By David W. Spitzer
Nuclear power was the rage back in the 1960s and 1970s until the incidents at Three Mile Island (1979) and Chernobyl (1986) brought nuclear power plant development to a grinding halt. Despite these setbacks, nuclear energy represents approximately 20% and 80% of the electricity generated in the United States and France, respectively. Recent fossil fuel price increases and concerns regarding global warming refocused attention on the development of more nuclear power plants because nuclear fuel is less expensive and because nuclear plants inherently do not generate greenhouse gases.
Nuclear power plants were typically licensed to operate for 40 years, and their design, construction and operation are strictly regulated. Rigid documentation requirements form significant impediments to upgrading instrumentation in nuclear power plants, especially when the operating license nears expiration.
However, the nuclear industry is constructing new nuclear power plants. In addition, many nuclear power plants are now renewing or in the process of renewing their licenses, so they can operate for another 20 years. Newer technology, plus additional years of operation, combine to increase the viability of upgrading the obsolete and cumbersome existing instrumentation systems that are difficult to maintain.
Larry Witt, director of applications of the Nuclear Division at Weed Instrument classifies nuclear power plant instrumentation, based upon its operating environment. The most demanding environments (Class 1E harsh) are inside the containment structure with exposure to high levels of radiation. These instruments are typically applied to important monitoring, safety and shutdown applications. They are qualified to environmental standards such as IEEE 323 and IEEE 344 that describe testing for seismic effects, thermal aging, radiation aging, vibration and loss-of-cooling accident.
Not Everywhere, But Lots of Places
Some instruments cannot be adequately age-tested for the full 40-year plant life. Witt adds that, temperature elements and other simple devices can usually be age-tested for 40 years. However, pressure and temperature transmitters can often be age-tested for 10 to 20 years, so they are replaced when their age corresponds to the age-test period in the environment to which they are subjected. Microprocessors in particular do not fare well in high-radiation environments, so analog instrumentation is commonly applied in these harsh locations.
Less demanding environments (Class 1E mild) are generally located outside of containment and used for safety functions. Less rigorous thermal and radiation testing is required to qualify instruments in these locations. In locations with low levels of radiation, microprocessor-based instruments can be applied. However, the required software verification and validation of these devices is both extensive and expensive, so many plants opt to install analog instrumentation in these locations, even though microprocessor-based transmitters are superior and might allow the plant to generate more electricity.
Nonetheless, fieldbus instruments could be used in these applications with appropriate qualification and testing. Willard Killough Jr., PE, instrumentation engineer at Duke Energy Carolina Oconee Nuclear Station in Seneca, S.C., is using, fieldbus instrumentation in some mild non-safety environmental areas including the borated water storage tank, bleed holdup tank and concentrated boric acid storage tank.
However, there is a significant amount of instrumentation in nuclear power plants that is located outside of these areas, where the equipment will not be exposed to radiation including the boiler, generator, cooling water, cooling tower and utility systems. These locations are often termed balance of plant (BOP) applications, where microprocessor and fieldbus equipment are acceptable. Witt estimates that the amount of instrumentation in Class 1E (harsh), Class 1E (mild) and BOP is approximately 10%, 20% and 70%, respectively.
Nuclear power plants in North America are typically operated continuously at or near their operating limit because this strategy tends to reduce the purchase of imported fuel while reducing cumbersome load changes. Shutdowns are generally limited the 20-to-30 day window required to refuel approximately every 18 months. Killough says, It is costly and difficult to make changes due to documentation issues that include drawings, calculations and the review process that entails operational and safety reviews. As such, the cost of hardware, software, configuration and installation is often minor compared to the paperwork involved.
Easier, Quicker, More Consistent
Killoughs experience indicates that upgrading to fieldbus was not that complicated.
Replacing 48 old recorders with multi-channel monitors was more difficult than upgrading to fieldbus because the logistics of working on the monitors in a concentrated area were more challenging, he says. In contrast, the fieldbus bricks (junction boxes) were installed prior to the outage. The outage time was used to replace the pneumatic system with a fieldbus system. The fieldbus system underwent both a factory acceptance test and a site acceptance test where approximately 90 transmitters were calibrated and configured in 4 days.
Figure 1. These new cabinets are located in the cable- spreading room in a mild environment that is air conditioned and heated to 66 °F.
Killough found that the work performed during the site acceptance test was easier, quicker and more consistent than previous tests that he performed. He attributes this to a combination of people and technology. In particular, the technicians were interested in the technology and were able to easily understand and use it.
He adds that, during the outage, the new instrument cabinets were installed, and the racks were replaced in approximately 45 days. The net result is that the plant now has the infrastructure to add points onlineeven though the plant typically prefers to wait to make changes during an outage.
David Larson, consulting engineer at Duke Energy Carolina Oconee Nuclear Station adds that, fieldbus saves approximately 40% of the wiring costs, since one cable can be used to communicate with multiple transmitters or devices. Some existing analog cables were tested and reused for fieldbus communications, the longest of which was approximately 180 meters (600 feet). Cable installations were typically twisted shielded pairs in interlocked or braided armor cable. These changes provided a fieldbus infrastructure by replacing existing instruments and utilizing the existing cables for the infrastructure. Most of the instruments replaced had previously provided process data to an operator aid computer or provided indication in the control room. With the infrastructure in place, the one twisted shielded pair cable would support eight to nine transmitters or devices that could be added to the segment at any time.
Six control loops were installed after their control valves were retrofitted with fieldbus positioners, he explains. The fieldbus installation was easy, and control of the turbine oil cooler control valve and F feed-water heaters is now significantly better.
The fieldbus equipment has a human-machine interface (HMI) with monitoring and trending that was not available with the pneumatic system. Larson adds that, In a few instances, logic is now performed with fieldbus relays (solid-state relays) because the existing (hardware) logic could not change in order to provide a wire-for-wire replacement of existing wiring. Even with this constraint (without constraints, the logic could have been performed in software), this implementation is more accurate, simpler, and easier to maintain as compared to the old system that had pneumatic pressure switches that provided dry contacts to the various interlocks and annunciators.
Art Martin, principal instrumentation and control engineer at Burns & Roe, Oradell, N.J., concurs that it should not be a problem to use fieldbus technology in BOP applications. Regarding non-BOP applications, Art says that, various aspects of the use of digital electronics of instrumentation and safety applications are currently being studied by the Nuclear Regulatory Commission (NRC). Key issues include diversity and defense-in-depth, digital communications, and cybersecurity. Newer nuclear plants in Europe and Japan use digital controls, but not digital measurement devices. There are ongoing NRC research projects focused on the above issues that are applicable to both new and existing nuclear plants.
Cutting Cable Cost
Martin sees fieldbus technology reducing the cost of cabling. Kevin Cole, assistant chief instrumentation and control engineer at Burns & Roe, adds, Fieldbus technology reduces drawing complexity as compared to using conventional measurement devices. However, the overall cost of the drawings is similar because more time is necessary to layout the segments. Nonetheless, fieldbus system installation costs are lower. Retrofitting existing installations can be costly because changes related to safety require the implementation of a 5059 process that analyzes the entire system to ensure that the change does not impact plant safety.
Martin adds, even non-safety changes require a significant amount of paperwork, including updating calculations, specifications, drawings (including as-built), and instruction, operating and maintenance manuals.
The two-way communications offer maintenance savings, while reducing the exposure of personnel to the process. Ideally, fieldbus technology would be great in mild and severe environments from a maintenance perspective. Unfortunately, this has not yet been full embraced, says Martin.
Fieldbus technology is typically 20 to 40 years newer than most of the existing technology installed in the BOP portion of nuclear power plants in North America. Many articles have been written about the virtues of fieldbus, including its lower installed cost, easier troubleshooting, extensive diagnostics and the like.
However, Mike Miller, engineering supervisor at Duke Energy Carolina, whose team is currently installing fieldbus instrumentation in the Oconee Nuclear Station says, Cost savings and faster startup may be nice. However, the major benefit that fieldbus technology brings to nuclear power plants is usually omitted from everyday discussions. In one word, our major benefit is the scalability of fieldbus technology. Our existing instrumentation is 30 to 40 years old and difficult to maintain. Documentation and installation issues make upgrading cumbersome and expensive, so, in the past, we have replaced broken equipment with equipment of the same 40-year-old design just to keep the plant operating. Even if an instrumentation upgrade were economical, it might take as long as a decade from inception to final implementation. The ability to add instrumentation to a fieldbus segment without affecting the remaining instruments on the segment (scalability) will allow us to change virtually all of the instrumentation without waiting for a major outage. This gets us over a large operational obstacle while providing significant cost savings attributable to reduced documentation, implementation and scheduling requirements.
Interoperability
The principle reasons that Duke Energy selected a fieldbus solution were integrity, interoperability and diagnostics, says Fernando Liboni, project manager at SMAR, Sertaozinho, Sao Paulo, Brazil, who supplied Duke Energys fieldbus instrumentation. Integrity is a critical factor in power plant operation that was formerly addressed using pneumatic instrumentation. Duke selected Foundation fieldbus technology instrumentation to achieve similar system integrity and reduced the number of potential single points of failure by implementing control strategies in the Smar System 302 host and field transmitters.
In addition to reliability, fieldbus technology also provides the interoperability between equipment provided by different suppliers. Redundant fieldbus segments working in conjunction with diagnostic information available to the operations and maintenance personnel provide online information that can be used to better diagnose and fix problems often before the process is affected.
Duke Energy was also able to use existing cables previously used for electronic instrumentation for over 30 years. This reduced the cost of the project, length of the shutdown, and start-up time because only the bricks and field equipment needed to be installed. Liboni adds, instrument availability has been 100% since the first start up in 2005. With this infrastructure in place, Duke Energy continues to add fieldbus loops to replace pneumatic instrumentation.
In short, fieldbus technology appears to be viable for both new and existing nuclear power plants. Not only can it replace legacy systems economically, but also provide advanced diagnostics and scalability to provide operational benefits and flexibility in the future.
David W. Spitzer is a principal in Spitzer and Boyes LLC
845.623.1830 or www.spitzerandboyes.com
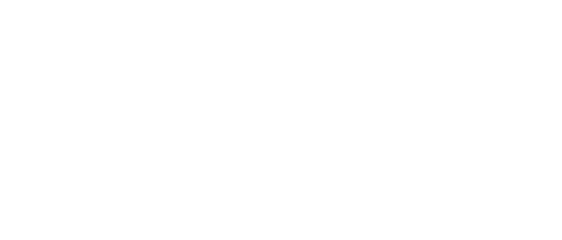
Leaders relevant to this article: