This Control Talk column appeared in the September 2021 print edition of Control. To read more Control Talk columns click here or read the Control Talk blog here.
Greg McMillan: The first versions of the proportional-integral-derivative (PID) controller date back almost 100 years, and have evolved into the most powerful and prevalent tool for basic and advanced regulatory control. Starting in the 1960s and over the five following decades, Greg Shinskey detailed the use of the PID for almost every type of application in the process industry, and showed how the PID is the best controller for handling unmeasured process input (load) disturbances.
Shinskey also showed how the PID can handle interactions by relative gain analysis (RGA), decoupling feedforward signals and valve position control. Sigifredo Nino, a Shinskey protégé, has continued his legacy, particularly in using of RGA in refineries. My entire career except for an occasional dabbling in model predictive control has been to make the most out of PID control. My 2015 Momentum Press book Tuning and Control Loop Performance Fourth Edition seeks to build on what I learned from Shinskey, confirming revelations by test cases to show what a PID can do employing often underutilized key features. Sigifredo and I did a tribute to Shinskey in the Control feature article “The greatest source of process control knowledge” that highlights what we learned with a list of Shinskey’s 7 books and 17 of his most influential articles and papers. The fact that all of Shinskey’s books documenting the treasure of his knowledge are out of print is a sad commentary on our publishing system. Fortunately, his last book, Process Control Systems Fourth Edition, is available from the Schneider Electric education department. The depth and extent of knowledge in his books will never be approached and may be lost to future generations. I am trying to keep his legacy alive through my publications and by the automation community via its technical society composing and issuing a comprehensive technical report.
The International Society of Automation (ISA) has done a great job in developing technical reports and standards for many aspects of automation system design and configuration. Back in fall 2019, I decided to form a committee of industry experts on process control to create a technical report titled "PID Algorithms and Performance."
The participation by leading experts has been exceptional. A 137-page ISA 5.9 technical report has been issued for general review and comment by the ISA 5.9 committee. Anyone can join the ISA 5.9 committee by contacting Torry Bailey at ISA headquarters ([email protected]). In this series of columns, we get the views of key ISA 5.9 contributors Yamei Chen, Pat Dixon, Mark Darby, Cheri Haarmeyer, Peter Morgan, Sigifredo Nino, Russ Rhinehart, Michel Ruel, Nick Sands, Jacques Smuts, Hunter Vegas and me.
Pat Dixon, what is particularly important knowledge provided for design and configuration?
Pat Dixon: I think the knowledge that ISA 5.9 provides that helps in design and configuration is to have a comprehensive way to explain functionality and features that are independent of any particular vendor. The way the report is constructed abstracts the details of any particular vendor, but does cover capabilities found in nearly every case. Even when a particular vendor may not offer a built-in feature, ISA 5.9 describes how an engineer or integrator could configure logic to accomplish the desired capability. It also covers caveats that must be considered during design and configuration.
For example, if feedforward capability is required for a loop but not built into a system, the report helps the engineer design and configure feedforward logic in a way that ensures the loop initializes properly when the output is disconnected (secondary loop is not in CASCADE mode). This is one example of many others in 5.9 that helps convey the proper way PID should be designed and configured. In addition, it can serve as a blueprint for anyone developing PID capability in a control system to ensure all features are covered and presented in a generally accepted way.
Greg: We're careful to not use terminology, nomenclature or diagrams from a particular supplier. Michel Ruel, how can suppliers and users benefit from the report?
Michel Ruel: Technical report ISA 5.9 should, in the near future, become the reference for suppliers. Every supporting document and every operations manual should refer to 5.9. For example, when describing their PID algorithm, each supplier should pinpoint which structure they utilize. When selecting an option, they should not only use the same terminology, but in lieu of long descriptions, they should refer to a section of the technical report. If they correctly reference this report, confusion should be reduced.
On the other hand, users will now have the basics to understand and properly select options when configuring a system. They will also have a reference to compare between suppliers even when those suppliers don't use the right terminology or incorrectly program their control systems.
If we spread the good news, customers will push on suppliers to use this reference!
Greg: We're hoping the knowledge offered in this report will increase the use of the many PID features underutilized today as those features can certainly increase loop and process performance.
We begin here with a brief discussion of signals, since they're the starting point for good PID action. Hunter Vegas, what are the key takeaways on signal types?
Hunter Vegas: Users need to realize the limitations as to update times, resolution and diagnostics.
Analog signals entering the system through native input/output (I/O) cards typically have fast update times and excellent diagnostics. However, analog data that enters through wired HART, WirelessHART or third-party gateways can have significant delays and lack the diagnostic data that comes “out of the box” with a native I/O card. The diagnostic information may be available, but it may require additional programming to access. If this isn't properly configured, the PID block may have no way to determine a signal has failed.
Users must be aware of resolution limitations determined by the number of bits on an I/O card. Assuming a bit is used for sign, variable frequency drives with eight-bit analog I/O cards have only a 0.8% resolution, and controller thermocouple input cards with 12 bits can result in steps of 0.5 degrees, causing a serious bump from derivative action.
A PID controller’s performance can be significantly hampered if the input and/or output signals are subjected to delays or poor resolution. Good control starts with high-resolution data and fast update times.
Greg: So far as the future, recent developments with Ethernet Advanced Physical Layer (Ethernet-APL) in conjunction with Single-Pair Ethernet (SPE) are a game changer, enabling much more data and much faster communications with field devices in both directions. Much more intelligence from the synergy of smart instrumentation diagnostics, data analytics, and first principle models via a digital twin can greatly increase automation system and process knowledge plus open the door to inferential measurements of key process variables, most notably composition of recycle and product streams. For much more on the opportunities, see the Control article “Ethernet-APL ready for prime time” and the Automation World article “Industrial Ethernet Advances Broaden the Network’s Value Across Industries.”
Mark Darby, what are some the important aspects of signal filters?
Mark Darby: Signal filtering is performed to remove undesirable aspects of a signal, often higher frequency components termed noise. For control purposes, filtering may be needed for effective derivative action and to avoid excessive manipulated variable movement, which can come from proportional and derivative contributions. Excessive variable movement may cause disturbances to other control loops and valve wear and tear.
If, instead of focusing on manipulated variable movement, filtering parameters are selected based on a process variable (PV) response that's pleasing to the eye, the result can be over-filtering. The additional lag that often is effectively deadtime impacts loop performance, particularly for loops that need to be aggressively tuned.
Often, derivative filtering is an option built in the PID block. If it's not and derivative action is warranted, then filtering needs to be applied to the loop PV. With or without derivative action, filtering of the loop PV may still be required to obtain acceptable manipulated variable movement. Because the PV may also be used for other tasks such as display and alarming, one may want to create a separate tag to filter the PV for the PID controller.
The following filters are often used: exponential/first order or moving average filter. A second order filter, either overdamped or Butterworth, has shown better loop performance for the same amount of manipulated variable movement than a first order filter. A second order Butterworth filter is characterized by a damping factor of 0.707, exhibiting a slight overshoot to a step change. I discovered that Shinskey’s Butterworth filter isn't equal to standard Butterworth. It has the same damping factor, but a different time constant, so if one is tuning the time constant, one will get similar results.
Because both filtering and tuning affect loop behavior, simulation can be used to determine both settings. Simulation metrics include integral absolute error (IAE), peak error, and manipulated variable travel (sum of absolute controller moves) for both load and setpoint changes. Simulation studies have shown that significant reduced manipulated variable movement can be achieved with only a moderate impact on IAE and peak error.
1-1. Seek inputs from everyone everywhere
1-2. Keep an open mind
1-3. Be a good listener
1-4. Read articles and books that advance your understanding by principle driven practical knowledge
1-5. Maximize intelligence and minimize filtering of knowledge gained and communications so that response to events is not seriously delayed and reaction to noise is not disturbing
1-6. For difficult error prone knowledge and communications, seek three inputs and use middle value
1-7. Deal with lack of rangeability by using multiple sources of knowledge and communication
1-8. Address biases in knowledge and communications by realizing effects of situational factors, limited experience, personal goals, salesmanship, and egos
1-9. Find the most recent impactful knowledge and communication
1-10. Use the most precise sources of knowledge and communication
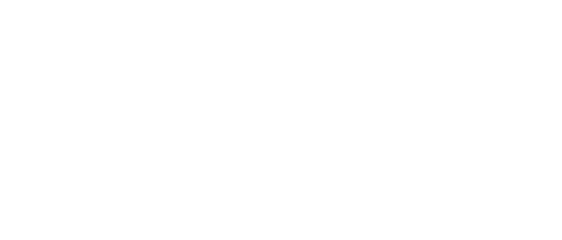
Leaders relevant to this article: