Q: I came across your “Ask the experts” column at www.controlglobal.com, and I'd like to ask a question I’ve had for quite a while regarding the control of fuel gas to a fired heater.
This particular unit is a natural-draft heater used in a diesel hydrotreating plant at a refinery, but I'm actually looking for a general answer. The question in itself is very simple: should we use a flow controller or a pressure controller to regulate the fuel gas used by a fired heater? Is one of these options always the right choice? If both are possible choices, what are some guidelines or considerations to choose between the two?
What we're trying to control is the outlet temperature of the heater. This is the master controller to the flow or pressure slave controller. Being off-gas from other units, the fuel gas composition varies (has H2 and H2S), so during a week, the density of the fuel gas varies widely between 0.44 and 0.7 Kg/nm. We did some modeling of the effect of gas composition on the master temperature controller, and it seemed to be rather small. But beyond that, I can’t say much.
Juan Florentino / Process control engineer, BP Rotterdam Refinery
----------
A: As you've asked, before answering your specific question, I'll give a general description of controlling any larger fired-gas heater. Figure 1 shows a common control system that's referred to as a parallel, closed-loop control with air and fuel limiting system. You can find other configurations for all sizes of fired heaters in the 4th edition, Volume 2, Chapter 8.6 of my Instrument and Automation Engineers’ Handbook. The controls shown in the figure provide both dynamic compensation and efficiency optimization.
In this control system, the firing rate signal sets the air and fuel flows in parallel. The air/fuel ratio control guarantees that the proper stochiometric amount of air is provided to combust the fuel, plus some excess because of the inefficiencies due to nonideal mixing and imperfect combustion conditions. The largest savings (optimization) in any burner is obtained by the excess oxygen trim (AIC) loop, which is minimizing the amount of excess air that otherwise would travel through the burner (just for the ride), picking up good heat and taking it out the stack.
As the load (feed flow and temperature) varies, feedforward compensation (4th ed., Vol. 2, Ch. 2.6) with lead-lag dynamic trimming (4th ed., Vol. 2, Ch. 2.9 and 2.29) are provided to accommodate variations in the load.
As to your specific question on fuel flow controls, what we must do is to match the heat provided by the fuel flow to the heat demand of the feed. In small (primitively controlled) heaters, this is done by using pressure control on both the fuel and the air. The limitations of this configuration are:
- Using pressure drop through the burner nozzles for fuel flow detection is like measuring volumetric flow with an orifice plate without square root extraction. It's very inaccurate and is also unstable because the loop gain (4th ed., Vol. 2, Ch. 2.35) varies with flow.
- The control loop has a very low rangeability.
- Density compensation slightly improves the accuracy of heat input measurement, but does not directly measure the heating value of the gas. Only calorimeters (CAL) do it.
For the above reasons, my recommendation is to use a linear mass flowmeter (5th ed., Vol. 1, Ch. 2.16), and compensate its measurement signal by a calorimeter (5th ed., Vol. 2, Ch. 1.27) that measures the heating value of the gas.
In addition, the figure shows the cross-limited parallel metering system for the air-fuel ratio (A/F) controls, which always limits the fuel flow rate to the available air flow, so that air is leading on load increase and lagging on load decrease. This feature also protects the system from accidents caused by a fan failure or fuel valve sticking. In addition, a minimum fuel flow bypass is provided (FCV) to guarantee stable flame, and a minimum air flow signal is provided (HIC) to match that minimum fuel flow.
To prevent interaction between the two valves on the fuel line, make sure the PCV is far away from the flow control valve.
----------
A: I've always used pressure control on cascade successfully. Flow control also could work well if gas source pressure is very stable and readings are accurate. Generally, the fuel gas pipes are small, sometimes less than 2 in. In that case, flow measurement requires costly instruments like mass flowmeters. Pressure measurements are simpler.
----------
A: Based on normal operational issues, the answer is that you could use pressure control, but it would not be a best option. If you use pressure control, you'll have the following issues:
- The pressure control isn't really relevant to the flow required to control the heater.
- The pressure control tends to be static when in normal operation, but more difficult to handle with upsets.
If you still prefer to do pressure control, you may need to find the correlation between flow and pressure in the line vs. the temperature required in the heater.
So, the best solution is generally to control the flow of fuel to the heater. If it's compensated to mass flow, it could be controlled to provide the heater performance required.
----------
A: The target temperature (in your case, the heater outlet) is influenced by the amount of the fuel (mass/unit of time) and its heating value (Btu/lb., J/kg, Kcal/kg, etc.), assuming the heater process input (flow and temperature) is stable.
Assuming all other parameters (e.g., heating value) are not changing much, controlling the fuel flow gives you direct control of the heat input quantity.
In your case, you're lucky to have direct measurement of the fuel gas density in kg/Nm3. The fact that it's referred to as “normal m3” excludes the influence of any variations in the pressure or gas temperature. This gives you the option (which I would have taken, if I were you) to build a “calculated point” to have the value of the fuel gas volumetric flow multipleid by the fuel gas density, which yields the fuel gas mass flow. This value should give a very good estimation of the total heat input into the heater. Controlling this quantity should enable you to achieve better control of your target temperature. A few more tips:
- Be sure to use the right size of filter on each of both readings before performing the calculation.
- If the furnace feed flow conditions (flow and temperature) are not constant, I recommend considering feedforward ratio control from the furnace feed heat inflow calculation.
- The two control valves (the PCV at the gas reservoir outlet and the control valve at the fuel inlet to the heater) should have as much gas volume between them as is practically possible to minimize interactions between them. This can be achieved by placing them as far apart as possible and/or enlarging the gas line as much as possible.
In general, I prefer controlling the inflow of fuel mass to the heater, rather than the pressure, because this way you control the amount of heat input. In the past, in fuel oil applications, I had very good results by controlling the pressure on the burners, but it was (mainly) because of shortages of other instruments (like separate flow measurment or fuel density detectors).
Also, I've just come across a very good article in HPC, June 2014, “Automate Furnace Controls to Improve Safety and Energy Efficiency,” which doesn't answer your questions explicitly, but deals with the problems you are facing.
[sidebar id =2]
[sidebar id =1]
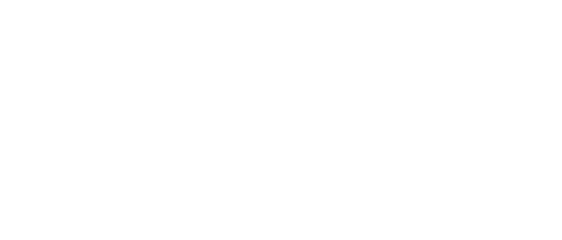
Leaders relevant to this article: