Pastry Plant Doubles Production with Automation
Rolling Dough
Figure 1. After mixing, the feeder puts dough on a conveyor line where it is spread and layered, then topped with butter and filling.
Just as they have been doing for the past two decades, workers at Country Maid, which manufactures Butter Braid braided pastry products in West Bend, Iowa, braid their pastries by hand for fundraising groups across the United States.
However, thatās the only part of the process that remains manual. In 2012, Country Maid, which was founded in 1991, decided to invest in automation to better manage costs and improve quality as it continued to grow in response to increasing customer demand.
Rising Expectations
Figure 2. The PlantPA-x-based automation system includeds a visualization, analysis and reporting portal, provides detailed documentation and supports mulitiple alarm setupsĀ
Automation Helps Plant Make More Dough
Prior to the automation project, workers were far more involved in the production process. They did the batching and scaling of every pastry batch by hand, and they cut open each bag of flour to pour into the mixer. Operators also collected and reported basic production data manually, which left room for inconsistencies and other human errors. The completely manual process was also time- and labor-intensive.
One of the goals of automating the process was to improve overall operational efficiencies throughout the facility. Another was to gain advanced data collection capabilities to ensure that each batch would attain the same high quality.
"The company started out with one line, which had a manual batching process,ā says Raymond Berning, lead control systems analyst for Interstates Control Systems in Siuox Center, Iowa, which worked with Country Maid to install its new process automation. "There were no equipment controls or recipe management. Everything telling operators how much of each ingredient to add and how long to mix them was on paper.ā
As demand grew, Country Maid realized it needed to build a second production line. It could replace the existing mixer with a larger one, or it could install a new, smaller, automated mixer. "Theyād just built the facility they were in and realized that, if they installed a larger, manual mixer for both lines, theyād need to perform major renovations to fit the mixer in, including cutting off and rebuilding the roof,ā says Berning.
Instead, the company decided to shift to an automated process, which would allow a smaller automated mixer that could serve both lines, without having to retrofit the building. "This option was less expensive and would achieve the same goal,ā says Marc Banwart, systems integration specialist at Country Maid. "We knew that the change would help us meet growing production requirements, and give us access to data that would allow us to make better operating decisions.ā
Dashboards Keep Tabs on Daily Bread
Research led the company to opt for PlantPAx from Rockwell AutomationĀ as the core system for the two lines. The system includes a visualization, analysis and reporting portal. "PlantPAx software provides detailed documentation,ā explains Berning. "It can also configure multiple alarm setups.ā
The system includes a process historian, which allows operators to view production trends such as the balance of ingredients. It also uses FactoryTalk VantagePoint EMI software to track data and pinpoint production trends.
Operators can view data on a variety of role-based dashboards in real time. "The main dashboard provides material usage,ā adds Berning. Operators can use this data as a discovery and analysis tool, allowing them to strategize improvements for each batch based on various parameters such as temperature and dough consistency.
For example, sometimes dough development was inconsistent, but no one could tell why. By using VantagePoint EMI software, operators were able to locate the source of the problem. The plantās flour silos are located outside of the building, which can cause inconsistencies due to temperature and humidity changes.
Operators are now able to monitor and adjust each batch based on the changing temperature and humidity conditions within the holding bins.
"Initially, this was not an objective,ā said Reid Vander Veen, business development manager at Interstates Control Systems. Employees noticed they had access to data and could thus make these determinations.
William Atkinson is a Control contributor.Ā
Data Drives Quality, Compliance
When Country Maidās staff decided to automate their processes, they wanted to gain quality data and tighter control. They also wanted to be able to make better decisions based on data from each batch. The automated system has allowed the company to achieve these goals and more.
One of the "moresā relates to FDA reporting. Country Maid is required to conduct quality measurements for the FDA and keep copies of the resulting quality reports, including freezer temperatures, sanitizing, etc. "We helped the company automate this process,ā adds Berning. "We developed a mobile app for them on an iPad. Now operators can enter all of the information into the iPad as they go around conducting measurements, and all of this information is stored in a database.ā
The iPad solution is eliminating six pages of paper reporting per shift. "We can eliminate four more pages,ā says Berning. "We hope to extend the iPad app to warehouse and maintenance employees to streamline their daily work and data collection processes.ā
The system also provides a wealth of information via trending, usage and batch reports, adds Berning. "After studying the reports, they can find ways to reduce costs or increase line speeds by making certain adjustments.ā
By adding the second line, the company was able to more than double its product output (2.2 times increase in production output). It was also able to achieve a 14% line speed increase, and reduced mix time by 23%.
Installing the automated mixer instead of a larger one saved $120,000 in equipment, plus the cost of removing and replacing the roof to install the larger, manual mixer. And the new data collection capabilities are reducing batch labor by more than $45,000 a year.
For now, the only part of the process that the automated system canāt touch is the hand-braiding component for each pastry ā a task that no machine has been able to duplicate with as much precision as a workerās hands.
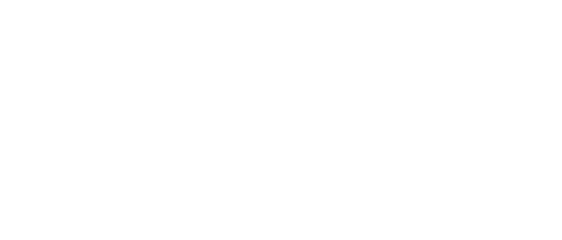
Leaders relevant to this article: