See our Wireless Guide at www.controlglobal.com/wirelessguide.html
Some have called it a coming inflection point in the manufacturing industry. Some have called it a curse and a potential weak spot perfect for cyber hackers to exploit. Many are waiting for the hype and the FUD (fear, uncertainty and doubt) Even more are confused.
Here weāll try to clear up the confusion and help you find your way to the best use of wireless communication technologies in your plant.
Weāve spent the last two years learning about wireless, going so far as to join the ISA SP100 standards committee, and so weāre pretty much up to speed. Weāve even done original researchātwo surveysāfor this article. The first (see sidebar āSurvey Snapshots Wireless Usersā), undertaken by Control under the auspices of SP100, details the responses of 499 end users over a four-month period. The second was a survey of attitudes toward fieldbus and wireless. It is available at www.controlglobal.com/fieldbusmarketreport.html.Ā Both surveys are original, and the data is presented here for the first time.
Weāve also produced some web-based material that will help you broaden your understanding of how industrial wireless works. At various points in this article, weāll refer you to the ControlGlobal.com website, where you will find videos, podcasts, and extended versions of parts of this article. For web-based information, look for the .
The important thing, though, is to keep focused on what wireless technologies will do for you. Will they make your job easier? Complicate it unmercifully? Help or hurt?
A Brief History of the Wireless World
Wireless communications in the industrial world grew directly out of the telemetry methodologies developed in the 1950s and 1960s for rocketry and space exploration. Very quickly, industries such as the power, water and wastewater utilities, and oil and gas pipelines discovered that they could use radio to monitor, and in some cases even control, their far-flung assets. Throughout the later 20th century, first with walkie-talkies and then with cellular telephony, end users in utilities, discrete manufacturing, and the process industries found ever more uses for wireless communications.
By the mid-1970s, SCADA systems in water/wastewater, oil and gas and utility service increasingly were using radio communications between RTUs (remote terminal units) and the SCADA head end (the main office), where there were repeater āpanel wallsā and, finally, computerized command-and-control centers. This writerās first experience with wireless in SCADA was in 1976 doing a radio survey for a system installed by Northern Californiaās East Bay Municipal Utilities District for wastewater collection system pump stations. Wireless in control systems has been around for a long time.
The cost of leased telephone lines was the main impetus toward radio SCADA, but later, the lack of available frequencies made it harder to do, especially in developed areas.
All non-licensed industrial and commercial uses of wireless rely on a group of frequencies collectively called the ISM (Industrial, Scientific and Medical) band that were set aside by all governments to make possible the use of wireless for peaceful purposes. The ISM band is a relatively small group of frequencies, and cellular telephones, wireless telephones for home use, wireless Internet and all of the other uses you can think of, other than governmental, military, and emergency service uses, are part of the ISM band. The general rule is that no use of an unlicensed transmitter or receiver in the ISM band should interfere with the operation of any other. Remember this rule, because it is going to become important as wireless becomes more prevalent in process plants.
Wireless in Discrete Manufacturing
Many companies support wireless technologies devoted to the discrete manufacturing industries. Companies like ABB and Siemens have complete wireless networks designed and constructed for the discrete manufacturing sectors.
At the recent ABB Automation World, chief technology officer Peter Terwiesch pointed out that ABB has been a pioneer in wireless technology.āI donāt recommend wireless for critical closed-loop control,ā he said, ābut in discrete automation, it is very much the other way around.ā
In the exhibit area, ABB had a completely wireless robotic manufacturing cell, which even had its power delivered wirelessly. Wireless motion control is very much alive and well in discrete manufacturing, as is RFID (radio frequency identification). Woodheadās Ed Novotsky believes that this is where the industrial use of Bluetooth technologies will really take off.
Convergence and COTS
The IEEE has led a drive toward consensus convergence standards for wireless, and this drive has been incredibly successful. Most offices and even many homes have wireless networking technologies based on IEEE 802.11x standards. The ubiquity of āwireless Internetā has reduced the cost of components to very low levels.
COTS (commercial-off-the-shelf) wireless networking devices can be bought at pharmacies, supermarkets, hardware stores, and discount stores. Companies like Advantech,Ā ProSoft,Ā Cirronet,Ā and many others make āindustrially hardenedā versions of theseCOTS networking appliances, and sell them into the industrial markets.
Whoās Using Wireless Now?
You are, thatās who. Our survey (see the sidebar āSurvey Snapshots Wireless Usersā) shows that over 50% of you use WiFi in the plant, while 40% use proprietary wireless networks and 24% use RFID in your plants.
What seems to be happening is a sort of āguerrilla wireless.ā Maintenance organizations are working with wireless tablet PCs, such as we described in our article āWireless While We Workā in the Aug. ā06 issue .Ā Cell phones and web-enabled PDAs are running applications like Transparaās Visual KPI.Ā 802.11b, g and n nodes abound around the plant environment, in control rooms, marshalling rooms, and other sometimes unlikely locations.
Wireless Asset Management and Process Optimization
Although the wireless survey shows that only about 24% of users are interested in using wireless for maintenance systems, the big noise from suppliers and involved end users about the proposed use of wireless sensors has been asset management. Temperature, vibration, and pressure monitoring of rotating machinery has been touted repeatedly as a primary wireless sensor application, especially if low-power, low-cost, wireless-enabled sensors are common. The HART Communication Foundationās Ron Helson says just the ability to extract the diagnostic data from all the existing installed HART-enabled field transmitters and control valves would enable improved asset management, with concomitant savings. He notes that of the 22 million-plus installed HART-enabled devices, less than 10% currently extract their diagnostics in real time.
Other wireless pundits point out the advantages to process optimization using wireless sensors. The reason we originally used single-loop control was that it was easier and less expensive to do, especially with pneumatic control loops. Wireless and inexpensive sensors will change that. The mathematics is clear on this point: multiple casual measurements of multiple parameters can provide more robust and more precise measurement overall than a single highly accurate point measurement can.
āThis may be the next inflection point,ā says Dave Kaufman, Honeywellās director of business development. āThe development of ālick and stickā sensors is coming rapidly, and will make those casual measurements possible and practical.ā
The Standards Landscape
The standards landscape is still littered with overlapping standards, methodologies and interest groups.
Vendors can and do take advantage of this to sow FUD. When asked about the future of proprietary wireless networks, such as his own, Sensicast Systemsā CEO Gary Ambrosino says, āThe wireless āstandards warā taking place in industry today is far from over!ā
Yet our survey shows that more than 70% of end users want one standard or one network for many applications.
Ambrosino continued, āDriven by technology capabilities, vendor traction and market politics, the wireless industry and ongoing developments in standards bodies will continue to be in flux. Sensicast believes āproprietaryā radio systems will continue to thrive, and be deployed for as long as they can drive compelling wireless applications and provide business value to those who deploy them.ā
Ambrosino may not be wrong. According to Yu-Gene Chen, Honeywellās business unit manager for wireless, Honeywellās own surveys indicate that its primary customers in the petrochemical industry are willing to continue using proprietary networks until at least such time as SP100 announces a standard.
If SP100 is delayed in development, proprietary networks may have enough time to develop a strong foothold, and they may never be dislodged by an āofficialā standard.
WirelessHART
The good news is that standards development is moving forward. In June, the members of the HART Communication Foundation voted to approve the HART 7 Specification, and with it the standard for WirelessHART. While compliance testing methodologies have yet to be worked out, more than 10 companies, including Emerson Process Management,Ā Yokogawa,Ā Elpro ānow part of MTL, ABB,Ā and others will have WirelessHART devices, both for connection to existing HART devices, and new, WirelessHART-enabled field devices, for sale by the end of 2007 or early 2008.
Plans for this have been going on for nearly two years now, as you can see by listening to a podcast interview with Elproās CEO, Graham Moss, recorded in 2005.Ā āWeāll have a device out within six months after the specification (WirelessHART) is approved,ā Moss said.
In May, Helson and Wally Pratt, HARTās chief engineer, made a formal presentation to the SP100 committee to describe the then-proposed system, which has since been adopted as the standard. You can see their presentation on ControlGlobal.com by going to www.controlglobal.com/articles/2007/184.html.
All the Different Ways to Wireless
Many standards can mean tough decisions for process control engineers.
contributor and SP100 Users Subcommittee co-chair, Dick Caro, reported in the July issue (www.controlglobal.com/articles/2007/204.html)Ā that while the protocol specifications for WirelessHART are very close in many ways to the planned protocol for SP100.11a Release 1, they are not identical. The protocols used for the upper communications layers are not the same, making it impossible for either network to carry signals from the other.Control
The SP100 UserĀ Working Group noted that users have always stated a need for a single wireless data communications standard in their plants, and this situation would result in two non-interoperable protocols installed in the same plant areas and operating in the same radio frequency band.
There seem to be only three possible alternatives:
- Request WirelessHART to adopt the ISA100.11a protocol;
- Request ISA100.11a to adopt a protocol compatible with WirelessHART;Ā
- Do nothing and allow both protocols to be installed and manage the co-existence issues, if any.
WirelessHART already has been adopted, and vendors already are prototyping products based on the technology used for this specification. While it would make technical sense to ask WirelessHART to use ISA100.11a protocol, thereās actually nothing to recommend, since these protocol layers of ISA100 arenāt yet completed. This would unnecessarily delay the adoption and release of WirelessHART.
It might be technically feasible for ISA100 to use the same middle-level protocols planned for WirelessHART, but the HART Communications Foundation has not released this intellectual property to ISA100, nor have any of the details of its protocol been revealed.
So what does this all mean to end users? Is it safe to use WirelessHART? Yes.
Caro says, āThe situation in which both WirelessHART and ISA100.11a instruments are installed in the same plant will most often result in both networks working normally. If excessive interference occurs, it can be resolved by assignment of channels used by both protocols for their channel-hopping in such a way that they will not overlap. The user may give up efficiency and scalability of the frequency spectrum in doing this, but the impact will be local to this application alone.ā
Caro concludes, āAny interference means the ISA100 device will retry that message on a different channelāprobably not the same one as the next channel used by WirelessHART. For these reasons, WirelessHART and ISA100 will most likely coexist without problems in most situations.ā
One of the significant advantages of WirelessHART over other wireless protocols is an artifact of the dual nature of the original HART protocol: digital data superimposed on an analog 4-20 mA DC carrier. While the analog value reports the process variable, the digital data carries much more information, including additional process variables, diagnostics and calculated data. Because the digital data is being carried on the 4-20 mA signal wires, the digital data can be picked off anywhere between the field device itself and the I/O terminals to which the 4-20 loop is connected.
Several vendors have indicated they plan to produce devices that can inductively couple to the 4-20 loop from which theyāre intended to transmit HART data, pulling both operating power and digital signal from that loop. If inexpensive enough, these may be the first of the ālick and stickā sensors Honeywellās Kaufman is talking about.
ISA100: The Universal Network?
ISA100 is intended to be a single āuniversalā network for the wireless transport of information from all types of industrial wired protocols including:
- HART,
- Foundation Fieldbus, both H1 and HSE,
- Profibus, including PA, DP and ProfiNet,Ā
- Modbus, including RTU and TCP.
The proposed ISA100 Application Layer technology supports HART messages over the wireless network, along with data for other protocols providing this āuniversalā capability for the user. The Technical Steering Committee of the Fieldbus Foundation has voted to base its future wireless protocol on ISA100. A similar response is expected from Profibus International. It previously has stated its position to not develop its own wireless protocol, but to influence the design of ISA100 to meet its needs.
The One Big Network Option
In the meantime, big companies are trotting out their own, proprietary, āone big networkā programs. Smaller companies, such as Banner Engineering and Turck,Ā are producing new proprietary networks too.Ā These companies, among others, are betting that Sensicastsā Ambrosino is right.
Honeywellās entry is called āOneWirelessā and is described in this advertising videocast released at this yearās Honeywell User Group Americas in June. Honeywell wants to leverage the other wireless technologies from other divisions of the company, such as security, RFID, personnel location, hazardous gas and fire safety, as well as process information and control.
Invensys and Apprion have partnered around Apprionās ION network. You can hear a recently recorded podcast interview with Invensysā Harris (Hesh) Kagan, talking about the system, and about his chairmanship of WINA, the Wireless Industrial Networking Alliance (part of the Automation Federation) at www.controlglobal.com/wina.html.
Cisco and Rockwell have partnered around Ciscoās own brand new industrial wireless networking offering called āFirst Mile Wireless.ā In its press release, Cisco claims, āThe standard Cisco First Mile Wireless solution is architected and comprised of Cisco 1500 Series wireless mesh access points with specialized blast-proof, hardened cases, Cisco WCS for wireless network management, supported by Cisco Secure Services for network security. A combination of pretested and validated backhaul technologies, including Wi-Fi bridging, WiMax and satellite connectivity, and operation technologies and applications complete the transformation of the oilfield from an isolated, hard-to-reach location, to an oasis of information fully connected to remote expertise and analysis.ā
The Future of Proprietary Networks
The question that must be asked is, āWhat about SP100 and these proprietary networks?ā Sensicastās Ambrosino is very clear. āSensicast is actively involved in the ISA Wireless Systems for Automation standards committee (ISA-SP100). Our participation is motivated by our belief that the specification will work its way into a variety of standards and markets that will drive up both the quality and quantity of SP-100 platform solutions.ā
Honeywellās Chen and Kaufman are also very clear. āOneWireless is not a draft standard version of ISA100.11a,ā Kaufman says, ābut it does use technologies and configurations likely to be part of the final ISA100 standard.ā
Chen concurred, āWe intend to migrate OneWireless to the ISA100 standard as soon as it is adopted,ā he said at HUG in June.
Invensysā Kagan and Apprionās Fuhr, both deeply involved in SP100, have said similar things.
It is likely that Cisco will co-operate with SP100 as well.
Yet, what about Ambrosinoās comment about proprietary networks? Much can happen between now and October 2007, when the draft ISA100.11a is supposed to be finalized, and sent out for comment. And even more can happen between then and the time in 2008 when the first ISA100 standard is set to be adopted. If ISA100 is derailed, anything can happen, and most likely will.
The Early Adopters
Since there are no actual users yet of either WirelessHART or ISA100, we have to look at the end users who have been beta-testing these devices.
At the 2006 Emerson Exchange, BP Cherry Point Refineryās Marty Gering described prototyping Emersonās SmartWireless system at the refinery. Gering, wireless data collection coordinator and wireless worker adminstrator for the refinery, noted that there are many locations in the refinery where large bodies of uncaptured data exist. āThis data is valuable,ā Gering said, ābut we canāt touch it because of the expense of wiring and running conduit.ā
Emersonās SmartWireless is specifically intended to be a draft-WirelessHART network, and is guaranteed upgradeable to WirelessHART whenever the customer wants to do it.
Gering said, āWeāre sticking to monitoring and alerting only, but weāre designing the systems so that if we choose to move to control in the future, we can.ā
The next project for Cherry Point is the tank farm. āWeāre beginning a new project to wirelessly connect those tanks with backup level,ā said Gering last October. āWe have hundreds of valves that weād like to have positioner information on, as well as other pressures and temperatures. We have mixers with motors weād like to monitor current on, and lots of other things. Weāre looking at 300 points.ā Gering hopes to have the project implemented by the end of 2007.
Honeywellās OneWireless has its beta tester, too. Byron Lewis, process control specialist at Alon USAās Big Spring Refinery, in Big Spring, Tex., talked with Control at this yearās HUG. āWeāve had 100% uptime,ā Lewis said. āWe installed the gateway, and then I took a sensor and walked around every one of the proposed installation sites, and we saw if the gateway was receiving or not. It was that easy.ā
Lewis also reports on his activities in this Honeywell-produced advertorial video, also shown at HUG. (www.controlglobal.com/articles/2007/162.html.)Ā āWe deployed this system at an approximate delta of $10,000 over wired transmitters,ā says Lewis in the video, āand we were therefore able to purchase additional transmitters.ā
When asked if he would be willing to use the Honeywell transmitters for control, he seemed startled. āI hadnāt thought of doing that until just now,ā he said. āBut you know, with the reliability that weāve seen, I think I would. Theyāre as reliable as wired transmitters, as far as weāve seen.ā
David Runkle, production manager at the Lower Colorado River Authorityās Lost Pines Power Park says, āInvensysā comprehensive managed approach to the new wireless technology has enabled us to unify both plants in the Lost Pines Power Park under a common communications system. They did this at a fraction of the cost of a wired solution, while providing an extremely flexible platform for future wireless-enabled applications, including remote equipment condition monitoring and tank farm level monitoring.ā
The Lower Colorado River Authority is one of the largest power generation utilities in Texas, and has been assisting Invensys and Apprion to prototype the ION system, which Invensys and Apprion intend to migrate to S100 eventually. āThereās certainly a lot of hype in the marketplace about wireless technology being the next game-changer in automation,ā Runkle said. āAnd while this might indeed be true, it also means that the technology is still relatively unproven in many of the types of industrial wireless applications that we are considering.ā
The Nay-Sayers
Runkle is not wrong about the unproven nature of industrial wireless in process applications. Neither is Herman Storey, senior automation consultant for Shell Global Solutions, and co-chair of ISAās SP100.11 committee. He told this writer last year, āFrankly, I donāt think there are as many wireless applications as some vendors believe. Those applications that can be done with wires will be done with wires.ā
Venerable automation sage and chairman of the board of Yokogawa Electric, Isao Uchida, is also less than sanguine about wireless in the plant. āWe have invested heavily in the production of high-speed, fiber-optic networks,ā he said at last yearās user group meeting and Tech Fair. āCritical data will always move on wires.ā
Jake Brodsky, of Washington Suburban Sanitary Commission, and an automation, controls and SCADA expert, said in a recent post on the SCADA mailing list, āFolks, I like radios. Iāve been fascinated with them since I was five years old. I tinker with them to this day as an amateur radio operator. However, there is a place and time for everything. And in my opinion, unlicensed wireless gear is not suitable for plant control system infrastructure of any significance.ā
Brodsky went on to explain his reasoning. You can read the entire post on Sound Off!, the Control Editorsā Blog.
However, these concerns arenāt keeping Uchida, Storey or Runckle from investing heavily in wireless products.
Will Ethernet Sneak In and Win?
In early 2007, a small company in San Francisco, Arch Rock Corp., introduced the first commercial implementation of IP (Internet Protocol) over low-power wireless. Using the same basic radio standard that WirelessHART, Zigbee and S100.11a are using (IEEE 802.15.4), Arch Rockās technology enables standard IP communication over wireless, directly from the sensor.
Invisible Umbrella
Lost Pines Power Park uses an overall WiMax umbrella, WiFi access points and wireless speakers to unite two facilities.
Ciscoās Mark Wylie noted in a meeting in June that Ciscoās āFirst Mile Wirelessā would stop at the field controller, primarily because thatās where industrial networking has always stopped. Having sensors with the ability to communicate using IP-over-Ethernet would make it possible to bypass all of the proprietary and semi-proprietary fieldbus networks, such as Profinet, and Foundation fieldbus. ARC Advisory Groupās Harry Forbes has written an ARC Insight on this technology. It is available at www.controlglobal.lopan.html.
No one can afford to bet against Ethernet. It has become the one true network protocol because it is ubiquitous, and it is ubiquitous because it works, it is scaleable, upgradeable and easily implemented. This self-fulfilling prophecy has brought the cost of even industrially hardened gigabit Ethernet managed switches down to the low thousands of dollars, and commercial-grade products down to the low hundreds. Many industrial operations even use consumer-grade Ethernet switches hubs and routers in non-critical applications because they are inexpensive enough to be āthrowaways.ā
How to Set Up a Wireless Plan
āItās all about the network! Sounds like a Verizon commercial, but itās true,ā says Honeywellās Kaufman. āJust as cell phone customers are ramping up their wireless usage to download videos, send text messages, receive emails and, oh yeah, make phone calls, so are industrial customers ramping up their usage of wireless. But as they begin to do that, theyāre discovering a limit to the available bandwidth and functions they can execute.
āMost industrial systems today are using the ISM bands, which can only do so much, for wireless communications. So when every department in the plant wants to use those wireless bands, you get a very uncoordinated, unplanned train wreck of band usage. You limit what youāre doing now due to lack of optimization, and severely limit any future usage. If you donāt plan the usage of the wireless bands in your plant today, youāre planning to fail in the future. I highly recommend that customers develop an overall wireless plan for their facility. Take into account every departmentās needs, and plan, plan, plan. You want to ensure you are using a very limited resource in the best way possible to produce the greatest results for your operations.ā
Cherry Pointās Gering agrees. āWe set up a plant wireless governance group to deal with this issue. I am on it; the I&C supervisor is on it. Thereās somebody from IT on it, and the guy who is in charge of our Maximo CMMS system is on it, and a couple of others. Basically, if you want to bring a wireless device onto the plant site, you have to bring it through us.ā
Thatās a very good first step.
Winning at Wireless
Once youāve established a wireless technology authority for your plant, itās time to look at what you can do with wireless. First, survey what youāre already doing. You will likely be surprised at how much wireless is already in use at your plant. Then look at all of the process and process-related activity you would like to monitor wirelessly. Add to that some of the other non-process activity like personnel location, building automation, fire and gas safety and physical security that you might want to add into your systems either immediately or later. Put together an overarching plan, and then carry it out.
Many end users weāve talked to say they plan to do what Marty Gering at BP Cherry Point says. āI think it is a good idea to start small,ā Gering said. He recommended trying one of the starter kits from Emerson. Honeywellās OneWireless offering also comes with a starter kit, so end users can experiment, and not get too deep into the wireless pool.
Wireless may well be the next inflection point, but prepared end users will stay on top and in control.
Plenty More Where This Came From
ForĀ more information on wireless and the complete results of our wireless survey, go to www.controlglobal.com/wirelessguide.html
For Survey Snapshots Wireless Users click here.
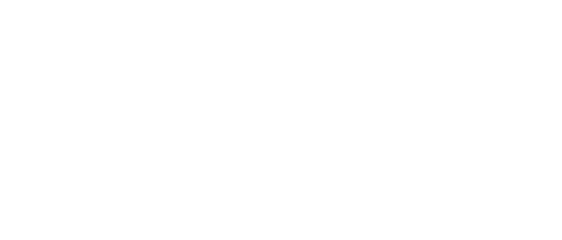
Leaders relevant to this article: