The Field Device Integration (FDI) specification and ecosystem isn’t resting on its laurels.
“FDI packages and hosts help bring field device information to control and upper-management systems, so their key is providing better interoperability, saving time and reducing headaches for users,” says Achim Laubenstein, integration technology director at the FieldComm Group. “However, as FDI packages and hosts from ABB, Emerson, Siemens and others begin to arrive, suppliers want to use the FDI information model and OPC UA to connect to other communication protocols, get data to the enterprise level via Microsoft Azure, and participate in the Industrial Internet of Things (IIoT) and Industrie 4.0.”
FDI was conceived to bring previously hard-to-reach data into uniformly reported and displayed formats, to help improve decisions and increase profits for process automation companies. It merges the advantages of an FDT Device Type Manager (DTM) and Electronic Device Description (EDD) in one, scalable software device package to help manage the complete lifecycles of basic and sophisticated components, including commissioning, configuration, diagnostics, calibration, maintenance and other functions.
“The clear benefit of FDI is its simplified drivers for different host systems,” says Michael Bückel, product manager at Endress+Hauser’s Flowtec division. “Where we used to have many drivers for many different host systems in place, FDI shrinks it to just one package that’s needed to get a device up and running or for operations and maintenance.”
In addition to simplifying the device management process, FDI will also enable:
- Open access to cloud-based computing services via jointly developed OPC UA information models,
- Offline configuration,
- A device package repository,
- Security, and,
- Communication servers for automation protocols.
[sidebar id =1]
These initiatives will enable FDI (published as the IEC 62769 standard) to fulfill its mission statement: ONE device – ONE package – ALL tools.
“The FDI standardization team did an excellent job of writing the FDI specification—fully supported by the FDI Package IDE [Integrated Development Environment]—and it’s a huge difference from the past,” says Neil Shah, global product manager for fieldbus and asset optimization in ABB’s Industrial Automation division. “Where users previously had to tweak device drivers on each system and modify EDDs to comply with each supplier’s host, FDI makes EDDs independent of individual supplier protocols, and allows all instruments to work with any host.”
Shah reports there are presently three host systems that support FDI, including:
- Field Information Manager (FIM) from ABB;
- Instrument Inspector from Emerson Automation Solutions, and
- Process Device Manager (PDM) from Siemens
“They all have the same purpose of integrating field devices into systems, and also allow configuration, commissioning, diagnosis and parameterization,” explained Shah.
Despite its potential advantages, some suppliers are concerned that FDI means they’ll have to develop software for it in addition to the EDDs and DTMs they already write for their field devices, which continue to be deployed in systems worldwide.
“FDI packages and hosts are at the beginning of their implementation cycle. They will eventually replace EDD and DTM,” adds Laubenstein. “We’ve already held several plugfests where different suppliers can compare and work hands-on with FDI packages and hosts, and we’re going to have more. We did confirm at the plugfests that FDI can achieve much better interoperability, and so our advice is to try FDI with OPC UA server because it’s ready for IIoT and Industrie 4.0.”
[sidebar id =2]
Offline configuration
One of the most sought-after capabilities in process control has been uncoupling configuration and other tasks from the components themselves, which allows this programming to be done remotely and completed before equipment is installed on plant floors.
“Offline configuration and user interface plug-ins (UIP) are so important because they let us create standardized configuration files, and download them to many devices, mostly when commissioning new plants,” says Dan Ryan, engineering program manager for Plantweb at Emerson and chair of the FieldComm Group Integration Working Group. “FDI lets us take device packages and work up configurations without the spreadsheets and manual processes we used to use. That’s a big savings in labor and time.”
Ryan explains that UIPs are equally useful because they enable enhanced interfaces for troubleshooting. UIPs are an optional part of an FDI device package. For example, Emerson’s Rosemount Radar Master Plus UIP provides annotated, interactive graphics, added graphical tools, and improved interoperability. “The UIP in FDI allows Radar Master Plus to be used on any FDI host,” says Ryan. “There’s more work to get FDI phased in now and it is a longer-term investment, but everything’s going to be better with it.”
Mani Janardhanan, program management director for Plantweb and IoT at Emerson, reports that FDI is beginning to enhance the capabilities of its products, including development plans for AMS Device Manager and the AMS Trex device communicator. “Our customers want a unified technology to communicate securely with their field devices from any platform, and FDI is that solution,” says Janardhanan. “Emerson is already well down the path on FDI, we introduced our Instrument Inspector in 2016, and it’s downloadable from our website. These solutions will make the offline configuration of plants and deployment better, which can help users and EPCs save man-years on commissioning.”
Integrating disparate networks
Today’s plants may contain a mixture of device technologies, some based on proprietary and open standards. FDI can access these devices using FDI Communication Servers. The Communication Servers integrate to the FDI Server using Communication Server Packages, allowing FDI to integrate these different networks within a single information model. This enables users to leverage their installed base of devices when migrating to the new FDI technology. FDI Communication Servers even support nested communication, where a remote device may be tunneled through a different protocol, supporting complete access to the embedded device data. Just like devices, communication servers are fully exposed in the FDI Server Information model. FDI Servers communicate with FDI Communication servers using OPC UA.
Cloud connectivity is enabled with the implementation of OPC UA on the FDI Server that exposes the FDI Information Model. The FDI Information model provides a consistent presentation of the device (the “digital twin”) for enterprise applications, cloud based services, etc. The Information Model of each device is defined in the device’s “FDI Device Package” using EDDL technology.
Smitha Rao, co-founder of Utthunga Technologies, adds that, “FDI enables the secure and remote communication to the field devices using FDI Communication Server, which is built based on industry-proven OPC UA technology.”
Device package repository
Because technicians configuring instruments don’t want to download software to each one individually, FieldComm Group is building a cloud-focused repository of all certified, FDI packages and secure EDD packages. This allows FDI-enabled devices to connect automatically, and check if they have any updates.
“The plan is to have an online system provide FDI device packages on request, which will give users quicker access to the latest versions,” says Endress+Hauser’s Bückel. “Again, that one device package can be installed in a user’s registered host system no matter what supplier it comes from, which makes that system simpler to maintain, and reduces lifecycle costs.”
Stephen Mitschke, director, Foundation Fieldbus Technology, FieldComm Group, adds that the FDI Device Package and Repository initiative is similar to the way Microsoft Windows downloads updates without requiring its users to go and get any software. Though still being built and tested, the repository will be built on Microsoft Azure.
Successful security
To maintain security even as it establishes more connections to outside users and systems, Mitschke reports that the FDI specification uses multiple layers. Improving its security on an ongoing basis is another FieldComm Group initiative.
“All FDI packages have digital signatures, which authenticates that software is coming from a trusted source, and indicates if it’s been modified,” explains Mitschke. “The FDI environment can also be implemented as a client on a server architecture, in which case we can rely on OPC Unified Architecture (UA) and its certificate-based security.
Latest from Home
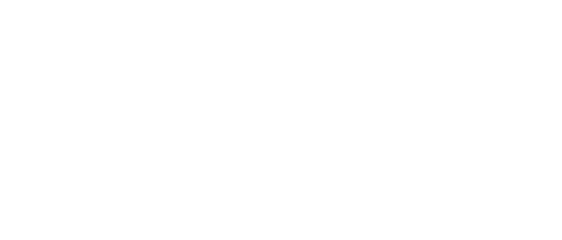
Leaders relevant to this article: