How to simulate wireless control
Terry Blevins, principal technologist, and Mark Nixon, director of applied research, Emerson Process Management, are members of the Control Process Automation Hall of Fame.
The simulation can be used off-line with the existing distributed control system (DCS) monitoring and control modules and operator interface to explore and get familiar with tools for wireless control, such as PIDPlus for wireless control (May '15, p. 39) or wireless model predictive control ("Control Talk," June '15, p. 55). The capability also may be used to build comprehensive operator training systems.
How a modern simulation works
When a DCS is structured, for example, to allow control modules to be created using Foundation fieldbus function blocks, the analog output (AO) block is used to manipulate final control elements, such as valves, dampers or variable-speed drives. The analog output block's OUT parameter represents the current or digital signal to these final control elements and is the input to the process simulation. Similarly, in discrete process control, the OUT_D parameter of discrete output blocks may be added as input to the process simulation. Measured and unmeasured disturbances may be included in the simulation as adjustable discrete or analog parameters. When included, these parameters are also inputs to the process simulation.
The process conditions that result from the manipulated and disturbance inputs (e.g., monitored measurements of process conditions, such as flow, pressure, temperature, level or composition, or the discrete state of a limit switch) are reflected in the process simulation outputs, and may be easily included in the simulation. Some of these process conditions may be measured in the field using transmitters or switches, and thus, the simulated values can be provided to the modules that access these field measurement values using analog and discrete input blocks.
The current or digital outputs of these transmitters and switches are normally accessed in a control system using the analog and discrete input blocks. However, the normal processing of analog and discrete input blocks can be altered by enabling the Simulate parameter. When simulation is enabled in an input block, a Simulate parameter value is used in place of the field measurement. Thus, the simulated process output values may be used by analog and discrete input blocks in place of field measurements. Process simulation may be incorporated into the control system via this basic control system capability.
The most common way to add process and wireless communication simulation capability to a control system is to create new modules that contain only the process and wireless communication simulation. These simulation modules may be added without modifying existing modules because most modern control systems include the capability for a module to read and write parameters contained in another module (Figure 1).
Figure 1: Simulation modules may read the output value of analog and discrete output function blocks that are part of a control module. The results of the simulation modules may then be written back to the simulation input parameters of the analog and discrete input blocks of the existing modules.
The I/O blocks' Simulate parameter can be enabled in the existing modules to use the process simulation. When simulation is enabled, the normal operator control displays and engineering tools may be used to view the monitoring and control functions performed by the existing control system modules.
Develop the simulation from the P&ID
The plant piping and instrumentation diagram (P&ID) often serves as the starting point to develop a process and wireless communication simulation for control system checkout or operator training. In most cases, one process and wireless communication simulation module should be developed for the modules that support control or monitoring functions associated with each piece of equipment. Thus, a first step in developing a simulation is to break down the equipment and piping on the P&ID into multiple processes that may be simulated in one or more simulation modules.
Figure 2 uses the example of a recycle tank to show how the equipment and piping on the P&ID may be broken into smaller sets of equipment that represent processes and then expressed as a simulation diagram.
The simulation diagram may be implemented as a simulation module that references the existing control modules. The processes and wireless communications on the simulation diagram are implemented as composite blocks in the simulation module. Process inputs from final control elements are added as external references to the setpoints of the analog and discrete output blocks in the existing control modules. Unmeasured inputs to a process should be added as parameters. Process outputs and wireless communication simulations that represent field transmitter measurements are then implemented as external references that write to the Simulate parameter of the existing modules' analog and discrete input blocks.
Simulation implementation
Figure 2: The highlighted areas of the P&ID will be simulated processes that are interconnected and can be documented along with the simulated wireless communications in a simulation diagram. Here, the makeup flow to the recycle tank is regulated by LC134 using a wireless on-off valve, FV134, based on the wireless level transmitter, LT134. The flow out of the tank, FT133, is regulated by LC134, using a wired throttling valve, FV133, based on a wireless flow measurement, FT133, and PIDPlus for flow control, FC133.
When a control system is commissioned, the step response of a self-regulating process is often characterized as first order-plus-dead-time. Similarly, the step response of an integrating process is often characterized by the dead time and the integrating gain. It's appropriate to design a process simulation to duplicate the step response. For example, the simulation of a single input-single output (SISO) self-regulating process may be created using a filter block, a dead-time block and a multiplier block to simulate the process deadtime, time constant and gain. Process noise may be added to the simulated process outputs using a signal generator block.Simulation of an integrating process should take into account the module execution period, and should support a varying number of inputs. In addition, the calculated value for the level should be limited to the vessel height. For example, a combination of standard function blocks and a calculation block may be used to implement the recycle tank level simulation.
The real-time dynamic response of the simulated tank and associated control modules will accurately reflect changes in flow to the reactor and in the recycle tank inlet flow disturbance input that is defined in the recycle tank simulation module.
Figure 3: A single composite may be created to simulate communication of a measurement value from a wireless transmitter to the gateway and its access by the control system. Here, the composite COM_TRANS allows either WirelessHART continuous (periodic) or window (non-periodic) communication to be simulated based on its setup parameters.
A single composite may be created to simulate communication of a measurement value from a wireless transmitter to the gateway and its access by the control system. For example, the composite COM_Trans shown in Figure 3 allows either WirelessHART continuous (periodic) or window (non-periodic) communication to be simulated based on the setup parameters of the composite.
Four parameters are provided in composite to define the communication setup:
- COM_DB – The percent change in the measurement valve from the last communicated value that will trigger a communication.
- COM_Default – The maximum time in seconds between communications.
- COM_Period – The period at which the transmitter wakes up, makes a measurement, and determines if the new value should be communicated based on the change in value and the time since the last communication.
- EXEC_Period – The execution period in seconds of the module that contains the COM_Trans composite.
By setting COM_DB to zero (0), the measurement value will be communicated on a periodic basis based on the update time specified in the parameter COM_Period. When COM_DB is set to a positive non-zero value, the measurement value is compared to the last communicated value on the period specified by COM_Period. If it exceeds the dead band specified by COM_DB, the value is reflected in the composite output to simulate communication of a new value. If the time since the last communication exceeds the default update time, COM_Default, the composite output is also updated to simulate the value that is communicated. If the measurement is used in control, PIDPlus detects communication of a new value by determining that the measurement value has changed.
Simulating non-linearity
For more information on control using wireless control simulation see Chapter 11 of the book, Wireless Control Foundation–Continuous and Discrete Control for the Process Industry. Workshops contained in the book are used to highlight key points. YouTube videos showing workshop solutions can be viewed at the book's website. The book may be purchased through the ISA website and on Amazon.
A non-linear installed valve characteristic may be simulated by substituting a characterizer block for the gain multiplier block. Similarly, non-linear response often seen in analytic measurements, such as concentration after blending two streams or heater outlet temperature for varying inlet flows, may be accounted for in the process simulation. The corrections in process gain must be based on input/output relationships determined by performing energy and/or mass balance at steady state.
Other considerations
Many excellent commercial simulation products may be purchased for process design. The simulation tools supported by these products are based on first-principle analysis of equipment, based on established laws of physics and chemistry, that does not make assumptions such as empirical model and fitting parameters. These simulations typically provide better results over a wider operating range than is possible using a step-response model. Though such tools have been successfully used for operator training, the cost of engineering a simulation with these tools is often prohibitive if the simulation is to be used only for control system checkout or operator training. Also, the expertise needed to update these types of first-principle simulations to reflect changes made at plant startup is often not available in process plants.
References
- Blevins, T. and Nixon, M. Control Loop Foundation – Batch and Continuous Processes, Research Triangle Park: International Society of Automation (ISA), 2011.
- Culter, C. "Operator training simulation" World Oil, p. 3, April 2005.
Latest from Multivariable Control
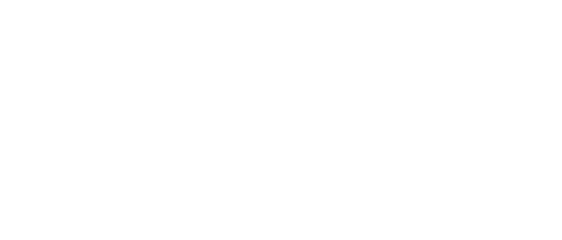
Leaders relevant to this article: