Megan Ray Nichols is a STEM writer and blogger. More of her work can be found on SchooledByScience.com, and she can be reached at [email protected].
The impact of the Internet of Things (IoT) is already evident in industries ranging from health care to agriculture. Not surprisingly, it's spurring progress in chemical process control, too. The connected sensors, devices and apps comprising the IoT can help chemical engineers improve chemical process control to increase the likelihood of consistent results while reducing the probability of production delays or shutdowns.
When a company has a fully optimized process, it has successfully identified which of the variables in the process yield the best results. Generally, an enterprise has a single and measurable goal that helps it define what constitutes the best results. For example, one optimized process might give cost savings while another allows for more production without sacrificing quality.
Here are some of the ways that IoT technology supports chemical process control.
Helping chemical plants move into the future
Successful brands in the chemical sector must continually make improvements regarding safety, efficiency and other aspects that contribute to their bottom lines. Many companies realize the IoT is the solution for meeting their goals. In one case, Texmark Chemicals, which manufactures hazardous components for the petroleum supply chain, recently entered the last segment of a three-phase plan to incorporate the IoT into the company's practices.
More specifically, the plant manufactures dicyclopentadiene (DCPD), a polymer used in products like printer ink, insecticides and varnishes. Growing demand for DCPD was one of the main things that urged Texmark Chemicals to invest in the IoT for better chemical process control. Moreover, the company's insurance deductibles doubled due to its need for an up-to-date inspection plan.
The company knew it needed to update its control system to facilitate more timely inspections, too. One of the ways it did that was by installing IoT sensors on the pumps that move products through the chemical processes. A misaligned pump can significantly decrease the expected lifespan of the part, causing production disruptions.
Texmark Chemicals employees currently spend 35,000 hours per year monitoring the plant, resulting in more than $1 million in inspection-related costs. Although the company has not yet determined how much money it'll save because the IoT sensors allow reducing the number of hands-on inspections, company representatives expect substantial improvements. Moreover, IoT technology helps chemical plant workers achieve processes in 90% less time.
Also, because the IoT sensors give so much data at every stage of the process, engineers can see what's happening at all times, allowing them to spot problems or notice areas for improvement. Having access to such information that both enables enhancements and prevents problems should put Texmark Chemicals in an excellent position to meet the growing market needs — and that's just one example of how the IoT can help.
Assisting with ongoing and predictive maintenance
Chemical process control requires managing the small details that equal the as-expected results at a plant. If companies start becoming haphazard with some parts of their processes, catastrophes can result. Fortunately, there are automated solutions that take care of various requirements. For example, one of the most significant challenges in the manufacturing of high-purity chemicals is cleaning the equipment.
Automating the cleaning processes keeps equipment running without compromising production output. Scheduling equipment allows businesses to guarantee that it doesn’t occur during peak operational hours. If businesses apply IoT sensors to machines, they could get alerts that remind them to clean the equipment frequently enough to match a chemical plant's needs. Then, it becomes less likely that human error might become a detrimental aspect that compromises chemical process control. Additionally, IoT sensors can also program specific lighting. Chemical cleaning often requires a blacklight to verify that contaminates aren’t still in the equipment. By creating a system of “smart blacklights” the company can improve their cleaning efficiency, by syncing when they turn on to the end of the cleaning cycle.
The IoT can also assist in letting plant employees know how to react so they maintain the equipment in ways that prevent process disturbances that lead to ceased operations. In one case study, a company received a leak detection alert related to an underground tank containing chemicals used for aluminum anodizing. A previous issue with the tank caused an unplanned shutdown, and the company wanted to avoid a repeat of that outcome while looking into the matter.
Plus, the nature of the chemicals created hazards to humans, making a manual inspection of the tank unfeasible. The company ultimately solved the problem with an IoT-enabled mobile robotics platform that delivered a high-quality video feed of the tank's condition and gave workers the details they needed to make a preventative maintenance analysis. This method saved 30 labor hours in inspection time.
Some companies involved in chemical process control also use related technologies like artificial intelligence (AI) to examine the data collected by IoT sensors and receive notifications of potential disruptions before they happen. These examples show how technology can make both everyday maintenance and preventable problems easier to manage.
Enabling chemical plants to meet a nation's needs
IoT technology is also beneficial when chemical plants need to scale up their production capabilities when a country's chemical plants are collectively unable to meet demands. Ramping up production runs the risk of compromising quality control, especially if facilities try to increase output at unsustainable levels.
But, IoT technology can cut down on possible problems. It typically does so by automating many parts of the process and giving plant workers data that could indicate when things are amiss.
A chemical plant in India called Deepak Nitrate recently invested in IoT technology to increase its production of phenol and acetone. Before the plant grew its availability, the availability of phenol in India only met 22% of the country's needs, resulting in India paying about $400 million in import costs. However, the production of phenol in India went up by approximately 80% due to Deepak Nitrate's IoT investments.
In this example, Deepak Nitrate recognized that using the IoT to boost its chemical process control would allow the company to facilitate more profitability internally while having positive external impacts for the country at large. As such, it showed that it's possible to retain an emphasis on quality while significantly increasing production, all thanks to the IoT.
Promoting continual process improvements
Chemical plants commonly have hundreds or thousands of control loops. Each one relates to something specific about the broader process of producing a chemical that adheres to standards. One control loop might maintain the proper temperature while another monitors the flow level of a substance moving through a pipe. Statistics show that more than 35% of control loops have associated issues.
Then, they run at below-optimal levels. Addressing control loop problems means maintaining the correct functionality of individual components such as valves. Plant operators tune those parts of machines as a necessity for excellent chemical process control. Improper tuning negatively affects the control loop and can hurt chemical process control as a whole.
IoT equipment can identify bottlenecks in a complete process while also continuously optimizing the plant's operations — using something often referred to as performance supervision.
The information provided by IoT equipment can help chemical plants tweak their equipment, have more awareness about the effectiveness of their control loops and identify steps in a process that could be particularly well-suited to automation. That last point is particularly helpful if companies are eager to investigate the benefits of automation, but don't know how to get started.
Since IoT sensors gather data and give managers all-encompassing visibility into a plant's operations, it becomes possible to see process shortcomings and research how to improve them through automation or otherwise. Taking that step could help brands excel during their day-to-day operations, plus make them more prepared for regulatory inspections and other events that require proving the ability to meet chemical process standards.
Purposeful IoT investments are worthwhile
As the coverage here shows, chemical plants invest in IoT tech in the most relevant ways to meet well-defined needs. So, when company representatives think about how they might allocate some of their budgets to buy IoT equipment, they should first identify what problems or challenges the technology could solve. Doing so ensures companies spend their money wisely as they explore how technology promotes better chemical process control.
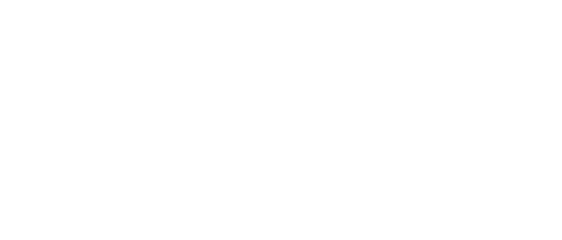
Leaders relevant to this article: