepts," http://modelingandcontrol.com/2011/07/top-ten-limitations-%e2%80%93-concepts/). How can you extend your knowledge to others in our profession?
Joe: Time is major limit to sharing with a larger community. It is difficult to find time unless I give up all my outside interests. I guess I always thought of myself as a practitioner trying to apply the knowledge of others. Over time, I suppose I developed my own thoughts and ideas, never considering that they were of value outside of my own sphere of influence. The trick is to formulate the knowledge in a way that's useful to others in another context. Abstract it to a level that is more of a common denominator.
I am going to try to figure out a way to maybe capture some of these small pieces of what might be useful information to others, and get it out there in some useful form. I think ISA is a great forum for that. I'm just not sure of the mechanism within ISA that would work. I think your conversation/interview approach is a great idea. I was thinking that maybe once a quarter a topic could be thrown out there to a group of "old timers" to see what kind of response you get. Maybe that would be a useful thing.
Stan: What is ISA doing for you now?
Joe: ISA seems to be aimed at the wet chemical business. I looked there when I was charged with coming up with the safety instrumented systems initiative for our company. The main difference was in the equipment and type of processing. We are more machine-oriented. It was hard to find information within ISA that was applicable to the types of things I was trying to accomplish. I talked with Paul Gruhn about it during class I took from him, and he agreed that there wasn't much on the subject within ISA. Part of this I determined, as I investigated further, was because of the differences in the way that machinery safety standards are used in the United States versus the European community.
Top 10 Things You Shouldn't Say When You Enter a Control Room
10. Does this hard hat make my butt look big?
9. At the last plant I was in we always did it this way.
8. I added alarms to each loop.
7. Does that flare out there always shoot up that high?
6. Ooooh! Did you mean to do that?
5. Can't somebody do something about all those alarms?
4. We just downloaded the version released yesterday
3. Here, I will show you how to operate this plant.
2. Are you ready to put all your loops in Remote Cascade?
1. We want a "lights out" plant!
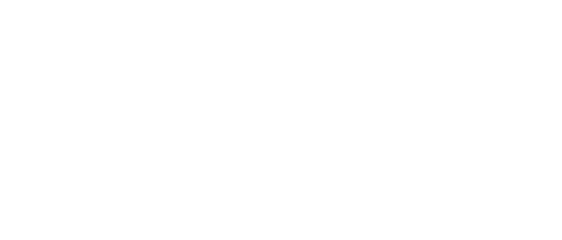
Leaders relevant to this article: