Chevron Phillips Chemical Company LP named Plant of the Year
Photo: Cedar Bayou facility in Baytown. Image courtesy of Chevron Phillips Chemical Company LP and may not be reproduced without permission.
Designing, building, integrating, commissioning and starting up a new process plant is difficult enough, but dealing with a hurricane and flooding at the same time is just plain unreasonable. Nevertheless, thatās exactly what Chevron Phillips Chemical Company LP achieved when it undertook its U.S. Gulf Coast (USGC) petrochemicals project and built a new unit at the plant for Ethylene production. Located at its Cedar Bayou facility in Baytown, Texas, the plant has a design capacity of 1.725 million metric tons/year (3.8 billion pounds/year).
The USGC Ethylene project at Cedar Bayou started in 2012, mechanical completion was done at the end of year 2017, and commissioning was finished and startup began in March, 2018. Near the end of construction, the Cedar Bayou facility also weathered Hurricane Harvey, and used its smart HART and FOUNDATION Fieldbus devices to help hasten the plantās recovery, for which it has been named the FieldComm Group 2019 Plant of the Year.
Smart control in the field
As part of the USGC Ethylene project at Cedar Bayou, the plantās automation architecture consists of a well-known distributed control system (DCS) with Field Control Station (FCS) controllers and safety instrumented systems (SIS).
Primary advantages enabled by instruments and controls using FOUNDATIONĀ Fieldbus and HART protocols at the greenfield 1594 Unit ethane plant at the Cedar Bayou facility in Baytown, Texas, include:Ā
- East of HART-based, partial-stroke testing (PST) deployed form a central asset management platform for all safety instrumented system (SIS) valves has extended the turnaround time for the unit to five years, which means more total production.
- Device diagnostics and improved asset availability, which reduced time for on-specification and on-design product to less than five weeks after mechanical installation was completed.
- Correctly installed and maintained asset management system aids troubleshooting, which speeds up problem resolution and quickly returns devices to normal working states. Less device downtime means improved production and reduced maintenance costs.Ā
- Documenting actions taken to resolve problems, which helps technicians know the best correction procedure in the future.
āWhen FOUNDATION Fieldbus and HART technology were chosen for this project, the DCS was selected because it offered an integrated asset management software platform to use with the digital information from the field instrumentation,ā says Amit Ajmeri, DCS specialist for the USGC project at Chevron Phillips Chemical Company.
In addition, the ethylene production unitās control system incorporates about 4,150 FOUNDATION Fieldbus field devices from multiple vendors for process measurement and control, and about 2,250 HART field instrumentation devices from different suppliers for its programmable logic controller (PLC) packages and safety applications. These intelligent devices were employed to help shorten start-up time with help of advanced diagnostic capabilities, while PRM streamlines and unifies integration of devices and networks, providing one centralized access point for the entire application of project.
āI had used HART and FOUNDATION Fieldbus technology before, and I knew that their capabilities would bring the value of digitalization and improved diagnostics to our new unit,ā says Ajmeri. āEstimated capital cost savings associated with using these technologies at our USGC Ethylene project made it a no-brainer for us to convince management to use them.ā
Ajmeri reports that designing the new ethylene plant to gain the advantages of the FieldComm Groupās technologies was his teamās biggest challenge. āWriting proper design specifications and change-in-project execution strategies to maximize the benefits offered by HART and FOUNDATION Fieldbus was crucial,ā adds Ajmeri. āTurnaround time for the new ethylene unit was five years, but to make it happen, we also needed to design the process unit with safety and reliability in mind because they were the criteria for the project.
āIn addition, we needed to change the work procedures for instrument technicians to gain the benefits from FOUNDATION Fieldbus and HART. Remote device diagnostics, partial-stroke testing (PST), FOUNDATION Fieldbus physical layer testing, echo curves from radar gauges, online instruction manual access and specification sheets are some of the key benefits for maintenance staff.ā
For example, Ajmeri adds that PST allowed his team to perform online testing of safety valves, so they could prolong full-stroke testing (FST) and achieve a five-year turnaround time for their process unit.
Intelligence aids recovery
Near the end of construction phase, Hurricane Harvey and its record-breaking downpours arrived in August, 2017, and put the brakes on the entire project. Similar to large parts of Baytown and Texas in general, the plant experienced some flooding. Fortunately, most of the plantās instruments, I/O, controls and field junction boxes were located above the flooding, and werenāt water damaged. The project team had verified data for their healthy-device list before Harvey arrived, and confirmed that most devices were still in the same healthy condition after the storm, so they didnāt have to perform any diagnostic checks for them.
āFortunately, we didnāt have to recommission the checked loops because we looked at the physical layer of FOUNDATION Fieldbus instruments and segments after the flood and could quickly tell if theyād been affected by the water/moisture because their communication signals would have had more noise. Because we used FOUNDATION Fieldbus for process and HART for safety, we were able to tell from the asset management system reports that they werenāt water damaged, and that was very good news.ā
Figure 1: After Hurricane Harvey flooded the Cedar Bayou plant, personnel were able to run physical layer diagnostics on their smart FieldComm instruments and loop segments, view Yokogawa PRM reports, and quickly determine that they were healthy and weren't water damaged.
Commission and startup
During the Ethylene Unitās commissioning phase, Ajmeri reports project participants sought to capture available diagnostic information during loop-check procedures. Their objectives were to confirm that asset management was fully utilized for device connectivity, as well as device description (DD) and device type manager (DTM) handling for all instruments; and create baseline data for all field assets for future diagnostics.
āFor instance, they checked to make sure control valve signatures were captured during loop checking,ā says Ajmeri. āEase of parameter setting was another key benefit of the FDT-based PRM. Control room access to parameters in all devices provided a big time saving, especially with project delays caused by the hurricane.ā
During the plantās startup phase, Ajmeri adds that asset diagnostic data from earlier project phases proved to be invaluable for troubleshooting to eliminate communication problems and other issues. In addition, plant engineers were able to streamline tasks such as fine-tuning device configurations, calibrating valves and transmitters, and optimizing functional test procedure support. Plus, they also took advantage of detailed reports on bad instrumentation.
āReducing the time for site acceptance testing (SAT), faster commissioning and loop-check, and record time for production startup were key savings generated by using HART and FOUNDATION Fieldbus,ā explains Ajmeri. āEasy access to all device diagnostics from the asset management system in the centralized control room and early indication of device performance was also essential.
āAfter successfully starting up the Ethylene Unit in record-timeājust 35 days to reach 100% on-design and on-spec productsāwe realized we could also use FieldComm Group technologies to achieve tighter control and increased production. For instance, FOUNDATION Fieldbus showed us how far instrument measurements went above 100%, so we could re-range instruments for higher range for more production capacity. Within one month, we were able to run the unit over design capacity, which can generate extra production every year. Management was very happy with the Unitās faster startup time and over-design production capacity.ā
Operations health and wealth
Now that the new Ethylene Unit has been up and running for more than a year, Ajmeri reports plant personnel are using asset management and diagnostics from a central location to help manage day-to-day asset monitoring and alarms, manage software upgrades, and create reports that ultimately reduce the cost and downtime associated with repairs.
āWeāre using predictive diagnostics from HART and FOUNDATION Fieldbus to drive a field instrumentation preventive maintenance program,ā says Ajmeri. āKey examples are temperature monitoring of pressure transmitters to make sure that heat tracing for impulse lines is working, historical reports for all FOUNDATION Fieldbus segment physical layer diagnostics, valve stroke counts and total travel counts for valve maintenance.ā
āFor example, we can track accumulated cycle counts for valves, see which valves have high total counts and are candidates for maintenance, and do it without going out. This also means we can schedule maintenance better, and technicians will know what to expect when they get there.
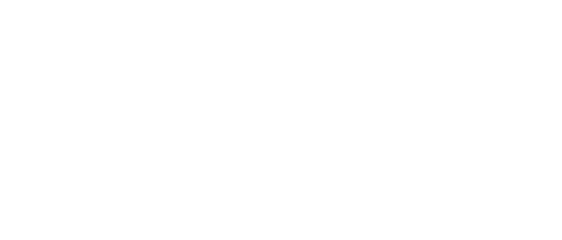
Leaders relevant to this article: