THE LEVEL of discontent between end users and skid builders has become quite disturbing. Some end users think skid builders are arrogant, don’t follow specs, don’t understand their problems, and don’t meet their standards. Meanwhile, skid builders think many users are unrealistically demanding, don’t precisely define their needs, and are too reliant on third-party contractors. It all seems to come down to a failure to communicate. Fortunately, there are some common-sense remedies to these conflicts.
So, what is a “skid” exactly? In general, a skid is a self-contained system shipped to a process plant on an integral platform. It contains instrumentation, controls, reactor vessels, valves, pumps, piping and all the necessary equipment to perform a specific task, such as waste remediation, pH neutralization, mixing, pumping, metering, compressor control, etc. Skid builders tend to be specialists in certain areas. They also run the gamut from extremely cooperative to very difficult to get along with.
Winter of Discontent
Ian Drazin, electrical and instrumentation supervisor at Potlach Corp., a supplier of potash fertilizers in North Las Vegas, Nev., is very upset with the quality of skid-built equipment. “My company recently purchased seven chemical skids and they have been nothing but a major problem,” he reports. “Problems include motor failures and pulsing positive displacement pump flows being measured by incorrectly specified flow transmitters. Where was the engineering? Did they ever field test their design?”
Drazin also is unhappy that the equipment wasn’t built to spec. “None of our corporate electrical standards were followed,” he adds.
So why buy skid-mounted equipment in the first place? “I have the expertise in my department to build any system I wish,” he says. “The problem is limited man-hours. We simply have too many other items on our plate that will directly affect machine run-time if we don’t work on them first. There isn’t enough time left over to devote to building our own skid system. Therefore, we turn to third-party suppliers.”
Gary D. Jacobson, P.E., a project manager at Boston-based CH2M Hill, says, “My latest problem is from two different vendors for automatic pH neutralization and polymer mixing and injection. Though the systems generally do the job for which they were purchased, the equipment supplied doesn’t meet the desired configuration and standards. Our clients sometimes want the system to conform to their standard for PLCs or operator interfaces, and the vendors either refuse or don’t provide what they have accepted an order for. Skid vendors have completely ignored comments to submitted drawings and documentation, or have agreed to incorporate comments, but then didn’t do so.”
Some other end users would only comment anonymously. One reported, “I wouldn’t want to leave the impression that we are unable to manage the vendors. Although, in this case, I guess we can’t apparently, but neither can anyone else.”
FIGURE 1: PILOT SKID
This entire computer-controlled skid mounted pilot plant for polymer research arrives on a skid from Unitel Technologies.
Richard Neff, president of skid builder Irrigation Craft, in Ft. Lauderdale, Fla., also agrees. “Skid builders often are incapable of building custom systems,” he says. “They lack the knowledge and engineering skills to correctly understand the specifications and intelligently communicate with the specifying engineers. They bid a low price, and then they resent having to provide what the specifications require.”
Jacobson summed up his discontent this way: “I’m looking forward to the skid manufacturer on my last project coming forward to propose on my next project, at which time I will do my job as the owner’s engineer and disqualify them from consideration.”
A Failure to Communicate
Warren Searles, president of HydroTec Systems, a skid builder of waste and water treatment systems in Rockton, Ill, says problems often originate with the end user/owner, and a lack of communication from the owner to its vendors. “We provided a system involving several large pressure vessels, each fitted with a control harness of valves and sensors,” he explains. “The control is held together with an Allen Bradley controller and network.” The entire system wasn’t coordinated as an entity, but was put together on site. The results are not pretty. “Once installed and started, the system functions, but not as desired by the owners, the operating management, and the operators,” adds Searles.
How’s that again? “The system does meet the specification as written and enforced by the owners, therefore the project was signed off by the owner,” he explains. However, problems persist. The operator interfaces were designed for engineers, not for operators, so the interfaces’ operator functions aren’t simple to understand. Also, engineering management is the first responder if problems occur, but if engineering management isn’t available, then the system must be shut off.
Searles calls this project a “disjointed agglomeration,” and wishes he’d been allowed to build the system on a skid at his own shop, instead of being required to assemble it on site. “The creation of the confusion is traceable to the owners,” he says.
However, miscommunication also happens with people who are supposedly competent as communicators. For example, one would assume that engineering and procurement contractors (EPCs) would understand specifications, and communicate them to the skid builders, but this is not necessarily so. One refinery control engineer, “Bob,” who requested anonymity, explains, “The source of our problems often comes from engineering contractors we hire to manage projects, and be our primary reps to third parties. When these contractors don’t insist that the skid builder meet our specs and standards, we’re going to have issues.”
Contractors, EPCs Can Help
Michael Frey, sales engineer for Daniel Measurement & Control, a Houston-based subsidiary of Emerson Process Management, says his firm relies on engineering contractors to be their liaison with the end user. “As a metering system package supplier, Daniel interfaces with the EPCs for basic design requirements,” he explains. “These requirements are based on the application of the metering system, destination of system, fluid measured, technology applied, industry standards, etc. It is actually the EPC’s responsibility to integrate the different skids to each other. As a skid supplier, it’s necessary for us to strictly adhere to specifications provided by EPC and end user. There’s no room in our scope of supply for a ‘one size fits all’ and ‘take it or leave it’ stance.”
Mobile Process Technology's ChromaSep separation process module for sulfuric acid and copper sulfate is controlled by any PLC the user chooses.
Usually, the typical skid isn’t meant to operate as a standalone module. It’s often part of a larger integrated system, which means that upstream and/or downstream interfaces have to be carefully designed. “If these interfaces don’t match, a field retrofit can be a very expensive and time-consuming affair,” adds Unitel’s Randhava.
Working Around Skid Builders
Some end users have novel ways of dealing with non-cooperation from skid builders. Eric Marcelo, a control engineer in the coffee department of Nestle Phils, Cagayan de Oro, in the Phillipines, says it just takes a little extra effort. “For the most part, I haven't had a problem with obnoxious skid builders. Most of the skids are designed by our company, and skid builders just build them to spec. These guys are the ones we've done business with for a long time, so they know how we work. This usually means they use the same PLCs we use, so communication is just a matter of laying out a cable and connecting it to the network.”
Even so, communication problems still come up. “One manufacturer neglected to tell us they could build us a skid with the same type of PLC we usually use,” adds Marcello. “So these skids became standalone, when they easily could have been tied in with our system.”
Being a big company also seems to help. “Our company has enough clout that we could threaten to blacklist a supplier that doesn't perform to our standards,” he notes. “This usually keeps them in line. However, close coordination is still the best way to ensure that everybody does what is expected of them.”
End User Needs
End user are not trying to be obnoxious, unreasonable or demanding. They have real concerns about integrating skid systems into their plants. “Skid builders should be receptive to end user stated standards and preferences, and recognize that these are desired for good reasons,” says Jacobson.
Unitel’s Randhava says, “Usually, three types of interfaces have to be taken into consideration. These include fluids, such as gases, liquids and solids; electrical; and computers and data. The correct specification of the wiring in the skid should always be of critical importance, especially if the end product will be shipped overseas. Electrical codes and explosion-proof requirements can vary significantly by country. Strange as it may seem, even within the same country, regional and local regulations can sometimes supersede national standards. In any event, rewiring in the field is always a nightmare.”
Go Face to Face
How can users get skid builders to follow their electrical standards and good practices? More face-to-face discussions can help. Jacobson offers these suggestions for end users:
- Insist on a face-to-face, pre-design meeting, and/or a face-to-face meeting to review comments to submittals.
- Recognize that customization is costly and expect to pay not the lowest price, but the price that enables the skid builder to deliver the desired level of customization.
- Keep general contractors from preventing the owner's desires or the manufacturer's needs, questions and costs from being communicated to skid builders.
- Withhold payment until the system meets the specification, and write specifications that hold a percentage of payment until completion that will ensure compliance.
Drazin agrees with holding face-to-face meetings and withholding payment. “The only way to hold skid builders accountable is to have discrepancies in standards affect their bottom line,” he says. “Incorporate a contractual penalty fee for not meeting specification into every contract and then hold skid builders accountable to that contract.”
Conforming to Open Standards
Control equipment vendors have a simple solution for end users and skid builders “Use our open-architecture equipment,” they say, “and you can integrate everything easily.” Though self-serving, there is a certain amount of truth in this suggestion because fieldbus architectures are readily available these days. HART is built into just about every field instrumentation device on the market, making it easy for a skid builder to obtain diagnostic and calibration information. Though a bit more expensive, it is also possible to offer Foundation Fieldbus, Profibus and DeviceNet instruments and controls. By having a fieldbus network built into the skid equipment, integration becomes much easier. The plant’s DCS could easily control fieldbus-based devices through a simple interface.
Finally, connecting the skid’s controls to the plant network is much easier if the skid’s PLC or PC-based controller is based on an open architecture. Virtually all the controllers available from major manufacturers offer some kind of universal connection to DCSs. Also, because most open architecture PC-based controllers use Windows, it is a simple matter to create a universal database/historian that can be accessed by a DCS over an Ethernet connection.
It would be beneficial to skid builders if they could advertise the fact that their systems are easy to integrate. Skid builders could change their image overnight from that of arrogant suppliers to helpful suppliers. Besides, by working with end users, they might discover a new niche in the market and increase their sales.
Basic End User Issues
HERE ARE some the fundamental tasks skid builder need to address to collaborate successfully with end users.
Maintenance: If the skid or package is going to be maintained by plant technicians, then end users usually prefer that equipment, such as instrumentation and controls, be similar to what is already being used in the plant. This minimizes training costs and keeps spare parts inventories low.
Best Practices: Some users have developed installation and wiring standards based on long experience in their particular application or industry. They know what works and what causes problems. Therefore, they want skid builders to conform to these practices.
Regulatory: Some plants must conform to rules and regulations from the FDA, EPA, OSHA and similar agencies. They want skid systems to conform to these rules, too. “Within our customer base we see an increasing demand for integration of skid-based systems, such as clean-in-place (CIP) and batch systems that are controlled by the DCS,” says Todd Stauffer, PCS 7 marketing manager at Siemens Energy & Automation. “We have one large customer in the brewing industry that insists on tightly integrating its CIP system into the main process control system. They report that this helps minimize the chance that a CIP cycle is missed, helps create consistent reporting, and eliminates the need for specialized training on the CIP system.”
Integration: While some users treat skid systems as appliances, that is, a universal device that plugs in and does its job all by itself, many users want to integrate the skid system into an overall plant control scheme. If the skid is a closed system, then integration becomes much more difficult. “Today, it is no longer acceptable for a skid-based system to be designed and implemented without thought about the equipment with which it will be integrated,” says Stauffer. “Users are tired of the struggle and extra cost that is typically required to integrate a skid-based system into the host or supervisory control system. Ten years ago, the DCS community was happy to have a Foreign Device Interface available for connectivity. Now, they expect much more. Our market analysis has shown that ‘Ease of Integration’ is one of the top three buyer criteria for selection of a new process automation system.”
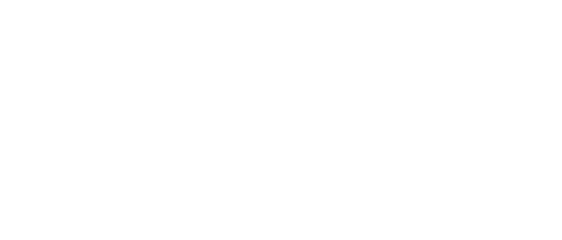
Leaders relevant to this article: