What does good control room design look like?
[sidebar id =6]“Of course I know what good control room design looks like.” Anyone who’s ever spent time in an operations center for a large refinery or chemical plant knows a good control room when they see one. Or do they?
In our experience, having been in many 24/7 mission-critical control rooms in continuous process industries, finding examples of “good control room design” isn’t easy. Think about your own experience. How many control rooms have you actually been in where the spaces were crowded, messy, disorganized, even perhaps mildly depressing? Did the room feel something like a dark, subterranean dungeon? Perhaps the image below recalls your own experience with control rooms (Figure 1).
[sidebar id =1]
Awareness and ISO 11064
However, there have been improvements over the past decades in control room design, along with our understanding of the role design plays in the efficiency and safety of these mission-critical spaces. There’s been a spreading, international awareness of safety in control room design due to standards published in 2000 by the International Organization for Standardization. In particular, ISO 11064 spells out standards for ergonomics in the design of control centers, and the layout and dimensions of workstations for maximum efficiency and safety. Adherence to these best-practices guidelines is recommended in all industries with control rooms. Indeed, compliance with ISO 11064 standards can aid a company’s defense and help mitigate legal liability in case of an accident, incident or personal injury case. In the U.K., ISO 11064 is cited in guidance to the legislation as best practice, so companies are advised to use it. Also, facility siting and building design from the operator-out and good control room design can be measured against ISO 11064. The result are facilities that offer return on investment via maximized efficiency and minimized abnormal events.
ISO 11064 helps establish good design standards with measurable results to avoid control rooms like many of us have experienced. BAW Architecture designs control rooms, control buildings and operation camps that feature a user-driven approach, work with ISO 11064 requirements, and integrate architectural, interior design and human-factors elements to optimize performance. Our buildings for Fortune 100 companies can be found worldwide.
[sidebar id =2]
Starting with control room safety
The first critical step in good control room design is facility siting, and hiring an experienced control room architect can assist with planning the best location of the building in proximity to the process plant. Will it be in a blast zone or located outside the process plant fence?
Since the BP Texas City explosion in 2005, the American Petroleum Institute and regulatory agencies, such as OSHA and the U.S. Chemical Safety and Hazard Investigation Board, have focused on developing new and revised recommended practices for risk assessment and mitigation requirements for temporary and permanent buildings located in or around processing units, including API RP-752, “Management of Hazards Associated with Location of Process Plant Buildings,” and API RP-753, “Management of Hazards Associated with the Location of Process Plant Portable Buildings.”
[sidebar id =3]API RP-752 covers permanent, occupied buildings at refineries, petrochemical and chemical operations, and provides guidance for managing risk from explosions, fires and toxic material releases. Development of new technologies pertinent to building siting evaluations include prediction of blast damage to buildings, determination of occupant vulnerabilities, and estimates of event frequencies. APR RP-753 adds that, if using occupied, portable buildings, their use should be minimal and should be located away from process areas. During periods of increased risk, including unit startups or planned shutdowns, it adds that occupancy of these portable units should be minimized. If using portable buildings, they should be designed, built and maintained to protect occupants from potential hazards.
In addition to the regulatory compliance and liability benefits of developing a facility siting risk-mitigation plan, developing a master facility plan is critical to the longterm planning for a site. It not only addresses the immediate risk assessment requirements, but also addresses longterm (five-, 10- and 15-year) facility infrastructure improvements and asset optimization, addressing security, IT infrastructure, site circulation and workforce optimization (Figure 2).
Brain of the process plant
Once the control building is sited properly, the next step is to focus on the control room. As the center of operations and production, control rooms are where businesses make or lose money, and where catastrophic incidents are identified early and mitigated. Their operators often work long shifts in front of computer screens to ensure 24/7 operations coverage.
However, even though it’s among the most important physical spaces in a plant, chances are its furniture isn’t nearly as comfortable or up to date as furniture in the conference room. More often than not, it’s one of the spaces that companies invest in the least. Many control rooms today were designed in the 1980s or 90s. Since then, technical upgrades have been crammed into these poorly designed spaces without taking a step back to consider the true importance of these spaces or their technology. Operators forced to work in these crowded rooms are the victims of this lack of foresight and investment in operations. Understanding the operator’s needs and how they interface with complex systems in a high-pressure environment is the first step, and subsequent design decisions emanate from it.
The risk of an abnormal situation escalation is always present in a control room. A state-of-the-art control facility enables operators to return the situation to normal in the shortest time. Dozens of factors must be taken into account, such as orientation of consoles, screen information, noise reduction, arc of reach, line of sight, clutter mitigation and manual placement. All have the potential to improve or degrade the operator’s reaction time and ability to communicate.
Design from the operator out
A human-centered approach to control room design considers the needs of the operators first and foremost. Instead of designing from the outside-in by creating the architecture first, the building unfolds from within, with operators and their functional and physical needs as the starting point. As demands on human-machine interfaces (HMIs) have increased, so have the consequences of inappropriate operator actions. Similar to advances in HMI software that have consoles, ISO 11064 lays out measurable guidelines for ergonomics, or human-factors engineering (HFE), which have a primary role in selecting furniture, lighting, acoustics and interior finishes, and are proven to reduce inappropriate operator actions (Figure 3).
[sidebar id =4]Some specific operator needs include:
- Proximity to other operators to enhance communication, collaboration and efficient workflow;
- Access to other areas, such as test, exercise, kitchen and restrooms;
- Operator tasks and functions that determine the number of screens and size of workstations;
- Modifications to workstations or other equipment for individual requirements, such as providing a footstool to a shorter users; and
- Further workstation customizations, such as individual radiant heat panels, sound showers for sound masking, overhead task lighting, sit/stand capability or ergonomic seating with headrests.
Finishes and lighting
Selecting finishes in accordance with ISO 11064 guidelines creates a comprehensive list of measurable criteria. The hierarchy of value goes from dark to light, and from floor to ceiling. Floor finishes should have a light reflectance value (LRV) of between 0.2 and 0.3; wall finishes should have 0.5 to 0.6; and ceilings should have 0.8 and a matte finish. In addition to the ISO requirements, the design must adhere to local building codes for flammability and slip resistance, as well as clients’ requirements. Above all, finishes must be functional, durable and maintainable because many control rooms must last 30 years or more.
Some finishes can provide multiple uses. Acoustically absorptive wall panels can double as tackable panels, or triple as visual breaks in large wall planes or as decorative elements, reflecting regional identity while mitigating sound.
Likewise, rather than an afterthought, good control room lighting should be as integrated into the design as the placement of the ceiling, walls and floor. Optimum lighting demands quality ambient, uniform illumination, which is a combination of fixtures such as indirect, task and suspended lighting (Figure 4). If all light comes from the ceiling, glare makes screens unreadable. In fact, many operators will shut off lights and sit in the dark rather than deal with headaches and errors caused by glare. Screens mounted to a sit-stand workstation required by ISO 11064 could also potentially bump into suspended fixtures. Therefore, adequate ceiling height is required to accommodate suspended fixtures.
In addition, dimming pre-sets for overall lighting work with operator preferences and lighting requirements throughout the day. One approach is to provide low-, medium- and high-level presets to adjust lighting levels on ambient lighting, while keeping on a consistent, low-level indirect light source. Task lighting at the work surface can be integrated into consoles and aimed onto documents, instead of bouncing off screens. This reduces eye strain and improves operator efficiency. ISO 11064 has guidelines that spell out lighting requirements throughout the control room, such as 47 foot candles (FC) at work surfaces, with an acceptable range of 18.5–46 FC.
Acoustics and furniture
Just as crucial as lighting and finishes, acoustics can make or break a control room. ISO 11064 dictates ambient noise can be 30-45 dB. Alarms, conversations, radios and computer noise create a distracting environment, but they can be mitigated by articulating ceiling and walls shapes and using acoustic-absorptive material for ceiling, wall and floor surfaces.
Similarly, furniture also contributes to a work environment informed by the science of ergonomics to maximize productivity and minimize risk of personal injury. Operator seating, sit/stand and height-adjustable workstations, screen display quantities and mounting heights, and mobile files positioned and designed according to ISO 11064 complete the good control room picture. We’ve also included treadmills, exercise bikes and even small exercise rooms with cardio and weight machines into our designs. Furniture must be ergonomic, adjustable and robust, especially in remote locations where parts aren’t easily available.
As for consoles, ISO 11064 has ergonomic guidelines for reach and eyesight distances. Flat-panel displays and touchscreens take up less space, are more energy efficient, and require less internal cooling. The size and quantity of consoles should dictate the size of the control room, rather than the reverse, with a set amount of square footage allowed per operator.
[sidebar id =5]
Economic benefits
Though the cost of a good control room is significant, the return on investment (ROI) in operator safety and efficiency is real and demonstrable. And abnormal situations and catastrophic events have a better chance of being avoided, which saves lives, money and the environment.
When control rooms are designed correctly the first time, they can save up to 15% savings in capital expenditures, according to a 2002 study by Shell’s Harrie Rensink, “ROI in use of human factors in offshore systems: closing the gap between conceptual design and engineering, field construction activities and operations,” U.S. Dept. of Transportation—Publications & Papers. Paper 23.
Using ISO 11064 can guide control room design decisions. With the assistance of an experienced control room architectural and interior design firm, the elements of good control room design can be integrated into a building that’s not only safe for operators, but improves the bottom line.
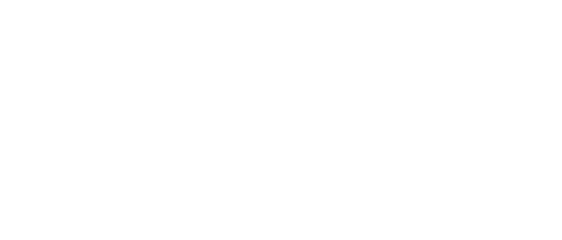
Leaders relevant to this article: