EIGHT: 41.35pt; mso-element: dropcap-dropped; mso-element-wrap: around; mso-element-anchor-vertical: paragraph; mso-element-anchor-horizontal: column; mso-height-rule: exactly; mso-element-linespan: 3; mso-line-height-rule: exactly">E |
ver since Wal-Mart started demanding Electronic product code compliance, Radio Frequency Identification (RFID) tags have become standard operating procedure for the giant retailer's myriad suppliers. And as RFID technology suppliers crank out more and more product, prices are coming down, making RFID attractive to use on the plant floor for tracking, monitoring, and controlling your processes. EPC, which you’ll often see used in conjunction with RFID tags is a hot new technology destined to replace barcodes. Although EPCs function like bar codes, when teamed with RFID tags they can do much more (see sidebar). RFID tags offer several advantages over barcodes in that they can:
- Withstand harsh environments
- Be read without any optical alignment
- Allow simultaneous reads of several tags, even in concealed boxes
- Contain more data than a bar code (e.g., batch number, production line)
- Allow for protocols such as EPC
- Allow writing of data to the tag, which allows continuous updating of data
Product Monitoring Marvel
On the plant floor, when teamed up with a manufacturing execution system (MES), an RFID tag might log the conditions in which a product was manufactured, allowing engineers to trace any shifts in production equipment or product status. For example, RFID keeps autoclave sterilization records for an Italian pharmaceutical manufacturer, Pierrel-Ospedali, which must prove to the government that bottles on a tray (to which a read/write RFID tag is attached) were kept at 120° C for a required length of time. So, not only are RFID tags able to withstand the brutal heat, the devices eliminate human error in the process.
Smart Couple
Smart Coupling series from Colder integrates RFID technology into a host of standard couplings and package inserts to automatically exchange product data at the exact time and location of the connection.
According to Andreas Somogyi, Rockwell Automation RFID global program manager, RFIDs offer great flexibility and utility as far as what kind of data can be tracked, and how RFID can be applied to batch or continuous processes. "Production data is very crucial," he said, "and needs to be stored on the tag: date created, batch number, production line, serial number, expiration date, SKU, etc. For batch operations, it’s WIP tracking, broken (scrap) tracking, and reprocess tracking."
Rockwell has made a major foray into the RFID field with an experimental testing lab in Milwaukee and by putting RFID to work in one of its production facilities. "We just finished an implementation for material movement at our manufacturing facility in Twinsburg, Ohio. We tag three different catalog numbers with RFID tags, read them, and marry them with the standard barcode," Somogyi says. "Then we ship them to our global distribution center in Champagne, Ill. where we read the items via an RFID dock application. We also use it for quality control purposes in Champagne where the RFID gets linked to the customer purchase order number," he adds.
Achieving tight control of fluid processes and the fluid lines within machinery is critical for many of Colder Products Company (www.colder.com) customers. Misconnections in fluid handling can cause significant delays in production, and are potentially hazardous to operators or end users. RFID helps prevent these mistakes—and costs—caused by unavoidable human error.
How Does RFID Work? |
RFID systems consist of a reader (radio transmitter-receiver) and a transponder "tag." Today’s readers (also called controllers) can be a portable, handheld device or a box-based system that integrates directly into PLCs, DCSs, or most any control system that is capable of serial, device-level bus, or Ethernet connections. RFID is not new and goes back to the "IFF" (Identification—Friend or Foe) systems used on military aircraft as early as World War II. Tags, in a variety of sizes, memory capabilities, ranges, and levels of durability, are placed on the product you want to track. They are small enough to be embedded in an animal or large enough to cover a desk and can be built into labels on paper or polyester, or a printed-circuit board to be embedded on carriers. Active tags contain a built-in energy supply (usually a battery), silicon chip, memory, coil, and antenna. Active tags are capable of transmitting to the controller on their own without additional power. Passive tags have no power supply of their own and rely on converting some of the controller’s transmitted signal to energy to send a signal back to the controller. Tags are available as read-only, and read/write. Read/write tags can be classified as reusable and disposable. A reusable tag typically would be used within the plant for tracking and reworking purposes. A disposable tag may follow the product from manufacture to distributor to retailer to end user. In general, read-only tags have the lowest memory capability—often 20 bits or so. Active read/write tags can often hold as much as 32 Kbytes or more. Read/write speeds depend on several factors: length of data to be transmitted, the physical range between the transponder and controller, the radio frequency on which the system operates, modulation technique used, etc. Generally speaking, higher-frequency radio systems can send data faster, but may have shorter range than lower frequencies. The most commonly used ranges are: 125/134.2 kHz, 13.56 MHz (ISO 15693), 900 MHz (typically for EPC), and 2.45 GHz. There is a tradeoff between frequency usage and noise. Lower frequencies should have longer ranges than higher frequencies, but noise at lower frequencies can degrade operation. The higher frequencies often can penetrate metal enclosures better than lower frequencies, but higher frequencies are susceptible to standing wave nulls, which can cancel shorten reliable distances. |
Wayne Labs is a process automation veteran with more than 15 years engineering experience and 20 years in senior editorial positions. You can reach hime at www.waynelabs.com.
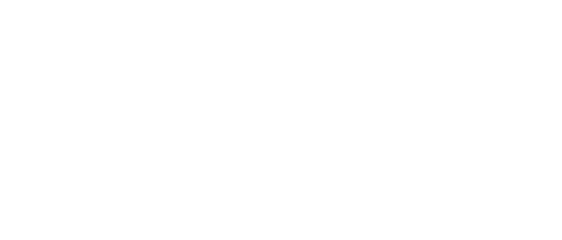
Leaders relevant to this article: