By Jim Montague, Executive Editor
How can you play power chords on a Stratocaster if the strings aren’t there? Most youngsters would likely say all you need is a guitar-like interface with lots of colorful buttons. So, if you need training on a process control system that hasn’t been built yet, what you need is a good simulator.
Steam by the River
Figure 1. Staffers at Con Ed’s East River Repowering Project in New York City learn to run their new truncated, combined-cycle, 320-megawatt power plant with help from Emerson Process Management’s Scenario simulation software.
This latest, multi-million-dollar, East River Repowering Project (ERRP) migrated the plant from boiler/steam turbines to new truncated, combined-cycle equipment, including two new GE gas turbines, two heat-recovery steam generators (HRSGs) and one steam ring header. Basically, the gas turbines generate electricity, and the HRSGs recover waste heat to make 1.2-1.5 million pounds/hour of steam more efficiently for heating and cooling Manhattan’s numerous skyscrapers. However, these new technologies meant there was no way for Con Ed’s operators to get the training they needed ahead of time.
“We starting adding design data into our simulator, so the Dell PCs running the simulated plant model ensure the simulator’s Sun Microsystems’ Solaris operator workstations provide power plant control data consistent with the workstations on the actual plant control system. These workstations allow plant operators to monitor pressure, temperature, flow elements, valves, current and voltages,” says John Mansell, shift supervisor at Con Ed’s East River facility. ERRP uses Emerson Process Management’s Scenario simulation technology and its Ovation control system. “We used to train in classrooms and do on-the-job training (OJT), but this retrofit’s new technology meant that OJT wasn’t available, and so it was even more important to simulate start-ups, shutdowns and other scenarios.”
To Training and Beyond
While seeking the best ways to educate their operators, Con Ed’s engineers also evaluated how ERRP’s simulation logic was going to work at East River and found they could pretest the system before commissioning. Doing this uncovered items that might otherwise not have been found, such as control of raw water to the plant, a lack of recirculation capability, and pump and valve cycles that weren’t the same type.
“The new gas-turbine and HRSG technologies extended through our plant’s distributed control system (DCS), but we didn’t know how they were going to work together before commissioning because we’d never integrated them in our DCS before,” says Hsiu-Chen Wang, senior engineer in Con Ed’s Central Engineering and Mechanical Controls group. “By putting all these elements together in a simulator before commissioning, we were able to check, verify and validate all these parts before start-up, and that was a tremendous help. In fact, we cut our start-up time from three or four months to just one month.”
Mansell adds that its $1.3-million simulation allowed ERRP to begin using an iterative process. For example, simulating designs before implementation turned up issues that could help revise those designs before startup. “So, when the plant went into full service, all the data from commissioning was loaded back into the simulator, which made it even better,” he explains. “The plant’s reliability is now better than 90%, and our operators can learn on a seamless simulation tool that’s the same as what they’ll use in the plant.”
Similarly, if Con Ed’s operators and engineers later find process improvements they want to do, these ideas can be tested on the simulator first and then taken to the DCS if they’re approved. “Simulation is much more than a teaching tool,” adds Wang. “It’s a multi-purpose device that can help every aspect of engineering and operations.” In fact, Mansell adds that Con Ed’s Scenario simulator even allows it to take some I/O points off scan and see how its real plant system would be affected. “This means we can go into the plant with a lot more confidence in the adjustments or repairs we have to make because we know more about the possible risks involved,” says Mansell.
Show, Don’t Tell
In short, Con Ed’s experience demonstrates why this motto is so useful to teachers and trainers. It’s because specific demonstrations are far more effective at conveying and instilling useful information than vague descriptions. Hands-on, on-the-job (OJT) training in any activity engages more of the body’s senses and neurons and so builds stronger pathways in the brain for deeper, longer-lasting learning.
Want to learn more about Simulation and Training online resources?
Check our simulation page!
Unfortunately, OJT takes time and often can’t convey unusual problems or emergency situations. So, in the past, only big-ticket process applications could afford to reproduce enough of their hardware and proprietary software in mock-ups accurate enough for useful training. Sadly, belief and investment in simulation have often only followed tragic accidents, such as the laws requiring simulation training on all North Sea oil and gas platforms established after the Piper Alpha explosion and fire that killed 167 men in 1988.
Fortunately, in recent years, ever faster and more affordable computing power have enabled steadily improving emulation systems and simulation software, and allowed users to implement increasingly realistic simulations in more diverse and smaller applications.
“It’s becoming a lot easier and more affordable for us to use simulation for training in process applications,” says Ed Diehl, owner of Concept Systems, a systems integrator in Albany, Ore., and Seattle. “I can simulate a complex control system with my laptop while sitting on an airplane because I can emulate the controller and HMI from a real process on a PC. Though a few users are asking for bids that include simulations with their factory acceptance test (FAT), we’re not seeing too much demand from customers. We’re actually doing a lot more simulation ourselves because it costs less, helps us meet our schedule, and it reduces our risk onsite because there’s less shutdown time, etc.
“We’re emulating control systems by running logic, toggling bits and changing address values in response, but we’re not simulating real I/O points yet. I think this will increase in the future, however, because it’s becoming easier to develop and use graphical mock-ups and simulation tools. They help us communicate designs, even as part of the proposal effort. For example, we use SolidWorks software to communicate designs because it’s more effective to show a client a 3-D demo than 10 paragraphs of text. It’s also easier to maintain design details and document code by showing them graphically.”
Amazingly, this growing sophistication and use of simulation is even beginning to blur traditional lines between design, training and operation. For instance, system integrators putting in controls systems are finding their displays and plant-floor data can be exported and reproduced for design tweaks and training, designers are learning their simulations can be retained to help identify problems before configuration and start-up of actual control systems, and trainers are discovering their educational tools can be used during their application’s whole lifecycle.
Reproducing the Real
Fueled principally by computing’s growing power and declining costs, the most important evolution in simulation is its incorporation of plant-floor data into increasingly sophisticated models to create more accurate representations of individual applications. Though they’re becoming more affordable, software-focused simulators usually retain some type of cockpit controls and/or an HMI duplicating plant-floor stations, as well as connecting to a math mode-based emulation of the actual control system. In the past, implementing a simulator often meant buying an added control system, but now users can take their DCS and put a virtualized training version on a PC.
For instance, to help build the immense, China-based Shanghai SECCO petrochemical complex on schedule, its engineers employed Honeywell’s UniSim operator training simulator (OTS) to quickly test, modify, retest and deploy control solutions and operating strategies. SECCO reports its simulator saved three weeks by avoiding engineering-phase start-up issues; helped design the facility’s advanced process controls (APC) and annually retrain operators; and is synched to incorporate any plant changes or modification as part of its regular engineering routine.
“The benefits of implementing OTS were huge for SECCO because large, commodity chemical enterprises must be able to avoid shutdowns,” says Paul Bowdler, SECCO’s production director.
Similarly, Dassault Systemes reports that its 3-D design and simulation tools are being used for training purposes. “Users are taking our 3-D mechanical models and applying controls data via PLCs to perform virtual validations,” says Michael LaPerre, Delmia’s global business development director. “Simulation can save a lot of headaches. It’s like taking Advil just before you need it.”
LaPerre adds that Dassault’s year-old Virtual Design and Production strategy allows users to train and be ready before actual control systems are built, which again is far less costly than training after installation. “One U.S. automaker we work with expects to save 50% in debugging, commissioning and reworking by using this method,” he says. Also, bi-directional synchronization between Delmia’s mechanical design and controls creates tags and references in its users’ PLC software, which aids concurrent engineering, virtual commissioning, and plug-in software emulation. This enables PLC code to run in Delmia’s 3-D model, which lets users check nominal behavior of their devices, run what-if scenarios, and perform training exercises.
Want to learn more about Simulation and Training online resources?
Check our simulation page!
Even inexpensive, Excel-based training tools are allowing users to quickly customized front ends onto dynamic models, so they can deploy simulations with little or no programming experience. “For example, our Aspen Simulation Workbook lets users drag and drop variables into the front end, so users in the plant can play with the model,” says Glenn Dissenger, Aspen Technology’s senior Operator Training Simulator (OTS) product manager.
Keeping Knowledge Handy
Besides gaining resolution and preserving the know-how of the many baby boomer engineers expected to retire soon, simulations also are crucial because they can better train users in procedures, events and problems that rarely occur in today’s automated applications and facilities.
“A refinery may run three to five years before turnaround, and so one compressor may not shut down for five years. However, the technicians on staff after a shutdown and repairs may not know how to start that compressor up again,” says Jim Siemers, Emerson’s educational services group manager. “A good simulator will let users practice any skill or malfunction they want and assess their responses, too.”
For instance, by updating and maintaining its simulation tools as part of its maintenance program, Shell Canada Ltd. reports it can more easily check the flowmeters in its mass-balance modeling practice and detect which are bad or trending toward it. Assigned software can then flags these devices to the maintenance management system, and possibly even automatically create work orders for them. Shell uses Invensys Process Systems’s SimSci-Esscor Romeo platform for data reconciliation, interfacing to the plant historian, flow compensation modeling, scheduling reconciliation runs, and e-mailing reports to users.
“First-principle simulation models always have been an indispensable part of conceptual process design. Such rigorous models now are increasingly becoming standard tools for operator training and online operations decision support,” says Harpreet Gulati, director of Invensys’ hydrocarbon simulation products. “The boundaries between design, training, and operations support are dissolving due to consistent model techniques and platforms across various applications.
“This means developers and users can look at simulation in a much boarder scope, and come to see it as part of an overall design, training, and optimization process. This combined view needs users to adopt a consistent approach that retains data and good practices as they move from design to training and from operations to optimization. Prior models become outdated because users think of them as one-shot events, but today’s simulation software is flexible enough that it can continue to provide quick updates that reflect current plant conditions, and can be used by a broad community of users in the plant.”
Branching Out to Networks
Because most simulations can be easily reproduced for multiple users, they also can be distributed via industrial networks and the Internet over wide geographic areas to standardize training for operators at many sites. Siemers adds that simulators initially focused on design and optimization, but now are used to validate configurations. “A good simulation can find errors and ease plant start up even before it’s used for training,” he says. “Some engineers may use it informally to familiarize themselves and teach each other, and then educators can use their results information to develop a more formal curriculum, but it may now have training on possible upsets.”
For instance, when Tyco Healthcare/Mallinckrodt used Mynah Technologies’ MiMiC software to handle calculations in an evaporator, the simulator saved time by identifying code problems. “Instead of four days, we were able to go live in four hours,” says Lucinda Weaver, Tyco’s principal instrument/control system engineer.
Likewise, while building Ineos Chlor’s new chlorine plant in Runcorn, Cheshire, U.K., in 2006, its engineers decided to use Visual Solutions Inc.’s VisSim simulation software, which it’s been using in other applications for about 10 years. However, this time Ineos Chlor’s engineers wanted an OPC interface with their simulation, which models the chemistry, heat and brine-treatment mass balance of the plant’s three-stage process. Ineos Chlor’s distributed control system (DCS) uses Emerson’s Delta V, which is linked to the plant’s training simulator model that has upwards of 12,000 blocks and a five-layer hierarchy.
“We thought it would be useful to have OPC to interface the model with the controllers and let us train operators while the new cell is still being built,” says Philip Masding, Ineos Chlor’s process control manager. “We tried to build a training simulator a few years ago, but we had to use analog I/O cards to establish a 10-signal link between the controller and the model. Now that VisSim has OPC, we’ve got close to 200 signals. We’re going to get the operators familiar with the controls, and even throw in a few faults. We want to get things right in the simulator, so there are no surprises when using the real thing.”
Better Experience = Better Education
While many simulation tools look exactly like the controls they represent, and use actual plant data so they’ll respond in the same way as the application, most sources agree that simulators can’t be used for control—yet. However, even though simulation still has some limits, many users are pleased with the gains they’ve made. For example, Wang and Mansell report that Con Ed’s simulator provides better training more quickly to its new operators. So far, the simulator has been used to train about 20 operators, or four on each of the plant’s five regularly scheduled watches. New operators go through 10 weeks of classroom training and three weeks on the simulator, while experienced operators get three days of refresher training on the simulator each year.
“I can run drills on the simulator, such as upset conditions, failed equipment, and recreate other real events,” says Mansell. “This is a much better quality educational experience.”
Selecting Your Simulator
To choose and install the most appropriate simulator for your process application, users and integrators recommend the following basic steps:
- Define your training objectives. What do you need your operators to know to make your application more successful?
- Examine your existing training program. What new skills do you need from your simulated training environment?
- Project what personnel will be involved and what their roles will be.
- Adopt a consistent simulation approach, which also includes design, training, and eventual application optimization.
- Decide what part of the application needs high-fidelity simulation and what parts are less crucial.
- Quantify costs, benefits and savings of proposed simulator, and seek sponsorship from senior management.
- Select a competent supplier and integrator, if needed, and clearly define expectations and deliverables.
- Redefine the scope of the project in accordance with available funding and time schedule.
- Install simulation software and hardware and use it to test new controls, train operators, maintain processes and add future equipment and capabilities.
A Journey from Control to Simulation
While the traditional design-then-build procedure might seem logical for simulation, at least one system integrator has found the opposite path to be true. It might be counterintuitive, but well-established controls apparently can form the foundation of a useful simulation and training program.
“There’s been lots of evolution in simulation and training, but they aren’t meshing as well as they could yet,” says Rande Allen, training manager at Polytron, an Atlanta-based process and packaging system integrator (SI). “Many companies are good at simulation, training or integration, but very few are good at all of them. This is because their skills sets and experience historically concentrate on what they need to do right now, so SIs focused on getting systems to work, and simulation focused on modeling. For example, we were originally good at designing and installing control systems, but the question was always—how do we prepare the application’s operators to run and maintain it without our help and resources? This is the job of a good training organization.
“We still have classrooms and face-to-face education, but we’re always seeking tools to make training more effective, and today that means using simulation because it’s more hands-on and experiential. We used to go over how to operate a system by telling operators what to do when there’s a jam, painting a verbal picture in a classroom. Simulation and emulation lets us show what to do, and then have operators do it themselves by using a plant-floor interface while they’re sitting in the classroom. Being able to touch and feel the systems gives users a more realistic and interactive experience.”
In fact, Brent Stromwall, Polytron’s business development VP, says it and partner E2M’s homegrown PolySim simulation software and services grew out of the control system programming it had been doing when installing PLC-controlled, automated batch systems using products such as Rockwell Automation’s RS Batch and ControlLogix and Wonderware’s InTouch solutions.
“We’d been using PolySim to check the automation on the systems we install, and recognized we might be able to bring it to the classroom as a way to improve training,” says Stromwall. “Because we already did the PolySim emulation, we could sit with our control engineers, review their applications and create teaching tools. We took our model, used it for training, and we now have a multi-faceted PolySim program that we use with 90% of our customers. We and our users all like it because training can happen before we install a system, and, once installation is complete, its operators can use it right away, start normal operations more quickly, and get performance levels up sooner. So, not only do we have more effective training, we help users gain quicker and better ownership of their new platform.”
As it develops higher-resolution, more realistic models in the future, Allen says Polytron’s simulations will move into more phases of projects. For example, besides using simulations in design, control check-out and verification, and pre-start-up, simulations can help in concept development before design. Likewise, once an application has been operating for awhile, its simulations can be used to help with maintenance, continuing education or updated to teach users when new functions or equipment are added to the application. “We use PolySim models to post-assess the effectiveness of the knowledge transfer process, and also are looking at using other tools to help pre-assess operators and fill skill gaps.”
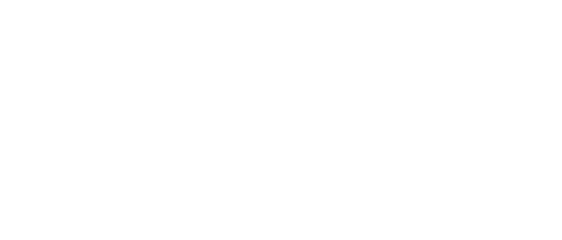
Leaders relevant to this article: