By Gary D. Nichols, PE
This is the tenth article in this series of Controlglobal articles on process analyzer systems, and the third and last on process analyzer system reliability, maintenance and service. (See PAT System Reliability and Process Analyzer Reliability, Maintenance & Service.) Inasmuch as these articles cover the lifetime costs of process analyzer systems, we must address the wear-out and obsolescence of analyzer systems.
While it would seem at first glance that dealing with wear-out and obsolescence would be a simple matter of replacing a necessary analyzer system and permanently removing analyzers that are not in use, for whatever reason, we shall see that the matter is not quite so simple in every case. Financial and regulatory considerations supplement technological wear-out and obsolescence factors in the decision to remove and/or replace analyzer systems—or not.
Financial justification is usually the reason for removing an analyzer system from service. One financial justification might be that service and maintenance costs have risen above the cost of capital or annual depreciation for the replacement. However, recall from previous articles and personal experience that replacement analyzer systems may be more costly than expected due to safety, ergonomic, environmental and technological improvements to the analyzer system since its original installation.
You might also want to remove an analyzer system from service because of poor performance or because you need the physical space for other uses. The system could also be an experimental installation that did not meet expectations or one that is inherently is out of safety or environmental compliance. To understand these justifications, it is helpful to remember that an analyzer system installation typically has a lifetime of 10 to 20 years, during which any of these justifications might arise.
Technological improvements which result in improved safety and environmental considerations, better accuracy or precision, up-to-date communications modes, new analytical methods, more ruggedness, improved stability to power-line upsets, lower service and maintenance costs, etc., may justify replacing an analyzer system. Analyzer systems seldom are replaced precipitously for these reasons, but technological improvements may accelerate a replacement schedule.
Lastly, regulatory requirements may necessitate replacing an analyzer system. Personnel protection, loss prevention or environmental regulations can all motivate replacement. Personnel protection issues could include the ways sample or calibration fluids are vented and disposed of, exposed hot or cryogenic surfaces or electrical wires, poor ergonomics, and dangerous (glass) sample-handling components. Experimental analyzer installations are usually in a special expensed class of assets.
Usually, replacement or removal is sold based a combination of financial, technological and regulatory. Although some of the reasons may be difficult to put in financial terms, financial justifications generally lead the way. Again, this is a good time for the analyzer engineer to consult the capital equipment accountant and the operations manager responsible for the analyzer.
Some Questions to Ask about Replacement versus Repair
- Is the system still safe to operate and maintain? – This is a question of regulatory obsolescence and personnel safety.
- Does the analyzer system still do what it needs to do? – This is technological obsolescence. It may not be an analyzer system problem if the operating requirements have become tighter due to market and process requirements.
- Does the analyzer system still need to be doing what it is intended to do? – This is technological obsolescence. Consider that other control and process changes have addressed the problem that previously justified the analyzer system.
- Is the analyzer system still supported by its manufacturer or other ongoing sources of parts, service and information? – New analyzer models replace older models; vendors usually give advance notice, sometimes as much as 10 years. Some analyzer system vendors and suppliers go out of business or are sold to owners who discontinue the analyzer product line.
- Is there something better to replace the current analyzer system, given cost, obsolescence and performance.
- Is there an opportunity to replace the current analyzer system, e.g., turn-around, revamp, other outage, non-critical need? – Unanticipated opportunities sometimes become financially or ergonomically advantageous for improving an analyzer system installation before it is technologically or legally necessary.
- What’s the system’s salvage value? See “Disposal” below.
- Should the system be abandoned in place or physically removed after decommissioning – Operations and analyzer maintenance sometime abandon an analyzer system “in place” if it doesn’t interfere with the safe operation of other equipment. The analyzer system can be used for spare parts for similar system.
Defining Our Terms
Finally, let us become familiar with some of the terms that are helpful when discussing analyzer system wear-out and obsolescence. These terms probably are defined in engineering project cost accounting. They are usually expensed items, but the analyzer project engineer should check with the capital equipment accountant or cost engineer regarding their proper use as capital or expense for the specific project.
- Repair – Repair is used here in the conventional meaning of the word: stopping a leak, replacing a power supply, replacing a needle valve or unplugging a sample line. Repair also may refer to repairs to an analyzer system location rather than the analyzer system itself; this may include thermal insulation, electrical or signal wiring, emergency lighting and signals, etc.
- Replacement – Replacement refers to replacing an analyzer system “in kind” or with an “improved” installation. An analyzer system that is truly “in kind” or identical to the existing system can usually be paid for on a maintenance budget, but a replacement system with significant improvements, whether desired or not, should come from the capital budget. Consult your capital equipment and/or tax accountant.
- Relocation – In some cases, an analyzer system is not obsolete. Relocation to a more convenient spot will solve the problem. This is often the case with peripheral equipment such as gas cylinder racks, lighting, junction boxes and process sample points.
- Reapplication – Reapplication usually refers only to the analyzer and assumes that the sample conditioning system will have to be replaced. Frequently an existing analyzer that is unsuitable for its current application can be “reapplied” by its manufacturer for a new, unfilled, application that has developed since the original installation. Reapplication may involve putting new valves, columns and detectors in a GC or new sample cell, optical filters, and source in a photometric analyzer. Reapplication of an available “old” analyzer is not always inexpensive, but it can save time and money over a new analyzer.
- Decommissioning – Decommissioning can be as simple as turning all analyzer system switches and valves to the “off” position and cooperating with an operations representative to apply “Do Not Operate” or similar safety tags to the utility and fluid cutoff points. Be sure to deactivate and eliminate the corresponding analyzer alarms in the control room.
- Decontamination – Decontaminating refers to making an analyzer system slated for removal safe for personnel to work on. This may mean forcing air or neutralizing fluid through the tubing, steam cleaning, immersing in neutralizing solution or washing down with soap. Decontamination extends to making the equipment safe for a recycler or metal salvager.
- Demolition – Demolition is removing the analyzer system and preparing the site for its next construction. With proper isolation and safety measures, decontamination can take place after demolition or dismantling. Dismantling and demolition are identical.
- Dismantling – Dismantling and demolition are identical, though one should be aware of company-specific and site-specific definitions.
- Disposal – Disposal refers to recycling and salvaging. Generally, analyzer systems consist of cast metal cases and stainless steel wetted parts. Lack of precious and semi-precious metals in analyzer systems and their small size relative to abandoned process equipment, usually make recycling and offsite salvaging unprofitable. Because of this, worn out or obsolete analyzer systems frequently can be used for spare parts. The analyzer engineer should check with the tax accountant before doing so.
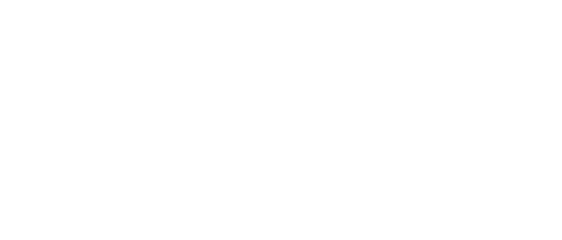
Leaders relevant to this article: