Two major changes are going on right now in the world of manufacturing:
- Plants are becoming more automated and networked—digitized.
- The “great shift change” is occurring as retiring workers are replaced by a new generation.
Taken separately, both of these are enormous, but taken together the impact promises to be unprecedented. The combination of people and technology will drive greater change than either individually. Let’s think about why.
Welcome the Millennials
Hundreds of articles have been written about millennials and how they are changing the workforce. As we have been told again and again, millennials are different than Gen X’ers and baby boomers in many ways. This is all just as true when they work in a manufacturing plant. Here are two key elements:
Tech natives: Internet and smartphones were almost ubiquitous when they were small children and the millennials have weaved these technologies into the very fabric of their lives. They trust technology implicitly, and in many respects, cannot function without it. Information must be available with a few swipes at the touchscreen. Communication needs to be direct, instantaneous and unaffected by distance. It should be just as easy to keep in touch with someone in Rio de Janeiro as in Denver.
Social responsibility: This generation has a strong sense of how an individual’s actions should fit into the larger picture of sustainability, and how what happens today could affect the future. Any career path should have some element designed to serve the greater good and deliver something meaningful to society. So how do these characteristics affect manufacturing?
Old-school versus digital plants
Looking at new opportunities requires thinking about what we have come from. Picture a traditional manufacturing environment. There may be computerized machines and robots, but the general concern from management is capacity—finding ways to make the most widgets, or produce the most product in a process plant, with the greatest quality and efficiency. There’s nothing wrong with this approach if the only goals are quantity, quality and efficiency—which is why this model has survived for so long.
But we’ve come into the world of mass customization. Yes, that term has been kicking around for a long time, but it’s difficult to implement in a meaningful way in an old-school plant. Customers may ask for new things, but unless a facility has been set up with the specific plan of creating custom products, making “specials” is often regarded as a nuisance because it interferes with regular production. Moreover, systems designed to support regular manufacturing (part drawings, item numbers, licensed processes, etc.) make it difficult and expensive to make anything outside the normal stream of production.
Digital manufacturing makes customization easier, or at least it can if manufacturers put its capabilities to work. But new technologies in old-school environments are often used to pursue the same goals as always: quantity, quality and efficiency for the smallest number of products and processes. Customers are still steered away from what they need to existing output.
Clashes with Millennials
When hired to work in such an environment, most millennials have a hard time understanding why manufacturing convenience invariably overcomes any desire to satisfy customer demand. They want to get rid of the any-color-as-long-as-it’s-black mindset and give customers what they are asking for. They want manufacturing to adapt to customers rather than the other way around. If the systems can’t handle the new reality, they want to change the systems.
If the traditionally-minded company digs in its heels, the ambitious millennial will look for another job. The company will continue with its methods until it is driven out of business by more agile competitors. A more sensible company will ask what must change to embrace the new reality, realizing the change will be disruptive.
Matching people and technology
As just suggested, millennials working in an old-school environment will find the experience highly frustrating. If the kinds of technologies used in all other aspects of life are suddenly withdrawn and the individual finds him or herself in a world of binders and manual processes, it won’t last. Questions along the lines of, “Why do I have to do it this way?” will be constant until he or she simply gives up.
An old-school manager in a digital environment won’t necessarily experience frustration, but using all the new capabilities to support traditional manufacturing approaches represent a wasted opportunity.
The ultimate combination is placing millennials in digital factory environments. That’s when good things really begin to happen.
Everything is connected
When millennials come into a digital factory, they take to it like a duck to water. Everything is interconnected and the entire process, from product design through all manufacturing steps, is done on or controlled by computers. The actual production equipment is heavily automated taking full advantage of the capabilities of robots. The same is true in a process plant, where custom formulizations reside comfortably side by side with standard products.
Placed in this kind of environment, a millennial can use his or her creativity to the utmost, working with customers to develop and make exactly the kinds of products they demand. Even if quantities are low, it’s possible to create something new and special because the design work is done on a computer, and all the necessary information is sent directly to the manufacturing equipment. If a different hole needs to be drilled in a part or a different color seat inserted into a vehicle, it’s no big deal. If the cheese needs to be extra sharp cheddar instead of just sharp due to changes in consumer demand, this can be done quickly and easily.
Millennials will look at the people working in a facility and push to optimize job functions. They have a strong grasp of what kinds of tasks people should be doing and what should be handled by machines. In that respect, they tend to drive for automation wherever practical. Humans should not be performing robotic tasks because they aren’t good at it. A robotic task should be performed by a robot.
Humans should be innovators and creators, functions which are even more important in a digital environment. A smart individual must figure out how to solve the customer’s problem, and then the machines make the product. People should be smart and creative and given all the tools they need to maximize their creativity.
In some cases, this causes a dilemma for a responsible millennial. The need for manual labor in such an environment is low since automation should be used in every possible application. On the other hand, the desire to provide jobs as an element of greater social responsibility is also strong. Such situations can be difficult to resolve. More on that in a moment.
But is it profitable?
Someone from a traditional manufacturing background may look at the discussion so far and conclude that it all sounds wonderful but can’t possibly make money. All the automation in the world can’t cover the costs of customization to this degree.
Compared to a traditional facility, a digital factory typically has a much different cost structure, but the more essential element of the discussion is the desire to be profitable—millennials understand what it takes to stay in business. They understand what represents value to the customer and are rarely afraid to charge appropriately. The concept of sustainability applies to the company as well as the environment.
To find evidence of this, visit a liquor store and look at the craft beer offerings, or visit the taproom of a local craft brewer. This industry is of, by and for millennials and there is no compunction to charging anywhere from $10 to $15 for a six-pack, and this segment of the industry has been growing strongly for years. Contrast this with the beer your father grew up with, half or less the price of craft beer, and with flat to declining sales for years now.
This is just one example, and they are many more. Some are due to changing customer tastes and demands, and others are driven by the evolving nature of certain industries. For example, power plants used to run at or near base loads for extended periods of time, but must now constantly cycle their output up and down to fill the gaps caused by the intermittent nature of renewable power. This is another form of customization, the same product, but produced at very different rates throughout the day, and often at premium prices.
Again, more on that in a moment.
Approaching situations differently
Millennials like to use people in the best ways possible and they have a low tolerance for suffering, so this influences how they approach various situations. Here’s a case in point: an oil company working in the Canadian tar sands was looking at opening a new site. The traditional approach involved hiring a group of low- to medium-skill operators and sending them to live in a camp in the boonies to perform basic day-to-day tasks.
A millennial will see this as a waste and a poor decision since nobody wants to go live in such an environment doing things that should all be automated. Instead of hiring those people, use the concepts of smart manufacturing: install the automation and run the operation remotely from a location where someone might be willing to live.
The control center can run multiple production sites. So long as there is some type of rapid response group close to the site able to handle problems, perhaps a single group across a number of sites in the area, don’t send a large group of people into such an awful place.
The millennial approach in this kind of case, among others, is to look for a technological solution first. Begin with automation rather than conceiving it first as a human action which can be automated later. Millennials think this way more easily and naturally than boomers.
The three elements of success
Millennials have a strong sense of mission in their lives, which influences the companies they decide to work for. Few will want to be associated with a company they don’t respect, even if the salary is high. The ultimate objective is for a company to satisfy three objectives simultaneously:
Socially responsible: A worthy company must to do something desirable for the greater good. Not only should it not make harmful products, it should be perceived as philanthropic, benefiting its community in multiple ways. Here is where the labor question comes into play as a company may have to find other ways to help a community if it can’t hire more people.
Environmentally sustainable: This area is important, but often difficult to define. In some situations it can relate to feedstocks and resources, and how they’re sourced. Fortunately, most smart manufacturing equipment and techniques have a strong energy efficiency component.
Economically sustainable: Here’s the profitability element. A company unable to ensure its own sustainability cannot fulfill the first two. The ability to capture enough margin from the customers who can afford and are demanding the customized products makes the others possible.
Companies unable to understand and fulfill these points will have a tough time recruiting and retaining millennial employees.
Get ready to be disrupted
Moving from traditional manufacturing to smart manufacturing will disrupt your company. Hiring millennials will also disrupt your company. Doing both at the same time compounds the discomfort, but the synergistic effects can be very beneficial to your company if handled correctly.
Companies unable to break free from old techniques and cultures will have a difficult time recruiting a new generation of skilled people. They will also have a hard time developing the kind of agility necessary to adapt to changing customer demand.
Better to adapt now and create an environment where customer and employee demands are met simultaneously, delivering customized products from flexible facilities, and selling these products at the premium prices millennials have proven willing to pay.
Latest from Home
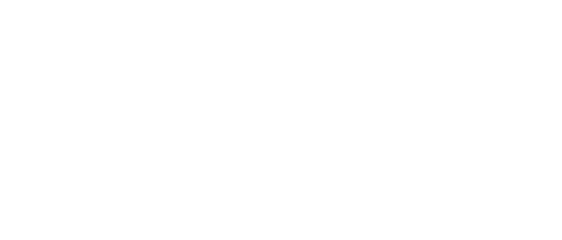
Leaders relevant to this article: