From the very beginning, HART Communication filled a crucial need for digital communications from instrument to control and maintenance systems. As the needs of the process industries have grown and changed, HART Communication has evolved to meet those needs, and is clearly the choice of the process industries for the communications protocol of the future.
HART in the Beginning
The Highway Addressable Remote Transducer (HART) Protocol became an open protocol in 1990; HART Communication Foundation (HCF) was established in 1993, multiple vendors began offering HART communication as an option, and eventually it became the standard I/O solution.
"As it relates to digital field communications for instrumentation," Michael Robinson, solutions business manager at Endress+Hauser notes, "HART has been in the marketplace as a reasonable solution for a substantial amount of time. The market has embraced the technology, and the implementation costs are relatively low for either a brownfield or greenfield installation."
Shannon Foos, process segment manager, fieldbus and asset management, at Rockwell Automation says, "Coming from the world of electrical control based on 4-20 mADC, HART provides added value by superimposing digital information on the analog loop-- an incremental step above the traditional 4-20 mA device. This incremental step was easy for both users and automation vendors to implement."
Robinson continues, "If you also consider that the technology is integrated into 'de facto' PV/CV field signal technology, and that most 4-20 mA instrumentation outputs are supplied with HART communication as a standard option with no additional cost to the user, it does not surprise me that its adoption has been significantly more successful than the other bus technologies or protocols."
Gary Prentice, national sales manager for Moore Industries International, puts it bluntly. "Even the earliest versions of HART filled the need to manually perform configuration and diagnostics remotely. Many (HART) users have not outgrown this basic need. More sophisticated users take advantage of the multiple dynamic variables with a single process penetration and the online diagnostics. Most users' needs continue to be met with HART, and they are comfortable with the technology."
In 2012, HART has more than 35 million installed instruments and devices, far surpassing any other process fieldbus. Garrett Schmidt, wireless product manager for Phoenix Contact explains why. "HART is the world leader of field device protocols because it is backward-compatible to standard 4-20 mA. You can use HART instruments without upgrading the control systems."
Mark Nixon, lead system architect at Emerson Process Management, says that the reason HART has more than twice as many installations as its nearest competitor is, "Simplicity. The industry has been using 4-20 mA and HART for over 20 years, so there is a wealth of experience to draw on and a very well-defined set of tools and processes that have been developed. WirelessHART simply built on the success already achieved with HART. The HCF and its member companies continue to drive HART and its related technologies for customer value. The standard continues to evolve so that real-world problems can be solved in a standards-driven manner. For example, the latest release of HART includes support for discrete-oriented devices such as on/off valves."
Jeff Dobos, ProComSol president, says HART is "inexpensive and easy to use, makes use of existing wiring in plants, and cost and installed base will keep it dominant for a long time."
Thomas Holmes, president of MACTek Corporation, sums it up. "HART is here to stay because no other field communication solution can cover the wide range of devices and applications—wired and wireless, analog and digital. Since HART includes the 4-20 mA signal, it is the only solution that works with the existing installed base of control, safety and monitoring systems and the installed base of measurement devices."
Figure 2: The digital signal is superposed on the analog signal.
The Basics: How HART Works
There are three basic modes of operation for the HART protocol.
In point-to-point mode the digital signals are superimposed on the 4-20 mADC loop current. One process variable (PV) is sent on the 4-20 mA signal, and other signals, such as secondary or calculated PVs (up to four or eight in newer devices), as well as device setup, calibration and diagnostic and maintenance status, can be transmitted digitally over the 4-20 mA signal.
Multi-drop signals are transmitted with the current loop set at 4 mA. Multi-drop mode allows up to 64 devices on a single loop. Multi-drop mode "has been very successful on RTUs in remote wellhead monitoring," says Jonas Berge, director of applied technology for Emerson Process Management, Singapore.
The third mode is WirelessHART. This mode is true HART, but the data is sent wirelessly using an IEEE 802.15.4 radio. "The goal with WirelessHART was always to extend the capability of the proven wired technology," says Ed Ladd, senior business development manager for process automation at Mitsubishi Electric Automation, Inc. "It was designed to provide a reliable sensor level network that could interface with current systems in the field."
WirelessHART was designed so it could be used to retrofit wired HART devices with a wireless adapter that is a native HART device and can be located either at the device or anywhere along the current loop. Thus, any HART device can be upgraded to act as a WirelessHART device, within the capabilities of its native HART version.
Because the HART protocol was designed for multiple vendors, many HART commands are universal and must be adhered to by all vendors for any device. This forms the backward-compatibility to other previous versions of HART, so that any installed HART device can be used with any other HART device, completely interoperably. Other commands, such as Common Practice, include calibration and PV range, while a third set of commands includes device-specific commands such as Linearization Tables.
HART, whether wired or wireless, uses EDDL (Enhanced Device Description Language), with all the information needed by the host to communicate with a field device. The DD (Device Description) is a binary file which cannot be read as a text file. This enhances the cyber security of field devices.
The DD is generated via a tokenizer during the development and testing of the instrument. The DD contains all of the information required by a connected host, either a handheld communicator or a PC, for an engineer to be able to support the instrument. More complex instruments have been able to benefit from a backward-compatible upgrade to the DD that allows a more graphical user interface, much the same as that offered by the Device Type Manager.
HART data can be transmitted using a multiplexer (available from several vendors), connected to many field instruments with a single connection to a host system. The multiplexer is often incorporated during the design phase of the project, but can also be added as a retrofit due to the backward-compatible and interoperable nature of the HART protocol. Recent control systems have been able to take advantage of I/O cards that can pass HART commands over a fieldbus network such as Profibus DP. HART data can also be transmitted via OPC to the control system or the asset management system.
[sidebar id="3"]
What People Use HART For
Most users use HART for calibration and routine diagnostics. This is changing rapidly. More HART devices are being connected directly to the process control system or asset management system now than previously. Endress+Hauser's Robinson says, "This depends on the individual's perspective of how that process device impacts the profitability of the plant. Even though a process asset isn't connected to the plant controls does not minimize its importance to the process. We all know that the right information in the right hands at the right time always yields positive results."
Phoenix Contact's Schmidt says, "Being able to use HART has a lot of benefits; I think one of the most overlooked uses is for getting off of preventative maintenance schedules and being able to predict device failure with the HART data—especially for valves. Partial stroke testing (PST) and positioning feedback data is extremely valuable."
HART and the future
Users discover more ways to use HART Communication to make their plants competitive and sustainable; suppliers offer more intelligent HART products; and the use of HART technology grows globally.
The ARC Advisory Group reports about half the worldwide installed base of process measurement and control devices is HART enabled. ARC forecasts the number of installed HART devices will surpass 37 million by year end 2012 .
ARC says, "HART continues to have the largest share of the market. We see strong, continued growth (for HART) ."
The HART Communication Foundation continues to enhance the HART Protocol. HART technology developments support changing industry requirements and preserve investments, to provide new opportunities for both users and suppliers. Backward compatibility ensures that an investment made in a HART device is protected into the future.
IEC 62591-WirelessHART, designed to bridge the gap between wired and wireless, is the first international wireless standard for process monitoring and control. WirelessHART benefits both existing and new monitoring and control applications. The development of wireless capabilities and other enhancements for the functionality of the HART Protocol preserves the viability of the technology's future indefinitely.
And more enhancements will come to extend, amplify and improve your HART assets for the future.
HART technology for today and the future
Planning an automation solution requires many considerations, including technology risks mitigation, funding, resources capability, team agreement, leveraging of installed assets, system integration and real-world needs assessment. From point-to-point to multi-drop to wireless, HART technology enables real answers. HART Communication is the most robust, most versatile fieldbus protocol, and positioned to carry the industry well into the future.
Latest from Asset Management
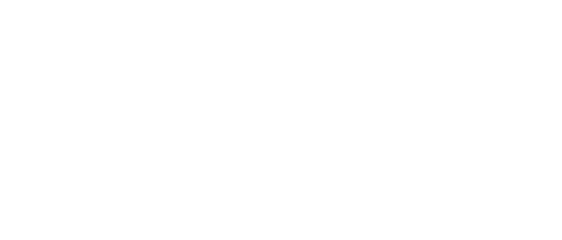
Leaders relevant to this article: