By Andrew Bond, Industrial Automation Insider
Schneider steps up ODVA participation
Major consolidation of Industrial Ethernet protocols in the works.“We believe that our strengthened relationship with ODVA will make Ethernet/IP the most widely used industrial network.” The general consensus seems to have been that this year’s Hanover Fair, incorporating the last vestiges of the once mighty Interkama, was a pretty low-key affair, at least as far as the automation industry was concerned.
That’s strange because we may look back on the week of the show, April 16-20, 2007, and the one which preceded it as the time when the automation industry finally saw sense and began to react to what its users had been telling it since at least the early 1990s: that what they really want is a single fieldbus standard that enables them freely to mix and match best of breed devices from multiple vendors within the same installation.
IEC 61158 Legacy
Of course that’s not what they’re going to get—any chance of that finally disappeared with the IEC’s decision back in 2000 to ratify, in IEC 61158, a fieldbus standard incorporating not one, but eight competing and incompatible protocols. Since then any promising moves toward rationalization, such as the decision of the major fieldbus organizations to cooperate in the development of a common Electronic Device Description Language (EDDL), have been followed almost immediately by a spectacular falling out, most recently over whether there was any benefit to be had from what Emerson Process Management President John Berra described as “this FDT nonsense.”
But then conventional fieldbus is not the only game in town. Even before the ink was dry on IEC 61158, it was becoming clear that many users were more interested in the potential of industrialized versions of the already ubiquitous Ethernet, and so it has proved. Moreover, while the conventional fieldbus power brokers have tried to extend their existing fiefdoms into Industrial Ethernet territory, we have not seen the repeat of the “fieldbus wars” that many had predicted. That’s due in part to the fact that it’s a whole lot more difficult to lock users into a particular flavor of what is already a universal standard and also, and possibly consequentially, because this time around users have made it clear that they simply won’t stand for it.]
So the announcement by Schneider Electric, the week before Hanover/Interkama that it is to become a “principal member” of the Open DeviceNet Vendor Association (ODVA) and that coincidentally ODVA is to extend its Common Industrial Protocol (CIP) network specifications to provide compatibility with Modbus/TCP is hugely significant and a triumph for user power.
Like so many such announcements, this one needs a bit of decoding. Schneider, through its ownership of the Modicon brand, is in effect custodian of the Modbus protocol, although the intellectual property and responsibility for its maintenance and development have been vested in the independent Modbus–IDA consortium since 2004.
Mirror Image
As such its position is pretty much a mirror image of that of Rockwell Automation, which developed the CIP-based DeviceNet and ControlNet and then passed them over to the independent Open DeviceNet Vendors Association (ODVA). Since then ODVA has, at one extreme, adapted CIP as the basis of its Industrial Ethernet implementation, Ethernet/IP, and at the other, to its recently released sensor–actuator bus and ASi rival, CompoNet. Just how independent of their respective parents are these two organizations is debatable, although the cynical answer would probably be, “At least as independent as Profibus International is from Siemens.”
Developed originally in the late 1970s, Modbus’ claim to be regarded as a fieldbus is tenuous in the extreme, but its very simplicity and almost universal acceptance has sustained its popularity.
Modbus IDA claims more than 7 million Modbus nodes in Europe and North America, and that popularity has in recent years extended to the Industrial Ethernet implementation. ARC’s most recent study of the market in 2005 showed Modbus/TCP and EtherNet/IP to be the most widely supported industrial Ethernet protocols.
Market Share
We asked ARC’s Harry Forbes whether that justified ODVA’s claim that the two protocols between them accounted for more than 50% of the market but he, perhaps understandably, wouldn’t be drawn, only saying that “We are working on that data for a new study to be published later this year … with node counts of all the IE flavors.”
Clearly the implication of the ODVA claim is that a combination of Ethernet/IP and Modbus/TCP would have more installed nodes than Profibus International’s (PI) ProfiNet. Back in 2004, PI’s Geoff Hodgkinson predicted that the number of ProfiNet nodes would exceed that of Profibus nodes by 2010. Given that PI is now predicting that Profibus will meet its target of 20 million nodes by 2008 with ease, we asked them what the current position was, only to get the response that they don’t know.
“We are working on the issue, but there are a number of questions to resolve, the most important being: What’s a node?” explained Carl Henning, director of ProfiNet marketing with the North American Profibus Trade Organization (PTO). “Should the count include switches? Do some technologies count each module because it has an IP address? Do others just count the overall controller? There is a real danger of trying to compare apples and oranges. We’ll have an answer to define and accurately count ProfiNet nodes probably early next year. And we’ll state our methodology (and what exactly we’re counting) then.”
ODVA will bring the Modbus community under its umbrella by integrating Modbus connectivity into the CIP architecture in a way that will require no changes to the existing Modbus slave devices. This will be achieved by extending the definition of Ethernet/IP “originators” to include the optional ability to communicate with Modbus/TCP slaves. The integration will also be backwards-compatible with the existing CIP standard, ensuring that both existing Modbus/TCP and Ethernet/IP devices will be covered. ODVA says that the next release of the EtherNet/IP specification, which will include Modbus support, will be available before the end of the year, while Schneider says that it expects to have products based on the new protocol available in 2008.
Critical Mass
The development has major significance at a number of levels. DeviceNet and its related networks have been the dominant force in factory automation in North America, but have had much less impact in the rest of the world, where Profibus can justifiably claim market leadership. However adding Modbus/TCP—and the Schneider user base—gives ODVA the critical mass and global coverage it has previously lacked and puts it on a comparable footing with ProfiNet.
There could also be a knock-on effect in the process automation market, given that, as a ‘Producer-Consumer’ protocol, CIP has more in common with Foundation fieldbus than with Profibus PA, the process automation implementation of Profibus.
As a result vendors and end users might be tempted to reassess their choice of network for ‘non-process’ applications in process industry environments, an area where Profibus and ProfiNet have traditionally been strong.
By no means the least significant potential consequence is the impact on the PLC market. As ARC’s Harry Forbes points out in an “Insight” document discussing Schneider’s strategy, ODVA’s principal members, which include Omron as well as Rockwell and Schneider, between them now account for 36% of the global PLC market, and that share is pretty evenly distributed across North America, Asia and Europe. If Schneider’s closer involvement in ODVA were to lead to closer cooperation between it and Rockwell on a broader front, perhaps giving the latter a broader platform from which to address European and Asian markets, then the combination could pose a significant challenge to Siemens’ current position as the global automation market leader.
Forbes is in no doubt about the significance of the development. “It is unusual to see several automation majors joining in such close collaboration, especially in a strategic area such as industrial Ethernet, and it adds to the value of ODVA and its CIP Network technologies in the automation industry. Automation users of Modbus/TCP can now look forward to benefiting from CIP Networks. Schneider Electric products will also benefit from the many capabilities of CIP, but end users will be the real winners here, because future CIP Networks will offer them a broader range of choices.”
Other Networks
Schneider says that its decision in no way diminishes its commitment to its other core networks, SERCOS and CANopen, but that it now sees Ethernet/IP as the foundation of its network strategy. “Our customers want the level of interoperability and seamless automation of factory floor equipment that only networks using standard, unmodified Ethernet can provide,” said senior vice president of innovation for automation business Adrien Scolé. “They also want a single network that they can use for control, information, configuration, safety, synchronization and motion. Ethernet/IP is the answer to meeting these needs, since it provides compatibility with existing Modbus/TCP products, as well as access to the complete suite of services provided by CIP. We believe that our strengthened relationship with ODVA will make Ethernet/IP the most widely used industrial network.”
That view was echoed by ODVA’s Katherine Voss, who described Schneider as “a leader in driving the adoption of standard, unmodified Ethernet technologies on the factory floor and throughout the enterprise. We look forward to leveraging the vast experience of Schneider Electric in automation, as well as its expertise with Ethernet and the Internet, to continue to expand the capabilities and benefits of ODVA technologies.”
Unmodified Ethernet
According to Forbes, that word “unmodified” is a key element in the Schneider strategy, which is aimed at reducing the “fragmentation of industrial Ethernet protocols, which they believe is throttling market growth,” he says. “They object to Ethernet automation systems that require custom protocol stacks (or in some cases ASICs) supplied by a controlled set of certified providers.”
Not everyone is entirely bowled over by the development, however. PTO’s Carl Henning, in his blog at http://us.profibus.com/community/blogs, isn’t impressed by the plan to encapsulate Modbus packets within CIP so they can be handled on the CIP network. “To me encapsulation is less than ideal,” he writes. “It introduces one more step in the process which adds to the response time. And encapsulating it in TCP/IP or UDP/IP adds to the uncertainty of the delivery time.” Henning quotes data from the University of Michigan which suggest that performance will be inferior to that of ProfiNet. More dismissively he adds that “The press release says products will be available in 2008. But there is no reason to wait; ProfiNet can communicate to Modbus today through a proxy … without encapsulation.”
One can’t help feeling that Henning is, perhaps deliberately, missing the point. Reducing the number of alternative Industrial Ethernet protocols must in long term be to the advantage of users even if in the shorter term it may not make choosing between them any easier. Now, isn’t it time Profibus started talking seriously to the Fieldbus Foundation?
Users Win Again as FDT and EDDL Bury Hatchet
Acrimony, name calling and general mutual abuse have characterized relations between the respective supporters of the rival FDT/DTM (Field Device Tool/Device Type Manager) and EDDL (Electronic Device Description Language) technologies for describing field devices in fieldbus systems over past three years. In 2004 the EDDL Cooperation Team (ECT), comprising the Fieldbus Foundation, the HART Communication Foundation and the Profibus Nutzerorganisation, with the OPC Foundation a later recruit, announced its enhancements to EDDL which, its advocates claimed, rendered FDT superfluous. Things got even worse later the same year when first Emerson and then, much more surprisingly, one of the original prime movers of the FDT initiative, Siemens, announced that they were not going to support FDT. That gave rise to a series of exchanges conducted mainly through the pages of publications such as INSIDER, which were reminiscent of the worst (or, let’s face it, for us journalists, the best) days of the Fieldbus wars.Users. Remember Them?
As ever, the last people to have their views taken into consideration were the users. They really did want vendor independence based on interoperable, interchangeable devices and didn’t just expect vendors to pay lip service to that concept. However, when they began to make those views known in the clearest possible way by the exercise of their check books, even the world’s largest automation companies had to take notice.
First signs of that came back last spring when it became clear that Emerson, despite earlier protestations to the contrary, was providing DTMs for selected Rosemount instruments Last November the FDT Group announced its intention of opening negotiations with ECT and, at ABB’s Automation World in Florida, we picked up strong hints of a possible “rapprochement” between the rival parties (INSIDER, April 2007) so, when it was announced that the FDT Group and the ECT would be jointly hosting an “Editor Panel” at last month’s Hanover Fair, and when Emerson’s own European PR consultants started sending out the invitations, it seemed likely that something was in the wind.
Mutual Capitulation
None of that, however, led us, or indeed many other people, to suspect what was actually announced, which was, in effect, mutual capitulation and the second triumph for common sense and user power in as many weeks. To the sound of swords being beaten into plough shares and hatchets being buried, standing knee deep in olive branches and through huge mouthfuls of humble pie, the representatives of the two organizations announced that they had reached agreement “to combine efforts and work toward a unified solution for device integration that is compatible with both technologies,” a decision which would, they acknowledged, “satisfy one of the most frequent customer requests.”
To that end, the FDT Group is to become the fifth member of ECT and is to work with representatives of the other organizations “to finalize a solution and achieve a common framework that meets the requirements of all parties.” A number of factors seem to have come together to bring about what is certainly, in automation industry terms and, to quote the press release, a “historic opportunity for cooperation.” FDT advocates have long argued that their technology complements rather than replaces EDDL, and Dick Caro, who as chairman of ISA’s SP50 fieldbus committee during the fieldbus wars, learned a thing or two about automation industry infighting, agrees. In an email recently quoted on Walt Boyes’ Sound Off! Blog, he wrote that “The most basic difference between them is that FDT/DTM allows the instrument supplier to format the HMI screen display for that instrument,” while “EDDL allows the HMI supplier (typically the DCS vendor) to format the screen display for all field instruments.”
Most end users he had contacted wanted the DCS supplier to control the look-and-feel of the HMI to ensure consistency for the operator, but some instrument suppliers believed that they couldn’t make some of their diagnostic and calibration displays available via EDDL. “There are many other technical and procedural differences that may be important in competitive situations, but my overall conclusion is that these are complementary technologies,” he wrote.
FDT+EDDL+OPCUA
With most FDT supporters taking that view, it was always going to be difficult for them to resist the notion of combining the two technologies if someone was able to show how that could be achieved without a loss of FDT functionality. Enter Professor Bender of the Institute for Technology in Munich (itm), who last November demonstrated how a combination of FDT, EDDL and the OPC Unified Architecture (UA) could provide a single common model. While there was understandable caution, it was recognized that this field device integration (FDI) model provided a way forward, if problems such as the provision of a migration path for existing DTMs could be overcome.
But then the FDT camp never denied the need for EDDL. Less easy to overcome, one suspects, were the prejudices of those in the EDDL camp who refused to recognize that there was any need for FDT at all. Here, we suspect is where Siemens Process Instrumentation & Analytics Division president Hans-Georg Kumpfmueller came in. He joined the Fieldbus Foundation board early last year and is also now the chairman of ECT. Last year he demonstrated a distinctly unSiemens-like flexibility on the subject of fieldbus by abandoning his company’s long standing policy of refusing to support Foundation fieldbus and entering into a technology sharing agreement with, of all people, Emerson. Under that agreement, Siemens gained access to Emerson’s Foundation fieldbus expertise in exchange for Emerson’s tapping into Siemens’ Profibus-related technology. After that, one might speculate, persuading Emerson Process Management president John Berra that it was time that Emerson accepted the inevitable on FDT would be comparative child’s play.
Unified Model
The final shape of the actual unified FDI model has yet to be determined, but it is clear that it will draw heavily on the itm proposals, using a subset of the OPC UA technology within a client-server architecture. One of the EDDL supporters’ key objections to FDT was its operating system dependence, while the FDT camp objected to the control over how information is displayed which EDDL conferred on the host system. As a result, the agreement specifies that the eventual solution should be operating system-, platform- and host-independent. Device vendors will have complete freedom to define the content of device pages to ensure that access is available to all the functionality of their devices. However, the look and feel will come from the host, although the device vendor will have the freedom to write applications for specific functionality.
FDI will also be compatible with existing EDDL and DTM based device descriptions, thereby preserving users’ existing investments, although it will be the responsibility of the separate ECT and FDT groups to develop migration strategies for their respective installed bases and to ensure backward compatibility with existing EDDs and DTMs.
The agreement also requires that the technology is applicable to any field device communication technology and to both hierarchical and heterogeneous network topologies, which effectively means all existing fieldbus technologies including, most importantly, HART, Profibus, Foundation fieldbus and the ODVA’s CIP-based networks. The aim is to develop an open specification which will, in the fullness of time become an international standard. The current time scale calls for draft specifications and prototypes to be in place no later than the end of 2008.
Major Step Forward
Kumpfmueller himself described the agreement as “a major step forward for device integration in several areas. It eliminates double efforts for customers and vendors, and preserves backward-compatibility and operating system independence … Our agreement is more than a compromise; it is the natural technical evolution based on the most up-to-date, open and flexible technologies.”
FDT group managing director Flavio Tolfo was equally enthusiastic. “This new cooperation follows our targets of openness and freedom of choice for the benefit of end users and is strongly supported by our members. After much discussion, we reached commitment to work together and protect the investment of each technology for the benefit of end users.”
So who has won? Well, this is certainly not another IEC 61158 and it’s difficult to avoid the conclusion that the EDDL camp has got pretty much everything it could possibly hope for. FDT becomes a member of ECT, rather than the other way round, and the eventual solution will maintain operating system independence, while look and feel will be largely determined by the host rather than the device supplier. So while Emerson and Siemens have had to concede that FDT may have some role to play, the 59 members of the FDT group are having to dance to a strongly EDDL-harmonized tune.
Saving Face?
That is perhaps why, in its own announcement, the FDT Group goes out of its way to say that “It must be emphasized that the existing technology development programs in the FDT Group are not affected at all. We have set up separate joint technical and marketing teams to manage this common project. Furthermore, all ECT member organizations, FDT Group, FF, HCF, OPCF, and PNO remain separate organizations, each with their own missions, objectives, membership, and organization structures.” Again, it’s hard to see how long that would survive acceptance of an eventual unified FDI.
Given the proven ability of the automation industry to snatch failure from the jaws of success, it’s still a long road from here to an eventual FDI standard. We suspect that Hans-Georg Kumpfmueller is going to need all of his proven diplomatic skills if the embryonic FDI is make it to full term.
SIS Health Monitoring Could Save $1M Annually
Honeywell’s latest contribution to the Safety Instrumented Systems (SIS) debate is the introduction of a set of technologies and services designed to help users monitor the health and reliability of their SISs. It quotes certain unspecified studies showing that companies can save up to $100,000 or even $1millon per year though correct engineering and maintenance of SISs and their associated Safety Instrumented Functions (SIFs).
Honeywell SIS-Health Monitoring was codeveloped with industry professionals in the maintenance, instrumentation and test engineering fields and is designed to reduce unnecessary maintenance and engineering and minimize failures that can lead to safety incidents and unexpected plant downtime. It’s also claimed to enable better work practices, which can lead to savings of between 20% and 30% on installation and operating costs. “Experience has shown that a poorly maintained SIS can be costly for any plant in any industry,” explained Systems marketing manager Jason Urso. “SIS-Health Monitoring helps facility managers keep tabs on their safety systems, which makes for more efficient and effective maintenance, increased process availability and decreased production losses.”
If it Ain’t Broke . . .
Honeywell’s aim is to address the 20% or more of plant incidents that it believes are caused by SIS maintenance and testing errors. Problems identified include too-frequent maintenance and testing of SISs because system status cannot be accurately monitored. Such unnecessary maintenance can, it argues, increase the possibility of human error and consequent failure, while lack of reliability data can result in unnecessary engineering of SIS which can again result in system failure.
SIS-Health Monitoring can be customized to meet specific plant requirements, conditions and process demands. It currently comprises two modules that can be operated as stand-alones or as an integrated system and applied to any type or brand of safety instrumentation. The SISHealth Monitoring Local Reliability Database stores all inventory information regarding a site’s safety instrumentation and, based on its failure behavior, helps determine reliability and safety performance characteristics, such as trends, demand rates and time-dependent failure rates. Meanwhile the SIS-Health Monitoring Analysis Tool enables operators to analyze, validate and optimize the SIF reliability and Safety Integrity Level (SIL).
“Many existing tools … are not capable of automatically monitoring the actual performance of an SIS,” claims Urso. “Honeywell’s SIS-Health Monitoring solution addresses that weakness by collecting necessary, meaningful data and giving engineers the tools they need to act on it.”
About the Author |
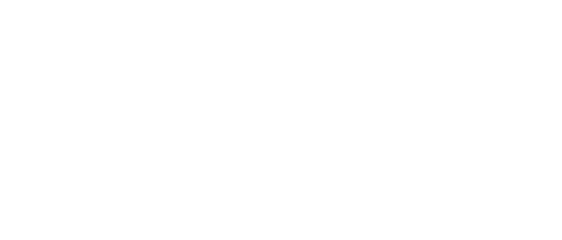
Leaders relevant to this article: