The manual process had required that two strong operators handle a red hot part between a furnace and quenching process. It also required controlling a combustible furnace and quenching process with their attendant safety risks, plus tight mechanical tolerances and process requirements. Adding to the difficulty was a 2,200°F, 40-lb aerospace gear that imparted a high moment load to the end of a robot arm.
Key to the project’s success was the Rockwell Automation high-performance architecture, related Bill Klick, O&G integration lead, who discussed the project at this week’s Rockwell Automation TechED event in Orlando. O&G decided early to use a fully integrated design and selected Rockwell Automation due to support and hardware availability at the end-user site in the Philippines. A Fanuc robot was selected as the workhorse of the system. With the control architecture selected, a conceptual design was created in AutoCAD Inventor and using Fanuc Roboguide to simulate the part movement.
A distributed approach
A single ControlLogix controller in the main panel worked with distributed controllers in each piece of equipment, Klick explained. "One of the biggest successes of this project was the use of distributed control in the design.” Each piece of equipment had its own control panel with Allen-Bradley POINT I/O modules, including the infeed conveyor, Fanuc robot, furnace, atmosphere, quench and washer.
[embed width="100" height="100" class="left" thumbnail="http://www.controldesign.com/assets/Uploads/Dave-Perkon-headshot-online.jpg?r=42105"]http://www.controldesign.com/assets/Uploads/Dave-Perkon-headshot-online.jpg[/embed]Dave Perkon is technical editor for Control Design. He has engineered and managed automation projects for Fortune 500 companies in the medical, automotive, semiconductor, defense and solar industries.
The equipment was designed, built and tested in O&G’s Liverpool facility in New York. "Once tested and 100% operational, the equipment was partially disassembled and shipped overseas," said Klick. "The modular design of the Rockwell Automation architecture made teardown and then installation at the end user simpler. Each piece of equipment had its own control panel, so the wiring stayed intact when shipped. “It didn't take much more than supplying each machine with air, power and Ethernet,” Klick said. “It reduced much of the commissioning and testing, such as checking for sensor and cable hook-up errors."
"A Stratix managed Ethernet switch was used to segregate the control network from the plant network," said Klick. "POINT I/O was the smartest platform we used on this project. The cost was less than some of the rack-based options, and it allowed us to combine both safety and non-safety I/O on a single adapter. We could do both safety and control via Ethernet."
The main operator interface is an Allen-Bradley PanelView Plus 6 graphic terminal. "The client requested a single operator interface with data acquisition. We utilized the DataStore functionality on the PanelView Plus to gather time, temperatures and transfer times. We also added a Cisco firewall / VPN to support the customer remotely."
Commissioning & training
O&G worked closely with the customer during commissioning and training. "Installation took a little over a week," said Klick. "Our control engineer was onsite to set up and teach the robot. And, during startup testing, we trained the operator using as many test parts as were available.”
“One of the keys to a successful project are engineers, operators and maintenance people who can properly support the equipment 24/7,” Klick added. “In this case, the operators took ownership of the machine quickly."
Replacing a risky manual operation with some automation and the Rockwell Automation architecture created a safe system that complied with industry safety requirements, increased production and improved product quality. It improved the furnace temperature uniformity from within 25°F to within 10°F, reduced transfer time from furnace to quench by 50%, increased throughput by 38%. In the end, the customer saw 100% ROI within 1 year and 7 months.
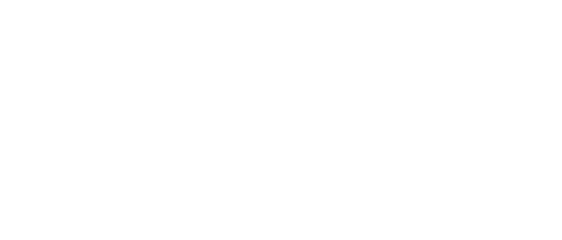
Leaders relevant to this article: