These days, manufacturers are putting more functionality into smaller-sized loop controllers, making it possible to shrink the the size of machines and control panels and reduce overall cost. However, many applications require more functionality than these tiny loop controllers can deliver. For instance, if end users have a variety of controllers from different vendors, networking is a highly attractive alternative. They can connect single-loop control to high-function networks such as DeviceNet or Ethernet. Then Internet connectivity is easy, which opens up a range of communication possibilities.
Dennis Schneider, product manager at Rockwell Automation says, “Loop controller trends currently include reduced costs and increased connectivity. The price of display technology has gone down, allowing integrated controllers to display more readable configuration and program characters. As the cost of microprocessors diminishes, control is getting faster, allowing improved intelligence and more communications with supervisory controllers.”
Paul Sagues, president of Berkeley Process Control, says, “The future direction of loop control is clearly toward more distributed nodes on standard networks. Whereas peer-to-peer architectures have been built as custom software applications, we see these identical, single-part-number, distributed modules using peer-to-peer architectures that are configured, not programmed. On some new semiconductor tools, we see the trend toward hundreds of such modules doing closed-loop temperature, pressure and plasma control control with nodes sharing information seamlessly.”
Patti Pool
Products Editor
DUAL SETPOINT CONTROL
Automata
530/478-5882
Control-RRR units operate pumps, valves and alarms based on a dual set point control algorithm. Each unit includes up to four control channels, and can display data from up to four sensors. The control is telemetry-ready for spread-spectrum radio, so sensors can be connected both locally and/or at remote sites. Each control output is associated with a sensor that provides feedback information to the controller. The controller compares sensor readings with two set points to determine whether to turn the control output on or off.
MINI CONTROLLER
Invensys, Eurotherm
703 443-0000
Mini8 controller performs PID loops outside the PLC without compromising the benefits of an integrated solution. It has four plug-in slots and can cater for a variety of signals such as thermocouples and RTD inputs and relay, logic and analog outputs. Up to eight discrete control loops can be connected to fieldbuses such as Profibus, DeviceNet and CANopen, which take responsibility for the loops outside the PLC. In the event the PLC is down, equipment pressure and temperature can still be maintained and failures avoided. It also offers Modbus both on RS485 or Ethernet.
WATER/WASTEWATER CONTROLLER
Moore Industries-International
818/894-7111
Model 555 ¼-DIN controller handles flow proportional control, residual control, compound control with lag times and dechlorination with sulfur dioxide. Designed for the water and wastewater industry, the controller can be used in the chlorination and dechlorination processes. The front panel is NEMA 4X-rated. All menu prompts are in English. The 55 has isolated 4-20 mA or 0-20 mA output for control or retransmission to an analog control system.
FUZZY LOGIC CONTROLLER
Ogden
800/OMC-4921
ETR-9300 1/16 microprocessor-based temperature controller has universal input, and all thermocouple, RTD, voltage and current types can be selected from the front panel. A universal power supply along with a low-voltage input option provides a wide operating range. An analog input allows the set point to be remotely adjusted. Remote networking of multiple controls is available with serial communications. The NEMA 4/IP65-rated front panel controller has an analog signal that retransmits the process value to a chart recorder, data logger or PLC.
INTEGRATED LOOP CONTROLLER
WATLOW
800/WATLOW2
EZ-ZONE ST integrated control loop integrates temperature control, power control, safety shut-down and power disconnect in a single package. It features a PID temperature controller connected to a high-amperage, solid state relay with the option of adding a properly sized heat sink, current measurement, an over/under temperature limit, a definite purpose mechanical contactor and digital communications in one package.
CREATE A CONTROL SYSTEM
National Instruments
888/280-7645
cRIO-9072 and cRIO-9074 CompactRIO systems have an integrated hardware architecture that combines an embedded real-time processor with a reconfigurable FPGA within a single chassis. Using this standardized architecture and LaBView tools, engineers can design and prototype industrial monitoring and control systems. Because engineers can reuse the same LabVIEW code during prototyping and deployment, they are able to shorten time to market.
SCADA APPLICATIONS
Control Microsystems
613/591-1943
SCADAPack 350/357 combines 32-bit processing with high-speed LAN and USB communications and power-saving features. The controller has an integrated power supply, 12 Vdc to 24 Vdc converter, analog and digital I/O, serial communication and turbine flowmeter counter inputs. SCADAPack 350/357 uses industry-standard Modbus and DNP3 serial protocols as well as Modbus TCP- and UDP-based Ethernet protocols and can be programmed locally or remotely through a choice of programming languages.
MODULAR CONTROLLER
Red Lion Controls
717/767-6511
Data Station Plus and Modular Controller now come with an XCDN DeviceNet option card. This card enables any connected devices to communicate with DeviceNet products to realize complete system integration and data transfer. In addition, the XCDN option card is isolated, protecting user’s equipment from potential harmful ground loops.
PLC/LOOP CONTROLLER COMBO
EZAutomation
877/774-3279
PLC packages include 8 built-in auto-tuned PID loop controllers for $40 to $60 a point, depending on display. An alphanumeric display with 8 in and 8 out is available for approximately $500. The EZPLC also has a PID monitor that allows the auto-tune cycle to be monitored and charted in Excel to achieve the best PID settings.
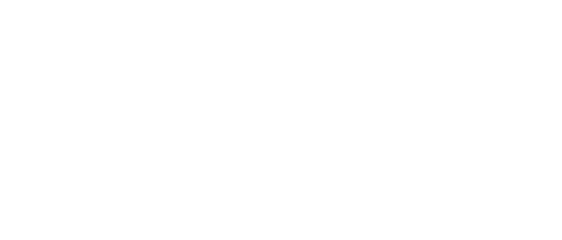
Leaders relevant to this article: