Download this article as a PDF
MORE THAN 30 years ago, the Dow Chemical Co. embarked on what ultimately evolved into a global corporate initiative: to develop and broadly leverage a standardized, highly integrated process automation system, incorporating basic process control, process information and safety-system functionality. Based on what we wanted to accomplish, and a lack of commercial offerings at that time, we developed several proprietary solutions, including a process control system that came to be known as MOD, which is short for “Manufacturing Operating Discipline.”
FOUNDED IN 1897 by Herbert H. Dow in Midland, Mich., the Dow Chemical Co. is a global leader in science and technology, providing innovative chemical, plastic and agricultural products and services to customers in 175 countries. From the very beginning, continuous improvement has been at the heart of the company, and forms the essence of its mission: “To constantly improve what is essential to human progress by mastering science and technology.” To achieve this, we’re committed to the principles of sustainable development. While it might sound lofty in some circles, this underlying philosophy has been an instrumental driver in our process control journey from the beginning.
The roots of our process automation philosophy go back to the 1960s, and are based on our operational strategy. Consistency and sustainability are key elements of that strategy. As a global company, it’s important to operate facilities in the same way, every time, to achieve consistently high quality, as well as process reliability and repeatability of best practices. We were striving for true “operational excellence” many years before it was coined by industry analysts.
Operational excellence includes safety performance, which was and is a key focus for Dow. We’re passionate about it. Protecting people, the community and the environment are non-negotiable priorities in our corporate culture. We must operate our plants safely and in the same way every time. Our "Vision of Zero" translates to zero incidents, injuries, illnesses, accidents and zero environmental harm. So our safety practices need to be repeatable and re-deployable as well.
We’re also driven to develop our own solutions by our engineering culture. We’re encouraged to look at problems and solutions differently. We ultimately integrate design, control and safety as a standardized system because we need solutions that improve the process. We design the solution around the process, not the process around the solution. Which element drives the development process is an important distinction here. You size the shoe to fit the foot. You don’t change the size of the foot to fit into the shoe. So, the needs of the process and our ingrained operating discipline are what ultimately create the solution. Our Manufacturing Operating Discipline (MOD) series process automation system was designed not by automation engineers, but by chemical engineers, who were intimately familiar with the intricacies of the process.
With enough iidot lights and pushbuttons to satisfy any primate, Dow's first attempts to automate were complex and wonderful.
This was the challenge, and we absolutely needed to accomplish all of it. However, in the beginning, commercially available process automation systems didn’t give us the capability that we needed. Technology was available that could be applied to the problem, and we developed several solutions based on general purpose computers and operating systems. Over time, we were able to develop a system that met our needs. In fact, Dow was the first company to certify a process control system with logical separation of the safety and automation functions in a common hardware platform. However, we didn’t exactly plan it that way. The driving force behind this was our passion for process safety, our operating discipline and the need to simplify the automation platform. We weren’t looking to invent something revolutionary. A confluence of process automation deficiencies in the market and the right people with the skills, needs and management support set the stage for Dow’s proprietary automation system.
In the late 1960s, all the plants we were familiar with operated with individual loop instrumentation, or even manually in older plants. Early efforts at automation were frustrating and cumbersome due to hardware incompatibilities and complexities. More time was spent dealing with keeping the control system running than was spent improving plant operations. This had to change. What was needed was a standardized, re-deployable process automation solution that supported our goals of overall consistency, productivity improvements, global operating discipline and innovation, all while maintaining high safety performance. The common thread throughout was our passion for process safety and this operating discipline.
Levi Leathers’ Operating Discipline Vision
One of the greatest influences on MOD’s early development was Joel Franklin Monroe (Levi) Leathers, a research and development pioneer, who became Dow’s executive VP. Levi was a larger-than-life individual, who had a tremendously positive impact on those around him, both personally and professionally. You may be fortunate enough to encounter someone like him once in your life.
In the early 1960s, Levi was R&D director and later general manager at Dow’s Texas Division. Under his direction, new processes and vast improvements to existing processes came into being. His words ring as true today as they did then: “If it doesn’t work, there is a reason why. If it does work, there is a way to make it better.” He embodied Dow’s passion for safety and operating discipline, and planted the technological seeds that brought them together. He didn’t know all that had to be done to achieve this goal, but he knew how to get people excited about the idea. The term he used to express his concept was “Operating Discipline.”
Levi shared his vision by traveling around the company to Texas, Midland, Sarnia, Canada and many other Dow sites worldwide. He didn’t just talk to control engineers, but to people at all levels, including process and instrument engineers, manufacturing, plant or line people, business leaders and senior management. Levi wasn’t the actual technology inventor, but his influence is easily seen in the early development efforts that began during this decade.
Converging Activities
Over the years, there were technology development activities throughout Dow, each addressing a different aspect of the overall automation opportunity. These activities ranged from creating process information systems to the developing closed-loop control applications. Ultimately, they all converged to one set of systems, but this took several years. Information sharing between engineering teams at multiple sites wasn’t what it is today. Travel between sites was limited, and the technology that facilitates information exchange between sites and work teams that we now take for granted today wasn’t a reality back then.
MOD 1 is Born
One major activity began about 1968 in the Midland Analog Simulation Facility, which was seeking better production process control. By performing differential equations on analog computers, researchers found they could simulate any conceivable control strategy. As a result, analog simulation was widely used to perform studies that would determine the best control strategy for controlling a unit operation or an entire plant.
However, the development of analog simulation also led to some frustrating times. Existing hardware, such as panel-mounted conventional controllers, often became a barrier to implementing the best process control methods. Compromises also had to be made to fit existing hardware.
Despite these constraints, some process control ideas were implemented on industrial analog computers built to withstand hostile environments in the field. However, while they had the flexibility to implement control ideas without hardware barriers, analog computers were costly and very limited in capacity. The logical question was: how to implement the technology of a large analog computer in the field at a much lower cost to the company?
The answer was MOD 1. Started in 1969 on a batch distillation column, MOD 1 resembled an analog computer, and had similar logic and computing components. It had approximately one-quarter of the power of the present MOD 5 computer, but it was the foundation for sequencing, alarms, flexible analog and digital control—the basic ideas for automating a chemical process. Built by Taylor Instrument Co., which is now part of ABB, the first MOD 1 cost $85,000.
The MOD Operator Station provides a standard graphical interface to the process control system as well as an integrated environment for development.
This Operating Discipline philosophy was implemented using the “sequencer” concept. The importance and value of subdividing the entire plant into unit operations (sequences), and then subdividing the time up into steps for each sequence boggles the mind. Plant people could now think about, document, and automate all of the actions required to operate a plant, including start-up and shut-down. The control system would then provide relentless enforcement of the best way to run the processes.
These ideas often met with opposition because they were viewed as impractical or unachievable. The trench-by-trench effort to get the plants to accept and use this level of automation was fought for many years, and is still being fought in some instances. However, the favorable economic impact of the successful implementations were felt throughout our company.
MOD 2 Moves to Mode Modular
By 1970, MOD 2 was created to reduce costs, and move from a standalone to a mode-modular system. It was the first process control system with a standard system packaging method. MOD 2 also used digital modules from Digital Equipment Corp. and hardwired logic cards. However, MOD 2’s analog function modules were designed internally.
MOD 3 Increases Control Capability
Coming into general use in 1972, MOD 3 was developed to increase system control capability and reduce overall cost. Some rewiring was required to change the control logic. Installation of a MOD 3 in a Latex plant in Sarnia, Ontario, was the first use of MOD’s concepts outside the Michigan division.
MOD 3 used the first all-digital CPU, which was called the Alpha 16 or the Naked-Mini. This CPU was made by Computer Automation Inc., and had 4 KB to 32 KB of memory. MOD 3 also was the first process control system to use DOWTRAN, a computer language for end-user programming.
MOD 4 Goes Global
MOD 4 followed in 1975. It was the first process control system to perform all temperature and flow calculations in its software. MOD 4 expanded the I/O capability of previous MODs, and displayed values in engineering units, instead of percentage of full scale operation. MOD 4’s LSI-2 CPU expanded memory to 80 KB, and was again built by Computer Automation. Mod 4 finally made it possible to backup all inputs and outputs. Installation of a MOD 4 in the Methocel plant in Stade, Germany, was the first use of MOD systems outside of North America.
MOD 5 Brings the Best Together
Dow began using MOD 5 in 1980. Most of the first process control concepts remained in the MOD 5, but were greatly enhanced by the accumulated knowledge from implementing the system worldwide. MOD 5 represents hundreds of person-years of experience for automating and controlling processes accumulated over a mere 16 calendar years.
MOD 5 also represents the true collaboration of Dow’s multi-discipline work teams (chemical engineers, process automation, instrumentation, etc.). The MOD series development was a pivotal endeavor that linked our technology center philosophies with our operating discipline. We understand better that cooperation between research (get the right process), engineering (use the right equipment), maintenance (fix it once, never again), production (optimized and safe operations), business (automated scheduling, shipping, etc.) and many other groups must occur and improve for our company to survive and excel.
We really started to see tangible, operational benefits with MOD 5, including repeatability, as well as consistency and productivity improvements. Repeatability of best practices was extremely important because it enabled us to operate our plants safely, day in and day out, no matter what else we were doing. It helps us to do it the same way, every time.
Consequently, in the mid-1980s, Dow decided to implement MOD 5 globally. The standard systems approach used here was extremely powerful because it means anyone familiar with a MOD 5 system can immediately relate to the MOD 5 hardware and software running a process anywhere in the world. As of 2000, we had 1,500 systems installed and more than 400 information systems in place.
In the 1990s, there were several enhancements to MOD 5. A control computer was provided that physically combined control and safety functions in the same hardware platform. However, these functions were logically separated. This version of the system was SIL 3 certified. Dow was the first company to certify a process automation system with logical separation of the control and safety functions.
There were also major projects to address the human interface to the control system and the information management functions. The MOD Operator Station provides a standard graphical interface to the process control system, as well as an integrated environment for control programming development. A single standard information system and process historian was created by combining technology from several products developed previously.
Significant Results
By combining our best technology, we’ve seen tremendous productivity benefits added to fulfilling our operating discipline and safety performance goals. We reduced control strategy development time by 45%, and reduced support costs by 50%. Process startups are automated and coordinated across multiple unit operations. Alarms are “intelligent” in the sense that they reflect the state of the process, rather than just a deviation from a limit. Batch processes are fully automated, resulting in reduced cycle times.
Embedding our operating discipline concept in the automation system also helped us achieve our environmental, health and safety (EH&S) goals. All these performance improvements contribute hundreds of millions of dollars to our businesses.
Looking Ahead: New Sustainability Options
Of course, all strategies must adapt. So, the time came when we realized it wouldn’t be cost-effective to continue to invest in proprietary hardware and software systems. In early 2000, we decided change was necessary. While we wanted to preserve our process automation expertise, we knew that we didn’t want to be hardware providers, and so we began to look at other options.
The next article in this series will describe our quest to find a sustainable process automation solution that could take us into the future. MOD 5 would be a very tough act to follow.
About the Authors |
Margaret R. Walker is vice president of engineering solutions for Dow Chemical's Technology Centers and Manufacturing and Engineering Work Process; Jerry N. Gipson is director of Dow’s Engineering Solutions Technology Center; Edward R. Sederlund is Dow’s Process Automation product manager; and Eric C. Cosman is Dow’s Engineering Solutions architect. The authors would like to thank Peter J. Kindt, Dow’s Process Control and Advanced Control discipline leader, who also contributed to this article.
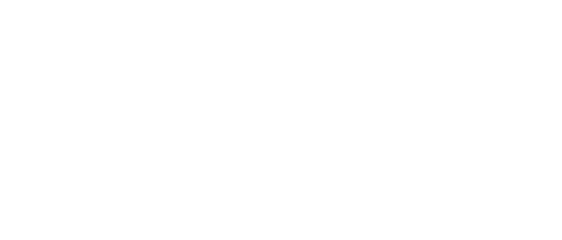
Leaders relevant to this article: