“It’s not only having a certified system,” said Luis Duran, product marketing manager, safety systems, ABB, in his session, “Technology to Enable Safety System Compliance,” today at ABB Automation & Power World in Houston. “As the system ages for 10 or 15 years, there are things to be done, and more to be done on the operational side.”
Duran compared our plants to automobiles. Each year, many accidents result in 3.5 million injuries and take 36,000 lives. “Cars now are much safer, with seat belts, air bags, and computerized braking systems,” he said. “But none of these can prevent distracted driving.”
It’s the same with our processes, Duran said. We try to reduce risk to an acceptable level—as low as reasonably possible (ALARP). But we can only address risks we know about. Just because we’ve gone 15 years without a lost day, just because no one is telling you it’s unsafe, does that mean it’s safe? Gaps in our layers of protection—our people, processes and plant assets—can eventually line up to allow a major incident.
“We understand how to do this. It’s in the books, but we must take it out of the books and do it.” ABB's Luis Duran presented 'Technology to Enable Safety System Compliance' today at ABB Automation & Power World.
“We must start with a safety culture that drives behavior across the organization, or our technology will fail,” Duran said. Establish the right targets and metrics, with active support by senior management. “People believe what they see on an ongoing basis,” he said, and will quickly understand if management only gives lip service to safety.Organize information and make it available. Control revisions through management of change, take data out of silos and make the right information available in the right place, at the right time, to the right person in the right format. Information above and outside the safety system supports the independent protection layers in the process control system, alarms, operations and management.
Incidents cost the process industries $20 billion per year, but 80% are preventable, and 42% are due to operator errors. Operators need to know, “What is the abnormal situation and what can I do about it?” Help those operators with alarm rationalization and proper presentation of information. Harmonize displays and design them for fast detection and elimination of disturbances.
Risk reduction technologies are the basis of safety. Understand the hazards, do hazard and operability studies (HAZOPs), and mitigate them. But over time, maintenance, changes and operational deficiencies can degrade the systems, leading to an accumulation of risk of hazardous events. Systems must be reviewed and renewed. “We understand how to do this, it’s in the books, but we must take it out of the books and do it,” Duran said.
Duran closed with a quote from Trevor Kletz: “If you think safety is expensive, try an accident. Accidents cost a lot of money. And, not only in damage to plant and in claims for injury, but also in the loss of the company’s reputation.
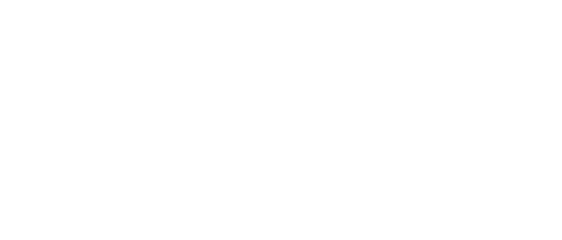
Leaders relevant to this article: