Q: I am Miten Thakkar from GSFC in India. I have a query regarding orifice-plate volumetric flow measurement. What can be the accuracy of a volumetric flow measurement when we measure differential pressure (DP) using a smart transmitter such as a Rosemount 3051 or Yokogawa EJA110E device?
MJ Thakkar
Deputy Manager (Instrument)
Inst. - Ammonia IV
Gujarat State Fertilizers & Chemicals
[email protected]
A1: The table shown in Figure 1 will give you the likely rangeability and accuracy of flow control loops when based on perfectly sized, accurately calibrated, correctly installed, clean and well-maintained orifice elements. But in my experience, this is never the case and, depending on the noted factors, the errors can be drastically greater. People often believe that using high accuracy and rangeability transmitters will make large improvements in the overall error, which is seldom the case because the errors are usually caused by generating inaccurate differential pressures, and not from the accuracy of reading them. If you read the comments of my colleagues below, you'll see how many potential error sources exist in orifice-based flow control.
Béla Lipták
[email protected]
Type of hardware | Rangeability | Orifice plate error | Transmitter error | Loop error at 10% flow | Loop error at 25% flow | Loop error at 35% flow | Loop error at 50% flow | Loop error at 100% flow |
Pneumatic | ||||||||
Standard transmitter | 3:1 | <1% AR | 0.5% FS | NG | NG | ∼3% | 2% | 1.5% |
Two plates or transmitters | 6:1 | <1% AR | 0.5% FS | NG | ∼3% | ∼3% | 2% | 1.5% |
Electronic | ||||||||
Standard transmitter | 4:1 | <1% AR | 0.2% FS | NG |
2% |
∼2% | ∼1.5% | 1.2% |
Smart transmitter | 15:1 | <1% AR | 0.1% FS | 2% | 1.5% | ∼1.5% | 1.2% | ∼1% |
Figure 1: The nominal accuracy of an orifice-plate flowmeter, as reported above, depends largely on a perfectly sized, accurately calibrated, correctly installed, clean and well-maintained orifice element. In practice, the pressure measurement itself is an unlikely contributor to error. (AR = actual reading; FS = full scale; NG = no good.)
A2: Often the accuracy of the transmitter is less of an issue than the accuracy of the meter calculation and compensation for deviation from design conditions. The DCS reading is the engineering unit high value / 10 * SQRT (% DP). This number is often off by 5 to 10%.
When the meter calculation is performed at the design stage, an orifice bore is calculated based on the desired orifice DP at the maximum flow. Before the meter is installed, the actual orifice diameter should be measured, and the existence noted of a weep hole and size, orifice plate material, and actual pipe size.
The meter calculation can then be run with correction factors for meter area thermal expansion; weep hole; actual flowing pressure vs. design pressure; actual temperature vs. design temperature; actual gas gravity vs. design gravity; gas super-compressibility (normally not needed except at very high pressure); and gas expansion factors. The resulting meter calculation at maximum DP gives a number that should be close to the engineering unit high value entered into the DCS.
Meter calculations also assume that the piping and orifice are clean and flow is homogenous across the orifice. I worked in a plant restart recently where meter readings were highly suspect. Many meters had rust buildup and scale partially blocking the orifice plate. These meters ran as much as 50% high.
Mass balances across sections of the plant helped determine which orifices needed to be removed, flushed, recalibrated and reinstalled.
Ralph J. McCloskey
Chief Engineer – Process Control Center of Excellence
Honeywell Process Solutions
[email protected]
A3: Although manufacturers might report the ability of their devices to have a 2% flow rate error, in my experience, best practicable is about 5%, and the error may be greater due to many reasons. Orifice flow rate devices are less expensive than other types of flow rate measurements, so they're often an economic preference. However, the user needs to balance cost with performance. I think the general rule is that if flow rate measurement is critical (such as in custody transfer), then use one of the more accurate devices. And if flow control is used for in-line composition, use composition measurement feedback to adjust the flow rate setpoint to correct the orifice measurement.
There are many issues to consider with accuracy and precision of orifice meters, and many are unrelated to the measurement device itself. Here's a list of issues that immediately come to my mind:
- The classic assumption of the square-root relation of volumetric flow rate to pressure drop is based on the ideal Bernoulli relation for non-viscous, linear, streamline flow. Installation geometry factors are critical, and even if they're closely followed, the square-root relation is not exactly true, and the orifice flowrate can be off by several percent.
- Orifice plates can be installed backward, and can erode or corrode over time. In any case, even if it was perfectly installed and calibrated, the calibration changes over time.
- Pressure taps can accumulate non-condensable gases, heavy liquids or particles, all of which will change the differential pressure, leading to a calculated flow rate error.
- If the liquid or gas density isn't well known, or is different from the calibration fluid, that will cause error. The size of the flow rate error is proportional to the ratio of density error to the fluid density. Therefore, if this ratio is 1%, then the calculated flow rate will have a 1% error.
- The DP sensor needs to be calibrated, and the calibration error may change over time, perhaps due to ambient temperature. This error is proportional to the DP error divided by the square root of DP. This can become very important at low rates.
- If the orifice plate is improperly sized (likely some ideal relation was used to size it), or even if once properly sized but the flow rate significantly changes, this could lead to out-of-range, high DP values or extreme low DP values in the very sensitive portion of the square-root functionality.
- The relationship between orifice flow rate and pressure drop is valid only for fully-turbulent flow.
- Error is caused if the measurement is noisy or fluctuates rapidly in time due to flow turbulence. In such cases, measurement averaging is needed to dampen the noise. If the noise is 5% of the signal (each sampling has a ±5% perturbation, which seems reasonable from my experience), then using the statistics central limit theorem to reduce the error on the signal to just 1% requires an averaging of 25 samples. If the sampling is 10 Hz, and a first-order filter is used, this means introducing a measurement lag of 2.5 seconds. Averaging reduces, but doesn't eliminate the measurement error due to process noise.
- There are two sorts of error. Bias (or systematic error) is the true average error due to installation and calibration imperfections. Random error is due to noise, with independent perturbations on each sampling. The reported measurement combines both.
- Because of noise filtering (or any sort of averaging, whether it's on the device or in any part of the communication and display system), the filtered value will lag the true value during a transient. So, if you're interested in tracking a transient, the error due to the lag might even be larger than the combined bias and random errors.
- Using the ideal square-root relation and propagating uncertainty, the error is proportional to the inverse of the square root of the DP. This means that, at low flow rates, the measurement error is much larger than at high flow rates.
- Likely, there are several digital processing steps in the DP device. If a device has a 10-bit processor, it can only have 2^10 = 1,024 values. If the middle 60% are used for the signal (such as 5-20 mA in a 25 mA range, or 3-15 psi in a 20 psi range), then counts between about 205 and 820 would be used for the signal. With only 820 - 205 = 615 values, the resolution due to digital discrimination is 100/615 = 0.16% of full scale. This means that, even if the DP sensor and equation to convert DP to flow rate were perfect, there would be a 0.16% error. Depending on where the digital process is happening, this resolution error may be invisible at high flow rates, and progressively dominant at lower flow rates.
R. Russell Rhinehart,
Emeritus Professor
[email protected]
Web: https://www.r3eda.com
Books: https://www.amazon.com/author/rrussellrhinehart
Latest from Home
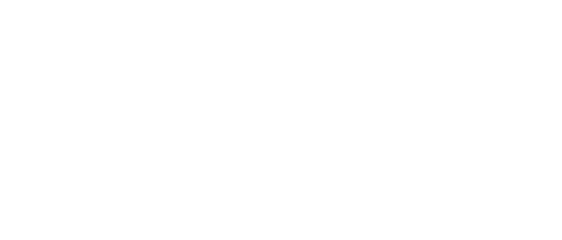
Leaders relevant to this article: