Tristan O'Brien is the wireless business leader at Control Southern Inc., a system integrator and distributor in Suwanee, Ga.
More recently, changes in the pharmaceutical market have increased demand for wood-based sterols, and one company that's poised to grow along with this demand is Arboris LLC, which is the world's leading producer of pine sterols. With manufacturing plants in Savannah, Ga., and Newark, Ohio, Arboris began operations in 2004, and has a cost-stable, long-term, raw-material supply of pine tree byproducts.
The company's flagship product is Sterols AS-2, a 99% pure mixture of naturally occurring sterols derived from pine trees free of genetic modifications. AS-2 is manufactured under stringent quality standards, including ISO 9001 at its Savannah plant, while its Newark plant follows the Codex Alimentarius Commission's Recommended International Code of Practice on the General Principles of Food Hygiene. Also, AS-2 is approved for use in specific foods by the Novel Food Board of the European Commission, the U.S. Food and Drug Administration and Health Canada.
Proprietary production steps
The raw material used to make AS-2 is tall oil pitch (TOP), which is a byproduct of the Kraft process that converts wood into wood pulp and refines it into cellulose fibers. The Savannah plant receives dark, black, liquid TOP at close to 200 °F from many pine chemical refiners via truck, railcar and pipeline. Since its beginning, the Savannah plant has relied on DeltaV from Emerson Process Management to control nearly all of its proprietary production processes.
The first step saponifies the TOP to obtain a mixture of free sterols and organic salts. The sterol-concentrated stream is then separated from residual organic salts by evaporation stages. Before being transported to the Newark plant, the sterols are further concentrated by distillation to obtain a high sterol concentration fraction. After reaching the Newark plant, the sterols are further refined through crystallization, filtration, drying and pilling until they reach near-perfect purity. The white, waxy particles are shipped to pharmaceutical, food and cosmetic manufacturers in 500-kg super sacks, 100-kg fiber drums or 25-kg fiber drums.
Arboris collaborated with integrator Control Southern on present and future planning, deployed electronic marshalling components to update and simplify its infrastructure, and optimized production of its pine sterol products.
Optimizing for Increased Demand
To maintain its leadership in sterols, Arboris' management recently established a continuous improvement program to examine each step of its production process. In February 2012, Arboris chose Kiel Hagberg to lead the Savannah plant as superintendent/plant manager. Formerly a production and engineering manager at the Newark plant, Hagberg was well aware of Arboris' automation system and production processes.
"The demand for non-genetically modified organism (GMO) products has been a big driver for our sterols," says Hagberg. "Also, the pharmaceutical industry uses our sterols as a precursor for manufacturing cortisone, progesterone and hormone replacements, creating a perfect storm of new demands for sterols."
With the increased demand comes increases in production goals and increased focus on plant optimization and reliability. As an automation and controls expert, Hagberg had two key performance indicators—improve throughput and upgrade the infrastructure to handle added capacity as needed and on demand. "I talked with Control Southern, our Emerson Local Business Partner (LBP) in Atlanta, and shared our two-fold vision for the plant," says Hagberg. "During one of the trips Control Southern's engineering manager, Harley Jeffery, pointed out a number of things we could do right away to optimize the process, so I said ‘Okay, let's give it a shot.' " Control Southern Inc. is a system integrator and distributor in Suwanee, Ga.
Beginning in April 2013, Hagberg reports Jeffery began talking with the operators, and spent a great deal of time in the control room. "The operators are notoriously leery of people coming in and messing with the system," adds Hagberg. "But when Harley visited, the operators said, ‘Oh, good. I've got some other stuff to ask him.' The guys like talking to him, and he gets results, so that makes him even more popular."
Jeffery also worked transparently behind the scenes without interrupting production. "We found the operators controlling the process spent a lot of time watching things, and manually making adjustments themselves, rather than the control system doing it automatically," explains Jeffery. "So I examined the previous programming and improved on that. We also did control loop tuning, and introduced some DeltaV advanced control options that were not yet enabled, including cascade and non-linear gain."
Jeffery optimized nearly every control process at Arboris' Savannah plant, including evaporation, distillation, vacuum, mechanical separation, centrifuges and utilities. "Control Southern has done an awesome job, especially on the distillation system," Hagberg says. "Harley took a system that was very, very manual and optimized it, allowing the loops to run in cascade and in control as they were originally intended. The distillation towers run smoothly now, which means a lot less stress on the operations group."
Since completing the plant's optimization in June 2014, Hagberg says production has remained stable, and the instability and reliability issues have not resurfaced. Financially, the optimization has saved Arboris well over six figures, according to Hagberg. "There's no swinging, and the operators are able to focus on other plant operations rather than manually controlling key facility parameters," he adds.
Building Tomorrow's Infrastructure
In August 2014, Hagberg turned his attention to the second part of his vision for the plant—expansion. He says a logical starting point was to focus on the plant's network communications infrastructure. Since the plant opened, a number of network communications technologies had been used, including Profibus, AS-i, and Foundation fieldbus. Hagberg explains the expansion includes introducing new Rosemount wireless gateway enabling communication between the DeltaV system and 802.15 wireless process measurement devices in the field, Ethernet and Emerson's characterization modules (CHARMs) I/O devices.
Hagberg adds that CHARM I/O enable any field wiring signal type to be terminated anywhere in the Savannah plant. CHARMs are a single-channel components with an A/D converter and signal characterizer inserted onto the terminal block where field wires are landed. After a CHARM is in place, the channel is electronically marshaled to any controller in the DeltaV system. Hagberg explains this means no cabinet marshalling or cross-wiring, fewer wires, much less work and fewer contact points for potential failures. Also, electronic marshalling requires no redesign or rewiring, which allows expansion as needed without extra cost or impacting start-up schedules.
"All we do is snap in a CHARM, and it can be whatever we need it to be," adds Hagberg.
Engineering Aids Future Roadmap
As the plant team at Arboris Savannah began to introduce the new I/O, they worked again with Control Southern to determine the infrastructure needed to support it. A three-member Control Southern team performed an engineering study in August 2014. Led by project engineer David Poindexter, the team was charged with creating a roadmap to make Hagberg's expansion vision a reality.
"With the network infrastructure well underway, a process control expansion study helped them characterize current states, and identify a future state that needs to support the growth," explains Poindexter. "We also identified best practices for the site and standards to follow. These included I/O enclosures, IT, process control network design, fault-tolerant network design, proper I/O grounding and power grounding to prevent any field instrumentation issues."
Over the next five years, Hagberg reports, suggestions from the engineering study will be executed in phases without disrupting the production process. "Control Southern gave us a plan, and that's what we needed," adds Hagberg. "Moving forward, we know how much cabinet space is needed, as well as the right licensing requirements and how many I/O are needed. That makes it much easier and less expensive to bid the construction because we'll avoid change orders. Contractors will know in advance where everything needs to land. This makes the construction bid process much quicker and more accurate, while also speeding up the installation."
Now that the Savannah plant is optimized, the network infrastructure is selected and the engineering study is completed, Arboris believes it's in a much better position to maintain its position as the premiere supplier of wood based sterols. As a small company with 70 employees, Hagberg reports that Arboris has the flexibility to work with partners like Control Southern to identify and implement changes quickly. This is especially important because its customers are among the world's largest food, chemical and pharmaceutical companies. However, he says it all starts with a plan.
"The pre-work isn't really that exciting or fun, but if you don't do it, you're shooting yourself in the foot," says Hagberg. "Now, we're going to start to see the results from all the upfront work because we already have a cutting-edge plan. We just have to execute it."
Continue Reading
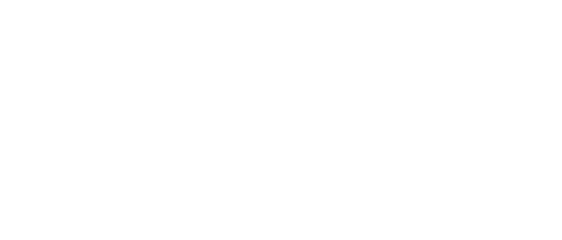
Leaders relevant to this article: