High-pressure mass spectometers offer robust, real-time, in-situ analysis
Industrial process control is facing one of its greatest challenges. Billions of dollars of pharmaceuticals and advanced process node semiconductor devices will be manufactured using processes where fast, accurate molecular analysis is critical to the quality of the end product. There's a pressing need for in-situ molecular analysis that delivers real-time results that are accurate, repeatable and quantitative from a small, rugged and easy-to-integrate solution. However, existing molecular analysis solutions such as residual gas analysis (RGA), gas chromatography-mass spectrometry (GC-MS) and optical solutions like near-infrared (NIR) and optical emission spectroscopy (OES) have limitations that make them impractical solutions.
Current solutions for molecular gas analysis applications have significant shortcomings. Mass spectrometry and residual gas analysis solutions have required low-pressure vacuum on the order of 1 x10-6 Torr to operate. Low-pressure operation requires sizable and expensive vacuum pumps, and ensuring there are no leaks makes installation and maintenance complex and costly. Further, low-pressure operation limits the sensitivity of the mass spectrometer or RGA, and while electron multipliers can be used to increase sensitivity, this comes at the expense of stability and repeatability, neither of which are process control-friendly issues. Gas chromatography (GC) has historically been used to isolate mixed gas components for quantitative analysis, but this process is slow, has significant consumable running costs and a high maintenance burden. Fourier transform infrared (FTIR) optical spectroscopy techniques can detect the presence of specific molecules, but getting quantitative data is very difficult, rendering them less useful in process control applications.
So how about ruggedized, high-pressure mass spectrometry? To be a useful process control tool, it must be process control production-ready. Basic production requirements are: to be fast and accurate, small and easy to install, field serviceable, robust, deliver stable and repeatable results, support easy software and system integration, and be low-maintenance.
Atonarp recently introduced a molecular sensor (quadrupole mass spec) solution that delivers on these requirements with: as many as 100 samples per second operation; sensitivity down to part-per-million (ppm) concentrations; small (20.4 x 20.0 x 25.6 cm) form factor; integrated vacuum pumps; and a rugged Faraday cup sensor that delivers high stability and infinite lifetime.
The miniature molecular sensor is about 5 cc and is mounted on 1.33-in. Conflat flange. It features an array of nine quadrupole mass filters operating in parallel. A single electron-impact ion source supplies ions to the individual quadrupoles to be filtered and collected on individual Faraday cups connected together. Driven at 11 MHz radio frequency (RF), the sensor is able to filter ions on the basis of mass-to-charge ratio with unit mass resolution from ultra-high vacuum (UHV) to pressures as high as several mTorr. Making the quadrupole small is offset by increasing the control electronics RF. The combination provides real-time, quantitative molecular analysis and virtually eliminates memory effects while allowing the system to work at higher pressures, which increase sensitivity.
Further, intuitive web-browser software, accessible via an Ethernet connection and industry-standard data file support (.json), make software integration, process datalogging and setup easy. To ease hardware integration, industrial analog and digital I/O are available, and can be used to control (and get input from) standard industrial sensors, actuators or PLCs.
Having the ability to do real-time, quantitative molecular analysis in-situ is an enabling capability for many industrial processes. Examples are given below for the pharmaceutical and semiconductor manufacturing markets of how small, rugged molecular sensor (mass spectrometry) is enabling disruptive process control techniques.
Mass spectrometry for pharmaceuticals
In aseptic pharmaceutical manufacturing, a common and critical solution for preservation and transportation of pharmaceutical product is to use lyophilization (freeze-drying) to stabilize and preserve the pharmaceutical until needed at point-of-care. The success of this process is dominated by two critical activities: accurate detection of the secondary drying endpoint and ensuring the purity of the product by detecting contamination. Historically, a Pirani gauge was used to detect the second drying endpoint, but the lack of accuracy and dynamic range of the Pirani gauge may result in residual water remaining in the pharmaceutical products, which would result in spoilage. Conservatively long secondary drying times are used to mitigate the limitations of the Pirani gauge solution. However, these result in inefficiencies plus the increased possibility of contamination. Pirani gauge solutions don't detect possible contamination, and historically, post-processing, lot-based sampling would be needed to ensure pharmaceutical product quality.
Measurements made during the freeze-drying process can be stored in the cloud (on public or enterprise networks), where additional analytics can be performed to provide process insights and reporting, plus predictions and recommendations for possible process optimization. The cloud-based software tool chain enables the intelligent Internet of Things (IoT). By moving the data to the cloud, a wealth of existing machine learning and artificial intelligence tools can efficiently uncover process optimizations. With a molecular sensor, the data being analyzed now is rich, quantitative, real-time molecular data—not just temperature, pressure and machine status information. The wealth and detail of collected data provides a path of continuous improvement, possibly further maximizing product quality, process efficiency, yield and profitability.
Important roles in semiconductor fabrication
Semiconductor process technology continues to shrink as requirements for high performance and lower power are pushed by applications as diverse as mobile communications, artificial intelligence, autonomous driving and augmented reality. Standard semiconductor processing steps include deposition and etch of materials, which are used to create three-dimensional structures on silicon wafers (molecular level manufacturing). As process geometries shrink to below 10 nm as a minimum feature size, the ability to quickly and accurately control the deposition and etch of materials to meet process tolerances has become increasingly complex. Process tolerances at 7 nm are only 1-2 nm, or less than 20 atoms (given that a silicon atom is about 0.1 nm in diameter).
Endpoint detection during etch is particularly challenging as aspect ratios get stretched at smaller process geometries. At endpoint, the concentrations of reactant and product species undergo a step change that today is commonly detectable by OES for reactive ion etch (RIE) plasma etching processes. As the exposed open area (contact hole or via) of the film being etched is reduced (less than 1% and shrinking), and the number of discrete etch steps for a semiconductor device increases (more metal layer or 3-D NAND structures), higher sensitivity, fast (rising and falling edges), multichannel detection methods at endpoint are needed. Molecular sensor analysis can play a decisive role in such a scenario by tracking the concentration changes of multiple species at endpoint and detecting unknown byproducts. Additional plasma excitation is not required with the Atonarp molecular sensor, which is important in atomic-level etch and deposition processes, as process chemistry changes mean that plasma is not used in all process steps. Molecular sensor data output may include signals for multiple signature peaks corresponding to given layers.
To manage etch and deposition complexity at less than 10 nm feature size, semiconductor process developers are turning to atomic layer control techniques such as atomic layer etch (ALE), where finite numbers of atoms (less than one atomic layer at a time) are deposited or etched from the surface of a wafer.
To achieve the control required for ALE and precision deposition of materials, real-time in-situ analysis of process chamber gases and pressure is needed, along with the ability to modulate the process plasma RF and bias in some process steps. A small inside- and outside-chamber footprint (i.e., 124 x 135 x 109 mm), fast molecular sensor is suitable for these applications as it is not invasive to the process and can be strategically located on the tool for rapid response time. The ability of Atonarp’s miniature quadrupole molecular sensor architectures to operate at high relative pressure, of as much as 5 mTorr, simplifies integration into the processing chamber. High-pressure operation also improves sensitivity, allowing for tradeoffs between speed and accuracy of measurement. Critical etch end-point detection can also be achieved based on molecular analysis of exhaust gases.
A further use of molecular sensors in semiconductor processing is to optimize the exhaust gas abatement process. The gases from a semiconductor etch process chamber often contain perfluorinated chemical (PFC) molecules (such as CF4 for etch) and nitrogen trifluoride (NF3, for chamber clean). The process utilization of the chemicals applied in plasma processes is typically less than 20%, so some of the PFCs/NF3 are found in the exhaust gases. Modern gas abatement systems can decrease such emissions. There are several abatement processes commercially available, but the wet-burn process is one of the most popular. A combination of high-temperature pyrogenic destruction and water are used to destroy and absorb harmful exhaust gases. In addition to monitoring tool condition, molecular sensors are able to modulate the gas consumption in the pyrogenic furnace by rapidly analyzing the post-burn gases to ensure the burn furnace is only on when needed and optimized when active to reduce exhaust gas contaminants to meet emerging regulatory requirements. Significant savings of natural gas burned and N2, which is used as a dilution gas, can be achieved over the life of the abatement system.
Late in the 19th century, J.J. Thompson created the first mass spectrometer. One hundred and twenty years later, mass spectrometry technology has been refined into a robust, process-ready, real-time molecular sensor solution. Rugged, fast and quantitative molecular sensors can now be part of the process architect’s arsenal for applications as diverse as paper products, food and beverage, stone, clay and glass, oil and gas, petroleum refining, primary metals, rubber and plastics, semiconductor etch/abatement/deposition, lyophilization (freeze-drying), fermentation monitoring and control, thin-film vacuum coating, leak detection, environmental monitoring, safety and security, and precision gas blending and mass flow control.
Latest from Data Acquisition
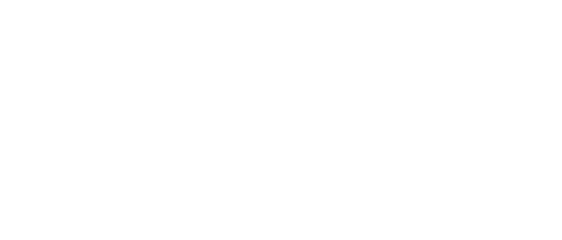
Leaders relevant to this article: