Greg: We got some insightful replies to the September column from Ed Bullerdiek, Chad Harper and Grant Wilson on the relative merits of PID versus MPC control of spouses and children.
Chad: Is PID or model-predictive control of your spouse better? Answer: PID. MPC or statistical process control would require the spouses behavior to be repeatable. Plus, if someone told me I could control my spouse with three tuning parameters, Im sold.
Ed: Based on my 23 years of observation (and yes, occasional response testing) the spouse system cannot be controlled. The system lacks sufficient instrumentation, has variable dead time and gainincluding reverse gainsand does not exhibit any statistical trends.
Grant: Approaching parenthood, I used to think in terms of integral-only control, highly detunednot interested in control, merely survival. Now that Im in sight (no pun intended) of the finish line (my boys are 15 and 19), my kids are so perfect, theres no dynamic behavior to model. Ive got to figure out what I (oops, we) did and write a book.
Stan: We didnt get any replies from children or spouses. This is probably because they are not reading this column in their spare time. We hope they dont pick up on this topic in the blogosphere, so we can maintain our technical advantage.
Greg: Communication is what most of us engineers know little about. It could be that we are the strong silent type, or we are too busy analyzing, but more likely we just do not have much practice speaking. In our defense, there may be more content in quiet than in noise. People who verbalize all their thoughts are distracting and tiring. The signal-to-noise ratio is poor. When normally quiet people finally say something, it usually contains content worth hearing. However, my experience is we tend to err on the side of saying nothing. Unfortunately, minimal communication leaves a lot unsaid and, therefore, to the imaginationa risky business when clarity is important.
We could talk about how important this is for our society and, even more important, our marriages, but lets stick to something we are more interested in as automation engineers, particularly since we have little or no control over politicians and spouses. Lets talk about communication intervals, control execution intervals, analyzer cycle times and input scan times.
Stan: We tend to think faster is better, but this is not always the case. This is something we have learned to appreciate in retirement, but it also is a consideration in process control.
Greg: For example, a bioprocess control engineer recently suggested that model- predictive control of growth rate in a fermentor would not work because the changes in growth rate were too small. If you consider it is just a matter of time frame, you see a resolution (pun intended). If an analysis were made every hour, the true change in biomass concentration would be small compared to the repeatability of the analysis. The signal-to-noise ratio for the rate of change of biomass concentration (biomass growth rate) would be poor. However, process control is still possible if the time interval between analysis data points is increased, and the result fed to a rate-of-change calculation, such as described in Full Throttle Batch and Start-up Response in Control, May 2006. Even though this calculation uses dead-time and velocity (rate) limit blocks, their proper setup does not introduce additional dead time.
For more details on such configurations, download the following pdfs.
Dead Time from Discrete
Devices and Analyzers
Rate of Change
Module
The use of a rate of change as the controlled variable is described for PID control of an exothermic reactor in my book, A Funny Thing Happened on the Way to the Control Room, and for model predictive control of a bioreactor in New Directions in Bioprocess Modeling and Control.Stan: In the old days, some project managers suggested using thermocouple DCS input cards instead of individual thermocouple transmitters to save money. The resolution (e.g., 11 bits), large-scale ranges (e.g., 632º) and fast scan rates (e.g., 0.25 sec) of these older DCS cards caused A/D chatter that was greater than the true change in temperature (e.g., A/D chatter of 0.30 versus a true temperature change of 0.001º). This A/D noise meant you could not use rate action or hardly any gain action even though it was permitted and even desirable per the process dynamics. The best solution is to use a smart transmitter and a newer DCS with a 16-bit A/D, but even so, a fast control execution interval may just be increasing loading rather than information and performance. A similar consideration holds for level control because the true level change during a time interval may be 0.0001% or less.
Greg: Whether we are talking about analyzers or any sort of digital communication, control and processing, a dead time is created for unmeasured disturbances from the time interval. The actual dead time to detecting and reacting to an upset depends upon the relative timing of the read (input), write (output) and the upset. If the output is done right after the input, the dead time varies from nearly zero to one time interval for an upset that arrives just before and after the input, respectively.
On average, we can say the upset arrives in the middle of the interval, so the average dead time is 1/2 the time interval. For unsynchronized digital devices, the worst-case dead time could be the summation of the time intervals. If the output is done at the end of the time interval, the dead time varies from one to two time intervals for an upset that arrives just before and after the input, respectively. This is the case for chromatographs and other analyzers where the sample is processed, and the analysis is ready at the end of the cycle time. Here the average is 1.5 times the time interval (cycle time).
Stan: In practice, the scan time of DCS inputs is set to reduce jitter and aliasing. But exception reporting and data compression can cause a distorted view of the data and can make any trend look flat, particularly large plot scales or short time frames.
This Month's Puzzler
What Times the Execution?
In a simulation test on the effect of module-execution time, what is the additional dead time from the module for a disturbance added to the measurement input to a PID block in the module with the same execution time as the module?
Send an e-mail with your answer, questions, or comments to The Puzzler.
Top Ten Signs Talk Radios Not for You
10. You have taken to using one-word sentences and one-syllable words like yep.
9. You think John Wayne was too verbose.
8. You feel life is just a series of subtitles.
7. Friends take to using sign language around you.
6. Strangers think you have laryngitis.
5. Your parents keep turning up their hearing aids.
4. You run off to become a roadie for the Blue Man Group.
3. Your favorite entertainment is watching mimes.
2. You let your slides do the talking.
1. You are mistaken for a statue.
About the Authors |
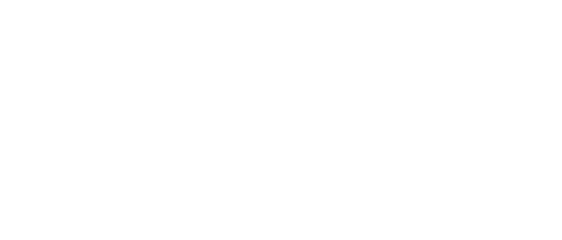
Leaders relevant to this article: