Have you ever found something to be good enough, but with very little additional effort it could be made good or even excellent? I have more than once during my career, as I’ll explain below.
After earning my electrical engineering degree, and then serving as an officer in the U.S. Marine Corps, I worked for an electric utility designing power line systems for many years—which was fine, but I craved a more hands-on experience. So, I became a licensed master electrician and worked in the field for the water/wastewater industry for a few decades (Figure 1). My years working for electric utilities were good enough, but I much preferred the hands-on water/wastewater electrician work.
During my master electrician years, I witnessed a lot of equipment failures and stopgap measures, including cannibalization of adjacent controls to keep at least one pump running. Many equipment sites are in terrible working condition. I developed a strong compassion for the operators and technicians tasked with keeping these always-on systems running, even though these systems were often designed by folks in an office someplace who never went to the field or busted their knuckles with real-life issues. I saw many systems that were good enough most of the time, but lacked features that could have made them excellent performers and easier to repair—and would have really helped those charged with operating and maintaining the systems.
This article is about how I developed pump automation panels based on programmable logic controllers (PLCs) that went well beyond good enough, but it's also a bit of a challenge to other designers in industry to think a little bigger, and consider those who will need to work with their creations for years to come.
User-focused, not custom-designed
There is a Marine Corps mantra that goes “improvise, adapt, overcome.” Those are important skills and can provide good enough results, especially in the very short term. But with some more time and resources much more can be done. For instance, a utility had 55 sewer lift stations, all with two pumps operated by floats, an alternator circuit, and a dialer that would signal trouble on high level.
However, each station was installed at different times by a different team in customized arrangements, so no two were alike. It was a nearly impossible task to maintain any sort of parts stock needed for emergency service.
As I troubleshot and worked on these different systems for the utility, meeting with operators who complained all the time about the difficult tasks before them, an idea formed in my mind and led me to develop a PLC-based system for each of these similar stations.
Figure 2: The AutomationDirect DirectLogic DL05 micro-brick PLC is DIN-rail mounted and uses removable terminal blocks, making it easy to work with. The U-Tap control panel is designed to be user friendly with clear labelling.
The system would be focused on end-user needs, with enough flexibility to work at any of the sites, even if there were minor variations among them. It was to be designed for easy installation, and to provide some diagnostics like run timers and cycle counters. It would present easily understandable alarms, such as a device failure. To the greatest extent possible, it would be standardized among the stations, simplifying maintenance and minimizing spare-part stocking requirements. Most importantly, an operator could be called to the field at any hour to any similar station, and simply swap out the module (if necessary) in a matter of minutes to return the equipment to service.
Though I had some formal 1970s-era programming experience from my education, it was not directly applicable, so I needed to teach myself microprocessor and PLC ladder-logic programming in the early 2000s. At that point, I turned to AutomationDirect and found all the products, resources and support I needed. Some key features I looked for included:
- Sufficient programming memory;
- DIN-rail mounting and pull-off terminal for easy service;
- Extra communications port for SCADA data access;
- LED indication of I/O signals; and
- Analog signal capability for pump motor current monitoring (important for developing an equipment track history and flagging potential issues such as a clogged impellor or stuck check valve).
When the first control system was ready around 2004, a site flooded by a storm surge presented the chance to install it as a first example. I had some initial concerns about how long the PLC would last because it was operating a small lift station with well over 700 pump cycles per day. Part of the design concept was to keep a spare programmed PLC on the shelf for a quick replacement, but I knew frequent service wouldn't be popular. However, over time I learned that little PLC had worked for several more years, and then was removed and placed into service at another station. Not only did it keep running, but its operation was straightforward enough for the field electrician to make the change when this station was later upgraded.
Improve, adopt, overachieve
Figure 3: An AutomationDirect C-more Micro EA3 series touchscreen HMI provides clear operational and configuration information, making it easy for operators and maintenance personnel to use the system and troubleshoot on the rare occasions when there are issues.
Using this robust PLC concept, it was possible to improve operations over and above basic functionality by adopting practical features with end users in mind, such as:
- Surge, lightning and metal oxide varistor (MOV) circuit protection to defend against electrical damage.
- For elevated storage applications, expanded design to handle from one to four pumps, with the ability to alternate up to four well pumps out of the box with built-in tracking, so all can be run simultaneously if necessary.
- Use of a pressure transducer (with resolution of 0.1 PSI) for elevated water storage to ensure the best control.
- Helpful alarms, like a float actuation sequence failure (usually caused by heavy grease interference), with provisions for an automatic control override for any float failures.
- The optional capability to monitor pump motor full load amps and upload this data for analysis, or to alert if a threshold is exceeded.
- A small, four-button operator interface, later upgraded to a touchscreen, so users could easily perform the work they needed to without being automation experts. Configuration is done by plain English prompts, with common field terminology and descriptions.
- “Plug and pump” design, with simple installation and operation so users don't need any automation expertise.
- Extensive field testing and pump-friendly features like time delays to keep from slamming equipment, as well as many anti-short-cycle features.
- “Tracking” feature for elevated water storage systems to better equalize runtimes, even when different-sized pumps were in service.
- 120 VAC panel (also available as 12-24 VDC if desired) with interposing relays to work with common control voltages and easily integrate with any type of starter.
Figure 4: With the addition of a cellular modem, the PLC-based solution can easily transmit the data end users need to create a cost-effective SCADA system.
The AutomationDirect DirectLogic DL05 micro-brick PLCs, used with a small operator interface, met all our needs (Figures 2 and 3). The PLC and other control panel components were easily installed on a standard DIN rail. Further, the removable terminal block means the PLC unit can be quickly replaced—thankfully, very rarely needed. Due to the simple graphical overlay applied to the face of the PLC, installers can connect a new unit without needing a separate wiring diagram.
This basic design was flexible enough that we adapted the same PLC and applied it for operating elevated storage, ground storage and hydro-pneumatic water stations with only software changes. The goal was to simplify the implementation to make the controller like a smart relay, so operators would have greater confidence working with it and changing settings. End users can even reset the system back to factory settings.
Originally, the old electromechanical, relay-based station controllers used an alarm dialer and a plain-old telephone service to annunciate alarms. This made sense with past infrastructures, but today a better solution is the integrated cellular modem that allows the controller to transmit the relatively small amounts of data directly to a website, bypassing expensive landline or fiber connections. This is a simple and cost-effective way for many smaller agencies to implement a very simple supervisory control and data acquisition (SCADA) system, without the need for the larger and more complex infrastructure required by many SCADA systems (Figure 4).
Useful for the end user
Creating serviceable pump automation control panels is not a glamorous job, but it's necessary to keep public utilities operating smoothly and safely. With over a dozen systems now in service and several new projects in progress, our small company has gained a great reputation for reliability and the ability to quickly upgrade any dilapidated station, while reusing existing equipment like starters where practical. By combining our end-user-centric design philosophy with reliable AutomationDirect devices, we believe we've created a flexible, helpful solution for utility operators everywhere.
Behind the byline
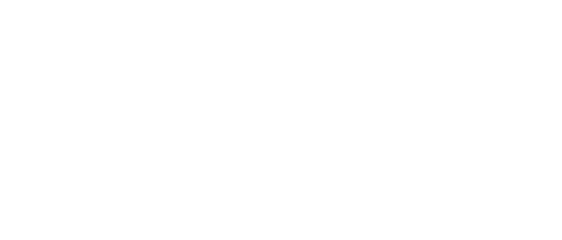
Leaders relevant to this article: