This article was printed in CONTROL'sĀ September 2009 edition.
By Dan Hebert, PE
If your plant has batch processes, significant production improvements can be realized by converting all or part of your processes to continuous operation. These improvements are summarized in Table 1 and detailed in the next section. They include but are not limited to increased throughput, better quality and less energy use.
- Improve quality
- Increase throughput
- Reduce inventory and associated storage
- Reduce raw material usage
- Reduce waste products
- Improve process safety
- Reduce air, water and power utility usage
- Reduce required floor space
- Reduce cleanup time
10.Ā Reduce operator involvement
Fortunately, others have blazed a path before you and are happy to relate their experiences. Read on to find out how your peers have successfully converted batch to continuous, reaping the benefits of improved operations.
Why Upgrade from Batch to Continuous?
You know that upgrading all or part of your processes from batch to continuous will be challenging, so why do it? "Continuous operations yield more consistent product quality, more predictable behavior and a better opportunity to maintain and perfect a steady-state process," says Carl Wikstrom, Ph.D., PE, director of research and development at Rineco Chemical Industries in Benton, Ark.
- More precise measurement and control
- Continuous flow and level measurement
- Modulating flow and level control valves
- On-line quality measurement
- Real-time quality control
- Tight control systems integration of each process step
- Extensive personnel training, particularly for operators
- Redundant controls and instrumentation
- Quick corrections to all process variations
- Advanced process control
A reason cited by an automation engineer at a pharmaceutical plant is that in a continuous process, manufacturers cam increase product yield because they don't have to discard material during start-ups and batch ends. Mark Hron, a cheese and dairy electrical engineer with Kraft Foods, notes the following benefits of converting from batch to continuous. "You can slow down or speed up production to match packing line speeds. Filling and emptying time lags can be reduced. Less operator input and interaction is needed, so labor is saved."
Integrators on Board
Bachelor Controls (www.bachelorcontrols.com) is a systems integrator headquartered in Sabetha, Kan. Bachelor worked with a brewer to convert a fermentation process from batch to continuous (See Figure 1). "The new process has resulted in much more consistent alcohol production," says Marvin Coker, senior project engineer with Bachelor.
Another integrator details benefits gained by switching from batch to continuous. "Continuous production minimizes intermediate storage of in-process materials that often have relatively low shelf life," notes Delmar Schmidt, an applications engineer with system integrator Melfi Technologies (www.melfitechnologies.com) in Ontario, Canada.
"Significant safety improvements can also be realized if these in-process materials are toxic or explosive," adds Schmidt. (See "Continuous Processes Safer," for more details.)
System integrator Optimation Technology (www.optimation.us) is headquartered in Rush, N.Y. It converted a 90,000 gpm, 17-cell industrial cooling tower water makeup system for a New York-based chemical company from a mostly manual batch operation to highly automated continuous control.
AĀ shift operator spent half his time adjusting makeup water to the towers via 17 valves," observes Dan Curry, senior process control engineer with Optimation. "Chemicals for water treatment were also added periodically by operators. The manual/batch operation of water and chemical addition resulted in large quantities of wasted water and water treatment chemicals, as well as inconsistent water temperature and chemical concentration. The cooling towers and associated water headers were segregated into five groups, and a level transmitter and control valve were used to automate water makeup and chemical additions."
He adds that "Benefits included reduced operator involvement, reduced energy consumption and reduction of heat exchanger and piping fouling due to lower chemical concentrations. Fewer chemicals were sent to the sewer and less water was sent to drains. Finally, the new system exhibited improved stability of chilled water supply temperature and lower demand of water from the central plant."
The benefits of switching from batch to continuous are substantial, but these benefits can't be realized by overcoming some significant automation challenges.
A Higher Level of Control
Simply put, continuous systems required a much higher level of control than batch processes. "With continuous operation, the control system needs to be able to correct more quickly, reliably and robustly to changes from steady-state," notes Wikstrom.
"With batch systems, there's usually an opportunity to pause the process and make corrections if things go awry. Not so with continuous processes. Operators no longer have the luxury of just pausing equipment, so they have to develop isolation strategies to keep an upstream issue from affecting the downstream processes. (See "Continuous Processes Need Redundancy," at the end of this article for more details on this batch-to-continuous conversion.)
For the aforementioned brewery fermentation processes, loop control of four fermenter tank levels was a particular challenge. "In a typical process, a loop response time might range from a few seconds to a few hours, but this project often had loop cycles of 24 hours or more. Inventive advanced process control techniques were developed to deal with these significant time lags," says Coker. "These techniques consisted of using much smaller gains, and then adjusting the bias for the PID loop based on the differences in the control variable (CV) output to the valve for the upstream and downstream fermenter level controls. Since the flow cascades through the four fermenters to the beer well, the flow out should match the flow in. Flow metering was not available between fermenters, so the differences in the CVs were used to approximate flow and the loop was biased based on that difference."
More Precise Measurement
Batch processes can be paused when things go wrong, but continuous processes often cannot. This means that instrumentation needs to be more reliable, often through the use of redundant transmitters. (See "Continuous Processes Need Redundancy," at the end of this articleĀ Ā for more information on how redundancy increases reliability.
Most batch processes use off-line measurements made in a lab to control quality and production. With continuous processes, these measurements now need to be moved on-line. This presents numerous instrumentation challenges, up to and including the use of soft sensors that infer process parameters when no direct measurements are possible.
"A soft sensor is a mathematical model based on first principles and empirical data that can approximate measurements based on various process parameters," explains Ric Snyder, senior product manager at Pavilion Technologies (www.pavtech.com), a Rockwell Automation company.
Hron of Kraft Foods details other measurement problems that can arise with continuous control. "There can be problems when going from a single scale in a batching system to multiple flowmeters in a continuous system. Often, extra calibration work is required along with more data monitoring. Most seriously, continuous processes may need sensors that just don't exist."
Not all processes can be converted from batch to continuous, but for those that can the benefits are substantial. The automation challenges involved with making the switch are significant, but can be overcome. The batch manufacturers that make the switch for all or part of their processes will forge ahead, while those that remain mired in the batch world will fall behind.
Dan Hebert is Control's senior technical editor.
Reactor Goes Continuous
In 2000, Bayer MaterialScience started up the world's first commercial continuous process for the production of polyether polyol at its Channelview, Texas, facility. The process had previously used a batch reactor, one of two reactors on-site.
"Continuous processing is inherently more efficient than batch processing," observes William D. Wray, PE, engineering consultant with Bayer. "However, in many processes, including ours, you can't simply decide you want to manufacture continuouslyāthe technology has to allow it. For us, the switch was made possible by a new catalyst with kinetic properties that allowed continuous processing,' continues Wray.
Bayer had a number of specific drivers for going continuous:
- Increased throughput ā The continuous reactor is about one-third of the size of the remaining batch reactor, yet can produce 1.5 times as much product.
- Increased energy efficiency ā The continuous process uses about 25% of the energy used for the batch process.
- More consistent product quality ā Although automation has made Bayer's batch products very consistent, continuous production quality and consistency is even better.
- A greener process ā The new catalyst technology eliminated the need for refining the reactor effluent into saleable product. In the conventional batch technology, the catalyst must be removed from the product. The new catalyst is only present in parts per million, has no deleterious effect on the product and need not be removed.
"The continuous process produces no waste, so every pound of feed is a pound of product," notes Wray.
Aside from mechanical changes, including beefing up the agitation in the reactor and adding cooling capability, instrumentation changes were needed.
Feeds previously batched into the reactor with a weigh vessel are now metered using redundant Coriolis flow meters and control valves. "We had previous experience with Coriolis meters for some reactor feeds, such as propylene oxide, but not all. The relative quantities of feeds not only control product quality, but also affect process safety by ensuring adequate catalyst feed to the reactor," explains Wray.
A second change affecting instrumentation is in level measurement, as the level instrumentation now needs to handle over-ranging caused by liquid full operation.
"Our plant was built in 1988 with a strong commitment to ISA-88 style modular batch automation, and the operations staff insisted we apply the lessons and techniques learned in batch automation to the converted continuous process. As it turns out, applying batch automation principles to continuous processes is pretty logical," feels Wray.
"There have been several papers presented at WBF - The Organization for Production Technology (www.wbf.org) conferences on this topic, and WBF continues to lead the expansion of ISA-88 principles into continuous operations. I recommend WBF as a resource for those contemplating a switch from batch to continuous. From an automation philosophy perspective, it might not be as big a change as expected," advises Wray.
Applying Batch Principles to Continuous Control
McEnery Automation (www.mceneryautomation.com) is a system integrator in St. Louis, Mo. Its president, Michael McEnery, PE, is the vice chairman of WBF - The Organization for Production Technology (www.wbf.org)."We've seen a trend to convert pure batching processes to semi-continuous in-line blending, and we've implemented these systems for several customers. A major reason is accommodating an increased number of finished products,"explains McEnery.
In several of these processes, one or two base products are still created in large quantities with a typical batch operation and stored in dedicated tanks. These base products are then used to create smaller quantities of the finished products through a semi-continuous in-line blending process. The final product may be stored in a finished product tank, but more likely it will be delivered directly to a packing line or rail car (See diagram below).
Besides the elimination of finished-product storage vessels, there are several other operational advantages. The blending process creates the exact quantity of product required, and it can be stopped or extended with minimal reaction time. This eliminates short-shipping a production run because the batch size is too small or having extra buffer capacity in each batch. It also minimizes the amount of over run, especially if a production run is terminated early because of equipment or supply chain issues. The amount of scrap material left at the end of the run is so small it is typically sent to a common reblend tank.
From a process control perspective, these continuous or semi-continuous blending applications can use ISA-88 batch control standards. "ISA-88 ideas and principles are flexible enough to work with different processes. Once you begin to view your process equipment as a collection of equipment and control modules and your procedure as a sequence of phases, the actual process type becomes somewhat insignificant as the boundaries between batch and continuous blur," observes McEnery.
The biggest instrumentation challenge for these continuous processes is product quality testing because there is no room for error when the finished product is going directly to a packing line, truck or rail car. "Our customers have implemented sophisticated in-line instrumentation to monitor key quality parameters such as color, calorie content, alcohol content, oxygen levels, pH, flow rate and temperature," says McEnery.
"Modifying a QA department's mode of operation to real time has been a challenge as the QA process needs to react in minutes rather than hours. But with in-line QA, issues can be detected immediately, rather than after the completion of the entire batch, thus reducing the amount of scrap or rework material," he adds.
For further information on WBF's role in the application of S88 to continuous processes, see the WBF web site for archived papers and presentations. Dennis Brandl, WBF member and author of "Design Patterns for Flexible Manufacturing," will be presenting a one-day expert seminar on "Non-Stop 88ā Applying Batch Methods to Continuous and Discrete Processes" at the ISA Expo 2009 on October 5, 2009. Registration information can be found at http://www.wbf.org/catalog/pages.php/page/39.
Continuous Processes Need Redundancy
An automation engineer at a pharmaceutical firm relates his experiences with converting from batch to continuous in a tablet making operation.
"The biggest improvements were to product yields because we weren't discarding material during start-ups and batch ends,"relates the engineer. "For continuous runs, I could set PID parameters to maintain tighter control responses, and the final product became more consistent because of fewer interruptions."
The plant identified mission critical devices and networks and then developed redundant controls. The plant also needed to take devices and instruments offline for calibration checks and maintenance functions without taking down production.
Ā
Three mission critical areas were identified: solution application, air flow and temperature. For temperature, three redundant temperature sensors were used. The control system switched from one sensor to another for maintenance.
The three temperature probes performed constant calibration checks. If a primary probe began to drift while the other two remain constant, then the controls switched from the primary to one of the backups. The controls were designed to alternate among devices at startup to ensure that the backups wouldn't fail due to lack of use.
The process also used a redundant solution skid that contained a pump along with automatic inlet and outlet diverter valves. Based on flow and solution pipe pressure, the system would automatically switch to the backup solution skid and alert maintenance of a solution skid problem.
The controls were set up so that the control variable output to the primary pump would be redirected to the backup pump. After a few seconds to allow the pump to reach speed, the diverter valves would slowly operate to accurately control solution flow.
Once the diverter valves were completely cycled, the loop control would be switched to automatic and the primary pump would be shutdown. If the solution deviated from parameters during this process, the controls would open a dump flapper to dump tablets into a reject bin until the process was brought back in control.
The air flow was controlled the same way as the solution with redundant supply and exhaust fans, motors and drives. If any of the devices failed, the control system would divert immediately and dump accordingly.
The plant had to develop strategies to isolate areas of the process to keep an upstream issue from affecting downstream processes. The controls also had to sequentially bring areas of the process up during start-up, and to sequentially stop areas of the process at the end of a production run.
"Continuous processes work great if you're producing a bulk material. We only have one continuous process, and it was very difficult to switch mindsets from batch. The entire continuous process included other upstream devices, such as weigh feeders and tablet presses that could be isolated with minimal impact to the process. But the continuous coating process is something that couldn't be stopped once the tablets enter the chamber," notes the engineer.
Continuous Processes Safer
A North America-based global manufacturer of aerospace carbon-fiber composites historically produced resins via batching. The batch process was easy to understand and control because of the isolated process cells, but batching forced the manufacturer to produce and store large quantities of volatile resins. Equipment needed to be cleaned between batches, and the plant needed to dispose of the residual material.
With continuous operation, resin production would be directly slaved to and immediately consumed by downstream operations, eliminating the requirements for intermediate storage and reducing cleaning requirements.
After extensive material testing at multiple blender suppliers, a continuous processor from Readco Kurimoto (www.readco.com) was selected (see Figure 2). "Readco's twin-screw co-rotating design has movable and interchangeable mixing elements that can be quickly rearranged to optimize production of different resins,ā says Delmar Schmidt, an applications engineer with system integrator Melfi Technologies (www.melfitechnologies.com) in Ontario, Canada. Melfi designed, installed and commissioned the new continuous system.
[sidebar id="4"]
"Factory test results showed improved consistency of the mixed resin. Continuous operation minimized in-process resin, and also reduced safety concerns because of the closed nature of the processor," adds Schmidt.
"System cleanability was enhanced due to mixing element close clearances and a self-wiping design. The clean-up between product changeovers simply consisted of the addition of a few gallons of solvent or cleaning agent circulating within the blender. Quite often the solvent could be saved and reused, reducing disposal costs," he notes.
The old batching process was a series of disconnected steps that each functioned as an island of automation with minimal control system integration. When the batch process reached a logical stop point, it was easy to measure, check and approve before pushing to the next step.
But the continuous process had to operate in a steady-state condition that required all process equipment to function as a single system. Specific start-up and shutdown sequences were required to ensure the processor wouldn't overload with powders, and the processor had to be purged of toxic or flammable ingredients when not in use.
Most of the suppliers of the liquid and powder process equipment at the plant provided stand-alone proprietary controllers, greatly increasing the difficultly of control system integration. So the manufacturer asked Melfi to devise a solution that would allow the entire continuous process to operate as one closely integrated entity.
Melfi chose to eliminate all of the proprietary controllers and replace them with a Rockwell Automation (www.rockwellautomation.com) solution consisting of a Process Automation Controller (PAC), PowerFlex EtherNet/IP motor drives and a Factory Talk SE touch screen HMI.
Perhaps the main challenge was controlling the continuous loss-in-weight feed subsystem. For control of this subsystem, Melfi linked the PAC to Hardy Instruments (www.hardyinstruments.com) weight transmitters via a dedicated EtherNet/IP network. The feeder control algorithms were then performed in the PAC, while the weight transmitter provided a direct local connection to the load cells.
The HMI displayed and controlled the entire process via a central recipe system. "Now that the continuous process has been integrated into a single system, the plant is enjoying the benefit of reduced manpower to manage the resin line. The composites manufacturer is already planning additional continuous process lines for North America and Europe," concludes Schmidt.
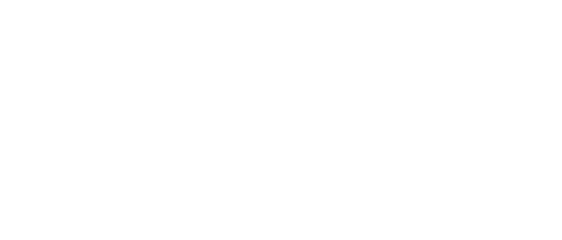
Leaders relevant to this article: