Nick Schreiber, Company Name Withheld
ANSWERS: You have an original idea for identifying at a glance the control loops that need to be fixed in your plant. I suggest that concentrating on tuning should not be your first step. First, look at the process to see if the design itself is correct and if the loop components are defective. You will probably find that 50 out f your 79 loops either have defective sensors or faulty valves (in one nuclear plant, 18% of the motor-operated valves were defective). You also will find that some tasks simply cannot be handled by a single feedback controller, because they require feedforward, de-coupling or model-based multivariable control.
To answer your question on tuning, I have asked some of my colleagues to fill in a summary table with some typical tuning valves. These are below. You will note that even these experts disagree on some aspects, such as the use of derivative on pH control (which I found very valuable on batch neutralization applications), or the use of positioners on flow loops, which in my view are not recommended. If you want to become knowledgeable on the subject of tuning, read the 200 or so pages on that topic in my handbook, the Instrument Engineers Handbook.
You also should consider the correct selection of control valve characteristics when reviewing your control loops. Liquid pressure and temperature control usually requires equal percentage valves, while for flow, level and gas pressure control we use linear valve characteristics if the ratio of maximum to minimum valve drop is under 2.0; above that, we use percent.
As to positional vs. velocity algorithms, you should keep in mind that a velocity algorithm has no internal reference, it gives an oscillatory response to large inputs, and a change in the sampling rate affects the loop again. These should not be used on noise processes such as flow.
When using positional algorithms, make sure they are not susceptible to reset windup and are capable of bumpless transfer. If the supplier provides these features by activating the integral term only when the output is connected, it will impair the testing capability of the loop.
Lots of luck to you in your new job. I like your attitude, because not even a single controller should be in manual in any plant. When a controller is in manual, somebody is not doing his or her job.
I DON'T HAVE any problem filling out the table. In fact, there is a very similar one in the 4th Ed. of my book Process Control Systems, (McGraw-Hill, 1996) p.99. Attached is my filled table.
Greg Shinskey
CONTROLLED VARIABLES |
PB* (%) |
I*Ā (minutes/repeat) |
D* (Minutes) |
OTHER (See Note) |
Level |
20-100 |
2-10 |
Ā |
PĀ Po |
Flow |
100-300 |
0.02-0.2 |
Ā |
Po |
Pressure |
10-50 |
0.2-2 |
Ā |
PĀ Po |
Temperature (std.) |
20-100 |
0.5-50 |
0.1-12 |
Po |
Cascade Master |
20-100 |
10-50 |
2.5-12 |
ERĀ Po |
Cascade Slave |
20-50 |
2-5 |
0.5-2 |
Po |
pH |
100-500 |
5-25 |
1-10 |
Characterize |
Note :
* typical range of setting
P:Ā control valve should have positioner
ER: external reset is recommended
Po or Ve: the digital algorithm used should be the positional or velocity type
SOME COMMENTS in addition to the figures given in the tabulation below:
- All controllers should have bumpless transfer. If the vendorās system requires external reset to achieve bumpless transfer, or to prevent windup of the cascade master when cascade slave is not in āremote,ā then ER is required, regardless of the application. Otherwise ER is required only on override control applications.
- The vendorās system will determine whether a positional or velocity type algorithm is used. The type of application is immaterial, since in general they will provide equal performance.
- Tuning parameter ranges assume an ISA āidealā form of PID algorithm is being used. If an interactive form is used, and the derivative mode is used, then the range of values for PB and for D should be doubled, and the range of values for I should be halved.
Harold Wade, Wade Associates, Inc. [email protected]
CONTROLLED VARIABLES |
PB (%) |
IĀ (minutes/repeat) |
D (Minutes) |
OTHER (See Note) |
Level, Surge Drum |
(HLA-LLA)-!0% |
Not reqād |
Not reqād |
Ā |
Level, Tight Cont |
40% - 200% |
1.5 ā 15 |
Not reqād |
P |
Flow |
100 ā 250% |
0.2 ā 1.0 |
Never |
Ā |
Pressure, Gas |
2% - 5% |
May not be reqād |
Not reqād |
Ā |
Pressure, Boilr Mstr Ā or DistTower |
10% - 50% |
3.0 ā 10.0 |
0.0 ā 1.0 |
P (if not a cascade master) |
Temperature (std.) |
10 ā 50% |
5.0 ā 20.0 |
0.0 ā 2.5 |
P |
Cascade Master |
10 ā 50% |
5.0 ā 20.0 |
0.0 ā 2.5 |
ER |
Cascade slave |
50% - 200% |
2.0 ā 5.0 |
CW Cont on Exoth Reactor: 0.5 ā 1.0 Otherwise: Not req |
P |
pH |
100 ā 1000% |
3.0 ā 20.0 |
0.5 ā 2.0 |
P (also linearize PV) |
BE CAREFUL ABOUTĀ general rules for specific PID numbers because there are different algorithms available.Ā In general, use positioners on all the loops.Ā Positioners may be overkill on fast pressure loops.Ā Use External Reset on inner (slave) loops of cascades or if there are limiters or selectors on the other loops.Ā Velocity or positional algorithms will work; however there are often two distinct advantages to positional algorithms: fewer numerical problems and better anti-reset windup.Ā If you use a controller from any of the major DCS vendors, you will be fine.
Using http://www.expertune.com/tutor.html#InitialPID and assuming a series PID algorithm the table becomes:
CONTROLLED VARIABLES |
PB (%) |
IĀ (minutes/repeat) |
D (Minutes) |
OTHER (See Note) |
Level |
1 to 50 |
1 to 100 |
.01 to .05 |
P, Po |
Flow |
50 to 500 |
.005 to .05 |
0 |
P, Po |
Pressure (gas) |
1 to 50 |
.1 to 50 |
.02 to .1 |
Po |
Temperature (std.) |
2 to 100 |
.2 to 50 |
.1 to 20 |
P, Po |
Cascade Master |
2 to 100 |
.2 to 50 |
.1 to 20 |
P, Po |
Cascade slave |
Assume flow |
Assume flow |
Assume flow |
P, ER, Po |
pH |
1 to 100 |
1 to 100 |
0 |
P, Po |
Keep in mind that there are products that can monitor the performance of your control loops on a continual basis and provide you with a prioritized list of loops to work on.Ā They also provide the tools to diagnose, repair and tune the loops.Ā A performance monitor directly answers the need you have.
John Gerry, ExperTune Inc.,Ā 262/369-7711
GIVING DEFAULT values for PID tuning parameters can be misleading. At the same time, being able to determine at glance it the values make sense is interesting.
We often do a short exercise with our customers, where we download the values from the DCS, convert them for an Ideal Algorithm, and apply simple rules such as:
- If Filter time for a flow loop is > 2s
- If Derivative is used for a flow loop
- If Integral time for a flow loop is >20s
- If Prop gain for a level loop is < 1
- If Integral time < Derivative time
- If Derivative time < Filter time
If any of these are TRUE, we turn it RED. After the exercise, we usually have more than 50% RED and we explain to our customers that those need attention. The loops should be looked at one by one. At a glance, many problems will be found; for example, a large reservoir with a very short integral time.
After this exercise the optimization work can be done: verifying configuration, set-up, ranges, and equipment.Ā Click this link.
We also have many papers at: http://www.topcontrol.com/techinfo/papers.php
Michel Ruel P.E., TOP Control Inc.
YOU HAVE AN original idea for identifying at a glance the control loops that need to be fixed in your plant. I suggest that concentrating on tuning should not be your first step. First, look at the process to see if the design itself is correct and if the loop components are defective. You will probably find that 50 out of your 79 loops either have defective sensors or faulty valves (in one nuclear plant, 18% of the motor-operated valves were defective). You also will find that some tasks simply cannot be handled by a single feedback controller, because they require feedforward, decoupling or model-based multivariable control.
To answer your question on tuning, I have asked some of my colleagues to fill in a summary table with some typical tuning values. These are below. You will note that even these experts disagree on some aspects, such as the use of derivative on pH control (which I found very valuable on batch neutralization applications), or the use of positioners on flow loops, which in my view are not recommended. If you want to become knowledgeable on the subject of tuning, read the 200 or so pages on that topic in my handbook, the Instrument Engineers Handbook.
You also should consider the correct selection of control valve characteristics when reviewing your control loops. Liquid pressure and temperature control usually requires equal percentage valves, while for flow, level and gas pressure control we use linear valve characteristics if the ratio of maximum to minimum valve drop is under 2.0; above that, we use percent.
As to positional vs. velocity algorithms, you should keep in mind that a velocity algorithm has no internal reference, it gives an oscillatory response to large inputs, and a change in the sampling rate affects the loop gain. These should not be used on noisy processes such as flow.
When using positional algorithms, make sure they are not susceptible to reset windup and are capable of bumpless transfer. If the supplier provides these features by activating the integral term only when the output is connected, it will impair the testing capability of the loop.
Lots of luck to you in your new job. I like your attitude, because not even a single controller should be in manual in any plant. When a controller is in manual, somebody is not doing his or her job.I JUST STARTED a job where I am responsible for operating a chemical plant that has some 350 control loops. My survey indicates that today, for one reason or another, 79 of my loops are switched to manual. I would like to get your help to allow me to focus in on the manual loops, which are obviously set incorrectly. Please give me guidance on which PID control mode should be used when, and what are their typical ranges of tuning settings, so I can pick out the loops with settings that stand out as being āway off.ā I thank you and CONTROL magazine for this free consulting service.
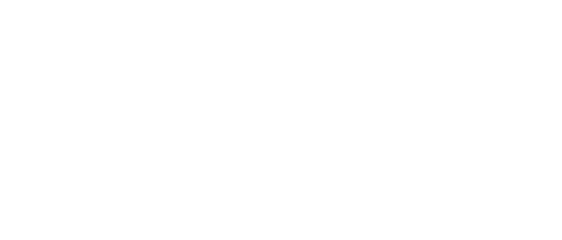
Leaders relevant to this article: