Preview
- In the wake of robust advanced process control (APC) activity for several decades, industry now finds itself with an APC paradigm that is largely obsolete, often unhelpful and sometimes misleading.
- The time is opportune to rethink APC to shape an updated, more accurate, realistic and useful paradigm to form the basis for greater APC success going forward.
Role of advanced process control
Figure 1: Advanced process control (APC) earns benefits by holding the process closer to constraints than manual control, even as the process operating point and constraint limits move dynamically.
Figure 1 is the most traditional and fundamental way to summarize the essential role of APC in real-time process control and optimization. It can be elaborated upon as follows:
- APC can keep a process closer to constraints, because its automated nature means that it can back the process away from encroaching constraints in a responsive and reliable manner, should that become necessary due to unexpected disturbances or changes in process conditions. By the same token, APC can automatically pursue constraints as they move further away, capturing additional earnings.
- In the absence of an automated APC application, operators tend to keep the process further from constraints in order to provide greater time to respond and a wider margin of error, should manual intervention become necessary. This greater distance from constraints typically translates into a cost penalty in terms of an incremental loss of capacity, yield, energy efficiency, etc.
This way of viewing and understanding the essential role of APC in process operations remains perfectly (and very usefully) valid today. However, several other aspects of the original paradigm have grown obsolete, unhelpful or even misleading.
Legacy APC paradigm
Current (obsolete) APC paradigm | Updated APC paradigm and vision |
APC is essentially synonymous with model-based predictive multivariable control technology (MPC), and is often exclusive of other approaches to APC. | APC refers to "a broad range of techniques and technologies implemented within industrial process control systems" (Wikipedia), including MPC and Advanced Regulatory Control (ARC), especially where more agile, high frequency, higher availability, more specialized, or smaller footprint solutions are desired. |
Process models are central to APC technology. Most APC activities center around obtaining and maintaining large numbers of detailed models. Most aspects of performance are related back to model quality. | Model-based control theory is sound, but over-emphasis on models can be counter-productive in practice. Sustained model accuracy is often impossible to achieve, since many process responses change frequently and dynamically. Where models are dynamic and not static, it poses a fundamental conundrum for model-based control. APC needs to re-orient itself, such that high-fidelity models are the exception, not the rule. |
An embedded optimizer is also an integral part of APC applications. The optimizer solves for both the optimum steady-state solution and the optimum path (minimum cost or error) to the steady-state optimum. | The optimum steady-state solution, or target operating point, is always well-known among the operating team, from the planning unit down to console operators. Targets can be entered directly into the APC application, rather than be solved dynamically within the application. An embedded optimizer is often redundant and unnecessary, while compounding application cost and complexity. |
The greater the number of variables and models, the more complete the solution. Matrix designs comprising dozens of variables and hundreds of models are common and are considered good practice. | Operating personnel typically utilize a much smaller set of variables to manage and optimize their processes. The greater the number of variables and models, the less reliability and higher costs the application will have. Established operation practice provides the most reliable and effective basis for matrix design, and usually yields a much more concise matrix. |
APC is a new technology made possible by computers. | Multivariable control has always been a central concept of industrial process operation. It is historically carried out manually by operators. MPC is one way to (partially) automation this function. There are other non-model-based solutions, such as automating the methods used by operators, who notably do not rely on detailed models, an optimizer, or an out-sized matrix. |
APC is the way to achieve aggressive profit maximization. | The value of APC is in alternately backing away from encroaching constraints and pursuing receding constraints (as explained in "The essential role of advanced control in process operation"), while carefully observing process speed limits and preserving process stability. Aggressive minimization of transient error is usually neither a large earner nor desirable behavior in industrial process operation. |
The current APC paradigm is well suited to the industrial process operation environment. | High cost, high maintenance, low agility, specialized support, short life-cycle, etc., are all strongly misaligned with industrial process automation and flexible manufacturing criteria in modern complex refineries. |
APC economics are solid. APC costs a lot, but it earns a lot. APC makes millions of dollars per year. | APC economics remain an area of concern. Costs have not come down. High maintenance, specialized support, and performance monitoring, were all unplanned and have added to costs of ownership. Meanwhile, benefits have not been as tangible as expected and often remain a matter of faith (Figure 3). Costs, maintenance and benefits need to come into line with each other. |
APC control performance is excellent and far exceeds, in terms of multivariable control and optimization, what can be accomplished without APC. | Performance also remains an area of concern. Degraded performance, low utilization and short life-cycles remain common problems. It remains an open (and rather urgent) question whether less complex, less expensive, smaller-footprint solutions can successfully automate the essential multivariable control applications and successfully capture the benefits. |
APC is inherently specialized and technical, and warrants a special place in terms of budgeting, scheduling, planning, support, etc. This can be expected to continue going forward. | Multivariable control is fundamental to process control and operation, and needs to be a core-competency at operating facilities. This means applications that reside at the DCS level, support that falls within the scope of on-site control engineers, sustained maintenance-free life-cycles, costs and schedules that fall within normal operating plans, etc. |
Matrix is a container for models. | Matrix guides operation, optimization, automation; useful handles, useful interactions, important constraints, optimization criteria... |
Adaptive modeling and auto-tuning. |
Figure 2: The legacy APC paradigm and a reimagined paradigm (or vision), based on accumulated experience, lessons learned, and more realistic goals and expectations from today's vantage point.
Figure 2 summarizes several gaps between the legacy APC paradigm and a reimagined paradigm that embraces experience gained, lessons learned, and more realistic goals and expectations from today’s vantage point. Where issues remain unresolved—as several core issues do—the reimagined paradigm fills in with promising possibilities so that it can also serve as an APC vision going forward.
One pillar of the conventional paradigm is that APC is highly specialized and expected to remain so, but the general trend in the reimagined paradigm is to evolve APC toward a core-competency at the industrial process operation level, where more agile, affordable and smaller-footprint multivariable control tools are needed for both process automation and process operation objectives.
The gaps in the current paradigm have undermined efficient communication between stakeholders. An updated paradigm that more accurately reflects the technology today and that accepts alternatives to some of the persistent root issues, which have impeded APC progress in the past, will help APC to more rapidly move forward again.
Figure 3: Many factors affect a process' controlled variables (CVs), making it problematic to identify the particular contribution of APC to benefits or performance.
Latest from Home
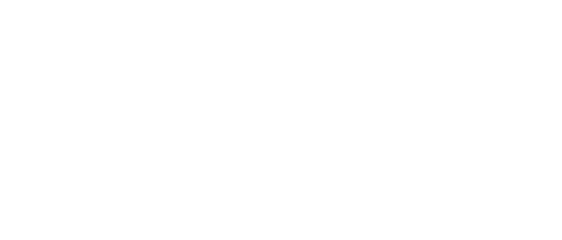
Leaders relevant to this article: