Founded in 1920 as a response to raw material shortages brought on by World War I, what was Eastman Kodak’s wood products plant in Kingsport, Tenn., is now world headquarters of Eastman Chemical Co., with 620 buildings on 4,000 acres producing chemicals, textiles, fibers and polymers as well as its own electrical power, steam, emergency services and fire protection. Along with myriad legacy automation and control systems, the facility has been working with NovaTech D/3® controllers for more than 20 years.
To integrate information from different units, rationalize alarms and improve operator efficiency, “We were looking for a way to connect across DCSs and PLCs. We decided on PlantState Suite by PAS,” said Cindy Bishop, Eastman's control systems specialist, to attendees of the NovaTech Futureproof Automation 2015 User Conference, Aug. 31, in New Orleans.
Safety depends on alarms
Out-of-tune PID loops not only impair alarm management and process optimization—they induce oscillations in process variables and controller outputs that can compromise quality, waste energy, and radically increase wear and tear on equipment and final control elements such as valves and actuators.
“Tuning extends the life of final control elements and gives us the opportunity to increase profitability by operating closer to the optimum setpoint,” said Lindsey Fink, field service engineer, Control Station, to attendees of the NovaTech Futureproof Automation 2015 User Conference, Aug. 31 in New Orleans.
Loop tuning often leads to a 2-5% increase in throughput and yield while reducing energy and material usage. “So why do manufacturers allow this?” Fink asked. “PID tuning is often poorly understood, and many existing software packages can’t handle excessive oscillations, noise or deadtime.”
Fink walked attendees through the process of tuning spray driers used to produce fracking beads. The gas-fired dryers have three zones and had been run on manual due to excessive process variability. They exhibited interacting temperature zones, long deadtime, asymmetrical response on heating and cooling, and stiction in the gas flow control valves.
Using Control Station PlantESP software, “We did a bump test and found new parameters that reduced temperature variation from 70º F to 12º F, saving $6,500 per year per line, plus downstream savings in the kiln and reduced pump/valve maintenance.”
Key elements for PID loop tuning are to use a large enough controller output or setpoint step or bump, “Four or five times the noise band,” Fink said. “Make sure you have a sharp and sudden change in the controller output, and do more than one test—both up and down—to capture different dynamics.”
Then the software can be used to choose the data to be included in the tuning calculations, check the resulting fit and, if desired, average the up and down models, shift tuning to be more or less aggressive, write the resulting tuning to the controller, and check the results.
“The latest version allows the tuner to be opened from Windows as well as from the controller, so you can do off-line tuning and statistics,” Fink said. “That allows you to find new tuning parameters for controllers that don’t connect directly.”
The Texas City refinery explosion and fire that killed 15 people and caused $1 billion in damages was due to instrument failure. “It looks to me like a case of not enough alarms,” Bishop said. But a witness report from the BP Deepwater Horizon oil rig disaster that killed 11 and cost $40 billion reported, “Then a gas alarm sounded, followed by more and more alarms wailing.” Bishop said, “They seem to have had too many alarms.”
PlantState Suite imports alarms, events and tags, and offers reporting tools, alarm & event analysis, documentation & rationalization, and auditing & enforcement, guided by best practices in alarm management.
“At Kingsport, we use those tools plus Dynamic Alarming (state-based alarms) and Alert Director (operator alert) modules,” Bishop said. They run on a central server on the plant network with a data collector and real-time server behind the DCS firewall.
The alarm management lifecycle
The three main elements of alarm management are a coherent philosophy, benchmarking and bad actor resolution. “Everybody’s got to develop their own philosophy,” Bishop said. “We follow the PAS approach. Typically 80% of your alarms are low priority.”
Each alarm is evaluated for its severity—its potential consequence from none to severe—on the three parameters of safety, environment and cost, as well as its maximum response time: less than 5 minutes, 5-15 minutes, 15-30 minutes, or more than 30 minutes. “If it has no consequence or doesn’t matter for more than 30 minutes, why have an alarm?” Bishop asked.
To benchmark, collect and analyze the data on frequent alarms. “We use PlantState Suite’s alarm and event analysis tool to run predefined analyses, then generate reports with Report Builder,” Bishop said. “It can be set up on a schedule to issue reports weekly or monthly.”
Alarms can be identified and sorted as frequent, chattering, duplicate or consequential, stale, disabled or inhibited, etc. Events also can be sorted and categorized as controller mode, controller setpoint, tuning constants or outputs. Users can report the number of alarms in each category per time period, and set targets for alarm reductions.
Bad actor resolution is done in regular meetings where operations, maintenance and DCS support personnel review the data and define the right action. “We recommend that Operations drive this,” Bishop said. “If it’s DCS, no one will pay attention.”
Beyond the lifecycle
PlantState Suite’s documentation & rationalization tools import DCS trip points to a master database. Its audit & enforce features can write data to the DCS, audit changes and enforce them to prevent regressions.
When the plant is ready, state-based alarming manages shutdowns, startups, transition states, parallel and spare equipment, and maintenance modes. Alarms can be shelved, nuisance alarms can be temporarily disabled, and there’s even a “snooze” feature.
One of the observations of the Deepwater Horizon incident report was that operators may sit at consoles for as many as 21 hours. “It is no longer acceptable to rely on a system that requires the right person to be looking at the right data at the right time.”
As users of PlantState Suite, “The reward is a database of all your tags and alarms that’s easy to maintain,” Bishop said. “More important, operators know that the alarms mean something.”
Latest from Alarm Management
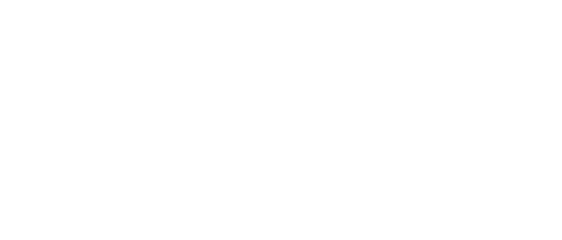
Leaders relevant to this article: