Real-Time Control for Optimization Goes Beyond Energy Saving
The growth potential of any technology or technological approach should be analyzed from two perspectives, the capability of the technology and scope of application. In the field of process control, for example, the introduction of multivariable predictive control provided a major leap forward in capability, but its scope of application was actually a bit narrower than traditional feedback control, primarily due to the cost and time required to apply it.
In fact, over the years, many advances in control technology have been based on capability, moreso than scope or enhancements. Process control technologies were developed to enable efficiency improvements in complex industrial production processes. Efficiency refers to process control applied to meet the production requirements of industrial operations safely while simultaneously working to reduce energy and material consumptions. The word control as used in industrial organizations is generally assumed to mean process control for improved efficiency.
See Also: How to Connect Real-Time Optimization to a Predictive Multivariable Controller
Today, control strategies are still largely focused on improving efficiency. To date, there has really been very little effort to formally apply real-time control to other industrial challenges beyond the scope of efficiency improvement. There is considerable evidence that this is about to change in a very big way.
[pullquote] A number of market-driving forces are causing industrial companies to consider the application of real-time controls in new domains. Perhaps the most influential driving force has been the transition of some critical business variables of industry toward real-time variability. Two decades ago, most of the critical business variables of industry changed very minimally or not at all for months on end. For example, the price industrial companies paid for the electricity they consumed was essentially and contractually a constant value for months at a time. When this was the case, there was no need to control the price of electricity because it seldom changed. All industrial companies had to do was apply real-time controls to reduce the consumption of electricity without any concern for its price, and the cost they paid would be correspondingly reduced.
Not anymore! With the deregulation of electric power grids, the price of electricity started to fluctuate in much shorter time frames, and those fluctuations have become larger over time. For example, today in the United States, the price of electricity can change on the open grid every 15 minutes. This means that consumers such as industrial plants need to control more than just the overall consumption of electricity. They need to control the consumption within very short pricing periods. If they don’t do this, they may reduce the overall consumption of electricity over a day, while the price they pay for the consumed electricity over that day actually increases because they consumed during high-price periods.
The real-time variability of electricity prices has triggered a domino effect across other energy sources and raw materials used throughout industry. Production processes consuming a significant amount of electricity have transitioned to a similar level of real-time variability. Today in the U.S., the price of natural gas on the open grid changes every 15 minutes, and the price of some raw materials used in industrial production, such as base minerals, may change as fast as multiple times each minute. The point is that some of the critical business variables associated with industrial production have transitioned to real-time or near real-time variability.
The traditional approach taken by industrial companies has been to manage business variables on a monthly, transactional basis while controlling operational variables, such as flow, pressure, level and temperature, in real-time frames. This worked fine as long as all business variables changed only on a monthly or greater time frame. As some of the business variables have shifted to real-time variability, traditional business management approaches and time frames prove insufficient. In fact, a number of industry executives I interviewed suggested that their production processes were in control, but their business processes were out of control.
This presents a daunting challenge to industrial companies. What is required to effectively meet this challenge is the application of real-time control on real-time business variables. This application is directly targeted to bring the real-time components of business profitability under control again. Therefore, the scope increase required to meet this challenge is the application of real-time control strategies to business profitability—real-time profit control. This requires development of real-time business measures for the real-time components of profitability because such measures are a prerequisite for real-time control.
When all the critical business variables directly associated with the profitability of business operations were stable for months at a time, industrial engineers applied linear and nonlinear optimization software to optimize to a selected business objective. The optimization software is designed to maximize or minimize to a particular objective (such as maximizing production value or minimizing energy cost) while not exceeding critical constraints, such as safety and environmental requirements. As key business variables have transitioned to real-time variability, control strategies are required to bring the business under control, but the objectives of these control strategies, the setpoints, must be set so as not to exceed the critical constraints, much in the same way as traditional optimization software.
Unfortunately, some constraint functions, such as the functions associated with safety and environmental risk, also tend to vary with the maintained state of the production equipment, quality of raw materials and phase of production. This has led to real-time variability in these constraint functions also requiring the application of real-time control. Therefore two additional potential scope increases for real-time control are safety and environmental risk control. Both of these require real-time measurement approaches to measure the risks associated with production processes.
Industrial operations are comprised of assets from physical process equipment right through critical business assets. In industrial operations, the phrase asset management has been co-opted to mean equipment maintenance. Maintenance departments are measured on the availability of the equipment assets and operations is measured on the production throughput realized from the operation of the assets. The challenge is that the production assets must continually operate at peak performance to drive optimal results for the business and operation. Neither asset availability nor production throughput directly measure asset performance. For optimal performance, the asset performance of every equipment asset in industrial companies must be measured and controlled in real time. Applying real-time control to asset performance of equipment assets provides a strong foundation for safety, environmental, efficiency and profitability control. This domain is referred to as real-time asset performance control.
One final, increasingly significant area where real-time control theory needs to be applied going forward is security control. Security in industrial companies has many facets. Perhaps the one in most urgent need of attention is cybersecurity. As industry pushed for more openness, standards and commercial off-the-shelf technologies (COTS) in automation systems, these systems were opened to cybersecurity risks. Openness is a desired characteristic of automation systems, but a high level of security is absolutely essential. Implementing an effective cybersecurity strategy involves bringing the security risks to industrial companies under control. Once again, this involves real-time measurement of cybersecurity risks and the application of real-time control.
Industry does not typically position profitability, safety, environmental integrity and security as real-time control challenges, but they are. I believe industry is at the dawn of a new era in the field of controls in which real-time measurement and control continue to be applied to process efficiency, but also to safety risk, environmental risk, security risk, asset performance and profitability. The knowledge and skills of control engineers are going to be the exact knowledge and skills industry requires moving forward.
The topological scope of the control problem is also increasing in multiple dimensions. Traditionally, process control was directed toward the control of process units or plant areas. Today, that control model must extend down the plant architecture to individual industrial assets and up the industrial hierarchy to include plants, enterprises and entire value chains. Extending both the functional and topological scope of control will result in huge improvements in efficiency, profitability, safety and environmental friendliness of industrial businesses. The talent required to lead the way is control engineering, but control engineering redefined for the future.
Is control engineering an obsolete discipline? No way. Control engineering will define the path for successful industrial companies that rise to meet the challenges of today and tomorrow.
Latest from Multivariable Control
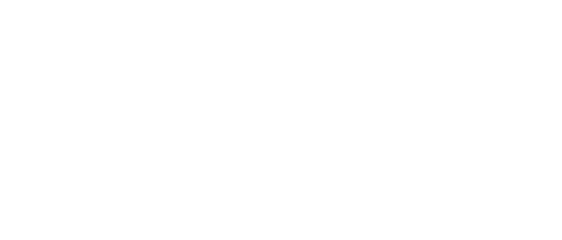
Leaders relevant to this article: