F |
rom the water wheel to the DCS and beyond, throughout history processors adept at identifying emerging technologies and then applying its potential affectively have continued to possess a competitive edge in the marketplace.
Whether to gain energy efficiency to lower costs or to develop precise command over a batch process for higher product quality, the wheels of commerce demand you adapt new technologies to do things better. But which technologies have the most potential?
We at Control would like to think we can help you decide and that's why we publish this article. But its not just our opinions that we publish. As with all of our feature articles, first we turn to our readers, process control users and independent systems integrators for input. Next we ask research organizations and suppliers for opinions. Then its our turn to sift through all the data, facts and conjecture we receive and try to make some sense of it.
Of course, some suppliers suggest that the next trend will coincide perfectly with their latest product release. Not to worry, such "trends" never make the list. We need to see that multiple vendors identify a trend before we recognize it as such. Then we do our own independent research.
One question that often arises is: Do we discern new trends each year, or do we recycle the prior-years trends? The answer is, a little bit of both. Tables throughout the article present technology trends CONTROLs editors identified in 2001, 2002 and 2003, as well as in this issue. As the table shows, some trends have legs and gain strength, while others fade, unable to hold up in the real world.
With that in mind, weve identified eight technology trends that are sure to impact the process industry control automation and instrumentation marketplace in the coming years.
TRENDS 2004 1. Asset management 2. The ultimate in closed-loop control 3. Real-time performance management 4. Smartphones conquer mobile computing 5. Software defines the system 6. Wireless again 7. IT requirements drive process control 8. Industrial biotech arrives TRENDS 2003 1. Industrial Ehernet marches on 2. Wireless 3. XML and web services provide data access 4. Frameworks offer super structure 5. Field-based control 6. Comprehensive condition monitoring 7. Engineering and finance converge to define optimization 8. Engineer's changing roles |
Asset management uses software-based monitoring systems to improve the uptime, performance, and operation of plants assets. Asset management can allow a controls company to run its customers plant remotely through imaging and monitoring systems that monitor assets (equipment, processes, people, software, and systems, etc.) from the top floor to the shop floor.Richard McCormick, a process control engineer with Ultramar Limited in St-Romuald, Qubec, sees asset management as especially useful. To keep data flow to a minimum, he suggests that "reporting by exception" be the accepted protocol. McCormick adds, "Asset management provides first-pass diagnostics based on reported symptoms. Then it directs us toward the causes so we know where to drill down and so that maintenance can to plan ahead for repairs." Terry Krouth, Emerson Process Managements (www.emersonprocess.com) vice president of PlantWeb technology, believes asset management, which is now only getting started, will grow in sophistication. "In the drive for improved availability and return on capital, asset management systems will continue to grow. Even though this technology has already delivered major benefits, it is still in its infancy. Users are beginning to understand and enjoy asset management benefits, including faster commissioning of plants and more efficient maintenance of assets," says Krouth."Growth will come with increasing integration of all plant assets into plant-wide automation systems and management systems. The holistic view of all the assets, presented in a form to help achieve and sustain operational excellence, will continue to drive further integration of machinery health management, real time optimization, and equipment performance monitoring," adds Krouth. Integration is key to asset management, and because integrated software is easy to use, its more likely to be used. Further, integration of expanded asset information on plant and enterprise HMIs is an empowering part of this trend.The Ultimate in Closed-Loop Control
Process control professionals have been performing closed-loop control for decades, but are they using the correct measured variable? Shuzo Kaihori, the president and CEO of Yokogawa Corporation of America (www.us.yokogawa.com), doesnt think so."The most important measured variable in any process is end user satisfaction. All other intermediate measured parameters such as pressure, temperature, and flow are simply steps towards ensuring that the ultimate customer is satisfied," observes Kaihori.
"Some suppliers suggest that the next trend will coincide perfectly with their latest product release." |
TRENDS 2002 1. The process control engineer's changing role 2. All-in-one architecture 3. Software licensing fees increase for large systems and decrease for small 4. Information centralization (data centers accessed via ASPs) 5. PC-based control & HMIs 6. Ethernet invasion 7. Wirelss TRENDS 2001 1. Web servers everywhere 2. Remote access via browsers 3. Path-to-profitability (P2P) replaces B2B 4. Ethernet everywhere 5. Wireless 6. PC-based control and HMIs 7. Rent software via ASPs 8. Smart instruments 9. Open systems 10. Plant floor/ERP integration |
If it moves and if it computes, smart cell phones can do it now or will do it soon. The cell phone markets economies of scale are so dominating that smartphones will simply bulldoze all competitors in their path to become the portable computing device of choice for billions of users worldwide.Mobile phone sales to consumers topped 510 million units in 2003 and will exceed 560 million units in 2004, according to the big three research groups that track mobile phones, the world's biggest consumer electronics market: Gartner Dataquest (www.gartner.com), IDC (www.idc.com), and Strategy Analytics (www.strategyanalytics.com).Smartphones, which feature calendars, email, pictures, music and other services in one device, were one of the fastest growing new categories. Worldwide shipments for 2003 rose 182% to 9.6 million devices.A great example of a technology likely to soon be displaced by smartphones are MP3 players like Apples iPod. Users download songs to the device and listen to the stored MP3 music files via headphones. Although just introduced, the writing is already on the wall for the technology.Why? Think about itusers are already downloading similarly formatted ringtones to cell phones at a startling rate. According to research group ARC, ringtone sales were $3.5 billion worldwide last year, up by 40% from 2002. Sales of ringtones, costing up to $4 each, have now overtaken those of CD singles. By contrast, Apple's iTunes generates annual worldwide sales of less than $100 million.With production rates in the hundreds of millions per year, it is inevitable that "smarter" phones will offer users increased memory storage and sound quality, enough to make carrying a single-use device like an Mp3 player redundant and unnecessary. The scenario will repeat itself for inexpensive digital cameras, and also for virtually any mobile computing application.Overwhelming economies of scale in the cell phone market mean that it will soon be feasible to equip all plant personnel with a smartphone priced under $100. These devices will deliver a host of integrated features including global positioning, RFID tags, video recording, digital displays, web browsers, e-mail, biometric user authentication, and corporate Virtual Private Network (VPN) connectivity. At that point, SCADA applications will be limited only by the imagination of end users. Remote cell phone access via SCADA screens, photos, and other information accessed via the corporate network will help technicians pinpoint problems. Remote access to control systems via a VPN will then allow long-distance troubleshooting from virtually anywhere in the world.COTS For All, So Software Defines the System
For several years major OS vendors fought the "Open" wars. The UNIX vendors couldnt agree on open systems, and PC OS vendors complicated the picture when networking took the PC away from its stand-alone model. Because there wasnt any one networking standard, systems integrators had a difficult time establishing even basic communications.
"Asset management provides first-pass diagnostics based on reported symptoms." |
"North America is the undisputed world leader in agriculture and in biotech. Which could provide thousands of jobs for process control professionals." |
As the table reveals, wireless has made our technology trend list for the past three years. It makes the list again this year as growth rates continue at a blistering pace. According to VDC, wireless Ethernet infrastructure networking components will experience a growth rate of nearly 35% over the next three years. Shipments of wireless Ethernet infrastructure access point/networking components for use in industrial facilities are forecast to increase from $62 million in 2003 to $152 million in 2006.Another VDC report shows that portable wireless operator interface terminal shipments are expected to grow to over $80 million by year-end 2005, a compound annual growth rate of 53.3%. These types of growth rates clearly mark a trend, and process control industry players agree.
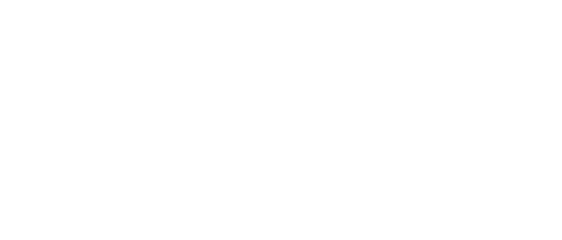
Leaders relevant to this article: