Greg: Precious few presentations exist on the potential advantages of variable-speed drives for eliminating the backlash and stick-slip associated with control valves. The best one Ive seen is in the presentation, Flow and Pressure Control Using Variable-Speed Drives by Greg Shinskey. In this paper, a VSD demonstrated a four-times faster set point response than a control valve, a rangeability greater than a magnetic meter, no measurable hysteresis, and no cogging (torque pulsing) at low speeds.
Stan: System design presents several practical problems. While for variable torque loads, such as liquid pumping, overheating is much less a concern at low speeds, the motor rating, frame and ventilation must be properly sized. When pumps feed downstream equipment with a static head (e.g., pressure controlled reactor), the pump speed must not drop the pump discharge pressure below the static pressure downstream, or there can be flow reversal, leading to some very nasty results. Automated on-off valves are required for interlocks and isolation, but even when a control valve is used, a separate automated blocking valve is added to increase reliability. In general, a throttling valve does not make a good isolation valve and vice versa.
Greg: Flow lab test results show a good globe valve with a digital positioner and a VSD provide about the same control loop performance. Details of particular cases can be cited to sway the argument for a valve or VSD. To ensure a perspective, it helps to know the normal range of key performance parameters. Control valves have a deadband (e.g., backlash) varying from 0.1% to 10% and a resolution (e.g., stick-slip) varying from 0.05% to 5%. The lowest number is for a sliding stem (e.g., globe) throttling valve with a diaphragm actuator, a digital positioner and low-friction packing. The higher numbers are generally for on-off valves disguised as throttling valves with high-friction packing, tight shutoff (e.g., high breakaway torque) and piston actuators.
Deadband and resolution increase loop dead time, create limit cycles and set the practical rangeability of the control valve via its impact on the minimum controllable flow. The stroking time of a control valve varies from 5 sec (small globe) to 50 sec (large butterfly or damper). Second-order responses have time constants of 0.1 sec to 0.5 sec and a pre-stroke dead time of 0.2 sec to 20 sec, depending again upon actuator size. The speed of the valve becomes important for fast loops such as flow, pressure and especially surge. Boosters can be added to speed up a control valve, but the combination of a booster in series with a positioner is unstable unless some of the air signal is bypassed around the booster so the positioner sees the larger volume of the actuator.
A VSD has a hysteresis ranging from 0.05% for tachometer feedback to 0.2%, and a resolution ranging from 0.05% for a 12-bit A/D input card to 0.2% for a 10-bit A/D input card. The lower numbers are improved on some drives by the use of special speed encoders and 16-bit A/D cards. The drive response dead time is negligible, but the time to ramp full scale for a VSD ranges from 10 sec to 100 sec, depending upon rotor inertia and imposed ramp rate limits. While even the lower time of 10 sec might seem long, it translates to 0.1 sec for a 1% change in speed. Most controller outputs dont change more than 1% in a scan. Following are four checkpoints for getting the best dynamics.
- Speed slip and hysteresis. For slow or integrating loops, consider the use of speed control. A secondary speed loop should be tuned to be five times faster than the master process loop sending the speed setpoint per the cascade rule. Vector control can greatly reduce slip and eliminate the need to add a speed loop.
- Dead bands or noise band settings to prevent frequent changes in speed. Minimize these settings and use a process variable filter to reduce noise.
- Speed ramp rate or velocity limit settings to prevent fast changes in speed. Maximize the ramp rate (%/sec) (ramp time minimized) based on rotor inertia and process requirements. Use a dynamic reset option in the PID controller to prevent the rate of change of controller output from reset action being faster than the rate of change of speed. If the controller output changes faster than the drive, the controller will burst into oscillations. Particularly confusing is that the oscillations may only develop for large disturbances that require big changes in speed. Big control valves, particularly dampers, are slow enough to require the dynamic reset option as well.
- Resolution of input VSD input cards. Some standard VSD input cards are only 10-bit, causing a resolution limitation of 0.2% (one sign bit). Use at least 12-bit resolution input cards.
Stan: While these issues are not well documented, they are all understandable, and youd think drive manufacturers could provide the necessary guidance. Intelligent options do exist to auto-detect motor data for setting up the drive to operate correctly. Galen Wilke, vice president at Fisher Slidning Stem Valves, found the real reasons why users are not choosing VSDs.
Galen:
- Drives are generally not built just for pumps. Many VSD menu choices and options are not pertinent to pumping applications.
- Electrical people dont like the complexitythe setup, maintenance and design issuesof the VSD. The electrical people also are not much into process control issues.
- Someone needs to do the right calculations on dollars saved. Calculations typically dont account for the drop in drive efficiency with speed, and the engineer doesnt know the duty cycle in advance. A high static head will erase the energy savings.
- VSD-to-valve comparisons are rare. Most projects dont have decision points in the project for such a comparison.
Greg: Setting up a VSD is no more complex than setting up a home entertainment system, so why do engineers relish setting up the latest TV/stereo system, but avoid a VSD even when application economics show it might be a good deal?
Why a Home Entertainment System Is More Fun than a VSD
10. 52" high-definition screen
9. Surroundsound of Eric Clapton, not inverter hum
8. An easy chair
7. Four remotes
6. Beer
5. Virtual rather than plant reality
4. Sportsunless you consider improving loops a sport
3. You cant TiVo the plant
2. You can save the best and erase the worst
1. Only slip you is sliding into is your vinyl recliner.
Stalking the Wild Process Parameter
What are implications of an integrating or a runaway process response on control dead band, resolution and stroking time requirements?
Send an e-mail with your answer to the Puzzler, CONTROL questions, or comments to [email protected].
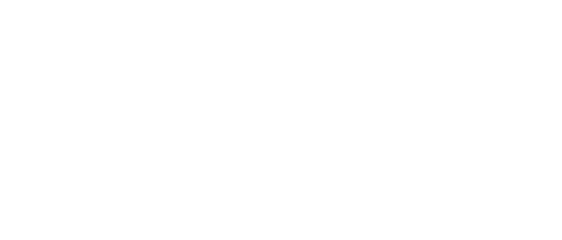
Leaders relevant to this article: