Call it what you will, it's still artificial intelligence
Oct. 27, 2004
Theyāre not really using Artificial Intelligence (AI)Ā over at the St. Maryās Paper plant in Sault Ste. Marie, Ontario , or are they? They are, but paper machine superintendent Dave Dube doesnāt look at it that way. āItās part of a puzzle that controls the caliper, and the gloss and smoothness of our supercalendared paper,ā he says. Sensors measure, in real time, the condition of the product going through manufacturing process, and automatically adjust the sheen in all directions.This used to be very difficult. "We would spot check a few feet of sheet," Dube recalls, āadjusting the result through the use of steam boxes.ā With real-time monitoring, Dubeās system can make adjustments using both caliper coils and steam boxes. "This is what all the engineers were telling us would be the real challenge on this project--not having caliper coils fight the steam boxes," Dube comments.Such a procedure could only be done effectively in real-time, which meant not just scanning the output, but adjusting the manufacturing process as it happened. No engineer can do this manually, but software can. In this case, itās a state-of-the-art, large-scale, model predictive controller for paper machines which strikes the balance. The software takes input from the sensors and passes instructions to the machines. Honeywellās Performance CD Multivariable controller is, in essence, a neural network. Honeywellās technology, however, is 15 years old, senior consultant Lance Johnson notes. What gave it AI capabilities is Moore ās Law, computer power getting faster and cheaper. That means software can now be embedded āat the base level control layer for single loops,ā resulting in āa model predictive controller at an execution interval of ü to ý second,ā says Johnson.Then, by encapsulating multiple systems āin one cohesive horizon,ā Johnson adds, you have a system for controlling a plant, not just a machine. The result is a complete network of sensors, actuators, software and hardware that can manage a plant to its optimum without operator intervention. In other words, Artificial Intelligence. From the Esoteric World of AI
Many techniques that came from the esoteric world of AI are now proving themselves on the plant floor. Besides neural networks, processors and manufacturers are installing software agents and expert systems. They are often retrofitting existing equipment with new software. But they donāt call it AI.Instead they just call it improved process control. Thatās the way Charles Cutler, president of Cutler Technology Inc. San Antonio, Texas describes what heās offering.Cutler, a CONTROL Process Automation Hall of Famer, first retired in 1996 after selling DMC Corp. and its Dynamic Matrix Control technology to AspenTech. "After I retired, I started thinking [about] this problem," he says, and began thinking of ways to improve the DMC algorithm.According to Cutler it was a revelation. "You put constraints on the system, via a linear program, and it keeps the machine inside those boundaries. When it comes up against a boundary, it makes a decision based on software, rather than [on some] arbitrar[y factor]," he says. Engineers were turning his linear controller into an expert system.Most major process control vendors are working on some form of expert system or neural network to enhance productivity. These companies are not just getting more production out of each worker, theyāre improving quality, extending equipment lives and using all inputs more efficiently.ARTIFICIAL INTELLIGENCE INSIDE
Ā
Ā
Ā
Ā
Many techniques that came from the esoteric world of AI are now proving themselves on the plant floor. Besides neural networks, processors and manufacturers are installing software agents and expert systems. They are often retrofitting existing equipment with new software. But they donāt call it AI.Instead they just call it improved process control. Thatās the way Charles Cutler, president of Cutler Technology Inc. San Antonio, Texas describes what heās offering.Cutler, a CONTROL Process Automation Hall of Famer, first retired in 1996 after selling DMC Corp. and its Dynamic Matrix Control technology to AspenTech. "After I retired, I started thinking [about] this problem," he says, and began thinking of ways to improve the DMC algorithm.According to Cutler it was a revelation. "You put constraints on the system, via a linear program, and it keeps the machine inside those boundaries. When it comes up against a boundary, it makes a decision based on software, rather than [on some] arbitrar[y factor]," he says. Engineers were turning his linear controller into an expert system.Most major process control vendors are working on some form of expert system or neural network to enhance productivity. These companies are not just getting more production out of each worker, theyāre improving quality, extending equipment lives and using all inputs more efficiently.
Over at IMC Agrico in Mulberry,
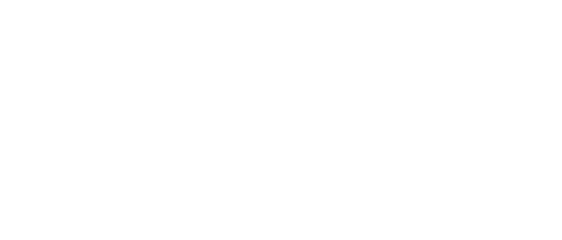
Leaders relevant to this article: