The automation profession suffers from the lack of a common understanding of the terms used and their units. By taking a closer look at key terms for plant dynamics, we can have more intelligent discussions and better recognition of the contributing factors so that we can find what part of the loop is the leading cause of poor performance whether it be excessive nonlinearity, delay, or deception.
I recommend every user get a copy of The Automation System and Instrumentation Dictionary 4th Edition published by International Society of Automation (ISA). Here I give a perspective of the role played and offer some descriptive words preceding the common terms to create more useable and descriptive terms seen in my publications and presentations but not much elsewhere. Let’s start with general terms and once we have that under our belts using a Texas size belt buckle if necessary, move on to specific terms. You can also use your cowboy boots to kick all that bull you now see out of your trail to success.
General Terms
The 3 key general terms used for describing all types of dynamics are dead time, time constant, and gain. There are two types of time constants. In almost every case we are talking about a negative feedback time constant. An important and not well understood case for a positive feedback time constant is a runaway reactor with extraordinary performance and safety considerations. A system is nonlinear if the dead time, time constant, or gain changes. Nearly all loops are nonlinear. The most common linear loops are flow or level loops (constant diameter vessel) manipulating the speed of a pump with low static head. Composition, pH, pressure, and temperature loops are nonlinear.
Dead time (delay) (sec) is the time after a change in PID output till there is a recognizable change in PID input. Dead time is detrimental wherever it exists because it prevents any recognition of an impending change in a process variable. For an unmeasured disturbance the peak and integrated errors are proportional to dead time and dead time squared, respectively. An increase in dead time makes a loop closer to instability unless retuned. Dead time slows down the setpoint response.
Time constant (lag) (sec) is the time for a variable to reach 63% of the final value once the variable starts to change (after the dead time has expired). For runaway processes it is a positive feedback time constant that is the time for a variable to reach 172% of the process value predicted by process gain. A time constant in the process is beneficial in terms of slowing down the effect of an unmeasured disturbance upstream of the time constant (most prevalent case is a disturbance at process input instead of process output as shown in control theory text books). A time constant in the automation system or path of the manipulated flow to the point of entry of the disturbance slows down the recognition and correction. A time constant anywhere slows down the setpoint response. An increase in the largest time constant can reduce the peak and integrated errors observed if the PID is retuned. If the time constant is in the measurement instead of the process, the actual process errors are greater than the observed errors due to filtering action. An increase in any of smaller time constants increase the dead time in a first order plus dead time (single time constant and dead time) approximation.
Gain is the change in output divided by the change in input to a part of the process or component in the automation system. The units depend upon the part or component. For the PID whose internal algorithm uses % inputs and % outputs, the gains used to reflect what the plant does and how the PID reacts are dimensionless (%/%). For a steady state response, the gain is a final change in output divided by a given change in the input. The gain here is the slope on the plot of the output versus the input. For an integrating response, the gain is a ramp rate divided by the given change. For the PID, an integrating gain reflecting the response of a process is 1/sec (%/sec per %). A high control valve gain (steep slope of installed characteristic) can magnify signal error, deadband, and resolution or threshold sensitivity limits. A low control valve gain (flat slope of the installed characteristic) can cause wandering and excessive wear of the valve. A high process gain is beneficial in terms of increasing sensitivity to detection of disturbances but if too high like in pH can cause excessive variability from valve deadband or resolution or threshold sensitivity limits and measurement noise. In general a high measurement gain is desirable because it corresponds to a smaller span and better accuracy when error is % of span.
Specific Terms
Total loop dead time (total delay) (sec) is the sum of all the sources of dead time in the loop that can originate in the process and automation system including the PID controller (termed the process dead time in most of the literature). A fraction of all time constants smaller than the largest are converted to dead time. The fraction approaches one as the ratio of the small to large time constant approaches zero. For practical purposes, small time constants are simply summed with all pure delays to estimate the total loop dead time since we usually underestimate the total loop dead time. Dead times from transportation delays are inversely proportional to flow and can dramatically increase at low production rates. The delay from discontinuous devices is ½ the cycle time plus the latency (time after that start of the cycle until the result is available). Thus, the delay from digital controllers is ½ the module execution time and for digital transmitters is ½ the update time. For chromatographs and most at-line analyzers the delay is 1.5 times the cycle time plus any delay from sample transportation and multiplexing.
Primary time constant (primary lag) (sec) is the largest time constant in the loop. Hopefully it is in the process but it can be in the automation system (termed the open loop time constant in my publications and presentations but is termed process time constant in most of the control literature). This time constant is defined by making a test with the controller in manual (open loop).
Secondary time constant (secondary lag) (sec) is the second largest time constant in the loop. Hopefully it is in the process but it can be in the automation system. This time constant is defined by making a test with the controller in manual (open loop). For integrating processes (e.g. batch) and runaway processes (e.g. highly exothermic reactors), the secondary time constant has a huge effect that can be compensated by derivative action (PID rate time = secondary time constant).
Open loop self-regulating (steady state) process gain (%/%) is the final change in the PID input in % divided by a fixed change in the PID output in % for a self-regulating process (termed the process gain in most of the control literature) with no disturbances. An open loop gain is the product of the manipulated variable gain (e.g. valve or variable speed drive gain), process gain, and measurement gain. For self-regulating processes the time units of a manipulated flow are cancelled by time units in the process gain. This is not the case for an open loop integrating process gain.
Open loop integrating process gain (1/sec) is the ramp rate of the PID input in %/sec divided by a fixed change in the PID output in %. In the control literature, the integrating process gain may have engineering units because the academic is looking only at the process. The integrating process gain is the product of the manipulated variable gain (e.g. valve or variable speed drive gain), process gain, and measurement gain. The units of 1/sec result from time units from the manipulated flow not cancelled out by the units in the process gain. For level the manipulated gain of kg/sec per % PID output are not cancelled by the process gain units of meters level per kg or the measurement gain units of % PID input per meters level.
Manipulated variable gain (e.u./%) is the change in manipulated variable per % change in PID output. For loops directly affecting the process, the manipulated variable is flow. The manipulated process input is almost always flow (exceptions are power for electrical heaters or speed for agitators). Thus, the manipulated variable gain is the slope of the installed characteristic of the valve, damper, guide vanes or variable speed pump, fan, or compressor. Here, I use the more specific term valve gain or variable speed drive gain in my publications and presentations. For upper level loops in cascade control or model predictive control manipulating the setpoint of the secondary loop directly affecting the process, the manipulated variable gain takes on the units of the process variable of the secondary loop. Here the manipulated variable gain is the secondary PID process variable scale span in engineering units divided by 100% PID output. Thus a change in secondary PID measurement calibration, valve trim and valve to system pressure drop ratio or variable speed drive capacity and static head will affect tuning.
Measurement gain (%/e.u.) is the change in % change in PID input for a change in the process variable in engineering units. Since nearly all smart measurements are linear, the measurement gain is 100% divided by the PID process variable scale span in engineering units. Thus a change in secondary PID measurement calibration will affect tuning.
Process gain (e.u./e.u.) is the change in the process variable in engineering units divided by the change in the manipulated variable in engineering units. The most common manipulated variable is flow. The process gain for continuous composition and temperature control is the slope of a plot of the change in process variable versus a change in the ratio of the manipulated flow to feed flow. Since the slope is nonlinear often getting steeper at low ratios and the required abscissa being a ratio to feed flow, the process gain tends to increase dramatically at low production rates.
Response Time (sec) is meaningless unless the % of final response is specified. It is used to quantify the dynamic response of an automation system component or steady state process. It cannot be used to describe an integrating or runaway process. 63% Response Time (T63) is the time to reach 63% of the final response (total loop dead time plus primary time constant in a first order plus dead time model). 86% Response Time (T63) is the time to reach 86% of the final response (total loop dead time plus 2 times the primary time constant). 95% Response Time (T95) is the time to reach 86% of the final response (total loop dead time plus 3 times the primary time constant). 98% Response Time (T98) is the time to reach 98% of the final response (total loop dead time plus 4 times the primary time constant).
Finally, take heart that while sometimes like this last week for me you may be called the “tail wagging the dog”, by more intelligent discussion you can graduate from the tail of the dog to the eye of the dog.
Continue Reading
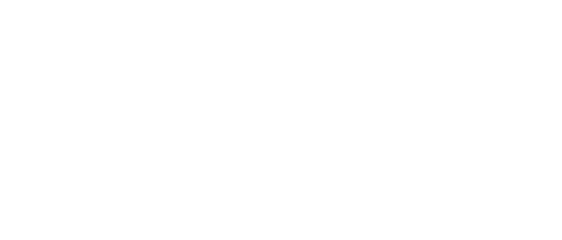
Leaders relevant to this article: